镍基单晶高温合金因其具有优异的高温抗氧化性和高温机械强度被广泛应用于高要求的工业部件,如燃气轮机叶片、喷气发动机和航空部件[1-4]。燃气轮机依靠连续流动的气体为工质带动叶片高速旋转将燃料的化学能转变为机械能实现运转。化石燃料和生物燃料 (C x H y ) 的燃烧产生大量水蒸气,因此研究水蒸气对合金氧化行为的影响至关重要[5-10],然而现在的研究大多集中于干空气氧化环境。
镍基单晶高温合金依靠在表面形成缓慢生长并具有粘附性的氧化膜以实现抗氧化的目的。常见的保护性氧化膜包括Cr2O3和Al2O3,研究[11-13]表明,使役环境中存在水蒸气会抑制镍基合金表面氧化膜形成元素Cr和Al的外氧化,进而加大了合金氧化速率。Wollgarten等[12]研究了Ni-14Cr-9Co合金在950 ℃空气和含20%水蒸气环境中的氧化行为。在干空气中氧化20 h后,合金表面氧化产物主要为连续的Cr2O3膜。而在湿空气中氧化后氧化膜为分层结构,氧化膜由外到内分别为NiO、Ni2CrO4和不连续的Cr2O3沉淀。Maris等[13]分析了镍基单晶高温合金N5和PWA 1484在1100 ℃下的氧化现象。在短时间暴露后,合金在干空气中形成了Al2O3膜。而在湿空气中水蒸气抑制了表面Al2O3膜的形成,合金内部只产生Al2O3沉淀。他们认为这种现象与氢掺杂导致NiO的生长增强有关,并通过在干燥和潮湿气体中暴露Ni-8Cr-6Al合金和纯Ni样品进行验证。
在不改变合金成分的情况下,将合金表面纳米化或者施加纳米晶涂层是促进表面Cr2O3或Al2O3膜形成的有效方法[14-16]。利用磁控溅射技术可以制备出与合金基体成分相同的纳米晶涂层。该涂层减缓了氧化后涂层与基体的元素互扩散问题。此外,与传统镍基合金涂层相比,在不增加涂层中Cr和Al含量的情况下,晶粒细化增加晶界体积分数从而促进元素扩散使得形成外部Cr2O3或Al2O3膜的临界含量降低,促进Cr或Al的选择性氧化[17-23]。楼翰一等[24]研究了K38G纳米晶涂层在1000 ℃的高温氧化行为,表明纳米晶涂层表面形成致密的Al2O3膜,具有优异的抗氧化性。Wang等[25]在1000 ℃静态空气中对高温合金N5及其纳米晶进行氧化试验,实验表明纳米晶涂层提高了高温合金的抗氧化性和抗剥落性。时龙等[26]将DD98M合金及其纳米晶涂层在900 ℃熔融Na2SO4+25%K2SO4盐中进行腐蚀试验,结果表明纳米晶涂层表现出良好的热腐蚀性能。但目前还没有关于溅射纳米晶涂层在中高温水蒸气环境中氧化行为研究的报道,这对于镍基高温合金及其纳米晶涂层的改进和发展具有一定影响。
本文在镍基单晶高温合金N5表面溅射纳米晶涂层,在900 ℃ O2和O2+20% (体积分数) H2O环境中对高温合金基体及其纳米晶涂层的氧化行为进行了对比研究,通过分析其氧化动力学、氧化形貌和元素分布规律,阐明合金基体和纳米晶涂层在O2和O2+20%H2O环境中的氧化机理。
1 实验方法
本实验采用中国科学院金属研究所自研的第二代镍基高温合金N5 (N5) 作为基体合金,名义成分 (质量分数,%) 为:Al 6.2,Cr 7.0,Co7.5,W 5.0,Ta 6.5,Mo 1.5,Re 3.0,Ni余量。合金经稀FeCl3溶液刻蚀后的表面形貌如图1a所示。由图可知合金由面心立方的γ基体相 (亮色区域) 和具有fcc结构的γ'强化相 (灰色区域) 组成。同时,局部区域不规则的分布着一些难溶元素 (白色颗粒)。将白色颗粒放大后如图1b所示,由该区域的面扫图1c和d可知,白色颗粒主要分布Ta。实验前通过线切割将单晶合金棒加工成Φ18×2 mm的圆片,并在试样顶部切割Φ1.5 mm小孔用于悬挂。试样表面经SiC砂纸打磨至2000#后,用乙醇和丙酮混合溶液超声清洗15 min,吹干备用。
图1 合金经FeCl3溶液刻蚀后的表面背散射形貌和面扫图
采用中频直流磁控溅射仪溅射纳米晶涂层,溅射靶材成分与基体相同,靶材尺寸为382 mm×128 mm×8 mm。样品装载后,将真空室抽真空至6×10-3 Pa,之后通入氩气。溅射过程中试样匀速旋转以保证涂层厚度均匀。溅射参数如下:氩气压力为0.2 Pa,基体温度为200 ℃,溅射功率为3000 W。
氧化实验在恒温管式炉中进行,测试温度为900 ℃。实验时,用镍铬丝将样品悬挂在石英管炉腔内。通过真空循环水泵,氧气带动水蒸气进入炉内来提供反应所需气氛。通过调控水浴温度和氧气流速控制水蒸气的体积分数。在氧气环境中进行氧化实验时不打开水浴系统,整个装置中将不产生水蒸气。水蒸气实验时设定水浴温度为60 ℃,氧气流量为50 mL/min,装置中水蒸气体积分数约为20%。在试样氧化前,测量样品表面积,并在精度为10-5 g的电子天平上称量样品的质量。然后将样品放入管式炉恒温区域进行氧化,每隔一定时间将样品从炉中取出,空冷至室温并测量其质量变化。由于样品在实验过程中悬挂放置,其称量质量不包含剥落和挥发的氧化物。每组试样选取3个平行样品进行实验,以保证实验准确性。
采用X'Pert PRO型X射线衍射仪 (XRD) 对氧化后样品的物相组成进行分析。采用Inspect F50扫描电子显微镜 (SEM) 观察样品的表面和截面显微结构,并使用INCA XMAX能谱仪 (EDS) 分析腐蚀产物的成分和元素分布。制备截面样品前,用化学镀的方法在样品表面沉积一层薄的镍以保护氧化膜,并将镀镍的样品嵌入到环氧树脂中。
2 实验结果
2.1 纳米晶涂层的微观结构
图2为溅射纳米晶涂层的表面和截面形貌。如图2a所示,涂层表面为“菜花”状形貌。图2b为试样经液氮浸过后得到的脆性断口形貌,涂层的全貌结构呈现柱状结构,排列均匀且致密。涂层截面的背散射图片如图2c所示,涂层与基体界面结合良好,涂层内部没有孔隙和裂纹。厚度约为23 μm。图2d为涂层表面的TEM图,由图可知涂层晶粒尺寸分布较均匀,晶粒尺寸分布范围为10~60 nm,平均晶粒尺寸为25 nm。晶粒内部和晶界存在大量缺陷,如堆垛层错。沉积态涂层的电子衍射分析结果如图2e所示,由于晶粒过于细小,电子衍射呈现连续的环状,对衍射环进行分析,发现涂层为γ/γ′相。
图2 溅射纳米晶涂层的表面和截面形貌
2.2 氧化动力学
图3为N5及其纳米晶涂层在900 ℃ O2和O2+20%H2O环境中氧化100 h的动力学曲线。在初始5 h内,N5合金在O2+H2O环境中质量增重较大,增重为0.12 mg/cm2,约为在O2中氧化增重的1.7倍。之后质量逐渐增加,直到80 h时质量减少,表明氧化过程中出现氧化膜剥落的现象。之后到100 h质量继续增加。而在O2中氧化,基体合金质量呈增长趋势,没有出现质量减少的现象。氧化100 h后,基体在O2中氧化增重为0.18 mg/cm2,在O2+H2O中氧化增重为0.23 mg/cm2,在O2+H2O中氧化的增量约是在O2中氧化的1.2倍。值得注意的是,基体在O2+H2O中氧化膜出现剥落情况,因此该增重不代表实际氧化膜增量。纳米晶涂层在O2和O2+H2O中氧化后,质量逐渐增加。随着氧化时间达到100 h后,在O2中氧化增重为0.11 mg/cm2,在O2+H2O中增重为0.17 mg/cm2。由上述结果可知,水蒸气的存在加速了合金和涂层的氧化。同时,与基体氧化增重相比,纳米晶涂层在O2和O2+H2O中的增重均低于基体合金氧化增重,且未发现质量减少现象,说明纳米晶涂层提高了合金的抗氧化性能,同时涂层具有良好的抗剥落性能,对合金基体起到了一定的保护作用。
图3 N5及其纳米晶涂层在900 ℃下O2和O2+H2O气氛中氧化100 h的动力学曲线
2.3 氧化形貌和相组成
N5及其纳米晶涂层在900 ℃ O2和O2+20%H2O环境中氧化100 h后的掠入射X射线衍射图谱如图4所示。合金基体在O2中氧化,表面形成NiO和少量Ta的氧化物。在O2+H2O中基体表面仅检测到单一的NiO。纳米晶涂层在两种氧化环境下均检测到明显的基体峰γ/γ′,说明生成的氧化膜较薄。在O2中氧化后表面的氧化产物为Al2O3。而在O2+H2O中氧化后的氧化产物除NiAl2O4,还检测到少量Al2O3。
图4 N5及其纳米晶涂层在900 ℃下O2和O2+H2O气氛中氧化100 h后表面的X射线衍射图谱
图5为合金基体在900 ℃ O2中氧化100 h后的表面形貌。如图5a所示,合金基体在O2中氧化100 h后,氧化产物表面大部分较平整,但局部区域弥散分布着一些球形瘤状凸起。瘤状产物放大后如图5b所示,瘤状产物疏松并伴随有裂纹。通过EDS结果可知 (图5c),该瘤状产物具有较高含量的Ta和O。结合XRD可知,该氧化产物为TaO2。如图1所示,大量难溶元素Ta不均匀分布在合金表面,其在高温下被氧化为TaO2。表面较平整区域具有较高含量的Ni和O,氧化产物为NiO。
图5 N5合金在900 ℃下O2中氧化100 h后的表面微观形貌及EDS分析
图6a为合金基体在900 ℃ O2+20%H2O环境中氧化100 h后的表面形貌。区别于O2中的氧化表面,氧化产物瘤状凸起较少。由图6b局部放大图可知,局部区域氧化膜发生了剥落,剥落区域露出内部氧化产物。经EDS分析可知表面氧化产物为NiO (图6c),内部氧化产物主要为NiAl2O4 (图6d)。
图6 N5合金在900 ℃ O2+H2O气氛中氧化100 h后的表面微观形貌及EDS分析
图7为合金基体分别在900 ℃ O2和O2+20% H2O环境中氧化100 h后的截面微观形貌。图7a为合金基体在900 ℃ O2中氧化后的截面显微照片,图中包含贯穿氧化膜的白色氧化产物,对其进行EDS分析,结合表1可知其具有较高含量的Ta和O,与图5b中的瘤状氧化产物相对应,为TaO2。氧化膜局部放大如图7b所示,从氧化膜表面到氧化膜/基体界面,存在多层氧化产物。结合XRD以及表1结果可知,外层浅灰色氧化层含有较高含量的Ni和O,为NiO。次外层深灰色氧化层除了含有较高含量的Ni和O,还具有较高含量的Al,由此可知次外层氧化产物为NiAl2O4。在次外层氧化膜靠近内层氧化膜部分弥散分布着许多白色颗粒,经分析可知白色颗粒为Ta的氧化物。内层黑色氧化膜具有较高的Al和O,其氧化产物为Al2O3。图7c为合金基体在900 ℃ O2+H2O环境中氧化后的截面显微照片,外层氧化膜和基体界面形成岛状内氧化区,外层氧化膜存在许多裂纹和孔洞。氧化区局部放大图如图7d所示,结合表1可知,外层疏松多孔的氧化膜为NiO,岛状内氧化区由外氧化膜到基体界面,依次为深灰色氧化产物NiAl2O4,白色颗粒组成的条带状氧化产物TaO2和黑色氧化产物Al2O3。
图7 N5合金在900 ℃下O2和O2+H2O气氛中氧化100 h后的截面微观形貌图
表1 图7中1~7点EDS分析
图8为溅射纳米晶涂层在900 ℃ O2和O2+20% H2O环境中氧化100 h后的微观表面和截面形貌。如图8a所示,纳米晶涂层在O2中氧化100 h后,氧化表面较平整且没有裂纹。结合EDS和XRD分析,涂层表面氧化产物为Al2O3。图8c为截面照片,氧化膜致密内部无裂纹等缺陷,且氧化膜为单层结构,结合XRD结果分析可得氧化产物为单一成分的Al2O3。氧化膜厚度约为0.5 ?m。图8b为涂层在O2+H2O环境中氧化100 h后的表面形貌图,涂层表面均匀分布颗粒状氧化物,表面未发现裂纹。对比涂层在O2中氧化后的表面可发现水蒸气存在明显增大了氧化物颗粒粒径。通过图8d的截面照片可以看出氧化膜由单层黑色平整氧化产物组成。对其进行EDS分析可知,氧化产物为NiAl2O4。氧化膜厚度约为1 ?m,其厚度约为O2中氧化膜厚度的2倍。
图8 纳米晶涂层在900 ℃下O2和O2+H2O气氛中氧化100 h后的表面和界面形貌图
3 分析与讨论
由上述实验结果可知,纳米晶涂层在O2和O2+20%H2O环境中氧化都有效提高了合金基体的抗氧化性能。同时相较于O2环境,水蒸气增大了涂层和基体的氧化速率,降低氧化膜粘附性并影响氧化膜组成。下面将结合上述分析结果,讨论合金和纳米晶涂层在O2和O2+H2O环境中的氧化机理。
3.1 合金和纳米晶涂层在O2环境中的氧化机理
如图3所示,基体在900 ℃ O2中氧化100 h后氧化膜为分层结构,外层为NiO,内层为Al2O3,两层之间为NiAl2O4。而纳米晶涂层在900 ℃ O2中氧化后表面氧化膜为Al2O3 (图4和8)。根据Wagner[27]理论,当涂层内的Al含量超过一个临界值时表面将形成外部Al2O3膜,这个临界判据用 式 (1) 表示:
其中,NODO是氧在合金中的渗透率,DAl是Al的扩散系数,g*是由Al2O3体积分数决定的因子,VM和分别是涂层和Al2O3的摩尔体积。由 式 (1) 可知,增加涂层内Al含量或降低其临界值有利于促进外部Al2O3膜的形成。而Al形成外部Al2O3氧化膜的临界浓度随Al扩散系数的增加或晶界数量的增加而降低。通过磁控溅射获得的涂层晶粒尺寸为纳米等级,它包含较大的晶界体积分数和缺陷,这些晶界成为Al、O等元素的快速扩散通道,有利于促进Al的选择性氧化,因此纳米晶涂层表面形成一层保护性的Al2O3膜。而单晶合金毫米级的晶粒尺寸使得其内部Al含量不足以在其表面形成完整的Al2O3膜,因此在合金表面优先形成一层连续的NiO膜,降低Ni的活度和合金/氧化膜界面的平衡氧分压。Al2O3平衡氧分压远低于NiO,在合金/氧化膜界面形成连续Al2O3膜。NiO和Al2O3反应生成NiAl2O4。Al2O3膜因具备较低的扩散系数、极低的标准Cibbs自由能、适中的 (1.2~1.6) 氧化物与金属的体积比 (PBR),被认为是一种较理想的抗氧化膜,因此纳米金涂层在O2中氧化表现出较合金更优的抗氧化性。
3.2 合金和纳米晶涂层在O2+H2O环境中的氧化机理
根据文献报道,当氧化环境中含有水蒸气时,相比于O2分子,H2O分子被认为是主要的氧化剂[28]。氧化时,H2O分子吸附至金属表面,然后分解成OH-和/或O2-,进而和金属反应生成氧化物。研究表明[29],H2O分子分解消耗的能量小于O2分子,其分解更易发生。同时,相比于O2-,OH-的半径更小[30],在相同温度下扩散速率更快。因此与O2分子相比,H2O分子在高温下具有更强的氧化性。
如图7d所示,基体在O2+H2O中氧化后,氧化膜组成与O2中氧化相同,但氧化膜更厚,在氧化膜/基体界面形成岛状内氧化区,甚至氧化表面出现裂纹和剥落。而在O2+H2O环境中氧化后,纳米晶涂层表面氧化膜为NiAl2O4 (图8d)。这些现象与水蒸气诱发氢掺杂促进NiO生长增强有关。在O2+H2O环境下,水蒸气吸附在合金基体或涂层表面,与Ni发生如下反应:
由于Ni的扩散比氧的扩散快,在氧化时Ni2+向外扩散,与表面的水蒸气发生反应生成NiO和H2。H2大部分解离为H+,解离的H原子一部分与O2重新结合形成新的H2O,另一部分以H2的形式脱附,还有一部分H原子固溶在金属基体和氧化膜中[31],并在氧化膜/金属界面处聚集形成H2分子,引发表面氧化膜鼓泡与开裂,最终导致氧化膜剥落。Maris等[13]认为H2O中的H可固溶在NiO中,通过反应使阳离子空位浓度增加,进而使镍通过NiO的传输增加。所以溶于氧化膜中的H将通过以下反应增加阳离子空位浓度:
阳离子空位浓度升高,促进Ni的向外扩散。在初始5 h氧化时,在O2+H2O环境中合金表面氧化产物质量增加速率更快,在表面快速形成一层NiO氧化膜。H2和H2O穿过表面氧化层到达氧化膜/基体界面,与界面发生于气体界面相似的反应,反应后将会产生过量的阳离子空位,随着氧化的进行,空位复合使内外氧化层界面出现空洞或孔隙。由于微裂纹的不断形成,少量的水蒸气可以通过微裂纹直接进入氧化膜/基体界面。由于在氧化膜/基体界面氧分压降低,氧的浓度和扩散系数随着氧分压的降低而降低,最终在氧化膜/基体界面向基体方向形成岛状的内氧化区,内氧化区成分依次为NiAl2O4和Al2O3。
相比于合金,纳米晶涂层在O2+H2O环境中形成尖晶石相的瞬态氧化阶段延长,因此纳米晶涂层表面主要为NiAl2O4氧化膜。尖晶石结构的氧化产物AB x O y 在高温环境下拥有一定的抗氧化能力。在本次研究中,由于金属阳离子在NiAl2O4的扩散速率低于NiO,因此试样外层形成的氧化产物按抗氧化性能的优劣排序为NiO<NiAl2O4<Al2O3,因此无论在O2还是O2+20%H2O环境中氧化,纳米晶涂层都显著的提高了合金在高温环境下的抗氧化性能。
4 结论
(1) N5单晶合金在O2和O2+20vol.%H2O中氧化后表面都形成了外层NiO、中间层NiAl2O4和内层Al2O3的分层氧化膜;但在O2+H2O中氧化时,氧化速率较大,而且外层氧化膜发生剥落。
(2) 纳米晶涂层显著提高了合金的抗高温氧化性能,在O2中表面形成Al2O3,而在O2+20vol.%H2O中形成NiAl2O4。但无论在O2还是O2+H2O中氧化,纳米晶涂层都没有产生开裂和剥落,起到了良好的保护作用。
(3) 水蒸气加快了N5合金和涂层的氧化速率,促进了合金表面氧化膜的开裂和剥落,并且影响了氧化膜的组成和结构。
参考文献
1 Wu Y, Narita T. Oxidation behavior of the single crystal Ni-based superalloy at 900 ℃ in air and water vapor [J]. Surf. Coat. Technol., 2007, 202: 140
doi: 10.1016/j.surfcoat.2007.05.018
2 Park S J, Seo S M, Yoo Y S, et al. Effects of Al and Ta on the high temperature oxidation of Ni-based superalloys [J]. Corros. Sci., 2015, 90: 305
doi: 10.1016/j.corsci.2014.10.025
3 Wang X Y, Xin L, Wang F H, et al. Influence of sputtered nanocrystalline coating on oxidation and hot corrosion of a nickel-based superalloy M951 [J]. J. Mater. Sci. Technol., 2014, 30: 867
doi: 10.1016/j.jmst.2014.01.001
4 Qiu P P, Shu X Y, Hu L L, et al. Research progress of Pt-modified aluminide coating on Nickel-base superalloys [J]. J. Chin. Soc. Corros. Prot., 2022, 42: 186
4 邱盼盼, 舒小勇, 胡林丽 等. Pt改性镍基高温合金铝化物涂层研究进展 [J]. 中国腐蚀与防护学报, 2022, 42: 186
5 Saunders S R J, Monteiro M, Rizzo F. The oxidation behaviour of metals and alloys at high temperatures in atmospheres containing water vapour: a review [J]. Prog. Mater. Sci., 2008, 53: 775
doi: 10.1016/j.pmatsci.2007.11.001
6 Zhu D D, Wang X L, Zhao J, et al. Effect of water vapor on high-temperature oxidation of NiAl alloy [J]. Corros. Sci., 2020, 177: 108963
doi: 10.1016/j.corsci.2020.108963
7 Yan K, Guo H B, Gong S K. High-temperature oxidation behavior of minor Hf doped NiAl alloy in dry and humid atmospheres [J]. Corros. Sci., 2013, 75: 337
doi: 10.1016/j.corsci.2013.06.017
8 Chandra-Ambhorn S, Saranyachot P, Thublaor T. High temperature oxidation behaviour of Fe-15.7 wt.% Cr-8.5wt.%Mn in oxygen without and with water vapour at 700 ℃ [J]. Corros. Sci., 2019, 148: 39
doi: 10.1016/j.corsci.2018.11.023
9 Cao J Y, Fang Z G, Li L, et al. Corrosion behavior of domestic galvanized steel in different water environment: fresh water and salt water [J]. J. Chin. Soc. Corros. Prot., 2021, 41: 169
9 曹京宜, 方志刚, 李亮 等. 国产镀锌钢在不同水环境中的腐蚀行为: I淡水和盐水 [J]. 中国腐蚀与防护学报, 2021, 41: 169
10 Liu Y C, Zhong X K, Hu J Y. Characteristics and mechanisms of elemental sulfur induced corrosion of sulfur-resistant steels in wet flow CO2 environment [J]. J. Chin. Soc. Corros. Prot., 2022, 42: 369
10 刘毅超, 钟显康, 扈俊颖. 湿气环境中抗硫钢的元素硫腐蚀特征及腐蚀机理 [J]. 中国腐蚀与防护学报, 2022, 42: 369
11 Zhao W, Gleeson B. Assessment of the detrimental effects of steam on Al2O3-scale establishment [J]. Oxid. Met., 2015, 83: 607
doi: 10.1007/s11085-015-9541-8
12 Wollgarten K, Galiullin T, Nowak W J, et al. Effect of alloying additions and presence of water vapour on short-term air oxidation behaviour of cast Ni-base superalloys [J]. Corros. Sci., 2020, 173: 108774
doi: 10.1016/j.corsci.2020.108774
13 Maris-Sida M C, Meier G H, Pettit F S. Some water vapor effects during the oxidation of alloys that are α-Al2O3 formers [J]. Metall. Mater. Trans., 2003, 34A: 2609
14 Wang J L, Chen M H, Zhu S L, et al. Ta effect on oxidation of a nickel-based single-crystal superalloy and its sputtered nanocrystalline coating at 900-1100 ℃ [J]. Appl. Surf. Sci., 2015, 345: 194
doi: 10.1016/j.apsusc.2015.03.157
15 Sun W Y, Chen M H, Bao Z B, et al. Breakaway oxidation of a low-Al content nanocrystalline coating at 1000 ℃ [J]. Surf. Coat. Technol., 2019, 358: 958
doi: 10.1016/j.surfcoat.2018.12.034
16 Yang S S, Wang Y Q, Chen M H, et al. Oxidation behavior of Al/Y co-modified nanocrystalline coatings with different Al content on a nickel-based single-crystal superalloy [J]. Corros. Sci., 2020, 170: 108700
doi: 10.1016/j.corsci.2020.108700
17 Liu Z Y, Gao W, Dahm K L, et al. Oxidation behaviour of sputter-deposited Ni-Cr-Al micro-crystalline coatings [J]. Acta Mater., 1998, 46: 1691
doi: 10.1016/S1359-6454(97)00346-7
18 Geng S J, Wang F H, Zhang S. Cross-sectional oxide distribution of cast IN738 and its sputtered coating at 1000 ℃ [J]. Surf. Coat. Technol., 2003, 167: 161
doi: 10.1016/S0257-8972(02)00909-X
19 Wang F, Tian X, Li Q, et al. Oxidation and hot corrosion behavior of sputtered nanocrystalline coating of superalloy K52 [J]. Thin Solid Films, 2008, 516: 5740
doi: 10.1016/j.tsf.2007.07.131
20 Cheruvu N S, Wei R, Gandy D W. Influence of thermal exposure on the stability of metastable microstructures of sputter deposited nanocrystalline 304 and 310 stainless steel coatings [J]. Surf. Coat. Technol., 2010, 205: 1211
doi: 10.1016/j.surfcoat.2010.10.035
21 Yang L L, Wang J L, Yang R Z, et al. Oxidation behavior of a nanocrystalline coating with low Ta content at high temperature [J]. Corros. Sci., 2021, 180: 109182
doi: 10.1016/j.corsci.2020.109182
22 Yang S S, Yang L L, Chen M H, et al. Understanding of failure mechanisms of the oxide scales formed on nanocrystalline coatings with different Al content during cyclic oxidation [J]. Acta Mater., 2021, 205: 116576
doi: 10.1016/j.actamat.2020.116576
23 Yang L L, Chen M H, Wang J L, et al. Diffusion of Ta and its influence on oxidation behavior of nanocrystalline coatings with different Ta, Y and Al contents [J]. Corros. Sci., 2017, 126: 344
doi: 10.1016/j.corsci.2017.07.017
24 Lou H Y, Chen G F. High temperature oxidation behavior of nanocrystalline Ni-Cr-Al super alloys [J]. Corros. Sci. Prot. Technol., 2003, 15: 147
24 楼翰一, 陈国锋. Ni-Cr-Al纳米晶合金在1000 ℃的高温氧化行为 [J]. 腐蚀科学与防护技术, 2003, 15: 147
25 Wang J L, Chen M H, Yang L L, et al. Comparative study of oxidation and interdiffusion behavior of AIP NiCrAlY and sputtered nanocrystalline coatings on a nickel-based single-crystal superalloy [J]. Corros. Sci., 2015, 98: 530
doi: 10.1016/j.corsci.2015.05.062
26 Shi L, Xin L, Wang F H, et al. Influences of nanocrystalline coating on hot corrosion behavior of DD98M alloy [J]. China Surf. Eng., 2017, 30(5): 1
26 时龙, 辛丽, 王福会 等. 纳米晶涂层对DD98M合金热腐蚀行为的影响 [J]. 中国表面工程, 2017, 30(5): 1
27 Wagner C. Reaktionstypen bei der oxydation von legierungen [J]. Zeit. Elektrochem. Berichte Buns. Phys. Chem., 1959, 63:772
28 Tomozawa M. Water diffusion in silica glass and wet oxidation of Si: an interpretation for the high speed of wet oxidation [J]. J. Electrochem. Soc., 2011, 158: G115
doi: 10.1149/1.3560037
29 ?kermark T, Hultquist G. Oxygen exchange in oxidation of an Fe-20Cr-10Al alloy in ~10 mbar O2/H2O-gas mixtures at 920 ℃ [J]. Oxid. Met., 1997, 47: 117
doi: 10.1007/BF01682374
30 Henry S, Mougin J, Wouters Y, et al. Characterization of chromia scales grown on pure chromium in different oxidizing atmospheres [J]. Mater. High Temp., 2000, 17: 231
doi: 10.1179/mht.2000.17.2.008
31 Zhang Y, Pint B A, Haynes J A, et al. The effect of water vapor on the oxidation behavior of CVD iron-aluminide coatings [J]. Oxid. Met., 2004, 62: 103
doi: 10.1023/B:OXID.0000038788.02094.cb
免责声明:本网站所转载的文字、图片与视频资料版权归原创作者所有,如果涉及侵权,请第一时间联系本网删除。
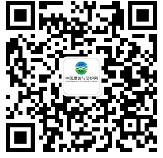
官方微信
《腐蚀与防护网电子期刊》征订启事
- 投稿联系:编辑部
- 电话:010-62316606-806
- 邮箱:fsfhzy666@163.com
- 腐蚀与防护网官方QQ群:140808414