铝合金具有高比强度/比模量、高耐蚀等优点,是两栖飞机和车辆、舰载飞机、跨海大桥等高技术海洋工程装备与构筑物十分重要的结构材料[1~3]。水上飞机和舰船用铝合金常选用耐蚀性好的2×××系、5×××系及6×××系[4,5]。海上铝合金装备长期受海水和盐雾的侵蚀,同时受海风和海浪冲击,工况条件复杂严酷,具有腐蚀类型多和速率高、腐蚀部位隐蔽多发、腐蚀损伤程度大等特点[6]。铝合金材料的腐蚀问题不仅造成巨大的维修成本,而且已成为决定海洋装备寿命、保证技战术水平的关键因素。
大型舰船、两栖飞机和车辆等铝合金海洋装备的服役环境除了海水和海洋大气外,还涉及海水/海洋大气的交界区域,即海水/大气界面区[7,8]。海水/大气界面区主要分为3种环境工况:水线区、潮差区和飞溅区。对于船舶等浮式结构物,“海水/大气界面区”通常称为“水线区”,是指船舶重载水线和轻载水线之间的船体区域,该区域由于经常交替受到海水浸泡和大气曝晒,表面涂层易受到海水以及漂浮物的冲刷和撞击而损坏,所以是腐蚀比较严重的区域。对于跨海大桥钢桩等固定式海洋结构物,“海水/大气界面区”即为“潮差区”,是指平均低潮位和平均高潮位之间的区域。飞溅区是指潮差区之上受到浪花飞溅作用的区域,除了表面有干湿交替外,浪花的冲击作用是很重要的因素。水线区、潮差区和飞溅区有相似之处(即干湿交替),但3者环境工况有明显差别。本工作主要研究的是第一种情况,值得注意的是此种情况下的海水/大气界面区是动态水线作用下的界面区(下文简称为水气界面区)。
水气界面处于干湿交替、供氧充足、盐分浓缩的环境中,腐蚀环境涉及大气、海水、海盐等多相耦合作用[9,10]。我国积累了铝合金在实海海水潮汐区[11]、全浸区[12]和飞溅区[13]长达16 a的腐蚀数据,总结了平均腐蚀速率和点蚀深度的变化规律。国外学者[14]也做了碳钢的实海暴露实验,发现浪花飞溅区和水线下方的腐蚀速率远远大于水线处和大气区。由于供氧差异等因素导致水气界面区的腐蚀电位与海水中的腐蚀电位不同,形成宏观腐蚀电池,导致材料表面局部阳极区域腐蚀加速[15]。低碳钢在静水条件下,由于水线上下区域的氧浓度差异和水线下方邻近区域因氧还原形成的pH梯度,水线腐蚀由氧浓差和pH共同控制[16];在流动环境中,由于水线附近的OH-容易扩散,并不会形成pH梯度,水线腐蚀此时完全由氧浓差控制[16]。目前国内外关于金属材料在水气界面区的腐蚀研究已取得了重要的进展,建立了模拟潮差[15]和浪花飞溅[17]等模拟测试装置,但缺少动态水气界面区模拟装置及配套的原位实时腐蚀测试技术。
本工作搭建由电动推杆、时间继电器及腐蚀电化学传感器组成的模拟动态水气界面腐蚀测试平台,采用腐蚀电位监测、电化学阻抗谱(EIS)和电化学噪声(EN)技术研究2024铝合金在水气界面区的腐蚀电化学行为及局部腐蚀机制,并分析水气界面区与全浸区腐蚀行为的差异性,探讨不同区域腐蚀电位不同对宏观腐蚀电池的影响机制,为深入理解海水/大气界面的局部腐蚀损伤机制奠定理论基础。
1.1 实验材料
实验所用金属材料为2024铝合金,冷轧后经固溶和时效处理,其化学成分(质量分数,%)为:Cu 4.7,Mg 1.4,Mn 0.86,Fe 0.55,Si 0.51,Zn 0.30,Ti 0.15,Ni 0.1,Al余量。试片尺寸为250 mm × 105 mm × 2 mm。
1.2 模拟动态水气界面综合腐蚀测试平台的搭建
搭建的模拟动态水气界面腐蚀测试平台如图1a所示,主要由水气界面模拟控制系统和电化学测试系统组成。水气界面模拟控制系统由电动推杆、时间继电器、水箱及试样架组成(图1a)。塑料试样架上可同时放置4片铝合金试样,在电动推杆及时间继电器的控制下试样架及其铝合金试样上下往复运动,推进步长为10 cm,每次上下移动时间间隔为30 s,即水气界面区处于交替的“浸入-移出”海水环境中,实验共进行54 d。铝合金试样处于大气区、水气界面区和全浸区的高度分别为10、10和5 cm (图1b)。水箱中盛有体积为40 L的3.5%NaCl (质量分数)溶液。电化学测试系统主要由4个电化学传感器和PARSTAT 2273电化学工作站组成。水气界面区和全浸区分别放置1个EIS测试传感器和1个EN传感器。值得注意的是,为了满足电化学测试稳定性的要求以及消除溶液Ohm电位降的影响,水气界面区的电化学测试是当试样移至水下时进行的。
1.3 EIS测试
EIS测试传感器由对电极和参比电极组成(图1c),主要用于测量水气界面区与全浸区的开路电位(OCP)及EIS。对电极为镀Pt铌棒,参比电极为Ag/AgCl电极(在3.5%NaCl溶液中相对于饱和甘汞电极的电位为1~3 mV)。EIS测试采用控制电位的方法,待腐蚀电位稳定后开始测试,施加电位正弦波的幅值为10 mV,测试频率范围为105∼10-2 Hz,共测40个数据点。EIS数据采用Orazem课题组近期编制的Measurement Model Installer (Version 1.4)软件进行拟合[18,19]。
1.4 电化学噪声测试
EN测试采用零阻电流(ZRA)检测模式,可同时测得电位噪声和电流噪声。EN检测传感器如图1d所示,传感器主要包括面积为1.48 cm2的圆盘形铝合金电极(记为WE2)和Ag/AgCl参比电极(图1d)。圆形电极与待测2024铝合金试片(记为WE1)为同种材质,因此,电流噪声实际上测的是WE1和WE2之间的电偶电流,电位噪声测的是WE1和WE2耦接后的电位随时间的波动规律。由于WE1和WE2的面积不同,实际上EN检测的电极系统属于非对称电极系统(asymmetrical electrode system)。采用非对称电极系统的目的是为了将来便于现场检测。由于非对称电极系统计算得到的噪声电阻与腐蚀速率之间的关系较为复杂,而且噪声电阻主要反映了腐蚀体系均匀腐蚀的速率,因此本工作并没有计算噪声电阻[20]。本工作主要采用EN数据的频域分析评估局部腐蚀敏感性,将EN数据先采用五次多项式拟合剔除直流分量[21],再进行快速Fourier变换(FFT)后,利用FFT频谱图中高频线性区斜率和白噪声水平判断局部腐蚀强度。高频线性区的斜率越陡,低频白噪声水平越大,局部腐蚀倾向越明显[22,23]。
1.5 表面和截面形貌观察及成分分析
采用VHX-2000C光学显微镜(OM)观察试样表面宏观形貌,采用SU1510钨灯丝扫描电镜(SEM)观察2024铝合金在水气界面区和全浸区的表面和截面微观形貌,并利用能谱仪(EDS)对铝合金不同位置的腐蚀产物进行元素成分分析。采用浓HNO3去除铝合金表面的腐蚀产物后,计算平均腐蚀深度(5~8个点取平均值)和蚀孔密度。
2.1 腐蚀电位检测
图2为水气界面区2024铝合金的腐蚀电位随“浸入-移出”水面的周期性变化趋势。2024铝合金腐蚀电位(移出水面时)总体变化趋势为先变正后变负,4、15和34 d的腐蚀电位分别为-0.798、-0.787和-0.794 V (vs Ag/AgCl)。实验至4 d时,界面区铝合金浸入溶液以后,腐蚀电位迅速负移约10 mV,移出水面后,迅速正移约10 mV。腐蚀电位主要由阴阳极反应进行的难易程度来控制,假定界面区和全浸区的阳极反应动力学基本一致,那么腐蚀电位主要由阴极反应进行的速率来决定。由于界面区的O含量相对全浸区较高,因此腐蚀电位较正。实验至15 d,腐蚀电位随“浸入-移出”水面的周期性变化幅度减小(约4 mV),而且随着浸入溶液,腐蚀电位缓慢负移,移出水面以后,腐蚀电位缓慢正移,这主要是因为表面覆盖一层腐蚀产物所致。由于腐蚀产物膜有一定厚度,因此溶液完全渗透需要一定的时间,腐蚀电位变化迟缓。实验进行至34 d,腐蚀电位周期性波动的幅值又增加至10 mV,这主要是因为铝合金表面不断生成的腐蚀产物使得原来的腐蚀产物部分脱落,露出铝合金基体。因此,浸入溶液后,铝合金的腐蚀电位负移的速率比15 d的快,但比4 d的慢。电位负移速率的快慢也与局部腐蚀敏感性有一定关系,相比表面覆盖钝化膜的金属来说,裸金属的电位负移速率要快。因此,电位负移速率的变化体现了局部腐蚀敏感性先降低后增加的趋势。
2.2 电化学阻抗谱特征
采用EIS技术对2024铝合金在水气界面和全浸区54 d的腐蚀过程进行了检测,结果分别如图3a和b所示。从图3a可以看出,水气界面区的容抗弧半径出现先增大后减小的趋势,33 d对应的容抗弧半径最大。1 d对应的容抗弧半径约15 kΩ·cm2,由于容抗弧半径近似等于腐蚀体系的极化电阻,说明此时钝化膜虽然有一定的耐蚀性,但易发生破裂,局部腐蚀萌生。随着腐蚀进行,铝合金表面生成一层较为均匀致密的腐蚀产物层,容抗弧半径不断增大,33 d达到最大值。此后由于腐蚀的不断进行,靠近铝合金基体的腐蚀产物的生成会导致外层的腐蚀产物膜部分脱落,容抗弧半径有所减小,与10 d的容抗弧半径相当。前5 d的EIS呈现“单”容抗弧特征,之后由于腐蚀产物膜的覆盖,呈现“双”容抗弧特征,表明腐蚀体系最开始的电极反应速率由钝化膜的完整性控制,逐渐变为由腐蚀产物膜层控制。
全浸区的EIS测试结果如图3b所示。容抗弧半径呈现逐渐增大的趋势,54 d的容抗弧半径最大。表明溶液区的腐蚀产物对基体的保护性与水气界面区有所不同。全浸区前5 d的EIS呈现“单”容抗弧特征,而后出现“双”容抗弧特征。
图4为钝性金属电极在电解质溶液中的电化学等效电路模型[24],Re为溶液电阻。腐蚀电位下总的阻抗主要包含2个独立的部分:阳极部分和阴极部分,分别对应阳极反应过程和阴极反应过程。阳极分支中,Cdl为双电层电容,Rox,i为带电物种(阳离子空位)在钝化膜中移动的阻力,属于离子运动的电阻;由于钝化膜/溶液界面和铝合金基体/钝化膜界面的电化学反应对应的阻抗相比于Rox,i很小,因此都可以忽略。ZF3O2为钝化膜/溶液界面O2还原的Faraday电阻,Rox,e为电子在钝化膜中移动的阻力。Cdl位于阳极部分,这主要是因为在钝化膜/溶液界面,钝化膜中的空位和离子与双电层中的离子达到了动态平衡,形成了稳定的双电层。
图4给出的电化学等效电路是一种理想情况,即仅针对铝合金表面覆盖一层完整的均质钝化膜。实际的腐蚀体系的钝化膜局部可能已经发生孔蚀,而且局部有腐蚀产物覆盖,因此很难准确判断实际腐蚀体系存在几个时间常数,因为不同区域的电容和电阻值是不同的。本工作所测的EIS数据存在时间常数的弥散现象,这可能是由于材料表面不同区域的传质过程不同,或是由于电极几何因素引起的电流和电位分布不均匀,或是由于腐蚀产物膜的多孔结构及其分布不均匀造成的。为了解决此问题,Orazem课题组[18,19]近期提出了一种普适性模型Measurement Model,该模型可以较为准确地提取溶液电阻、极化电阻和无限频率下的有效电容。当腐蚀体系存在k个电阻-电容(RC),电路的复阻抗Z表达式为[18]:
式中,k称为Voigt元件个数,其值由软件自动确定,当确定原则是增加k值,回归参数的拟合误差限制在95.4% (± 2) (为总体标准差)的置信区间;Ri和Ci为对应第i个元件的极化电阻和电容,1 ik;ω为测试频率。从 式(1)可以看出,当ω无限大时,可以通过 式(2)计算腐蚀金属电极的有效电容Ceff[18]:
式中,。当测试频率趋近于0时,可以得到体系的极化电阻Rp[18]:
图5为拟合得到的Rp和Ceff。可以看出,界面区的Rp先增大后减小,全浸区的Rp基本呈现增大-减小-再增大的趋势。界面区和全浸区的Ceff差别不大,且呈现先减小再增加的趋势。腐蚀前期由于界面区腐蚀产物的生成,导致表面膜的介电常数发生改变,因此Ceff减小。后期由于腐蚀产物膜的脱落,Ceff有所增大,但界面区和全浸区的Ceff差别不大。
2.3 电化学噪声特征
图6a和b给出了水气界面区的电化学电流噪声和电位噪声测试结果,测试时水气界面移至水下,以消除溶液Ohm电阻对测试结果的影响。3 d时的电位噪声出现典型的局部腐蚀的特征,即有很多暂态峰,幅值达到4 mV (图6b);电流噪声的波动幅值为20 nA (图6a),而且此时电位和电流噪声的波动频率较快,表明钝化膜破裂修复事件发生的频率较高。10 d时,电位噪声波动幅值有所减小,约为1 mV;电流噪声波动幅值也有减小,约为10 nA,表明由于腐蚀产物的覆盖作用,局部腐蚀发展速率有所减缓。实验进行至49 d时,电位噪声和电流噪声波动周期逐渐变长,表明随着腐蚀产物的增加,物质传递速率减慢,使得电位与电流波动周期变长[23,25]。
图7给出了全浸区的电流噪声和电位噪声测试结果。3 d时的电位噪声和电流噪声波动幅值和波动周期与水气界面区类似。随着时间延长至10 d,电位和电流噪声的波动幅值减小,表明腐蚀产物的生成一定程度上抑制了局部腐蚀的强度。49 d时,电位噪声和电流噪声波动周期渐变长,其原因与水气界面区相同。
图8给出了2024铝合金在水气界面区(图8a和c)和全浸区(图8b和d)的电化学噪声数据通过快速Fourier变换得到的功率谱密度(PSD),通过计算电位和电流PSD高频线性区的斜率可以看出,其值均小于或接近-20 dB/dec,表明其腐蚀形态主要是局部腐蚀。对比低频白噪声水平,可以发现,水气界面区电流噪声的低频白噪声水平先下降再上升(图8c)。全浸区的低频白噪声水平基本呈现一直下降的趋势(图8d),表明局部腐蚀强度随时间延长有所下降。水气界面区和全浸区的测试结果与EIS结果基本一致。
2.4 表面和截面腐蚀形貌分析
图9为2024铝合金大气区、水气界面区和全浸区宏观腐蚀形貌随时间的变化。图中4个虚线圆圈标出的区域为EIS和EN检测的区域。试样表面主要分为3个区域:上面是大气区,中间是水气界面区,下面是全浸区。实验3 d后,可以看到水气界面区和大气区交界处开始有盐层沉积。水气界面区有一层白色腐蚀产物,且腐蚀产物分布较为连续。由于界面区的铝合金处于“浸入-移出”海水的动态环境中,腐蚀坑内的腐蚀产物如Al3+随着试样移出水面,会随着水流方向流出蚀孔,遇到O2后会反应生成Al的氢氧化物和氧化物,因此导致水气界面区被一层白色腐蚀产物覆盖。全浸区也出现了白色腐蚀产物,但分布较为分散。当实验至第15 d,水气界面区和大气区交界处的盐沉积量明显增多,水气界面区的宏观腐蚀形貌变化不大,全浸区的点蚀数目增多。实验至第52 d,水气界面区和大气区交界处的NaCl盐沉积量增多,其他区域的宏观腐蚀形貌并无明显变化。
图10a和b为腐蚀54 d后2024铝合金试片不同区域的平均点蚀深度和点蚀密度统计结果。由图10a的结果可以看出,全浸区和水气界面区的点蚀深度为2~5 μm,且水气界面区的点蚀深度比溶液区的小。水气界面区的点蚀深度由下至上逐渐减小。低水线位置的点蚀深度没有显著突变,说明宏观电偶作用不明显。高水线位置上方由于盐沉积,点蚀深度增至约60 μm,高水线附近的宏观腐蚀电池作用明显,水线上方为阳极,下方为阴极。图10b的结果表明,全浸区的点蚀密度随着高度增加而增加,从234 mm-2增至612 mm-2。界面区的点蚀密度为119~250 mm-2,且随着高度增加有递减趋势。总体来看,全浸区的点蚀数量比界面区多,表明点蚀更容易萌生和发展。大气区由于腐蚀较为严重,点蚀密度无法进行统计。
图11给出了2024铝合金大气区、水气界面区和全浸区腐蚀54 d后的微观形貌。大气区主要观察的是盐层沉积物下的局部腐蚀情况,如图11a所示,其局部腐蚀较为严重。此区域由于盐度高,湿度大,因此腐蚀环境十分苛刻,铝合金的腐蚀电位较低,阴极反应不仅有O2还原,可能还有析氢反应(取决于蚀孔内部的电位是否低于析氢反应的过电位),蚀孔内部由于局部酸化,pH值降低,可导致析氢反应速率加快。图11b为水气界面区的微观腐蚀形貌,可以看出整个表面都有一层腐蚀产物,局部腐蚀产物发生了脱落。此外,图11b标出了界面区铝合金试样的上下移动方向,可以看出腐蚀产物在蚀孔下方有明显的“流动”痕迹(虚线圈出的区域),这主要是因为试样在向上移出水面的过程中,蚀孔内部腐蚀产生的Al3+流出蚀孔外部,并与O2反应生成Al的氧化物或氢氧化物。图11c和d为全浸区的微观腐蚀形貌,全浸区有部分区域没有明显的腐蚀产物,可以看出夹杂物在早期腐蚀过程中的作用。2024铝合金中的夹杂物主要有Al7Cu2Fe和AlCuFeMnSi相[26],Al元素在腐蚀过程中优先溶解,在夹杂物表面形成腐蚀产物;其他元素在腐蚀过程中因失去Al元素而发生重排,重新沉积在夹杂物表面,此时由于夹杂物表面电势高于周围基体,它们作为阴极相与基体之间发生微电偶腐蚀[27]。值得注意的是,夹杂物中Al的优先溶解是由原子级的脱合金化驱动的,而夹杂物周围基体的溶解则是由夹杂物与基体之间的微电偶效应驱动的。随着周围基体的溶解,在夹杂物与基体之间形成沟槽[28] (图11d)。随着腐蚀的进行,沟槽底部形成类似于点蚀的自催化环境,当腐蚀进行到一定程度时,夹杂物可以脱落[26]。
表1列出了图11中9个点的EDS分析结果。白色区域所在的位置O含量更高,说明白色区域主要是Al的氧化物和氢氧化物;深色区域O含量低,主要是表面腐蚀产物剥落之后的致密腐蚀层[29]。部分区域还存在少量的Si和Fe,主要来源于夹杂物。
2.5 水气界面与全浸区腐蚀行为的差异性
通过表面形貌观察和EIS、EN测试可以发现,水气界面区和全浸区腐蚀过程的主要差别在于O含量不同。水气界面区处于“浸入-移出”海水的动态环境中,移出水面后,其暴露于大气环境中,O含量较高;而且移出水面30 s的时间间隔内,其表面并未完全干燥,表面覆盖一层薄液膜,其腐蚀环境是高湿和高O含量的环境。在此环境下,铝合金腐蚀产物萌生较快,3 d后表面生成一层相对致密的腐蚀产物层,对腐蚀起了一定的抑制作用。由于铝合金表面不断生成新的腐蚀产物,在应力作用下会使上层的腐蚀产物部分脱落,耐蚀性有一定降低。但由于起始阶段生成的腐蚀产物膜层较为致密,对氧的传输扩散有一定阻碍作用,因此之后腐蚀产物膜层的生成速率减缓,第33 d阻抗模值达到最大值,而后阻抗模值有所减小。水气界面区蚀孔数量少且蚀孔小,说明在这一区域钝化膜即使易破裂,但点蚀萌生后发展比较缓慢。点蚀发展的必要条件是蚀孔内维持酸化条件,研究结果表明蚀孔内部的pH值可低至1~3[30]。蚀孔内的阳极反应和阴极反应如反应式(4)~(7)所示[31],阳极反应生成的Al3+会快速发生水解反应生成Al(OH)2Cl和H+[31],导致孔内产生酸性环境。蚀孔内的阴极反应除了H+还原以外(式(6)),还有O2的还原反应(式(7))[32]。由于界面区O浓度高,很容易通过扩散到达蚀孔内部,消耗H+,因此难以维持蚀孔内的酸化条件。
阳极反应:
阴极反应:
全浸区由于O含量较少,腐蚀产物生成速率较慢,蚀孔分布较为分散。另一方面,孔蚀一旦萌生,由于溶液中的O含量有限,不容易消耗H+,相比水气界面区较容易维持局部酸化的环境。因此,全浸区的蚀孔数量少,蚀孔作为阳极区,蚀孔周围的铝合金作为阴极区。
2.6 不同区域之间的宏观腐蚀电池效应
通过腐蚀电位测试可以看到,水气界面区的腐蚀电位和全浸区的腐蚀电位相差10 mV左右,因此低水线位置处存在宏观腐蚀电池效应。水线下方为阳极,水线上方为阴极。但由于电位相差的数值不大,耦合后的电偶电流数值较小。此外,宏观腐蚀电池效应只存在于低水线位置附近,因为水气界面区溶液电阻较大。因此,低水线位置对应的宏观腐蚀电池为氧浓差电池。邢佩等[33]研究了E690钢在不同O含量的NaCl溶液中的氧浓差腐蚀行为,结果表明阴阳极面积比和阴极区O含量都会影响氧浓差腐蚀过程,当阴阳极面积比c / a ≥ 4时,阴极区O含量是影响腐蚀过程的主要因素。关于水气界面区与全浸区的铝合金面积比是否对腐蚀有影响课题组正在进行研究。高水线位置附近也存在宏观腐蚀电池效应:高水线下方的电位较正;水线上方盐度大,几乎处于盐饱和的状态,而且湿度大,偶尔存在浪花飞溅,所以水线上方的腐蚀电位较负,通过SEM结果也可以看出此处发生了严重的局部腐蚀。因此,高水线上方为阳极,高水线下方为阴极,但高水线位置的宏观腐蚀电池主要为氯离子浓度引起的浓差电池,而不是氧浓差电池。
(1) 水气界面区随着铝合金浸入和移出水面,腐蚀电位呈现“下降-上升”的周期性波动,波动幅值为5~10 mV,腐蚀电位快速下降和上升的速率体现了局部腐蚀敏感性较大,缓慢下降和上升体现了由于腐蚀产物膜的覆盖作用导致局部腐蚀敏感性降低。
(2) EIS测试结果表明,水气界面区和全浸区的极化电阻均呈现先增大后减小趋势,表明界面区的腐蚀产物膜比全浸区的腐蚀产物膜耐蚀性好。界面区和全浸区的有效电容值差别不大,且均呈现先减小再增加的趋势。腐蚀前期由于界面区腐蚀产物的生成,导致表面膜的介电常数发生改变,因此有效电容值减小。后期由于腐蚀产物膜的脱落,有效电容值有所增大。
(3) EN测试结果表明,电流噪声的波动幅值及其PSD低频白噪声水平先减小后增大,表明局部腐蚀敏感性先减小后增大,电位噪声的PSD高频线性区斜率均小于-20 dB/dec,表明其腐蚀类型均为局部腐蚀。
(4) 动态水气界面区腐蚀产物呈连续分布特征,全浸区腐蚀产物分布较为分散,这主要是由于动态水气界面区O含量丰富以及腐蚀产生的Al3+流出蚀孔所致。
(5) 全浸区和水气界面区的点蚀深度为2~5 μm,高水线上方由于盐沉积,点蚀深度增至约60 μm。全浸区的点蚀密度随着高度增加而增加,从234 mm-2增至612 mm-2。界面区的点蚀密度为119~250 mm-2,且随着高度增加有递减趋势。与全浸区相比,界面区蚀孔数量少且尺寸小,说明在这一区域点蚀萌生后发展比较缓慢,主要是由于界面区O浓度高所致。
免责声明:本网站所转载的文字、图片与视频资料版权归原创作者所有,如果涉及侵权,请第一时间联系本网删除。
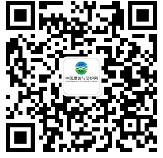
官方微信
《腐蚀与防护网电子期刊》征订启事
- 投稿联系:编辑部
- 电话:010-62316606-806
- 邮箱:fsfhzy666@163.com
- 腐蚀与防护网官方QQ群:140808414