失效分析定义
对装备及其构件在使用过程中发生各种形式失效现象的特征及规律进行分析研究,从中找出产生失效的主要原因及防止失效的措施,称为失效分析。
金属材料的失效形式及失效原因密切相关,失效形式是材料失效过程的表观特征,可以通过适当的方式进行观察。而失效原因是导致构件失效的物理化学机制,需要通过失效过程调研研究及对失效件的宏观、微观分析来诊断和论证。
失效分析与其他生产环节之间的关系
失效分析与其他学科的关系
失效分类
材料在各种工程应用中的失效模式主要由断裂、腐蚀、磨损和变形等,其中断裂失效的危害性最大。
失效形式的分类
弹性变形失效:当应力或温度引起材料可恢复的弹性变形大到足以影响装备正常发挥预定的功能时,就出现弹性变形失效。
塑性变形失效:当受载荷的材料产生不可恢复的塑性变形大到足以影响装备正常发挥预定的功能时,就出现塑性变形失效。
韧性断裂失效:材料在断裂之前产生显著地宏观塑性变形的断裂称为韧性断裂失效。
脆性断裂失效:材料在断裂之前没有发生或很少发生宏观可见的塑性变形的断裂称为脆性断裂失效。
疲劳断裂失效:材料在交变载荷作用下,经过一定的周期后所发生的断裂称为疲劳断裂失效。
腐蚀失效:腐蚀是材料表面与服役环境发生物理或化学的反应,使材料发生损坏或变质的现象,材料发生的腐蚀使其不能发挥正常的功能则称为腐蚀失效。腐蚀有多种形式,有均匀遍及材料表面的均匀腐蚀和只在局部地方出现的局部腐蚀,局部腐蚀又分为点腐蚀、晶间腐蚀、缝隙腐蚀、应力腐蚀开裂、腐蚀疲劳等。
磨损失效:当材料表现相互接触或材料表面与流体接触并作相对运动时,由于物理和化学的作用,材料表面的形状、尺寸或质量发生变化的过程,称为磨损。由磨损而导致构件功能丧失,称为磨损失效。磨损有多种形式,其中常见粘着磨损、磨料磨损、冲击磨损、微动磨损、腐蚀磨损、疲劳磨损等。
金属材料失效具体形式
失效原因分析
设计不合理
其中结构或形状不合理,材料存在缺口、小圆弧转角、不同形状过渡区等高应力区,未能恰当设计引起的失效比较常见。总之,设计中的过载荷、应力集中、结构选择不当、安全系数过小(追求轻巧和高速度)及配合不合适等都会导致构件及装备失效。构件及装备的设计要有足够的强度、刚度、稳定性,结构设计要合理。
分析设计原因引起的失效尤其要注意:对复杂构件未作可靠的应力计算;或对构件在服役中所承受的非正常工作载荷的类型及大小未作考虑;甚至于对工作载荷确定和应力分析准确的构件来说,如果只考虑拉伸强度和屈服强度数据的静载荷能力,而忽视了脆性断裂、低循环疲劳、应力腐蚀及腐蚀疲劳等机理可能引起的失效,都会在设计上造成严重的错误。
选材不当及材料缺陷
金属装备及构件的材料选择要遵循使用性原则、加工工艺性能原则及经济性原则,首先要考虑遵循使用性原则。使在特定环境中的构件,对可预见的失效形式要为其选择足够的抵抗失效的能力。如对韧性材料可能产生的屈服变形或断裂,应该选择足够的拉伸强度和屈服强度;但对可能产生的脆性断裂、疲劳及应力腐蚀开裂的环境条件,高强度的材料往往适得
其反。在符合使用性能的原则下选取的结构材料,对构件的成形要有好的加工工艺性能。在保证构件使用性能、加工工艺性能要求的前题下,经济性也是必须考虑。
制造工艺不合理
金属装备及其构件往往要经过机加工(车、铣、刨、磨、钻等)、热冷变形(冲、压、卷、弯等)、焊接、装配等制造工艺过程。若工艺规范制订不合理,则金属设备或构件在这些加工成形过程中,往往会留下各种各样的缺陷。如机加工常出现的圆角过小、倒角尖锐、裂纹、划痕;冷热成形的表面凹凸不平、不直度、不圆度和裂纹;在焊接时可能产生的焊缝表面缺陷(咬边、焊缝凹陷、焊缝过高)、焊接裂纹、焊缝内部缺陷(未焊透、气孔、夹渣),焊接的热影响区更因在焊接过程经受的温度不同,使其发生组织转变不同,有可能产生组织脆化和裂纹等缺陷;组装的错位、不同心度、不对中及强行组装留下较大的内应力等。所有这些缺陷如超过限度则会导致构件以及装备早期失效。
使用操作不当和维修不当
使用操作不当时金属装备失效的重要原因之一,如违章操作,超载、超温、超速;缺乏经验、判断错误;无知和训练不够;主观臆测、责任心不强、粗心大意等都是不安全的行为。某时期统计260 次压力容器和锅炉事故中,操作事故194 次,占74.5% 。装备是要进行定期维修和保养的,如对装备的检查、检修和更换不及时或没有采取适当的修理、防护措施,也会引起装备早期失效。
引起失效的原因分析
引起失效的常见缺陷
铸态金属组织缺陷
铸态金属常见的组织缺陷有缩孔、疏松、偏忻、内裂纹、气泡和白点等。
缩孔
金属在冷凝过程中由于体积的收缩而在铸锭或铸件心部形成管状(或喇叭状)或分散的孔洞,称为缩孔。缩孔的相对体积与与液态金属的温度、冷却条件以及铸件的大小等有关。液态金属的温度越高,则液体与固体之间的体积差越大,而缩孔的体积也越大。向薄壁铸型中浇注金属时,型壁越薄、则受热越快,液态金属越不易冷却,在刚浇完铸型时,液态金属的体积也越大,金属冷凝后的缩孔也就越大。
疏松
在急速冷却的条件下浇注金属,可避免在铸锭上部形成集中缩孔,但此时液体金属与固态金属之间的体积差仍保持一定的数值,虽然在表面上似乎已经消除了大的缩孔,可是有许多细小缩孔即疏松,分布在金属的整个体积中。
钢材在锻造和轧制过程中,疏松情况可得到很大程度的改善,但若由于原钢锭的疏松较为严重、压缩比不足等原因,则在热加工后较严重的疏松仍会存在。此外,当原钢锭中存在着较多的气泡,而在热轧过程中焊合不良,或沸腾钢中的气泡分布不良,以致影响焊合,亦可能形成疏松。
疏松的存在具有较大的危害性,主要有以下几种:(1)在铸件中,由于疏松的存在,显著降低其力学性能,可能使其在使用过程中成为疲劳源而发生断裂。在用作液体容器或管道的铸件中,有时会存在基本上相互连接的疏松,以致不能通过水压试验,或在使用过程中发生渗漏现象;(2)钢材中如存在疏松,亦会降低其力学性能,但因在热加工过程中一般能减少或消除疏松,故疏松对钢材性能的影响比铸件的小;(3)金属中存在较严重的疏松,对机械加工后的表面粗糙度有一定的影响。
偏析
金属在冷凝过程中,由于某些因素的影响而形成的化学成分不均匀现象称为偏析。偏析分为晶内偏析、晶间偏析、区域偏析、比重偏析。
由于扩散不足,在凝固后的金属中,便存在晶体范围内的成分不均匀现象,即晶内偏析。基于同一原因,在固溶体金属中,后凝固的晶体与先凝固的晶体成分也会不同,即晶间偏析。碳化物偏析是一种晶间偏析。
在浇注铸键(或铸件)时,由于通过铸型壁强烈的定向散热,在进行着凝固的合金内便形成一个较大的温差。结果就必然导致外层区域富集高熔点组元,而心部则富集低熔点组元,同时也富集着凝固时析出的非金属杂质和气体等。这种偏析称为区域偏析。
在金属冷凝过程中,如果析出的晶体与余下的溶液两者密度不同时,这些晶体便倾向于在溶液中下沉或上浮,所形成的化学成分不均匀现象,称为比重偏析。晶体与余下的溶液之间的密度差越大,比重偏析越大。这种密度差取决于金属组元的密度差,以及晶体与溶液之间的成分差。如果冷却越缓慢,随着温度降低初生晶体数量的增加越缓慢,则晶体在溶液中能自由浮沉的温度范围越大,因而比重偏析也越强烈。
气泡
金属在熔融状态时能溶解大量的气体,在冷凝过程中因溶解度随温度的降低而急剧减小,致使气体从液态金属中释放出来。若此时金属已完全凝固,则剩下的气体不易逸出,有一部分就包容在还处于塑性状态的金属中,于是形成气孔,则称其为气泡。
气泡的有害影响表现如下:(1)气泡减少金属铸件的有效截面,由于其缺口效应,大大降低了材料的强度;(2)当铸锭表面存在着气泡时,在热锻加热时可能被氧化,在随后的锻压过程中不能焊合而形成细纹或裂缝;(3)在沸腾钢及某些合金中,由于气泡的存在还可能产生偏析导致裂缝。
白点
在经侵蚀后的横向截面上,呈现较多短小的不连续的发丝状裂缝;而在纵向断面上会发现表面光滑、银白色的圆形或椭圆形的斑点,这种缺陷称为白点。
白点最容易产生在镍、铬、锰作为合金元素的合金结构钢及低合金工具钢中。奥氏体钢及莱氏体钢中,从未发现过白点;铸钢中也可能发现白点,但极为罕见;焊接工件的熔焊金属中偶尔也会产生白点。白点的产生与钢材的尺寸也有一定的关系,横截面的直径或厚度小于30mm的钢材不易产生白点。
通常具有白点的钢材纵向抗拉强度与弹性极限降低并不多,但伸长率则显著降低,尤其是断面收缩率与冲击韧性降低得更多,有时可能接近于零。且这种钢材的横向力学性能比纵向力学性能降低得多。因此具有白点的钢材一般不能使用。
引起失效的常见缺陷
金属锻造及轧制件缺陷
粗大的魏氏体组织
在热轧或停锻温度较高时,由于奥氏体晶粒粗大,在随后冷却时的先析出物沿晶界析出,并以一定方向向晶粒内部生长,或平行排列,或成一定角度。这种形貌称为魏氏体组织。先析出物与钢的成分有关,亚共析钢为铁素体,过共析钢为渗碳体。魏氏体组织因其组织粗大而使材料脆性增加,强度下降。比较重要的工件不允许魏氏体组织存在。
网状碳化物及带状组织
对于工具钢,锻造和轧制的目的不但是使毛坯成型,更重要的是使其内部的碳化物碎化和分布均匀。
钢材表层脱碳
钢加热时,金属表层的碳原子烧损,使金属表层碳成分低于内层,这种现场称为脱碳,降低碳量后的表面层叫做脱碳层。脱碳层的硬度、强度较低,受力时易开裂而成为裂源。大多数零件,特别是要求强度高、受弯曲力作用的零件,要避免脱碳层。因此锻、轧的钢件随后应安排去除脱碳层的切削加工。
折叠
折叠通常是由于材料表面在前一道锻、轧中所产生的尖角或耳子,在随后的锻、轧时压入金属本身而形成。钢材表面的折叠,可采用机械加工的方法进行去除。
划痕
在生产、运输等过程中,钢材表面受到机械刮伤形成的沟痕,称为划痕,也叫刮伤或擦伤。划痕缺陷的存在,能降低金属的强度;对薄钢板,除降低强度外,还会像切口一样地造成应力集中而导致断裂;尤其在压制时,它会成为裂纹或裂纹扩展的中心。对于压力容器来说,表面是不允许有严重的划痕存在的,否则会成为使用过程中发生事故的起点。
斑疤
金属锭及型材的表面由于处理不当,往往会造成粗糙不平的凹坑。这些凹坑是不深的, 一般只有2 ~3mm。因其形状不规则,且大小不一,故称这种粗糙不平的凹坑为结疤,也称为斑疤。
若结疤存在于板材上,尤其是主薄板上,则不仅能成为板材腐蚀的中心,在冲制时还会因此产生裂纹。此外,在制造弹簧等零件用的钢材上,是不允许存在结疤缺陷的。因为结疤容易造成应力集中,导致疲劳裂纹的产生,大大地影响弹簧的寿命和安全性。
表面裂纹
钢材表面出现的网状龟裂或缺口,是由于钢中硫高锰低引起热脆,或因铜含量过高、钢中非金属夹杂物过多所致。
分层
由于非金属夹杂、未焊合的内裂纹、残余缩孔、气孔等原因,使剪切后的钢材断面呈黑线或黑带,将钢材分离成两层或多层的现象,称为分层。
引起失效的常见缺陷
夹杂物及其对钢性能的影响
(1)夹杂物的分类
钢在加工变形中,各类夹杂物变形性不同,按其变形能力分为三类:
脆性夹杂物
一般指那些不具有塑性变形能力的简单氧化物(Al2O3、Cr2O3、ZrO2等)、双氧化物(如FeO·Al2O3、MgO·Al2O3、CaO·6 Al2O3)、碳化物(TiC)、氮化物(TiN、Ti(CN)AlN、VN等)和不变形的球状或点状夹杂物(如球状铝酸钙和含SiO2较高的硅酸盐等)。
钢中铝硅钙夹杂物具有较高的熔点和硬度,当压力加工变形量增大时,铝硅钙被压碎并沿着加工方向而呈串链状分布,严重破坏了钢基体均匀的连续性。
塑性夹杂物
这类夹杂物在钢经受加工变形时具有良好的塑性,沿着钢的流变方向延伸成条带状,属于这类的夹杂物含SiO2量较低的铁锰硅酸盐、硫化锰(MnS)、(Fe, Mn)S等。夹杂物与钢基体之间的交界面处结合很好,产生裂纹的倾向性较小。
半塑性变形的夹杂物
一般指各种复合的铝硅酸盐夹杂物,复合夹杂物中的基体,在热加工变形过程中产生塑性变形,但分布在基体中的夹杂物(如CaO·Al2O3、尖晶石型的双氧化物等)不变形,基体夹杂物随着钢基体的变形而延伸,而脆性夹杂物不变形,仍保持原来的几何形状,因此将阻碍邻近的塑性夹杂物自由延伸,而远离脆性夹杂物的部分沿着钢基体的变形方向自由延伸。
(2)夹杂物对钢性能的影响
大量试验事实说明夹杂物对钢的强度影响较小,对钢的韧性危害较大,其危害程度又随钢的强度的增高而增加。
夹杂物变形性对钢性能的影响
钢中非金属夹杂物的变形行为与钢基休之间的关系,可用夹杂物与钢基体之间的相对变形量来表示,即夹杂物的变形率v ,夹杂物的变形率可在v=0~1这个范围受化,若变形率低,钢经加工变形后。由于钢产生塑性变形,而夹杂物基本不变形,便在夹杂物和钢基体的交界处产生应力集中,导致在钢与夹杂物的交界处产生微裂纹,这些微裂纹便成为零件在使用过程中引起疲劳破坏的隐患。
夹杂物引起应力集中
夹杂物的热膨胀系数越小,形成的拉应力越大,对钢的危害越大。在高温下加工变形时,夹杂物与钢基体热收缩的差别,使裂纹在交界面处产生。它很可能成为留住基体中潜在的疲劳破坏源。危害性最大的夹杂物是来源于炉渣和耐火材料的外来氧化物。
夹杂物与钢的韧性
超高强度钢和碳钢中MnS夹杂物的含量对强度无明显影响,但可使韧性降低。其中断裂韧性随硫含量增加而降低,具有明显的规律性。
从夹杂物类型比较,硫化物对韧性的影响大于氮化物,在氮化物中ZrN 对韧性的危害较小,夹杂物类型不同而含量相近的情况下,变形成长条状的MnS对断裂韧性影响大于不变形的硫化物(Ti-S , Zr-S) 。
串状或球状硫化物对ψ和A kV 均不利,就对短横试样的危害而言,串状比球状危害更严重。
引起失效的常见缺陷
金属焊接缺陷
焊接缺陷的种类很多,按其在焊缝中所处的位置可分为外部缺陷和内部缺陷两大类。外部缺陷也叫外观缺陷。外部缺陷位于焊缝表面,借用肉眼或低倍放大镜就能观察到。内部缺陷位于焊缝的内部,必须应用破坏性检验或专门无损检验方法才能发现。
焊接缺陷分类
焊接区域示意图
焊缝尺寸不符合要求
焊缝尺寸不符合要求包括:焊缝外形高低不平、焊道宽窄不齐、焊缝余高过大或过小、焊缝宽度太宽或太窄、焊缝和母材之间的过渡不平滑等。
原因分析:(1)焊缝坡口角度、宽度及组装间隙不统一。(2)焊条直径选择不当,造成填充层过高,失去坡口轮廓线,使盖面宽窄不一,焊缝过高,波纹粗劣。(3)背面清根刨缝质量差,焊道宽度不一。(4)焊接电流过大或过小,运条手法和角度不当以及焊速不均匀。
危害性:尺寸过小的焊缝,会降低焊接接头的强度;尺寸过大的焊缝,不仅浪费焊接材料,也会增大焊接结构的变形。焊缝金属向母材的过渡处若不平滑,出现尖角,会造成应力集中,降低焊接结构的承载能力。
预防措施:(1)采用自动和半自动切割机或刨边机加工坡口。(2)焊缝组对间隙应控制在标准规范要求值以内,背面用碳弧气刨清根后,采用砂轮修整刨槽及碳化层,使刨槽宽窄一致。(3)选用适当的焊接电流和焊条直径,遵守焊接工艺,熟练掌握操作技术,保持焊速均匀;手工焊操作人员要熟练地掌握运条速度和焊条角度,以获得成形美观的焊缝。
咬边
咬边也称“咬肉”,是电弧或火焰将焊缝边缘的母材熔化后,没有得到填充金属的补充,而留下的凹陷或凹槽。咬边是一种危险的缺陷,它不但减小了基本金属的有效工作截面,而且在咬边处还会造成应力集中。咬边又是一种常见的缺陷,应该特别引起注意。
焊瘤
熔化金属流淌到焊缝以外未熔化的母材上形成金属瘤。该处常伴有局部未熔合,有时也称满溢。习惯上,还常将焊缝金属的多余疙瘩部分称为焊瘤。焊瘤处应力集中,还易伴生裂缝等缺陷;焊瘤也破坏了焊缝平整光滑的外形,管子内部的焊瘸,除降低强度外,还减小管道的有效截面,造成堵塞观象。
原因分析:(1)坡口边缘污物未清理干净;电流过大,熔池温度过高,使液体金属凝固较慢,在自重的作用下下坠而成;焊接速度太慢以及组对间隙太大等。(2)运条角度不当,操作不熟练。焊速过慢也极易产生焊瘤。
预防措施:(1)焊接前应彻底清理坡口及其附近的脏物;组对间隙要合适;选择适当的焊接电流和运条角度,熟练掌握操作技术,保持焊速均匀。(2)碱性焊条采用短弧焊接,极性反接。
弧坑
弧坑是焊接时,由于断弧和收弧不当,在焊道末端形成的低洼部分,表面低凹深度大于0.5mm以上。弧坑低于基本金属表面,降低了焊接接头的承载能力,而且弧坑内常伴有气孔、夹渣、微裂纹等缺陷。
弧坑是由焊缝熔池金属未填足,熄弧过快或电流过大(薄板时)而造成。预防措施:收弧过程中,焊条要在收弧处作短暂的停留或作回焊运条,使电弧不要突然熄灭、使焊条金属填满熔池。
飞溅
手工焊接时,在焊缝及其两侧母材上产生一般性飞溅和严重性熔合飞溅。一般性飞溅是手工焊接常见的焊接质量通病;但产生严重性熔合性飞溅,其危害甚大,它会增加母材局部表面淬硬组织,易产生硬化发生脆裂及加速局部腐蚀性等缺陷。
弧疤
电弧擦伤也叫弧疤或弧斑,多是由于偶然不慎使焊条或焊把与焊接工件接触,或地线与工件接触不良短暂地引起电孤,而在焊接工件表面留下的伤痕,形成许多小圆孔和凹坑。
电弧擦伤处由于电弧的短暂引燃与急速熄灭,冷却速度快,在易淬火钢及低温钢的工件上,会形成脆性淬硬组织,可能成为脆性破坏的起源点。在不锈钢等有耐腐蚀性能要求的工件上,电弧擦伤会成腐蚀的起始点,降低材料的性能。
原因分析:操作不慎,使焊条或焊把裸露部分与非焊接部位接触,短暂地引起电弧,将母材表面擦伤,形成许多小圆孔和凹坑。
预防措施:(1)精心操作,避免带电的焊条或焊把裸露部分与非焊接区域母材相碰引起电弧。(2)不得在非焊接部位随意引弧或试电流,引弧应在引弧板上或在焊道破口内进行。(3)地线与母材应紧固良好。
气孔
气孔是焊接熔池中气体在凝固时未能逸出,而残留在焊缝中所形成的空穴。根据孔穴产生的部位,可分为外部气孔和内部气孔;根据分布情况,气孔又可分为单个气孔、连续气孔和密集气孔等。存在于焊缝内的气孔,减小了金属的有效截面,从而使焊接接头的强度降低;气孔的边缘可能发生应力集中,密集气孔使焊缝组织疏松,使接头的塑性降低;贯通性气孔破坏了焊缝的致密性,造成渗漏。焊缝中的氢气孔还有可能导致裂缝的产生和扩展。
夹渣
夹渣是焊后残留在焊缝中的熔渣,有的夹在焊缝内部,有的夹在表面沟槽内。
焊缝中的夹渣,降低了接头的承载能力,容易引起应力集中;影响了焊缝金属的致密性,还可能造成焊缝的渗漏,由于夹杂物与焊缝金属的线膨胀系数相差悬殊,温度剧烈变化时,有可能产生较大应力而导致裂缝。
未焊透
未焊透是焊接时接头根部未完全熔化而留下的间隙的现象。
未焊透降低了接头的机械性能,同时由于未焊透部位的缺口及末端会产生严重的应力集中,导致产生裂缝。
未熔合
未熔合是指焊缝金属和母材之间或焊道金属和焊道金属之间未完全熔化和结合的部分,它可以分为侧壁未熔合、层间未熔合和焊缝根部未熔合。
未熔合减少了接头承载的有效截面,降低了机械强度。
裂纹
在焊缝或近缝区,由于焊接的影响,材料的原子结合遭到破坏,形成新的界面而产生的缝隙称为焊接裂缝,它具有缺口尖锐和长宽比大的特征。
裂缝按其产生的部位可分为纵向裂缝、横向裂缝、弧坑裂缝、根部裂缝、熔合区裂缝及热影响区裂缝等,按其产生的温度和时间,又可分为热裂缝、冷裂缝和再热裂缝。
热裂纹在高温下产生,而且都是沿奥氏体晶界开裂。
焊缝在结晶过程中,固相线附近由于凝固金属收缩时,残余液相不足,致使沿晶界开裂,故称结晶裂纹。结晶裂纹主要出现在含杂质较多的碳钢焊缝中(特别是含硫、磷、硅、碳较多的钢种焊缝)和单相奥氏体钢、镰基合金,以及某些铝及铝合金的焊缝中。
高温裂纹是指在焊接热循环峰值温度作用下,母材近峰区和多层焊缝的层间金属中,由于含有低熔共晶组成物(如S、P、Si、Ni等)而被重新熔化,在收缩应力作用下,沿奥氏体晶间发生开裂。
多边化裂纹:焊接时焊缝或近缝区在固相线温度以下的高温区间,由于刚凝固的金属存在很多晶格缺陷(主要是位错和空位)和严重的物理及化学的不均匀性,在一定的温度和应力作用下,由于晶格缺陷的移动和聚集,便形成了二次边界,即“多边化边界”,边界上堆积了大量的晶格缺陷,造成组织疏松,高温时的强度和塑性都很低,只要受少量的拉伸变形,就会沿着多边化边界开裂,产生多边化裂纹,又称高温塑性裂纹。这种裂纹多发生纯金属或单向奥氏体合金的焊缝中或近缝区。
再热裂纹:在进行消除应力热处理的过程中,在焊接热影响区的粗晶部位产生裂纹,在重新加热(热处理)过程中产生的这种裂纹称为再热裂纹,也即双裂纹。
在消除应力热处理过程中,热影响区的粗晶区存在不同程度的应力集中,由于应力松弛所产生附加变形大于该部位的蠕变塑性,则产生再热裂纹。再热裂纹与热裂纹虽然都是沿晶界开裂,但是再热裂纹产生的本质与热裂纹根本同,再热裂纹只在一定的温度区间(约550~650℃)敏感,而热裂纹是发生在国相线附近。再热裂纹多发生在低合金高强钢、珠光体耐热钢、奥氏体不锈钢,以及镍基合金的焊接接头中。
冷裂纹
冷裂纹是指在焊接接头冷却到较低温度时(对于钢来说在MS温度,即奥氏体开始转变为马氏体的温度以下)所产生的焊接裂纹。焊接冷裂纹包括淬硬脆化裂纹、延迟裂纹、低塑性脆化裂纹。
最主要的冷裂纹为延迟裂纹(即在焊后延迟一段时间才发生的裂纹,因为氢是最活跃的诱发因素,而氢在金属中扩散、聚集和诱发裂纹需要一定的时间)。
淬硬倾向大的钢在焊接热循环作用下产生淬硬组织,在应力作用下产生裂纹。产生裂纹的敏感温度在Ms附近,焊接接头冷却到一定温度以下即出现裂纹,没有延迟开裂特征。一些超高强度钢、马氏体不锈钢、工具钢具有较高的淬硬脆化裂纹敏感性。一些超高强度钢、马氏体不锈钢、工具钢具有较高的淬硬脆化裂纹敏感性。
低塑性催化裂纹是指在被焊母材或焊缝金属本身塑性过低,在焊接热应力和拘束应力作用下,发生的应变大于其延性而产生的裂纹。低塑性脆化裂纹在焊接接头冷却到一定温度以下即出现,多出现在焊缝和热影响区表面,没有延迟特征。铸铁、硬质合金堆焊容易产生低塑性脆化裂纹,高合金化钛合金、钛铝金属间化合物等航空材料也容易产生这类裂纹。
Ti3Al合金焊接结构低塑性脆化裂纹
层状撕裂
层状撕裂属低温开裂,撕裂温度不超过400 0C 。层状撕裂与一般的冷裂纹不同, 它主要是由于轧制钢材的内部存在有分层的夹杂物(特别是硫化物夹杂物)和在焊接时产生的垂直轧制方向的应力, 致使焊接热影响区附近或稍远的地方产生呈“台阶”状的层状开裂,并具有穿晶发展。
层状撕裂主要发生在屈服强度较高的低合金高强钢(或调质钢)的厚板结构,如采油平台、厚壁容器、潜艇等,且材质含有不同程度的夹杂物。层状撕裂在T形接头,十字接头和角接头比较多见。
金属热处理产生的组织缺陷
金属热处理缺陷指在热处理生产过程中产生的使零件失去使用价值或不符合技术条件要求的各种补助,以及使热处理以后的后续工序工艺性能变坏或降低使用性能的热处理隐患。
最危险的缺陷为裂纹,其中最主要的是淬火裂纹,其次是加热裂纹、延迟裂纹、冷处理裂纹、回火裂纹、时效裂纹、磨削裂纹和电镀裂纹等。
导致淬火裂纹的原因:(1)原材料已有缺陷(冶金缺陷扩展成淬火裂纹);(2)原始组织不良(如钢中粗大组织或魏氏组织倾向大);(3)夹杂物;(4)淬火温度不当;(5)淬火时冷却不当;(6)机械加工缺陷;(7)不及时回火。
最常见的缺陷是变形,其中淬火变形占多数,产生的原因是相变和热应力。
残余应力、组织不合格、性能不合格、脆性及其他缺陷发生的频率和严重性较低。
内应力来源有两个方面:(1)冷却过程中零件表面与中心冷却速率不同、其体积收缩在表面与中心也不一样。这种由于温度差而产生的体积收缩量不同所引起的内用力叫做“热应力”;(2)钢件在组织转变时比体积发生变化,如奥氏体转变为马氏体时比体积增大。由于零件断面上各处转变的先后不同,其体积变化各处不同,由此引起额内应力称作“组织应力”。
金属材料常见失效形式及其判断
金属材料在各种工程应用中的失效模式主要由断裂、腐蚀、磨损和变形等。
变形失效
在常温或温度不高的情况下的变形失效主要由弹性变形失效和塑性变形失效。弹性变形失效主要是变形过量或丧失原设计的弹性功能,塑性失效一般是变形过量。在高温下的变形失效有蠕变失效和热松弛失效。
应力-应变曲线
1 弹性变形失效
在弹性状态下,固体材料吸收了加载的能量,依靠原子间距的变化而产生变形,但因未超过原子之间的结合力,当卸裁时,全部能量释放,变形完全消失,恢复材料的原样。要有好的弹性,应从提高材料的弹性极限及降低弹性模量入手。
金属弹性形变的特点:(1)可逆性,金属材料的弹性变形具有可逆的性质,即加载时,卸载后恢复到原状的性质;(2)单值性,金属材料在弹性变形过程中,不论是加载阶段还是卸载阶段,只要在缓慢的加载条件下,应力与应变都保持正比的单值对应的线性关系,即符合胡克定律;(3)变形量很小,金属的弹性变形主要发生在弹性阶段,但在塑性阶段也伴随着发生定量的弹性交形。但两个阶段弹性变形的总量是很小的,加起来一般小于0.5%-1.0 %。
构件产生的弹性变形量超过构件匹配所允许的数值,称为过量的弹性变形失效,判断方法如下:(1)失效的构件是否有严格的尺寸匹配要求,是否有高温或低温的工作条件;(2)注意观察在正常工作时,构件互相不接触,而又很靠近的表面上是否有划伤、擦伤或磨损的痕迹。只要观察到这种痕迹,而且构件停工时,构件相互间仍有间隙,便可作为判断的依据;(3)在设计时是否考虑了弹性变形的影响及采取了相应的措施;(4)通过计算验证是否有过量弹性变形的可能;(5)由于弹性变形是晶格的变形,可用X射线法测量金属在受载时的晶格常数的变化验证是否符合要求。
当构件的弹性变形已不遵循变形可逆性、单值对应性及小变形量的特性时,则构件失去了弹性功能而失效。
过载、超温或材料变质是构件产生弹件变形失效的原因,预防措施如下:(1)选择合适的材料或构件结构;(2)确定适当的构件匹配尺寸或变形的约束条件,对于拉压变形的杆柱类零件、弯扭变形的轴类零件,其过量的弹性变形都会因构件丧失配合精度导致动作失误,要求精确计算可能产生的弹性变形及变形约束而达到适当的配合尺寸;(3)采用减少变形影响的连接件,如皮带传动、软管连接、柔性轴、椭圆管板等。
2 塑性变形失效
塑性表示材料中的应力超过屈服极限后,能产生显著的不可逆变形而未立即破坏的形态,这种显著且不可逆的变形称为塑性变形。通常反映材料塑性性能优劣的指标是伸长率δ和断面收缩率φ。伸长率和断而收缩率越高,则塑性越好。金属的塑性变形一般可看作是晶体的缺陷运动。
金属塑性变形的特点:(1)不可逆性,金属材料的塑性变形不可恢复,当材料应力等于或高于屈服极限后产生的变形,在卸裁后,其变形仍然保留在材料内。塑性变形的微观机制表明,位错运动及增殖使晶体实现一个晶面在另一个晶面上的逐步滑移,宏观表面是卸载后塑性变形保留至可观察及测量;(2)变形量不恒定,金属是多晶体,各个晶粒取向不同,晶面滑移先后不同,各晶粒变形有不同时性及不均匀性。一个构件在各个部位的塑性变形量不相同,因而个别塑性变形量大的部位将出现材料的不连续(断裂失效的裂源);(3)慢速变形,金属的弹性变形以声速传播,但塑性变形的传播很慢;(4)伴随材料性能的变化,这主要因为塑性变形时金属内部组织结构发生变化,由位错运动及增殖实现了晶面的滑移,亚晶结构形成;晶粒歪扭,微裂纹等缺陷产生;如在材料加工中,随塑性交形量增加,即产生了加工硬化,原因是位错密度增加、位错缠结、位错运动相互作用及运动阻力增加,其宏观表现就是应变硬化。
金属构件产生的塑性变形量超过允许的数值称为塑性变形失效,其变形失效判断以影响构件执行正常功能为依据。
材料塑性变形失效的主要原因是过载,使构件的受力过大,出现影响构件使用功能的过量的塑性变形。过载不仅是对构件承受的外载荷估计不足,还应该包括偏载引起局部应力、复杂结构应力计算误差及应力集中、加工及热处理产生残余应力、材料微观不均匀的附加应力等因素,使构件受力不均,局部区域的总应力超值。
塑性变形失效预防措施:(1)合理选材,提高金属材料抵抗塑性变形的能力,除了选择合适的屈服强度的材料,还要保证金属材料质量,控制组织状态及冶金缺陷;(2)准确地确定构件的工作载荷,正确进行应力计算,合理选取安全系数及进行结构设计,减少应力集中及降低应力集中水平;(3)严格按照加工工艺规程对构件成形,减少残余应力;(4)严禁构件运行超载;(5)监测腐蚀环境构件强度尺寸的减小。
3 高温作用下金属材料的变形失效
金属构件在高温长时间作用下,即使其应力值小于屈服强度,也会缓慢产生塑性变形,当该变形量超过规定的要求时,会导致构件的塑性变形失效。此时所称的高温为高于0.3Tm(Tm是以绝对温度表示的金属材料的熔点),一般情况下碳钢构件在300℃以上,低合金强度钢构件在400℃以上。
蠕变变形失效
金属在长时间恒温、恒载荷(即使应力小于该温度下的屈服强度)作用下缓慢地产生塑性变形的现象称为蠕变。由蠕变变形导致的材料的断裂,称为蠕变断裂。由蠕变变形和断裂机理可知,要提高蠕变极限,必须控制位错攀移的速率;提高持久强度,则必须控制晶界的滑动和空位扩散。
压力容器的蠕变变形量一般规定在105h为1%,即蠕变速率为10-7 mm/(mm·h)。
典型的蠕变曲线
第一阶段ab为减速蠕变阶段又称过渡蠕变阶段,这一阶段开始的蠕变速率很大,随着时间延长蠕变速率逐渐减小,到b点蠕变速率达到最小值;
第二阶段bc为恒速蠕变阶段又称稳态蠕变阶段,这一阶段的特点是蠕变速率几乎保持不变。一般所指的金属蠕变速率,就是以这一阶段的蠕变速率ε表示的。
第三阶段cd为加速蠕变阶段随着时间的延长,蠕变速率逐渐增大,到d点时产生蠕变断裂。
断口宏观特征
断口附近产生塑性变形,在变形区附近有很多裂纹(断裂机件表面出现龟裂现象);
高温氧化,断口表面被一层氧化膜所覆盖。
断口微观特征
冰糖状花样的沿晶断裂形貌
蠕变变形失效也是一种塑性变形失效,有塑性变形失效的特点,但蠕变失效也不一定是过载,只是载荷大时,蠕变变形失效的时间短,恒速蠕变阶段蠕变速度大。高温下不仅有蠕变变形引起的的构件外部尺寸的变化,还有金属内部组织结构特有的变化,导致高温力学性能下降、构件承载能力降、蠕变速度加快、失效加快。
材料的蠕变性能常采用蠕变极限、持久强度、松弛稳定性等力学性能指标。
蠕变极限是金属材料在高温长时载荷作用下的塑性变形抗力指标,是高温材料、设计高温下服役机件的主要依据之一。蠕变极限(MPa)表示方法有两种,一种是在规定温度下,使试样在规定时间内产生规定稳态蠕变速率的最大应力;另一种是在规定温度和时间下,使试样在规定时间内产生规定蠕变伸长率的最大应力。
持久强度是指材料在高温长时载荷作用下抵抗断裂的能力,即材料在一定温度和时间条件下,不发生蠕变断裂的最大应力(蠕变极限指材料的变形抗力,持久强度表示材料的断裂抗力)。某些材料与机件,蠕变变形很小,只要求在使用期内不发生断裂(如锅炉的过热蒸汽管)。这时,就要用持久强度作为评价材料、机件使用的主要依据。
应力松弛变形失效
材料在恒变形条件下,随着时间的延长,弹性应力逐渐降低的现象称为应力松弛。金属材料抵抗应力松弛的性能称为松弛稳定性,可以通过应力松弛试验测定的应力松弛曲线来评定。剩余应力是评定金属材料应力松弛稳定性的指标。剩余应力越高,松弛温度性越好。
金属的蠕变是在应力不变的条件下,构件不断产生塑性变形的过程;而金属的松弛守则是在总变形不变的条件下,构件弹性变形不断转为塑性变形从而使应力不断降低得过程。
第1阶段:开始阶段应力下降很快;
第2阶段:应力下降逐渐减缓的阶段;
松弛极限:在一定的初应力和温度下,不再继续发生松弛的剩余应力。
预防高温松弛失效的措施是选用松弛稳定性好的材料。对紧固性构件的实际使用也可以在构件使用过程中对其进行一次或多次再紧固,即在构件应力松弛到一定程度时重新紧固,这是经济而又有效的方法。但要注意到再紧固会对松弛性能有所影响,因为每进行一次再紧固,材料都产生应变硬化,剩余应力有所下降,随着塑性应变的总量增加,材料最终断裂。
断裂失效
断裂是金属材料在应力作用下材料分离为互不相连的两个或多个部分的现象。
金属材料的断裂过程一般有三个阶段, 即裂纹的萌生,裂纹的亚稳扩展及失稳扩展,最后是断裂。金属构件可能在材料制造、构件成形或使用阶段的不同条件下启裂、萌生裂纹;并受不同的环境因素及承载状态的影响而使裂纹扩展直至断裂。
金属构件断裂后,在断裂部位都有匹配的两个断裂表面,称为断口。断口及其周围留下与断裂过程有密切相关的信息。通过断口分析可以判断断裂的类型、断裂过程的机理,从而找出断裂的原因和预防断裂的措施。
1 断裂失效的分类
按断裂前变形程度分类,分为韧性断裂和脆性断裂。
韧性断裂前产生明显的塑性变形,断裂过程中吸收了较多的能力,一般是在高于材料屈服应力条件下的高能断裂。
脆性断裂前的变形量很小,不会出现明显的宏观变形量。断裂过程中材料吸收的能量很小,一般是在低于允许应力条件下的低能断裂。通常材料的塑性变形小于2%~5%的断裂均可称为脆性断裂。
(a)完全韧性断裂(b)部分韧性断裂(c)脆性断裂
按造成断裂的应力类型及断面的宏观取向与应力的相对位置分类,可分为正断、切断及混合断裂。正断可能是脆性的,也可能是韧性的,而切断一般总是韧性的。
正断是指当外加作用力引起构件的正应力分量超过材料的正断抗力时发生的断裂。断裂面垂直于正应力或最大的拉伸应变方向。
切断是指当外加作用力引起构件的切应力分量超过材料在滑移面上的切断抗力时发生的断裂。断裂面平行于最大切应力或最大切应变方向,与最大正应力约呈45°交角。
按断裂过程中裂纹扩展所经的途径分为三类:沿晶断裂、穿晶断裂及混晶断裂。
沿晶断裂是指裂纹沿晶界扩展至断裂,沿晶断裂多属于脆性断裂。
穿晶断裂是指裂纹的萌生和扩展穿过晶粒内部的断裂。穿晶断裂可以是韧性的也可以是脆性的。混晶断裂是指在多晶体金属材料的断裂过程中,多数是其裂纹的扩展既有穿晶型、也有晶间型的混晶断裂。如马氏体或回火马氏体材料的瞬间断裂。
裂纹扩展路径示意图
A-沿晶裂纹;B-穿晶裂纹;C-混晶裂纹
按负荷的性质及应力产生的原因分为疲劳断裂和环境断裂。
疲劳断裂是指由于在局部应力集中或强度较低部位首先产生裂纹,裂纹随后扩展导致的断裂。
环境因素(气相、液相腐蚀介质或氢)的作用引起形变和断裂的基元过程,从而导致应力脆断,因而以这种形式破坏失效的现象统称为环境断裂。环境断裂具体可分为应力腐蚀开裂(Stress Corrosion Cracking)、氢脆或氢致开裂(Hydrogen Induced Cracking)和腐蚀疲劳断裂(Corrosion Fatigue Cracking)三种。
按微观断裂机制可分为解理断裂、韧窝断裂、疲劳断裂、蠕变断裂及结合力弱化断裂。
解理断裂是在正应力作用产生的一种穿晶断裂,裂纹沿特定的结晶学平面扩展而导致的穿晶脆断,但有时也可沿滑移面或孪晶界分离。解理断裂常见于体心立方和密排六方金属及合金,低温、冲击载荷和应力集中常促使解理断裂的发生。面心立方金属很少发生解理断裂。
韧窝断裂是指在外力作用下因微孔聚集相互连通而造成的断裂。结合力弱化断裂是指裂纹沿着出于各种原因而引起的结合力弱化所造成的脆弱区域扩展而形成的断裂。
韧窝
沿晶断裂
2 韧性断裂
韧性断裂是指容器、管道在压力作用下,器壁上产生的应力超过材料的强度极限而发生显著的宏观塑性变形的断裂。
韧性断裂是一个缓慢的断裂过程,塑性变形与裂纹成长同时进行。裂纹萌生及亚稳扩展阻力大、速度慢,材料在断裂过程中需要不断消耗相当多的能量。随着塑性变形的不断增加,承载截面积减小,至材料承受的载荷超过了强度极限σb 时,裂纹扩展达到临界长度,发生韧性断裂。
韧性断裂有两种类型: 一种是宏观断面取向与最大正应力相垂直的正断型断裂,又称平面断裂,这种断裂出现在形变约束较大的场合,如平面应变条件下的断裂;另一种是攻关断面取向与最大切应力方向相一致的切断,即与最大正应力约呈45°,又称斜断裂,这种断裂出现在滑移形变不受约束或约束较小的情况,如平面应力条件下的断裂。
韧性断裂断口形貌
(1)宏观形貌
韧性断裂断口宏观形貌
在直径大的圆棒钢试样新断裂的金属灰色断口上能观察三个区:凹凸不平暗灰色且无光泽的纤维区、放射线纹理的灰色有光放射区及平滑丝光的亮灰色剪切唇区。
纤维区是材料内部处在平面应变三向应力作用下启裂,在试样中心形成很多小裂纹及裂纹缓慢扩展而形成。
纤维区外显示出平行于裂纹扩展的放射线状的纹理,这是中心裂纹向四周放射状快速扩展的结果,该区称为放射区。
当裂纹快速扩展到试样表面附近,由于试样剩余厚度很小,故变为平面应力状态,从而剩余的外围部分剪切断裂,断裂面沿最大切应力面和拉伸轴成45°,称为剪切唇区。
从韧性断裂宏观形貌三区的特征可分析断口的类型、断裂的方式及性质,有助于判断失效的机理及找出失效的原因。根据纤维区、放射区及剪切唇区在断口上所占的比例可初步评价材料的性能。如纤维区较大,材料的塑性和韧性比较好,如放射区比较大,则材料的塑性降低,而脆性增大。
断口三要素
1-纤维区 F;2-放射区 R;3-剪切区S
(2)微观形貌
滑断或纯剪切断口微观特征:(1)蛇形滑动、涟波状花纹;(2)大的塑性变形后滑移面分离造成;(3)涟波花样是蛇形滑动花样一步变形而平滑化的结果;(4)在缺口、纤维裂纹、孔洞等附近区域在力的作用下可发生纯剪切过程,其内表面出现蛇行滑动、涟波等特征。
在某些金属材料中,尤其是杂质、缺陷少的金属材料,在较大的塑性变形后,沿滑移面剪切分离,因位向不同的晶粒之间的互相约束和牵制,不可能仅仅沿某一个滑移面滑移,而是沿着许多相互交叉的滑移面滑移,形成起伏弯曲的条纹形貌,一般称为“蛇行花样”。
微孔聚集型断裂的微观特征:断口上有大量韧窝。材料在塑性变形时,在夹杂物、析出物等第二相粒子周围或有缺陷地区先出现裂纹,形成微孔,进一步塑性变形时,微孔长大、聚集、断裂。
韧窝是指韧性断裂断口的微观形貌呈现出韧窝状,在韧窝的中心常有夹杂物或第二相质点。根据受力状态的不同,通常可以出现三种不同形态的韧窝:
(1)在正应力(即垂直于断面的最大主应力)的均匀作用下,显微孔洞沿空间三个方向上的长大速度相同,因而形成等轴韧窝。拉伸试样断口的杯形底部和锥形顶部由等轴韧窝组成;
(2)在切应力(平行于断面的最大切应力)的作用下,塑性变形使显微孔洞沿切应力方向的长大速度达到最大,同时显微孔被拉长, 形成抛物线状或半椭圆状的韧窝,这时两个的韧窝朝着相反方向,这种韧窝称为剪切韧窝。剪切韧窝通常出现在拉伸断口的剪切唇区。
(3)撕裂应力作用下出现伸长或呈抛物线状的韧窝,两个匹配面上的韧窝朝着相同的方向,称为撕裂韧窝。撕裂韧窝的方向指向裂纹源,而其反方向则是裂纹的扩展方向。剪切韧窝与撕裂韧窝的区别在于对应的两个断面上,其抛物线韧窝的方向不同,对剪切韧窝凸向相反,对撕裂韧窝凸向相同。
韧窝的大小和深浅,决定于材料断裂时微孔的核心数量和材料本身的相对塑性,如果微孔的核心数量很多或材料的相对塑性较低,则韧窝的尺寸较小或较浅;反之,韧窝的尺寸较大或较深。通常韧窝越大越深,材料的塑性越好。韧窝尺寸与夹杂物的大小直接相关,而正当夹杂物呈圆颗粒时,韧窝呈等轴状,当夹杂物呈条状时,韧窝也呈长条形。
当材料含有较多的第二相质点或夹杂物时,则在形成韧窝过程中,第二相质点或夹杂物往往存在于韧窝底部,形成的韧窝数量较多,而且较小。
产生韧性断裂的影响因素:(1)零件形状(圆形、板状、光滑与缺口试样);(2)温度(随温度的降低,纤维区和剪切唇区减小,放射区增大);(3)加载速率(速率越大,放射区增大)。
3 脆性断裂
脆性断裂是指容器在破裂时没有宏观塑性变形,器壁平均应力远没有达到材料的强度极限,有的甚至低于屈服极限。脆性断裂的发生条件:设备、容器本身存在缺陷或几何形状发生突变;存在一定的应力水平;材料的韧性很差。
脆性断裂的特征
(1)脆性断裂时,工作应力不高,往往低于材料的屈服点,甚至低于设计时的许用应力。
(2)中、低强度钢的脆性断裂一般在比较低的温度下发生,因此脆性断裂也称为“低温脆性断裂”。与面心立方金属比较,体心立方金属随温度的下降,塑性将明显下降,屈服力升高;
(3)脆性断裂从金属构件内部存在的裂纹作为裂纹源而开始。
(4)脆性断裂通常在体心立方和密排六方金属材料中出现,而面心立方金属材料在特定的条件下才会出现脆性断裂;
(5)脆性断裂一般沿低指数晶面穿晶解理。解理通过破坏原子的结合力来实现,而密排面之间的原子间隙最大,结合力最弱,故绝大多数解理面是原子密排面。
(6)破裂时无明显的塑性变形,破裂之前没有或只有局部极小的塑性变形;
(7)断口宏观分析呈金属晶粒状并有光泽,断口平直与主应力垂直;
(8)在较低温度发生,且材料韧性很差。
脆性断裂的断口形貌
(1)宏观形貌
断裂前无明显的塑性变形,断口附近无颈缩;
断裂表面垂直于最大正应力方向;
断口平齐,无剪切唇;
断口上呈现小刻面;
断裂源点形成“人字条纹”或“山形条纹”
小刻面是指脆性解理断裂的断口呈平滑明亮结晶状。
根据断口人字条纹或山行条纹的图形可判断脆性断裂的裂纹扩展方向和寻找断裂起源点。人字条纹或山行条纹从细变粗的方向为裂纹扩展方向,相反的方向指向裂纹起源点。
(2)微观形貌
脆性断裂的微观形貌一般分为河流花样、扇形花样、舌状断口、鱼骨状花样;
河流花样实际上是断裂面上的微小解理台阶在图像上的表现,河流条纹就是相当于各个解理平面的交割。河流条纹的流向也是裂纹扩展的方向,河流的上游是裂纹源。
扇形花样:以裂纹源为中心单方向径向扩展,在焊接区冲击断口常见。
舌状花样:当材料的脆性大、温度低,临界变形困难,晶体变形以形变孪晶方式进行。舌状花样在低温冲击断口中易出现。
脆性断裂的影响因素
(1)应力状态与缺口效应
应力状态是指构件内应力的类型、分布、大小和方向。不同的应力状态对脆性断裂有不同的影响,如最大拉伸应力和最大切应力对形变和断裂起不同的作用。最大切应力促进塑性滑移的发展,是位错移动的推动力,它对形变和断裂的发生及发展过程都产生影响;而最大拉伸应力则只促进脆性裂纹的扩展。因此,最大拉应力与最大切应力的比值越大,构件失效脆性断裂的可能性越大,在三向拉伸应力状态下比值越大,极易导致脆性断裂。
在实际金属构件中,常见由于应力分布不均匀而造成三向应力状态,如构件的截面突然变化、小的圆角半径、预存裂纹、刀痕、尖锐缺口尖端处往往由应力集中而引起应力不均匀分布,周围区域为了保持变形协调,便对高应力区以约束,即造成三向拉伸应力状态。这是造成金属构建在静态低负荷下产生脆性断裂的重要原因。
(2)温度
低温下造成构件的脆性断裂是由温度的改变而引起材料本身的性能变化。随着温度的降低,金属材料屈服应力增加,韧性下降,解理应力下降;当温度在材料脆性转变温度以下时,材料的解理应力小于其屈服应力,材料的断裂由原来的正常韧性断裂转为脆性断裂。
(3)尺寸效应
钢板厚度增加,脆性转变温度升高,缺口脆性增加;关于板厚的脆化原因一般认为与冶金质量和应力状态有关。
(4)焊接质量
焊接缺陷一般有夹杂、气孔、未焊透和焊接裂纹等,而切中焊接裂纹的存在对焊接构件的断裂起着重要作用。
(5)工作介质
金属构件在腐蚀介质中,受应力(尤其是拉应力)作用,同时又有电化学腐蚀时,极易导致早起脆性断裂;
(6)材料和组织因素
脆性材料、冶金质量差、氢脆倾向的材料以及缺口敏感性大的钢种都能促使发生脆性断裂;不良热处理产生脆性组织状态,如组织偏析、脆性相析出、晶间脆性析出物、淬火裂纹、淬火后消除应力处理不及时或不充分等也能促进脆性断裂的发生。
预防脆性断裂的途径
(1)温度是引起构件脆断的重要因素之一, 设计者必须考虑构件的最低工作温度应高于材料的脆性转变温度。若所设计的构件工作温度较低,甚至低于该材料的脆性转变温度,则必须降低设计应力水平,使应力低于不会发生裂纹扩展的水平;若其设计应力不能降低,则应更换材料。选择韧性更高、脆性转变温度更低的材料;
(2)设计者在选择材料时,除考虑材料的强度外,还应保证材料有足够的韧性。应该从断裂力学的观点来选择材料,若材料有较高的断裂韧性时,则构件中允许有较大的缺陷存在;
(3)为减少构件脆性断裂,在设计时应使缺陷产生的应力集中减小到最低限度,如减少尖锐角,消除未焊透的焊缝,结构设计时应尽量保证结构几何尺寸的连续性(因为在结构不连续的过渡部位往往使构件应力集中而形成高应力区);过渡段的连接应采用正确的焊接方法;
(4)尽量减少焊接产生的缺陷。这种设计包括选择适当的焊缝金属缺口韧性,焊接预热和焊后的热处理制度,适当设计焊接条件以减少缺陷。
4 疲劳断裂
金属构件在交变载荷的作用下,虽然应力水平低于金属材料的抗拉强度,优势甚至低于屈服极限,但经过一定的循环周期后,金属构件会发生突然的断裂,这种断裂称为疲劳断裂,疲劳断裂是脆性断裂的一种形式。
疲劳断裂的现象及特征
①疲劳负荷是交变负荷。
②金属构件在交变负荷作用下,一次应力循环对构件不产生明显的破坏作用,不足以使构件发生断裂。构件疲劳断裂是在负荷经多次循环以后发生,高周疲劳断裂的循环次数Nf>104,而低周疲劳断裂的循环次数较少,一般Nf=102~104。疲劳断裂应力还小于抗拉强度σb,其值也小于屈服点σs。
③疲劳断裂只可能在有使材料分离扯开的反复拉伸应力和反复切应力的情况下出现。纯压缩负荷不会出现疲劳断裂,疲劳起源点往往出现在最大拉应力处。
④疲劳断裂过程包括疲劳裂纹的萌生、裂纹扩展和瞬时断裂三个阶段。
疲劳裂纹的萌生:大量研究表明,疲劳裂纹都是由不均匀的局部滑移和显微开裂引起,主要方式有表面滑移带形成,第二相、夹杂物或其界面开裂,晶界或亚晶界开裂及各类冶金缺陷、工艺缺陷等。金属构件由于受到交变负荷的作用,金属表面晶体在平行于最大切应力平面上产生无拘束相对滑移,产生了一种复杂的表面状态,常称为表面的“挤出”和“挤入”现象,当金属表面的滑移带形成尖锐而狭窄的缺口时,便产生疲劳裂纹的裂纹源。
疲劳裂纹的扩展:疲劳裂纹扩展的第一阶段为切向扩展阶段,裂纹尖端将沿着与拉伸轴呈45°方向的滑移面扩展。疲劳裂纹扩展的第二阶段为正向扩展阶段。在交变应变作用下,疲劳裂纹从原来与拉伸轴呈45°的滑移面,发展到与拉伸轴呈90°。即由平面应力状态转变为平面应变状态,这一阶段中最突出的显微特征是存在大量的、相互平行的条纹,称为“疲劳辉纹”。
疲劳裂纹在第二阶段扩展到一定深度后,由于剩余工作截面减小,应力逐渐增加,裂纹加速扩展。当剩余面积小到不足以承受负荷时,在交变应力作用下,即发生突然的瞬时断裂,其断裂过程同单调加载的情形相似。疲劳断裂与其他一次负荷断裂有所区别,它是一种累进式断裂。
⑤即使是塑性良好的合金钢或铝合金,疲劳断裂构件断口附近通常也观察不到宏观的塑性变形。
疲劳断裂的断裂形貌
(1)宏观形貌
起源区:即为疲劳裂纹萌生区。这个区域在整个疲劳断口中所占的比例很小。通常就是指断面上疲劳花样放射源的中心点或疲劳弧线的曲率中心点。疲劳裂纹源一般位于构件表面应力集中处或不同类型的缺陷部位。一般情况下,一个疲劳断口有一个疲劳源。疲劳区中磨得最亮的地方即是疲劳源(疲劳核心),位于零件强度最低或应力最高的地方。
扩展区:在此区中常可看到有如波浪推赶海岸沙滩而形成的“沙滩花样”,又称“贝壳状条纹”、“疲劳弧带”等,这种沙滩花样是疲劳裂纹前沿线间断扩展的痕迹,每一条条带的边界是疲劳裂纹在某一个时间的推进位置,沙滩花样是由于裂纹扩展时受到障碍,时而扩展、时而停止,或由于开车停车、加速减速、加载卸载导致负荷周期性突变而产生。
疲劳裂纹扩展区是在一个相当长时间内,在交变负荷作用下裂纹扩展的结果。拉应力使裂纹扩张,压应力使裂纹闭合,裂纹两侧反复张合,使得疲劳裂纹扩展区在客观上是一个明亮的磨光区,越接近疲劳起源点越光滑。如果在宏观上观察到沙滩花样时,就可判别这个断口是疲劳断裂。多源疲劳的裂纹扩展区,各个裂源不一定在一个平面上,随着裂纹扩展被此相连时,同的平面间的连接处形成疲劳台阶或折纹。疲劳台阶越多,表示其应力或应力集中越大。
断裂区:当疲劳裂纹扩展到临界尺寸时,构件承载截面减小至强度不足引起瞬时断裂,该瞬时断裂区域是最终断裂区。最终断裂区的断口形貌较多呈现宏观的脆性断裂特征,即粗糙“晶粒”状结构,其断口与主应力基本垂直。只有当材料的塑性很大时,最终断裂区才具有纤维状的结构,并出现较大的45°剪切唇区。
(2)微观形貌
微观形貌主要分为疲劳辉纹、轮胎压痕花样。
①疲劳辉纹是一系列基本上相互平行的条纹,略带弯曲,呈波浪状。并与裂纹微观扩展方向相垂直。裂纹的扩展方向均朝向波纹凸出的一侧。辉纹的间距在很大程度上与外加交变负荷的大小有关,条纹的清洗度则取决于材料的韧性。因此,高应力水平比接近疲劳极限应力下更易观察到疲劳辉纹。
②每一条疲劳辉纹表示该循环下疲劳裂纹扩展前沿线在前进过程中的瞬时微观位置。裂纹三个阶段有不同的微观特征:疲劳起源部位由很多细滑线组成,以后形成致密的条纹,随着裂纹的扩展,应力逐渐增加,疲劳条纹的间距也随之增加。
③疲劳辉纹可分为韧性辉纹和脆性辉纹两类。脆性疲劳辉纹的形成与裂纹扩展中沿某些解理面发生解理有关,在疲劳辉纹上可以看到把疲劳辉纹切割成一段段的解理台阶,因此脆性疲劳辉纹的间距呈不均匀,断断续续状。韧性疲劳辉纹较为常见,它的形成与材料的结晶之间无明显关系,有较大塑性变形,疲劳辉纹的间距均匀规则。
④疲劳断口的微观范围内,通常由许多大小不同、高低不同的小断片组成。疲劳辉纹均匀分布在断片上,每一小断片上的疲劳辉纹连续且互相平行分布,但相邻断片上的疲劳辉纹不连续、不平行。
⑤疲劳辉纹中每一条辉纹一般代表依次载荷循环,辉纹的数目与载荷循环次数相等。
⑥轮胎压痕花样是由于疲劳断口的两个匹配断面之间重复冲击和相互运动所形成的机械损伤,也可能是由于松动的自由粒子在匹配断裂面上作用留下的微观变形痕迹。轮胎压痕花样不是疲劳本身的形态,但却是疲劳断裂的一个表征方法。
影响疲劳断裂的因素及其改善的途径
①构件表面状态
大量疲劳失效分析表明,疲劳断裂多数起源于构件的表面或亚表面,这是由于承受交变载荷的构件工作时其表面应力往往较高,典型的是弯曲疲劳构件表面拉应力最大,加上各类工艺程序难以确保表面加工质量而造成。因此,凡是制造工艺过程中产生预生裂纹(如浮火裂纹)、尖锐缺口(如表面祖糙度不符合要求,有加工刀痕等)和任何削弱表面强度的弊病(如表面氧化、脱碳等)都将严重地影响构件的疲劳寿命。而且,材料的强度越高,则表面状态对疲劳的影响也越大。
②缺口效应与应力集中
许多构件包含有缺口、螺纹、孔洞、台阶以及与其相类似的表面几何形状,也可能有刀痕、机械划伤等表面缺陷,这些部位使表面应力提高和形成应力集中区,且往往成为疲劳断裂的起源。
③残余应力
如果构件表面存在着残余拉应力,对疲劳极为不利。但是,如果使构件表面诱发产生残余压应力,则对抗疲劳大有好处。因为残余压应力起着削减表面拉应力数值的作用。一些表面热处理工序,如表面淬火、渗碳和氮化;一些机械加工工序,如喷丸、表面、冷拔、挤压和抛光都产生有利的残余压应力。因此,工程上经常采用这些方法来提高构件的疲劳抗力。
④材料的成分和组织
在各类工程材料中,结构钢的疲劳强度最高。在结构钢中,疲劳强度随着含碳量增加而增高,铬、镍等也有类似的效应。碳是影响疲劳强度的重要元素,既可间隙固溶强化基体,又可形成弥散碳化物进行弥散强化,提高钢材的形变抗力,阻止循环滑移带的形成和开裂,从而阻止疲劳裂纹的萌生和扩展,以及提高疲劳强度。其他合金元素主要通过提高钢的淬透性和改善钢的强韧性来改善疲劳强度。质量均匀、无表面或内在连续性缺陷的材料组织抗疲劳性能好。
⑤工作条件
载荷频率对疲劳强度的影响是其在一定范围内可提高疲劳强度。
低于疲劳极限的应力称为次载。金属在低于疲劳极限的应力下先运转一定次数之后,则可以提高疲劳极限,这种次载荷强化作用称为次载锻炼。这种现象可能是由于应力应变循环产生的硬化及局部应力集中松弛的结果。次载应力水平越接近疲劳极限,其锻炼效果越明显;次载锻炼的循环周次越长,其锻炼效果越好,但达到一定循环周次之后效果就不再提高。
当加载应力低于并接近疲劳极限时,间歇加载提高疲劳效果比较明显,而间歇过载加载对疲劳寿命不但无益,甚至还会降低疲劳强度。这种间歇加载影响疲劳强度的规律,可以指导制订机器运行操作规程和检验规程。
温度对疲劳强度的影响一般是温度降低,疲劳强度升高;温度升高,疲劳强度降低。
腐蚀环境介质使构件表面产生蚀抗、微裂纹等缺陷,将会加速疲劳源萌生而促进腐蚀疲劳。
磨损失效
磨损是由于机械作用、化学反应(包括热化学、电化学和力化学等反应),材料表面物质不断损失或产生残余变形和断裂的现象。磨损是发生在物体上的一种表面现象,其接触表面必须有相对运动。磨损必然产生物质损耗(包括材料转移),而且它是具有时变特征的渐进的动态过程。
磨损按磨损机理可分为粘着磨损、磨粒磨损、疲劳磨损、腐蚀磨损、冲蚀磨损、微动磨损,按环境介质可分为干磨损、湿磨损、流体磨损。
1 磨料磨损
外界硬颗粒或者对磨表面上的硬突起物或粗糙峰在摩擦过程中引起表面材料脱落的现象, 称为磨粒磨损(又称磨料磨损)。磨粒是摩擦表面互相摩擦产生或由介质带入摩擦表面。
磨粒磨损是最普遍的一种形式,主要出现在采矿、钻探、建筑、运输与农业等机械相关零部件,据统计,工业中磨粒磨损造成的损失约占总的50%左右。
磨料磨损示意图
按力的作用特点划分为划伤式磨损、碾碎式磨损和凿削式磨损。
划伤式磨损属于低应力磨损。低应力的含义是指磨料与构件表面之间的作用力小于磨料本身压溃强度。
碾碎式磨损属于高应力磨损。当磨料与构件表面之间接触压应力大于磨料的压溃强度时,磨粒被压碎,一般金属材料表面被划伤,韧性材料产生塑性变形或疲劳,脆性材料则发生碎裂或剥落。
凿削式磨损的产生主要是由于磨料中包含大块磨粒,而且具有尖锐棱角,对构件表面进行冲击式的高应力作用,使构件表面撕裂出很大的颗粒或碎块,表面形成较深的坑。这种磨损常在运输或破碎大块磨料时发生,典型实例如颚式破碎机的齿板、辗辊等。
磨粒磨损的影响因素
磨砺磨损的改善措施:(1)对于以切削作用为主要机理的磨粒磨损应增加材料硬度;(2)根据机件的服役条件,合理选择相应的耐磨材料;(3)采用渗碳、渗氮共渗等化学热处理提高表面硬度;(4)机件的防尘和清洗。
2 粘着磨损
当摩擦副相对滑动时, 由于粘着效应所形成结点发生剪切断裂,被剪切的材料或脱落成磨屑,或由一个表面迁移到另一个表面,此类磨损称为粘着磨损。
粘着磨损的特征是磨损表面有细的划痕,沿滑动方向可能形成胶体的裂口。最突出的特征是表层金相组织和化学成分均有明显变化。磨损产物多为片状或小颗粒。
粘着磨损示意图
根据粘合强度、金属本体强度与切应力三者之间的不同关系,可以把粘着磨损分为四类:
粘着磨损的影响因素
(1)摩擦副材料性质的影响
脆性材料比塑料材料的抗粘着能力高;
相同金属或互溶性大的材料摩擦副易发生粘着磨损,反之则不易发生粘着磨损;
多相金属也不容易发生粘着磨损;
表面处理可以减小粘着磨损;
硬度高的金属比硬度低的金属抗粘着能力强。
(2)载荷与速度的影响
载荷增加——粘着磨损加剧,但有临界载荷;
在压力一定的情况下,粘着磨损随滑动速度的增加而增加,在达到某一极大值后,又随着滑动速度的增加而减少。
(3)表面温度的影响
表面温度升高可使润滑膜失效,使材料硬度下降,摩擦表面容易产生粘着磨损。
(4)润滑油、润滑脂的影响
在润滑油、润滑脂中加入油性或极压添加剂能提高润滑油膜吸附能力及油膜强度,能成倍地提高抗粘着磨损能力。
3 冲蚀磨损
冲蚀磨损是指流体或固体颗粒以一定的速度和角度对材料表面进行冲击所造成的磨损。
根据颗粒及其携带介质的不同,冲蚀磨损又可分为气固冲蚀磨损、流体冲蚀磨损、液滴冲蚀和气蚀等。
造成冲蚀的粒子通常都比被冲蚀的材料的硬度大。冲蚀磨损与腐蚀磨损的区别是前者对材料表面的破坏主要是机械力作用引起,腐蚀磨损只是第二位的因素;而腐蚀磨损则是在腐蚀介质中摩擦副的磨损,是腐蚀和磨损综合作用的结果。
冲蚀磨损的影响因素
(1)冲蚀粒子
粒度对冲蚀磨损有明显有对冲蚀磨损有明显的影响, 一般粒子只寸在20-200μm 范围内,材料磨损率随粒子尺寸增大而上升。当粒子尺寸增加到某一临界值时,材料的磨损率几乎不变或变化缓慢,这一现象称为“尺寸效应” 。粒子的形状也有很大影响,尖角形粒子与圆形粒子比较,在相同条件下,都是45°冲击角时,多角形粒子比圆形粒子的磨损大4倍,甚至低硬度的多角形粒子比较高硬度的圆形粒子产生的磨损还要大。粒子的硬度和可破碎性对冲蚀率有影响,因为粒子破碎后会产生二次冲蚀。
(2)攻角
材料的冲蚀率和粒子的攻角有密切关系。当粒子攻角为20°~30°时,典型的塑性材料冲蚀率达最大值,而脆性材料最大冲蚀率出现在攻角接近90°处。攻角与冲蚀率关系几乎不随入射粒子种类、形状及速度而改变。
(3)速度
粒子的速度存在一个门槛值,低于门槛值,粒子与靶面之间只出现弹性碰撞而观察不到破坏,即不发生冲蚀。速度门槛值与粒子尺寸和材料有关。
(4)冲蚀时间
冲蚀磨损存在一个较长的潜伏期或孕育期,磨粒冲击靶面后先使表面粗糙,产生加工硬化,此时未发生材料流失,经过一段时间的损伤积累后才逐步产生冲蚀磨损。
(5)环境温度
温度对冲浊磨损的影响比较复杂,有些材料在冲蚀磨损中随温度升高磨损率上升;但也有些材料随温度升高磨损有所减少,这可能是高温时形成的氧化膜提高了材料的抗冲蚀磨损能力,也有可能是温度升高,材料塑性增加,抗冲蚀性能提高。
(6)靶材
靶材除本身的性质以外,还与磨粒的几何形状、尺寸、硬度、攻角、速度和温度等条件密切相关。
4 微动磨损
微动磨损指受压配合面在微小幅度的振动下所引起的表面损伤,包括材料损失、表面形貌变化、表面或亚表层塑性变形或出现裂纹等,称为微动磨损。微动磨损是一种复合磨损(粘着、磨粒、疲劳、腐蚀)。
金属表面的微动磨损原理示意图
微动磨损可以分为两类。第一类是该构件原设计的两物体接触面是静止的,只是由于受到振动或交变应力作用,使两个匹配面之间产生微小的相对滑动,由此造成磨损。第二类是各种运动副在停止运转时,由于环境振动而产生微振造成磨损。
工程中常见的微动磨损
(1)轴承
滚动轴承存三个部位可能发生微动损伤,轴承和轴承座、轴的紧配合面及滚珠或滚柱和座圈之间。
(2)压配合
机车主轴一般用压配合装入轮毅中,运行过程中,在负荷的作用下,轴发生弯曲,和轮毅配合段的两端出现微动。
(3)榫槽配合
航空发动机的涡轮叶片榫头和轮盘配合,叶片相当于一端固定的悬梁臂,由于受强烈气流冲击而处在弯曲复合振动状态,从而使榫槽受到微动磨损,导致配合松动并萌生疲劳裂纹。
(4)铆接
飞机上广泛使用铆接。据估计,各种飞机上90%的疲劳裂纹起源于微动部位,而其中又以铆接和螺纹联接占多数。
(5)钢丝缆绳
由于其本身的柔性必然导致丝对丝或股对股之间的滑动,缆的往复运动造成一复杂的疲劳应力。
(6)核工业中的热交换器和压力管燃料元件
反应堆中的燃料,用耐辐射和耐磨性好的锆合金和镁合金包覆,在冷却液流作用下,各包覆件之间发生微动磨损,最终将包覆层磨穿。
微动磨损过程
微动磨损是一个复杂的过程,包含粘着、氧化、磨粒和疲劳等的综合作用。
微动磨损的过程一般是相互接触的两个物体表面,由于接触压力的作用使微凸体产生塑性变形和粘着,在小振幅振动作用下,粘着点可能被剪切并脱落,剪切表面被氧化。由于表面紧密配合,脱落的磨屑不易排出,在两表面间起着磨粒作用,加速微动磨损过程。
微动磨损初始阶段材料的流失机制主要是粘着和转移,其次是凸峰点的犁削作用。对于较软材料可出现严重塑性变形,由挤压直接撕裂材料,这个阶段摩擦因素及磨损量均较高。
当产生的磨屑足以覆盖表面后,粘着减弱,逐步进入稳态阶段。这时,摩擦因数及磨损率均明显降低,磨损量和循环数成线性关系。由于微动的反复切应力作用,造成亚表面裂纹萌生, 形成脱层损伤,材料以薄片形式脱离母体。刚脱离母体的材料主要是金属形态。它们在二次微动中变得越来越细并吸收足够的机械能以致具有极大的化学活性,在接触空气瞬间即完成氧化过程,成为氧化物。氧化磨屑既可作为磨料加速表面损伤,又可分开两表面,减少金属间接触,起缓冲垫作用,大部分情况下,后者作用更显著,即磨屑的主要作用是减轻表面损伤。
微动磨损的特征与判断
(1)表面特征
钢的微动损伤表面粘附着一层红棕色粉末,当将其除去后,观察到许多小麻坑。其形状不同于点蚀,它有两种类型,一种为深度不到5μm的不规则的长方形浅平坑,另一种为较深(可达50μm左右)且形状较规则的圆坑。
(2)磨屑特征
钢铁微动磨屑的重要标志是红棕色磨屑。
对于其他金属,大多数情况下, 磨屑为该种金属的最终氧化态。不活泼的金属如金和铂的磨屑由纯金属组成。磨屑的大小和成分与振幅有关,振幅较大时,磨屑直径较大,金属的比例也较高。材料的硬度影响磨损量,也影响磨屑的大小和成分,材料越硬,磨屑越细,氧化物的比例也越大。
5 腐蚀磨损
两物体表面产生摩擦时,工作环境中的介质如液体、气体或润滑剂等,与材料表面起化学或电化学反应,形成腐蚀产物,这些产物往往粘附不牢,在摩擦过程中剥落下来,其后新的表面又继续与介质发生反应。这种腐蚀和磨损的反复过程称为腐蚀磨损。
腐蚀磨损分类
腐蚀磨损可分为化学腐蚀磨损和电化学腐蚀磨损。化学腐蚀磨损又可分为氧化磨损和特殊介质腐蚀磨损。
腐蚀磨损是一种极为复杂的磨损形式,它是材料受腐蚀和磨损综合作用的磨损过程,对环境、温度、介质、滑动速度、载荷大小及润滑条件等极为敏感,稍有变化就可使腐蚀磨损发生很大变化。
(1)化学腐蚀磨损
化学腐蚀磨损最常见的是氧化磨损。氧化磨损的实质是金属表面与气体介质发生氧化反应,生成氧化膜。
脆性氧化膜与金属基体差别大,在达到一定厚度时,很容易被摩擦表面上的微凸体的机械作用去除,暴露出新的基体表面又开始新的氧化过程,膜的生长与去除反复进行。
当氧化膜的韧性较好,而且比金属基体还软时,若受摩擦表面微凸体机械作用,可能有部分被去除,在继续磨损过程中,氧化仍然在原有氧化膜的基础上发生,这种磨损较脆性氧化膜的磨损轻。
(2)电化学腐蚀磨损
电化学腐蚀磨损按腐蚀磨损产物被机械或腐蚀去除的特点也可分为两种磨损。一种是在均匀腐蚀条件的磨损过程中,局部腐蚀产物被磨料或硬质点的机械作用去除,使之裸露金属基底,但随后又在磨损处形成新的腐蚀产物,经过反复作用,此处腐蚀速度比腐蚀产物始终覆盖的其他部分快得多,严重得多。此类磨损称均匀腐蚀条件下的腐蚀磨损。
多相材料,尤其是含有碳化物的耐磨材料,由于碳化物与基体之间存在较大的电位差,形成腐蚀电池,产生相间腐蚀,极大削弱了碳化物与基体结合力,在磨料或硬质点的作用下,碳化物很容易从基体脱落或发生断裂。
另一种情况是形成局部腐蚀电池。由于磨料的磨损作用,金属材料表面产生不均匀的塑性变形,塑性变形强烈的部分成为阳极,首先受到腐蚀破坏,或者溶解,或者形蚀产物,在磨料的继续作用下,腐蚀产物很容易被去除形成二次磨损。这一塑性变形就是应变差异腐蚀电池的作用,它可使腐蚀速度提高两个数量级左右。
腐蚀磨损的特征
腐蚀磨损过程中,氧化膜断裂和剥落,形成了新的磨料,使腐蚀磨损兼有腐蚀与磨损双重作用。但腐蚀磨损又不同于一般的磨料磨损。腐蚀磨损不产生显微切削和表面变形,其主要磨损表面有化学反应膜或麻点。麻点比较光滑,磨屑多事显微细粉末状的氧化物,也有薄的碎片。钢摩擦副相互滑动的氧化磨损,沿滑动方向呈现出匀细的磨痕。磨屑是暗色的片状或丝状物,片状磨屑为红褐色的Fe2O3,而丝状的是灰黑色的Fe3O4。
影响腐蚀磨损的因素
(1)PH值
一般来讲,PH<7时,随着酸性增加腐蚀磨损量增加。在7<PH<12在相对运动速度不太高的情况下,随碱性增加,腐蚀磨损量下降。
温度 在其他条件相同的情况下,腐蚀磨损的速度一般随温度升高而增加。
(2)化学成分
化学成分是主要影响因素。对不同介质条件,在Fe-C合金中,加入适量的Cr、V、B等元素可提高耐磨性。不同介质加入不同合金元素才能获得良好的效果。
6 疲劳磨损
当两个接触体相对滚动或滑动时,在接触区形成的循环应力超过材料的疲劳强度的情况下,在表面层将引发裂纹并逐步扩展,最后使裂纹以上的材料断裂剥落下来的磨损过程称疲劳磨损。
疲劳磨损与整体疲劳的区别
①裂纹源与裂纹扩展不同。整体疲劳的裂纹源都是从表面开始,一般从表面沿与外加应力成45°的方向扩展,超过两三个晶粒以后,即转向与应力垂直的方向。而疲劳磨损裂纹除来源于表面外,或与表面呈一定角度,一般为10°~30°,而且只限于在表面层内扩展。
②疲劳寿命不同。整体疲劳一般有明显的疲劳极限,低于疲劳极限,疲劳理论寿命可以大大延长。而疲劳磨损尚未发现疲劳极限,疲劳磨损的零件寿命波动很大。
③疲劳磨损的工作条件更复杂更恶劣。疲劳磨损除循环应力作用外,还经受复杂的摩擦过程,可能引起表面层一些列物理化学变化以及各种力学性能与物理性能变化等。
疲劳磨损特征
疲劳磨损典型特征是零件表面出现深浅不同,大小不一的凹坑,或较大面积的表面剥落,简称点蚀或剥落。
点蚀裂纹一般都是从表面开始,向内倾斜扩展,最后二次裂纹折向表面,裂纹以上的材料折断脱落下来即成点蚀。单个点蚀坑的表面形貌常表面为扇形。剥落裂纹一般起源于亚表层内部较深的层次。
纯滚动接触时,裂纹发生在亚表层最大切应力处,裂纹发展慢,经历时间比裂纹萌生长,裂纹断口颜色比较光亮。滚动加滑动的疲劳磨损,因切应力和压应力,易在表面上产生微裂纹,它的萌生阶段往往大于扩展阶段,断口较暗。
疲劳磨损的基本原理
最大的正应力发生在表面,最大的切应力发生在离表面一定距离外。滚动接触时在交变应力的影响下,裂纹就容易在这些部位形核,并扩展到表面而产生剥落。若除滚动接触外还有滑动接触,破坏位置就逐渐移向表面。这是因为纯滑动时,最大的切应力发生在表面。
实际中,由于构件表面粗糙度、材料不均、夹杂物、微裂纹及硬质点,疲劳破坏的位置会改变,所以有些裂纹从表面开始,而有些从次表面开始。
影响疲劳磨损的因素
①材质
材料纯度越高寿命越长,钢中的非金属夹杂物,特别是是脆性的带有棱角的氧化物、硅酸盐以及其他各种复杂成分的点状、球状夹杂物破坏基体的连续性,对疲劳磨损有严重不良影响。此外要控制金属的组织结构。
增加材料的加工硬化硬度对疲劳磨损有重要影响,硬度越高裂纹越难形成,降低表面粗糙度可有效提高抗疲劳磨损的能力;表层内一定深度的残余压应力可提高对接触疲劳磨损的抗力,表面渗碳、淬火、喷丸、滚压等处理都可使表面产生压应力。
②载荷
载荷是影响疲劳磨损寿命的主要原因之一。
一般认为球轴承的寿命与载荷的立方成反比。
③润滑油膜厚度
润滑油黏度高且足够厚时,可使表面微凸体不发生接触,从而不容易产生接触疲劳磨损。由于接触表面压力很高,要选择在超高压下黏度高的润滑油。
④环境。周围环境,如空气中的水、海水中的盐、润滑油中有腐蚀性的添加剂对材料的疲劳磨损有不利的影响。如润滑油中的水会加速轴承钢的接触疲劳失效,甚至很少量都危害重大。
7 提高耐磨性的途径
金属材料的磨损主要是发生在表面的变形和断裂过程,提高承受摩擦作用的构件表面的强度和韧性,可提高耐磨性。
对于粘着磨损而言,改善润滑条件,提高氧化膜与基体金属的结合能力,以增强氧化膜的稳定性,阻止金属之间直接接触,以及降低表面粗糙度等都可以减轻粘着磨损。如果是沿接触面上产生粘着磨损,只需降低摩擦副原子间的结合力,最好是采用表面处理,如渗碳、渗氮、渗磷等。
表面处理实际上是在金属表面形成一层化合物层或非金属层,避免摩擦副直接接触,既降低原子间结合力,又减小摩擦因数,可防止粘着。渗硫并不提高硬度,但因降低了摩擦因数,故可防止粘着,特别对高温下和不可能润滑的构件更为有效。
如果粘着磨损发生在较软材料内部,则不但应降低摩擦副的结合力,而且要提高材料本身表层硬度,采用渗碳、渗氮、碳氮共渗及碳氮硼三元共渗等热处理工艺都有一定效果。
对磨粒磨损而言,如果是低应力磨粒磨损,应提高表面硬度。选用含碳较高的钢,并经热处理后获得马氏体组织,是提高抗磨粒磨损的简单方法。但当材料受重载荷,特别是在较大冲击载荷下工作,则基体组织最好是下贝氏体。因为这种组织既有较高硬度又有良好韧性。对于合金钢,控制和改变碳化物数量、分布、形态对提高抗磨粒磨损能力有决定性影响。消除基体中初生碳化物,并使次生碳化物均匀弥散分布,就可以显著提高耐磨性。提高钢中碳化物体积比,一般也能提高耐磨性。钢中含有适量残余奥氏体对提高抗磨粒磨损能力也是有益的。因为残余奥氏体能增加整体韧性,给碳化物以支承,并在受磨损时能部分转变为马氏体使硬度提高。采用渗碳、碳氮共渗等表面热处理也能有效地提高抗磨粒磨损能力。
腐蚀失效
腐蚀是材料表面与服役环境发生物理或化学的反应,使材料发生损坏或变质的现象,构件发生的腐蚀使其不能发挥正常的功能则称为腐蚀失效。
腐蚀有多种形式,有均匀遍及构件表面的均匀腐蚀和只在局部地方出现的局部腐蚀,局部腐蚀又分为点腐蚀、晶间腐蚀、缝隙腐蚀、应力腐蚀开裂、腐蚀疲劳等。
全面腐蚀和局部腐蚀的主要区别
各类腐蚀失效在化工事故中所占比例
工程中常见的金属腐蚀失效破坏类型的特征及产生的条件
电偶腐蚀
异种金属相接触,又都处于同一或相连通的电解质溶液中,由于不同金属之间存在实际(腐蚀)电位差而使电位较低(较负)的金属加速腐蚀,称为电偶腐蚀(或接触腐蚀)。
组成电偶腐蚀的两种金属由于电偶效应,使电位较正的金属由于阴极钝化使腐蚀速率减小得到保护,电位较负的金属由于阳极极化使腐蚀速率增加。
电偶腐蚀特征:腐蚀主要发生在两个不同金属或金属与非金属导体接触边线附近,远离边缘区域,腐蚀程度较轻。
缝隙腐蚀
金属表面上由于存在异物或结构上的原因而形成缝隙,使缝内溶液中的物质迁移困难所引起的缝隙内金属的腐蚀,称为缝隙腐蚀。缝隙腐蚀多数情况是宏观电池腐蚀。
缝隙腐蚀的起因是氧浓度差电池的作用,而闭塞电池引起的酸化自催化作用是造成缝隙腐蚀加速腐蚀的根本原因。
工程上,造成缝隙腐蚀的条件很多:铆接、法兰盘连接面、螺栓连接、金属表面沉积物、腐蚀产物等都会形成缝隙。
缝隙腐蚀的特征:
腐蚀发生在缝隙内,缝外金属受到保护;
构成缝隙腐蚀的缝隙宽度在0.025~0.1mm之间;
构成缝隙的材料无特殊性,金属或非金属缝隙都对金属产生缝隙腐蚀;
几乎所有腐蚀介质都会引起金属缝隙腐蚀,以充气含氯化物活性阴离子溶液最容易;
几乎所有金属或合金都会产生缝隙腐蚀,以钝态金属较为严重。
点蚀
金属材料在某些环境介质中,大部分表面不发生腐蚀或腐蚀很轻微,但在个别的点或微小区域内,出现蚀孔或麻点,且随着时间的推移,蚀孔不断向纵深方向发展,形成小孔状腐蚀坑,称为点腐蚀。
点蚀是一种隐蔽性较强、危险性很大的局部腐蚀。点蚀主要集中在某些活性点上,不断向金属内部深处发展,通常其腐蚀深度大于孔径,严重时可使管道或设备穿孔。点蚀还可诱发其他形式的腐蚀,如应力腐蚀破裂或腐蚀疲劳等。
点蚀的特征:
易发生在有自钝化倾向的金属表面;
蚀孔小且深,在表面有一定分布;
孔口有腐蚀产物覆盖;
蚀孔的出现有时间不一的诱导期;
蚀孔常沿重力方向或横向发展;
孔蚀的剖面特征形貌
晶间腐蚀
在某些腐蚀介质中,晶界可能先行被腐蚀。这种沿着金属晶界发生腐蚀的局部破坏现象,称为晶间腐蚀。
晶界是金属中各种溶质元素偏析或金属化合物(如碳化物和σ相等)沉淀容易析出的区域。
当金属材料发生晶间腐蚀时,其特点是在宏观上金属的外形尺寸几乎不变,但其强度和延性下降。受强烈的机械碰撞后,表面出现裂缝,严重者稍加外力,晶粒即行脱落。在微观上进行断面金相检查时,可看到腐蚀沿晶界均匀发展。
选择性腐蚀
合金中的某一组织或某一成分优先腐蚀,另一组织或成分不腐蚀或很少腐蚀,这种现象叫做选择性腐蚀。
选择性腐蚀结果轻则使合金损失强度,重则造成穿孔、破损,酿成严重事故。就介质条件而言,选择性腐蚀多发生在水溶液中,但某些材料在熔融盐、高温气体介质中也有选择性腐蚀出现。
选择性腐蚀破坏的形式则可大致分为两种,层状和栓式。
选择性腐蚀较均匀地波及整个材料表面(如黄铜的层式脱锌) ,称为层状选择性腐蚀;或选择性腐蚀沿表面发展,但不均匀,呈条状,称为带状选择性腐蚀。
选择性腐蚀集中发生在材料表面的局部区域,并不断向内深入(如黄铜的栓式脱锌) ,称为栓状选择性腐蚀。例如,在酸性介质中,黄铜含锌量高时,有利于产生层状脱锌;若介质是中性、弱酸性或碱性的,黄铜含锌量相对低时,则栓状脱锌占优势。
应力腐蚀破裂
金属设备和部件在应力和特定的腐蚀性环境的联合作用下,出现低于材料强度极限的脆性开裂现象,称为应力腐蚀开裂,简称SCC(Stress Corrosion Cracking)。
产生SCC的基本条件:敏感的材料、固定拉应力、特定腐蚀介质。
应力腐蚀按机理可分为阳极溶解型和氢致开裂型两类。
如果应力腐蚀体系中阳极溶解所对应的阴极过程是吸氧反应,或者虽然阴极是析氢反应,但进入金属的氢不足以引起氢致开裂,这时应力腐蚀裂纹形核和扩展就由金属的阳极溶解过程控制,称为阳极溶解型应力腐蚀。
如果阳极金属溶解(腐蚀)所对应的阴极过程是析氢反应,而且原子氢能扩散进入金属并控制了裂纹的形核和扩展,这一类应力腐蚀就称为氢致开裂型应力腐蚀。
应力腐蚀开裂的特征:
①裂纹出现在设备或构件的局部区域,而不是发生在与腐蚀介质相接触的整个界面上。裂纹的数量不定,有时很多,有时较少,甚至只有一条裂纹。
②裂纹一般较深、较窄。裂纹的走向与设备及构件所受应力的方向有很大关系。一般说来, 裂纹基本上与所受主应力的方向相垂直,但在某些情况下,也会呈现明显的分叉裂纹。
③ 设备及部件发生应力腐蚀开裂时, 一般不产生明显的塑性变形,属于脆性断裂。
④应力腐蚀开裂是在一定的介质条件和拉应力共同作用下引起的一种破坏形式。断口宏观形貌包括逐渐扩展区和瞬断区两部分。后者一般为延性破坏。应力腐蚀开裂可能沿晶,也可能穿晶。其断口上腐蚀产物呈泥状花样等。
易产生应力腐蚀破裂的金属材料与环境的组合
氢损伤
氢损伤指的是金属材料在含有氢或与氢相互作用而导致力学性能变坏的现象,按照氢损伤发生的温度条件可以分为氢脆与氢腐蚀;按照氢损伤是否可以通过消氢处理恢复材料原来的力学性能分为可逆与不可逆氢损伤。
(1)氢脆
氢脆可以包括氢压裂纹(钢中自点、H2S诱发裂纹、焊接冷裂纹和充氢或酸洗裂纹)和氢致滞后断裂等。
氢致相变导致的氢脆。很多金属能形成稳定的氢化物。 氢化物是一种脆性中间相, 一旦有氢化物析出,材料的塑性和韧性就会下降,即氢化物析出导致材料变脆。氢化物脆、氢致马氏体相变是一种氢致相变引起的氢脆。
(2)氢致滞后断裂
在恒载荷(或恒位移)条件下,原子氢通过应力诱导扩散富集到临界值后就引起氢致裂纹的形核、扩展,从而导致低应力断裂的现象称为氢致滞后断裂。所谓滞后是指氢扩散富集到临界值需要经过一段时间,故加载后要经过一定时间后氢致裂纹才会形核和扩展。如把原子氢除去后,就不会发生滞后断裂,故它也是可逆的。
(3)氢腐蚀
氢腐蚀实质是氢致化学变化导致的氢脆。在高温高压下氢进入钢中后与碳化物反应生成甲烧, 形成的CH4比分子不能从钢中扩散出来,就在晶界夹杂物处形成气泡,井有很大压力。随着C比的不断形成,气泡不断长大,当气泡中CH4的压力大于材料在该温度下的强度时就会使气泡转化成裂纹。 环境H2的压力愈高,温度愈高,则CH4气泡中的压力就愈大,当CH4气泡中的压力等于材料的断裂强度时就会导致微裂纹形核。与此同时,生成CH4的反应使钢形成脱碳,降低了钢的强度。
腐蚀疲劳
在交变应力和腐蚀介质同时作用下,金属的疲劳强度或疲劳寿命比无腐蚀作用时有所降低,这种现象叫做腐蚀疲劳。这里所谓“无腐蚀作用”,一般是指在空气中金属的疲劳行为。
具有应力腐蚀破裂敏感性的材料受交变应力作用时,如果应力半幅在能产生应力腐蚀破裂的临界值以下,则只能产生腐蚀疲劳。如果高于应力腐蚀破裂的临界应力,随着应力交变速度的降低,可能产生应力腐蚀破裂与腐蚀疲劳混合存在的情况。
冲刷腐蚀
冲刷腐蚀又称磨损腐蚀和磨耗腐蚀,是指溶液与材料以较高速度作相对运动时,冲刷和腐蚀共同引起的材料表面损伤现象。这种损伤要比冲刷或腐蚀单独存在时所造成的损伤的加和大得多。这是因为冲刷与腐蚀互相促进的缘故。广义的冲刷腐蚀包括湍流腐蚀(又名冲击腐蚀)、空蚀、摩振腐蚀(又称微动磨损和徽动腐蚀)等。
在冲刷腐蚀中,特别把主要由于金属构件几何形状变化而使较高流速溶液产生湍流造成的金属表面破坏叫做湍流腐蚀,又叫做冲击腐蚀。例如溶液流经管道弯头或涡轮机涡壳和叶片时,都能产生湍流腐蚀。
空泡腐蚀即空蚀,空蚀破坏在金属表面下产生了加工硬化层,空蚀点附近可产生裂纹。在空蚀破坏的性质方面,机械冲击作用比电化学作用为大。空泡腐蚀属于冲击腐蚀的特殊形式。
在有氧气存在的条件下,金属构件若沿着受载荷而紧密接触的面有轻微的振动或往返的相对运动,使在接触面上出现黑斑、小坑或细槽现象,即称之为微动腐蚀。这种腐蚀现象涉及三个过程:冷焊、局部断裂和氧化。
失效分析的基本方法
失效材料的检测
化学成分分析
化学成分分析包括对失效构件金属材料化学成分、环境介质及反应物、生成物、痕迹物等的化学成分的分析。
性能测试
力学性能包括包括构件金属材料的强度指标、塑性指标和韧性指标σb、σs、σn、σD、δ、ψ、Akv、KIC、δC及硬度等;
化学性能包括金属材料在所处环境介质中的电极电位、极化曲线及腐蚀速率等;
物理性能包括如环境介质在所处工艺条件下的反应热、燃烧热等;
无损检测
采用物理的方法,在不改变材料或构件的性能和形状的条件,迅速而可靠地确定构件表面或内部裂纹和其他缺陷的大小、数量和位置。金属构件表面裂纹及缺陷常用渗透法及电磁法检测:内部缺陷则多用放射性检测,声发射常用于动态-无损检测,如探测裂纹扩展情况。
组织结构分析
蜘蛛结构分析包括金属材料表面和心部的金相组织或缺陷。常用金相法分析金属的显微组织是否正常、是否存在晶粒粗大、脱碳、过热、偏析等缺陷;夹杂物的类型、大小、数量及分布;晶界上有无析出物,裂纹的数量、分布及其附近组织有无异常,是否存在氧化或腐蚀产物等。
应力测试及计算
构件残余应力的测定是在无外加载荷的作用下进行测定,目前多用X射线应力测定法。
失效件的取样及处理
失效件的保护
断口保护主要是防止机械损伤或化学损伤。
对于机械损伤的防止,应当在断裂事故发生后马上把断口保护起来。在搬运时将断口保护好,在有些情况下还用衬垫材料,尽量使断口表面不要相互摩擦和碰撞。有时断口上可能沾上一些油污或脏物,千万不可用硬刷干刷断口,并避免用手指直接接触断口。
对于化学损伤的防止,主要是防止来自空气和水或其他化学药品对断口的腐蚀。一般可采用涂层的方法,即在断口上涂防腐物质,原则是涂层物质不使断口受腐蚀及易于被完全清洗掉。
失效件的取样
为了全面地进行失效分析,需要各种试样,如力学性能试样、化学分析试样、断口分析试祥、电子探针试样、金相试样、表面分析试样和模拟试验用的试样等。这些试样要从有代表性的部位上截取,要对截取全部试样有计划安排。在截取的部位,用草图或照相记录,标明是哪种试样,以免弄混而导致错误的分析结果。
失效件的清洗
清洗的目的是为了除去保护用的涂层和断口上的腐蚀产物及外来沾污物如灰尘等。常用以下几种方法:
① 用干燥压缩空气吹断口,这可以清除粘附在上面的灰尘以及其他外来赃物:用柔软的毛刷轻轻擦断口,有利于把灰尘清除干净。
② 对断口上的油污或有机涂层,可以用汽油、石油醚、苯、丙酮等有机溶剂进行清除,清除干净后用无水酒精清洗后吹干。
③超声波清洗能相当有效地清楚断口表面的沉淀物,且不损坏断口。
④应用乙酸纤维膜复型剥离。通常对于粘在断口上的灰尘和和疏松的氧化腐蚀产物可采用这种方法,就是用乙酸纤维脂反复覆在断口上2~5次,可以剥离断口上的脏物。该方法操作简单,既可去掉断口上的油污,对断口又无损伤,故对一般断口建议用此法清洗。
⑤ 使用化学或电化学方法清洗。这种方法主要用于清洗断口表面的腐蚀产物或氧化层,但可能破坏断口上的一些细节,所以使用时必须十分小心。一般只有在其他方法不能清洗掉
的情况下经备用试样试用后才使用。
常见清洗腐蚀产物的化学方法
失效分析的基本技能
1 断口分析
断口分析重要性
断口上忠实地记录了金属断裂的全过程,即裂纹的产生、扩展直至开裂:外部因素对裂纹萌生的影响及材料本身的缺陷对裂纹萌生的促进作用;同时也记录着裂纹扩展的途径、扩展过程及内外因素对裂纹扩展的影响。
断口分析的依据
(1)断口的颜色与色泽
观察断口表面光泽与颜色时,主要观察有无氧化色、有无腐蚀的痕迹、有无夹杂物的特殊色彩与其他颜色;红锈、黄锈或是其他颜色的锈蚀:是否有深灰色的金属光泽、发蓝颜色(或呈深紫色、紫黑色金属光泽)等。
根据疲劳断口的光亮程度,可以判断疲劳源的位置。如果不是腐蚀疲劳,则源区最光滑。
(2)断口上的花纹
疲劳断裂断口宏观上有时可见沙滩条纹,微观上有疲劳辉纹。脆性断裂有解理特征,断口宏观上有闪闪发光的小刻面或人字、山形条纹,而微观上有河流条纹。舌状花样等。韧性断裂宏观有纤维状断口,微观上则多有韧窝或行花样等。
(3)断口上的粗糙度
断口的表面实际上由许多微小的小断面构成,其大小、高度差决定断口的粗糙度。不同材料、不同断裂方式,其断口粗糙度也不同。
一般来说, 属于剪切型的韧性断裂的剪切唇比较光滑;而正断型的纤维区则较粗糙。属于脆性断裂的解理断裂形成的结晶状断口较粗糙,而准解理断裂形成的瓷状断口则较光滑。疲劳断口的粗糙度与裂纹扩展有关,扩展速率越快,断口越粗糙。
(4)断口与最大正应力的交角
韧性材料的拉伸断口一般呈杯锥状或呈45°切断的外形,其塑性变形是以缩颈的方式表现。即断口与拉伸轴向最大正应力交角是45°。
脆性材料的拉伸断口一般与最大拉伸正应力垂直,断口表面平齐,断口边缘通常没有剪切“唇口”。断口附近没有缩颈现象。韧性材料的扭转断口呈切断型。断口与扭转正应力交角也是45°。
脆性材料的扭转断口呈麻花状,在纯扭矩的作用下,沿与最大主应力垂直的方向分离。
(5)断口上的冶金缺陷
夹杂、分层、晶粒粗大、自点、白斑、氧化膜、疏松、气孔、撕裂等,常可在失效件断口上经宏观或微观观察而发现。
断口的观察
宏观观察是指用肉眼、放大镜、低倍率的光学显微镜或扫描电子显微镜来观察断口的表面形貌。通过宏观观察收集断口上的宏观信息,则可初步确定断裂的性质,可以分析裂源的位置和裂纹扩展方向,可以判断冶金质量和热处理质量等。
微观观察是用显微镜对断口进行高放大倍率的观察,用金相显微镜及扫描电镜的为多。断口微观观察包括断口表面的直接观察及断口剖面的观察。通过微观观察进一步核实宏观观察收集的信息,确定断裂的性质、裂源的位置及裂纹走向、扩展速度,找出断裂原因及机理等。
剖面观察。裁取剖面要求有一定的方向,通常是用与断口表面垂直的平面来截取,垂直于断口表面有两种切法:平行裂纹扩展方向截取,则可研究断裂过程;垂直于裂纹扩展方向截取,在一定位置的断口剖面上,可研究某一特定位置的区域。
2 裂纹分析
裂纹分析的目的是确定裂纹的位置及裂纹产生的原因。裂纹形成的原因往往很复杂,如涉及上的不合理、选材不当、材质不良、制造工艺不当以及维护和使用不当等均有可能导致裂纹的产生。
裂纹分析往往需要从原材料的冶金质量、材料的力学性能、构件成型的工艺流程和工序工艺参数、构件的形状及其工作条件以及裂纹宏观和微观的特征等方向做综合的分析。其中牵涉到多种技术方法和专门知识,如无损探伤、化学成分分析、力学性能试验、金相分析、X射线微区分析等。
金属裂纹的基本形貌特征
裂纹两侧凹凸不平,耦合自然。其耦合特征是与主应力性质相关;若主应力属于切应力则裂纹一般呈平滑的大耦合;若主应力属拉应力则裂纹一般呈锯齿状的小耦合。
除某些沿晶裂纹外,绝大多数裂纹的尾端是尖锐的。
裂纹具有一定的深度,深度与宽度不等,深度大于宽度,是连续性的缺陷。
裂纹有各种形状,直线状、分校状、龟裂状、辐射状、环形状、弧形状,各种形状往往与形成的原因密切相关。
金属裂纹的检查
裂纹的宏观检查的主要目的是确定检查对象是否存在裂纹。裂纹的宏观检查,除通过肉眼进行直接外观检查和采取建议的敲击测音法外,通常采用无损探伤法,如X射线、磁力渗透着色、超声波、荧光等物理探伤法检测裂纹。
裂纹的微观检查是指检查裂纹形态特征,确定裂纹的分布是穿晶的,还是沿晶的,主裂纹附近有无微裂纹和分支。裂纹处及附近的晶粒度有无显著粗大或细化或大小极不均匀的现象,晶粒是否变形,裂纹与晶粒变形的方向相平行或相垂直。
裂纹附近是否存在碳化物或非金属夹杂物,其形态、大小数量及分布情况,裂纹源是否产生于碳化物或非金属夹杂物周围,裂纹扩展与夹杂物之间有无联系。
裂纹两侧是否存在氧化和脱碳现象,有无氧化物或脱碳组织;
产生裂纹的表面是否存在加工硬化层或回火层;
裂纹萌生处及扩展路径周围是否有过热组织、魏氏组织、带状组织以及其他形式的组织缺陷。
裂纹产生部位分析
(1)构件结构形状引起的裂纹
由于构件结构上的需要或由于设计上的不合理,或加工制造过程中没有按设计要求进行,或在运输过程中碰撞而导致在构件上往往有尖锐的凹角、凸边或缺口,截面尺寸突变或台阶等“结构上的缺陷” ,这些结构上的缺陷在构件制造和使用过程中将产生很大的应力集中并可能导致裂纹。所以,要注意裂纹所在部位与构件结构形状之间关系的分析。
(2)材料缺陷引起的裂纹
金属材料本身的缺陷, 特别是表面缺陷,如夹杂、斑疤、划痕、折叠、氧化、脱碳、粗晶以及气泡、疏松、偏析、白点、过热、过烧、发纹等,不仅其本身直接破坏了材料的连续性,降低了材料的强度与塑性,而且往住在这些缺陷的尖锐的前沿,造成很大的应力集中,使得材料在很低的平均应力下产生裂纹并得以扩展,最后导致断裂。
(3)受力状况引起的裂纹
在金属材料质量合格,构件形状设计合理的情况下,裂纹将在应力最大处形成,或有随机分布的特点。在这种情况下,为判别裂纹起裂的真实原因, 要特别侧重对应力状态的分析。尤其是非正常操作工况下构件的应力状态, 如超载、超温等。
主裂纹的判别方法
(1)T型法
将散落的碎片按相匹配的断口合并在一起,其裂纹形成T形。在一般情况下横贯裂纹首先开裂。主裂纹一般阻止二次裂纹扩展。
(2)分枝法
将散落碎片按相匹配断口合并,其裂纹形成树枝形:在断裂失效中,往往出现一个裂纹后,产生很多分叉或分枝裂纹。裂纹的分叉或分枝方向通常为裂纹的局部扩展方向,其相反方向指向裂源,即分枝裂纹为二次裂纹,汇合裂纹为主裂纹。
(3)变形法
将散落碎片按相匹配断口合并起来,构成原来构件的几何外形,测量其几何形状的变化情况,变形量较大的部位为主裂纹,其他部位为二次裂纹。
(4)氧化法
在受环境因素影响较大的断裂失效中,检验断口各个部位的氧化程度,其中氧化程度最严重为最先断裂者即主裂纹所形成的断口,因为氧化严重者说明断裂的时间较长。
金属的裂纹走向分析
(1)应力原则
在金属脆性断裂、疲劳断裂、应力腐蚀断裂时,裂纹的扩展方向一般都垂直于主应力的方向,当韧性金属承受扭转载荷或金属在平面应力的情况下,其裂纹的扩展方向一般平行于切应力的方向,如韧性材料切断断口。
(2)强度原则
强度原则即指裂纹总是倾向沿着最小阻力路线,即材料的薄弱环节或缺陷处扩展的情况。有时按应力原则扩展的裂纹,途中突然发生转折,显然这种转折的原因是由于材料内部的缺陷。在这种情况下, 在转折处常常能够找到缺陷的痕迹或者证据。
一般情况下, 当材质比较均匀时,应力原则起主导作用,裂纹按应力原则进行扩展,而当材质存在着明显不均匀时,强度原则将起主导作用,裂纹将按强度原则进行扩展。裂纹扩展方向到底是沿晶的还是穿晶的, 取决于在某种具体条件下, 晶内强度和晶界强度的相对比值。
应力腐蚀裂纹、氢脆裂纹、回火脆性、磨削裂纹、焊接热裂纹、冷热疲劳裂纹、过烧引起的锻造裂纹、铸造热裂纹、蠕变裂纹、热脆等晶界是薄弱环节,因此他们的裂纹是沿晶界扩展的;而疲劳裂纹、解理断裂裂纹、淳火裂纹,焊接裂纹及其他韧性断裂的情况下,晶界强度一般大于晶内强度,因此它们的裂纹为穿晶型,这时裂纹遇到亚晶界、晶界、硬质点或其他组织和性能的不均匀区时,往往会改变扩展方向。因此认为晶界能够阻碍疲劳裂纹的扩展, 这就是常常用细化晶粒的方法来提高金属材料的疲劳寿命的原因之一。
3 痕迹分析
构件失效时,由于力学、化学、热学、电学等环境因素单独或协同地作用,并在构件表面或表面层留下了某种标记,称为痕迹。
痕迹分类
(1)机械接触痕迹
构件之间接触的痕迹,包括压入、撞击、滑动、滚压、微动等单独作用或联合作用,这种痕迹称为机械接触痕迹,其特点是塑性变形或材料转移、断裂等,集中发生于接触部位,并且塑性变形极不均匀。
(2)腐蚀痕迹
由于构件材料与周围的环境介质发生化学或电化学作用而在构件表面留下的腐蚀产物及构件材料表面损伤的标记,称为腐蚀痕迹。
(3)电侵蚀痕迹
由于电能的作用,在与电接触或放电的构件部位留下的痕迹称为电侵蚀痕迹。电侵蚀痕迹分为两类。电接触痕迹由于电接触现象而在电接触部位留下的电侵蚀痕迹。静电放电痕迹由于静电放电现象面在放电部位留下的电侵蚀痕迹。
(4)热损伤痕迹
由于接触部位在热能作用下发生局部不均匀的温度变化而留下的痕迹。金属表面层局部过热、过烧、熔化、直至烧穿、表面保护层的烧焦都会留下热损伤痕迹。不同的温度有不同的热损伤颜色,且构件材料表面层成分、结构会发生变化,表面性能有所改变。
(5)加工痕迹
对失效分析有帮助的主要是非正常加工痕迹,即留在构件表面的各种加工缺陷,如刀痕、划痕、烧伤、变形约束等。
(6)污染痕迹
各种外来污染物附着在构件表面而留下的痕迹是污染痕迹。
痕迹分析主要内容
痕迹的形貌,特别是塑性变形、反应产物、变色区、分离物和污染物的具体形状、尺寸、数量及分布;
痕迹区以及污染物、反应产物的化学成分;
痕迹颜色的种类、色度和分布、反光性等;
痕迹区材料的组织和结构;
痕迹区的表面性能(耐磨性、耐蚀性、显微硬度、表面电阻、涂镀层的结合力等);
痕迹区的残余应力分布;
从痕迹区散发出来的各种气味;
痕迹区的电荷分布和磁性等。
免责声明:本网站所转载的文字、图片与视频资料版权归原创作者所有,如果涉及侵权,请第一时间联系本网删除。
相关文章
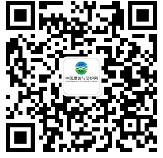
官方微信
《腐蚀与防护网电子期刊》征订启事
- 投稿联系:编辑部
- 电话:010-62316606-806
- 邮箱:fsfhzy666@163.com
- 腐蚀与防护网官方QQ群:140808414
点击排行
PPT新闻
“海洋金属”——钛合金在舰船的
点击数:8208
腐蚀与“海上丝绸之路”
点击数:6534