微生物的生命活动或其代谢产物直接或间接影响腐蚀的现象被称为微生物腐蚀(MIC),研究发现油气田系统中存在一种最主要的腐蚀性厌氧微生物——硫酸盐还原菌(SRB)。近年来,SRB在天然气生产中的影响逐渐明显,严重的SRB腐蚀会使管线发生穿孔泄漏,影响天然气生产,最终导致经济损失和环境污染。
从2017年7月起,四川某天然气区块井下油管、平台生产工艺管线、采气管线均出现了较严重的腐蚀穿孔,共影响产量7336万平方米,图1为现场腐蚀管道的宏观形貌。
图1 X区块天然气集输管道SRB腐蚀坑形貌
由图1可见,该管道上腐蚀坑边缘呈阶梯状,具有明显的攀爬现象,管道内表面坑蚀严重,坑点附近管材内表面呈黑色。X射线衍射测试发现,腐蚀产物中含有FeS,而管道输送介质中没有含硫成分。SRB生长代谢会产生含硫物质,因此初步判断造成X区块天然气集输管线腐蚀的主要原因是SRB腐蚀。
为深入研究天然气集输管线在含SRB的采出水中的腐蚀情况,新疆油田储气库有限公司和西南石油大学的研究人员通过浸泡腐蚀试验,针对X区块天然气气田的某管道建立腐蚀速率预测模型,以期为有效控制天然气气田集输管线的腐蚀提供一定的理论依据。
SRB腐蚀试验
01 试验材料与溶液
试验材料为天然气气田集输管线常用的N80S、N80、BG90SS、L245N、L360NS钢。试样尺寸为50 mm×25 mm×2 mm,试样依次经过200~1000号砂纸打磨、去离子水清洗、丙酮除油后,再将其放入酒精中浸泡,取出吹干,最后用滤纸包好,并保存于干燥器内,试验开始前需对试样进行30分钟的紫外线灭菌。
试验溶液为根据采出水配制的模拟溶液,其中含0.04125 g/L MgSO4、2.2977 g/L CaCl2、32.0346 g/L NaCl、0.436548 g/L NaHCO3,溶液pH为6.5。在模拟溶液中加入SRB,SRB加量分别为0、1×106、2×106、3×106、4×106、5×106、6×106 个/mL。
02 试验方法
分别在常压和高压条件下,对5种试验钢材料进行SRB腐蚀试验。
常压条件下,设定每组1个锥形瓶,每个锥形瓶放入2个试片,并分别向锥形瓶内倒入650 mL含不同量SRB的模拟溶液。对锥形瓶进行1小时的通氮气除氧,接着用封口膜密封瓶口,置于45 ℃恒温箱中,腐蚀时间为7天。
高压条件下,取800 mL含不同量SRB的模拟溶液置于高压釜中,向釜体内泵入氮气,使釜内压力提高至5.5 MPa,启动加热程序,加热至45 ℃,腐蚀时间为7天,每组试验各做3个平行样,达到预定时间后,切断电源,迅速取出腐蚀挂片。
试验结束后,按照GB/T 16545-2015《金属和合金的腐蚀 腐蚀试样上腐蚀产物的清除》标准对试片表面腐蚀产物和生物膜进行清洗处理,然后采用失重法计算不同条件下各试验钢的平均腐蚀速率及腐蚀速率增率,如下式所示:
式中:ri为试验钢在含SRB模拟溶液中的腐蚀速率增率,%;vi为试验钢在含SRB模拟溶液中的平均腐蚀速率,mm/a;v0为试验钢在不含SRB模拟溶液中的平均腐蚀速率,mm/a。
03 常压条件下的SRB腐蚀结果
(a) 腐蚀速率 (b) 腐蚀速率增率
图2 常压条件下各试验钢在含不同量SRB模拟溶液中的腐蚀速率及其增率
由图2a可见:常压条件下,所有试验钢的腐蚀速率均随模拟溶液中SRB含量的增加而增大;在未添加SRB的模拟溶液中,N80S钢的腐蚀速率最大,为0.187 mm/a,L245N钢的腐蚀速率最小,为0.148 mm/a;在模拟溶液中添加SRB后,N80S钢的腐蚀速率仍比其他4种试验钢大,而腐蚀速率最小的是N80钢。
以上结果说明,SRB会加速腐蚀各试验钢;在添加了不同量SRB的模拟溶液中,N80S钢最易腐蚀;在未添加SRB的模拟溶液中,L245N钢最耐腐蚀,而在模拟溶液中加入SRB后,N80钢最不易腐蚀。
由图2b可见:常压条件下在模拟溶液中加入SRB后,L245N钢的腐蚀速率增率最大,说明其受SRB的影响大,而N80钢的腐蚀速率增率最小,说明其受SRB的影响最小;5种试验钢受SRB影响的大小顺序为:L245N钢>L360NS钢>N80S钢>BG90SS钢>N80钢。
04 高压条件下的SRB腐蚀结果
(a) 腐蚀速率 (b) 腐蚀速率增率
图3 高压条件下各试验钢在含不同量SRB模拟溶液中的腐蚀速率及其增率
由图3a可见,高压条件下,所有试验钢的腐蚀速率均随模拟溶液中SRB含量的增加而增大;在未添加SRB的模拟溶液中,N80S钢的腐蚀速率最大,为0.203 mm/a,L360NS钢的腐蚀速率最小,为0.149 mm/a;在模拟溶液中添加SRB后,N80S钢的腐蚀速率仍是5种试验钢中最大的,而腐蚀速率最小的是N80钢。
以上结果说明,高压条件下无论模拟溶液中是否添加SRB,N80S钢均最易腐蚀;在未添加SRB的模拟溶液中,L360NS钢最耐腐蚀,而在模拟溶液中加入SRB后,N80钢最不易腐蚀。
由图3b可见:高压条件下在添加了SRB的模拟溶液中,L360NS钢的腐蚀速率增率最大,其最大值达80%以上,说明其受SRB的影响大,而N80钢的腐蚀速率增率最小,说明其受SRB的影响最小,表现出良好的抗细菌腐蚀性;5种试验钢受SRB影响的大小顺序为:L360NS钢>L245N钢>N80S钢>BG90SS钢>N80钢。
微生物腐蚀速率预测模型
X区块某条天然气集输管道的材料为L360钢,起点压力为5.5 MPa,起点温度为45 ℃,采出水pH为6.5,与试验条件相同。因此,基于半经验型腐蚀速率预测模型中的DW91模型,并结合该管道微生物腐蚀机理,以管道中SRB含量为变量,温度、压力、pH为定量,采用origin软件将试验所得数据代入DW91模型进行拟合,结果如图4所示。
图4 DW91模型拟合结果
根据DW91模型拟合得到微生物腐蚀速率与SRB数量之间的关系式:
式中:v为腐蚀速率,mm/a;t为管道运行温度,℃;p为管道运行压力,105 Pa;c(H+)为采出水中H+的浓度;n为SRB含量,个/mL。
运用PIPESIM软件模拟X区块天然气集输管道沿线的压力和温度参数,结果如图5和图6所示,并将参数代入式(2)中以验证腐蚀速率预测模型的适用性。管道腐蚀速率的模型预测结果与管道实际内检测数据对比如表1所示。
图5 X区块天然气集输管道沿线压力的模拟值
图6 X区块天然气集输管道沿线温度的模拟值
表1 管道腐蚀速率的模型预测结果与内检测结果
由表1可见,使用式(2)所示预测模型计算的腐蚀速率与测量值存在0.06~0.07 mm/a的差距。这是因为在实际测量时压力和温度不是定量,而是沿管线变化的。
分别以压力和温度作为变量,使用origin软件对原预测模型进行修正,得到修正的预测模型,如下式所示:
用修正后模型对管道的腐蚀速率进行预测,结果也列于表1中。由表1可见,修正后管道SRB腐蚀速率预测模型的预测值与测量值的相对误差均小于10%,该预测值更接近X区块天然气集输管道的实际SRB腐蚀速率,这说明综合考虑管道沿线温度和压力两大关键要素对原预测模型进行修正后的SRB腐蚀速率预测模型具有较好的可靠性。
结论
(1) SRB对腐蚀影响较大,即便是在试验中表现出良好抗细菌腐蚀性的N80钢,在加入SRB后,其腐蚀速率也增长了10%以上,并随着SRB含量增加而增大,而在常压下抗细菌腐蚀性弱的L245N钢,加入SRB后其腐蚀速率更是增加了20%~60%;在高压环境中加入SRB后,L360NS钢的腐蚀速率最高增长达80%。此外,相比于常压环境,高压条件下各钢材的腐蚀速率都有所增加。
(2) 结合X区块天然气集输管道基础情况和试验数据,拟合得到微生物腐蚀预测模型,计算得出的腐蚀速率与实测数据存在0.06~0.07 mm/a的差距;结合PIPESIM模拟得出检测点的压力和温度,对原模型进行修正,得到适用性更佳的微生物腐蚀预测模型。
免责声明:本网站所转载的文字、图片与视频资料版权归原创作者所有,如果涉及侵权,请第一时间联系本网删除。
相关文章
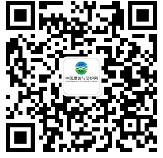
官方微信
《腐蚀与防护网电子期刊》征订启事
- 投稿联系:编辑部
- 电话:010-62316606-806
- 邮箱:fsfhzy666@163.com
- 腐蚀与防护网官方QQ群:140808414
点击排行
PPT新闻
“海洋金属”——钛合金在舰船的
点击数:8178
腐蚀与“海上丝绸之路”
点击数:6496