0 引言
目前,全球原油品质呈现下降趋势,相较于国外原油,我国的原油更呈现多样化、劣质化的特点。为了降低成本,国内许多炼化企业开始加工高硫、高酸等劣质原油,给炼油装置带来了严重的安全隐患。劣质原油中腐蚀介质大致可分为硫化物、环烷酸、氮化物、有机氯等。在原油的开采、运输和加工过程中,还常常加入含氯助剂。在生产过程中,部分物质可能会转化为硫化氢、二氧化碳、氰化物、盐酸、氨、有机酸和连多硫酸等腐蚀性物质,为装置带来巨大隐患。
为了掌握装置、管线的腐蚀情况,多种监检测方法被应用于石油石化工业,定性或定量监测设备、管线腐蚀的发生、发展过程,借此调配助剂、优化工艺防腐,并能够及时发现安全隐患,预防安全事故,提升科学化管理水平。本文介绍了几种重要的监检测技术特点,并对未来技术发展趋势进行了预测。
1 超声波技术
1.1 超声波测厚
超声波测厚是一种无损检测技术,是目前最广泛应用的材料厚度检测方法。它可以直接反应设备管线的实际厚度值,判断设备管线的减薄情况。
目前比较广泛使用的一般是脉冲式超声波测厚仪,频率一般在1~5 MHz。其原理是将在压电晶体制作的探头上施加电脉冲信号,使其发生强烈的振动产生超声波。超声波经过延迟块和耦合剂到达被测试件表面,部分反射回接受晶片;剩余部分超声波在工件内遇到缺陷或分界面时反射回来。通过两次反射波的时间差与声速计算即可得到工件厚度。由于超声波在不同材料中的传播速度不同,在对不同材料进行测厚时,需要分别校准声速。
图 1 超声波测厚仪的原理
随着技术的发展,超声波测厚的应用更加广泛,测厚温度范围更大。经过处理后的测厚数据能够较好地反映装置、管线剩余壁厚,可定量地分析其腐蚀状态,进行剩余寿命评估,对运行状态监测和安全生产,以及安排检修提供参考。
超声波测厚的缺点是其测量结果受仪器灵敏度、试件表面状态的限制,需要在试件表面涂抹耦合剂来保证测量效果。同时,手工测量也难以测量结构复杂和高空的部位。特别是温度>300℃的设备管线,表面处理难度较大,对于检测人员还存在一定危险性。为了解决这些问题,在线定点测厚系统得到了应用。中石油某公司选用了基于物联网的自动在线定点测厚系统,由带无线数据传输的测厚仪、无线网关、无线中继器和管理软件构成,可测量-100~600℃的设备管线,实现了在线定点测厚、数据录入和管理的自动化,节省了人力,减小了错误出现几率,有力保障了设备安全运行。燕山某炼油厂采用英国Permansense在线超声测厚系统,在蒸馏装置安装了22个超声波传感器,配合网关和诊断分析软件,稳定运行一年,未发生故障,仅需每3到4年在电池寿命到期时更换新电池,大大减少了维护成本。
1.2 超声导波技术
超声导波检测系统通常由探头、导波激励单元、导波接收单元和检测信号处理单元构成。使用时,将探头以阵列环绕安装在管道特定部位,由导波激励单元产生导波信号并将其放大,施加在探头上产生导波。导波在管壁中传播,管道的不连续处和形变处会引起导波传播速度的变化,产生相应回波射信号。对其进行提取、分析便可判断被测物体的损伤情况,确定缺陷的位置和尺寸。
图 2 超声导波的传播示意图
与传统超声波技术相比,超声导波具有以下优点:(1)常用的导波频率范围大约是20~100 kHz,频率较低,沿传播路径衰减很小,在理想的管道检测中可以一次检测百米以上,克服逐点扫描法的缺点,降低检测成本;(2)不需要耦合剂,也不需要对接触表面进行特殊处理;(3)可以检测难以接触的管体部位,如管道占压、穿越区域,或是管道缺陷的高发区域。
超声导波检测技术同样也存在一定局限性:(1)检测频率必须事先由实验得到;(2)无法对某一部位进行精确测量,不能反映管道的真实残余壁厚;(3)对环向缺陷的检出率比较高,而对于不超过70%壁厚的纵向裂纹很难检出;(4)对复杂管道系统检测结果的解释有一定难度;(5)沥青等外敷层会影响回波信号,减少检测距离。
超声导波检测技术目前在国内已经得到了一定应用:胜利油田[13]使用与清华大学联合设计研发的电磁超声导波检测仪对某长输原油管道进行了全面检测,检测结果与现场检验的验证符合率达86.7%。通过预埋地下的长期监测探头,能够解决超声导波检测反复开挖的缺点,节约了成本。渤海某油田使用MsS(磁致伸缩式传感器)超声导波检测技术对管线进行了腐蚀检测,两次不同位置、不同频率的检测结果均显示同一位置存在腐蚀情况,拆保温后发现减薄超3%的区域,验证了检测结果。
2 腐蚀挂片在线监测技术
腐蚀挂片检测是一种有损检测,既可安装在运行装置设备的具体部位;在一段时期内检测该设备管线的腐蚀情况,也可用于实验室模拟腐蚀环境,具有操作简单,数据可靠性高等特点;也可作为设备和管道选材的重要依据。腐蚀挂片法可同时对多种材料、多种环境进行测试。挂片可直接安装在具有代表性的工艺流程中,也可安装在特定旁路中,并根据需求改变工况条件。按照形状不同,腐蚀挂片一般分为条形挂片、棒状挂片、圆盘状挂片等等。实际在应用中,可根据需求加工成各种形状。挂片一般需要借助悬挂件安装,常见的悬挂件有螺纹连接悬挂件、法兰悬挂件、带压拆装式悬挂件。
由腐蚀挂片的质量损失可计算平均腐蚀速率:
其中,CR为腐蚀速率,mm/a;W为质量损失,g;A为腐蚀挂片暴露在腐蚀环境中的面积,m2;T为暴露时间,a;D为挂片金属的密度,g/cm3。
由腐蚀挂片的质量损失可以计算出其放置期内的平均腐蚀速率,也可以测量坑的深度来计算点蚀速率,观察点蚀的性状还能判断腐蚀的类型。另外,通过垢样分析可以判断结垢类型,并采取相应阻垢措施。
腐蚀挂片监测的缺点在于操作周期稍长,所测得的数据为装置设备在一段时间内的平均腐蚀速度,不能反映设备在某一点的腐蚀速度,因此无法用于实时在线分析。挂片本身的成本较低,但是挂片的安装、处理都需要耗费一定时间。所以腐蚀挂片监测需与其他监检测方法联用,监测设备选材和工艺防腐措施的应用效果。
长庆油田采用环状挂片,对腐蚀结垢相对严重的24座采出水回注站进行了腐蚀监测,结果显示,管线结构对局部点蚀影响很大:随着结垢程度的增加,点蚀变得明显严重。
3 在线探针
在线探针因其能够提供实时、连续的腐蚀监测数据的优点逐渐成为现代检测技术的主要发展方。按探针类型的不同,可分为pH探针、离子探针、电阻探针、电感探针和线性极化探针等等。通常一套在线探针腐蚀监测系统由腐蚀探针、数据采集器、变送器和数据处理系统等组成,腐蚀探针安装在工艺管线或设备上,得到与腐蚀速率相关的模拟信号,经变送器转换为数字信号并传送至计算机,处理后即可分析数据。借助在线探针,可以获取生产工艺信息与设备运行状态的关系,及时调整工艺参数,保证设备的正常运行。
3.1 pH探针
通常情况下,酸碱值与溶液的腐蚀性息息相关,因此对于石油石化行业中pH分析显得尤为重要。pH电极就是一种能将溶液中氢离子活度转换为电位信号的传感器。传统玻璃电极结构如图3所示,主要由以下几个部分组成:(1)敏感玻璃薄膜,能将待测溶液中的离子浓度转变为电位信号;(2)内参比体系,可以传导电位信号,由内部测量电极和内部缓冲溶液构成;(3)导线,将内导体系传导的电位信号馈送到仪器;(4)外参比体系,测量电极电位;(5)壳体,一般采用高绝缘、化学稳定性好的材料制成。当pH电极浸入待测溶液中时,在pH敏感玻璃薄膜的两侧因H+浓度不同将形成电位差,由测量电极导出。经过计算和温度补偿即可得到待测溶液的pH。为了应对更为复杂的工业环境,针对不同工艺条件固态玻璃电极、非玻璃型pH电极被开发出来,极大地丰富了探针应用范围。
图 3 pH 电极的基本结构
3.2 电阻探针
金属丝在腐蚀介质中发生腐蚀后长度不变而直径减小,截面积减小使得电阻增大。通过测试电阻丝电阻的变化即可换算直径变化量,进而计算出腐蚀速率。当所用金属丝的材质与所测量设备的材质相同时,就可用金属丝的腐蚀率近似地代表设备的腐蚀率:这就是电阻探针(ER)测试技术的基本原理。由于电阻易受温度的影响发生变化,通常会在电阻探头内串联一个温度补偿元件以消除其影响,从而减小测量误差。按照使用温度的区别,电阻探针可分为低温电阻探针和高温电阻探针,分别适用于0~260 ℃和0~450 ℃;根据探针形状,可分为丝状探针、片状探针和管式探针等,因灵敏度较高,一般多采用丝状探针。
与腐蚀挂片相同,电阻探针可适用于液相、气相等各种介质,但响应更快。且测量过程与工艺物料的导电性无关,原理直观。电阻探针的缺点是数据波动较大,试件加工较严格,另外,测量结果会受导电的腐蚀产物(如硫化铁)影响。
4 漏磁检测
漏磁检测(MFL)使用漏磁通原理:利用设备对被测件进行饱和磁化,在其内部产生磁场。当存在缺陷时,会导致缺陷处附近的磁场发生畸变,部分磁力线将穿出试件产生漏磁,通过磁敏探头检测漏磁场就可以发现管道缺陷。
图 4 漏磁检测示意图
漏磁检测不仅可以发现表面和近表面的缺陷及其尺寸,且具有非接触特性、检测速度快、成本低的优点,适用于生产期间的在线检测。但由于不接触被测试件表面,不可避免的存在提离值,减小了磁场强度;而涂层的存在也会降低检测灵敏度。另外,漏磁检测一般不适用于形状复杂的构件。
5 红外热成像
自然界中温度超过绝对零度(-273 ℃)的物体都会因分子的热运动向外辐射电磁波,其中红外线的波长在0.72~1000 μm之间。红外热成像监测是利用热感应相机的红外成像技术,通过光学元件将物体发射的红外辐射聚集到探测器上,将其转换为电信号,进而处理成可见图像,在显示屏上以灰度差或伪彩色的形式反映出被测物体表面温度的分布。
在石化行业,由于生产需要,许多设备管线是在高温条件下运行的,当出现保温脱落、腐蚀减薄等情况,表面热分布会出现异常。通过对温度分布的分析,可以监测反应器、加热炉、管线、散热器等设备运行状况,评价衬里损伤和保温效果,预测设备的运转情况,同时可以指导检修,增加检测的预知度。如图是工作人员使用福禄克Ti300便携式热像仪拍在炼厂拍摄的管线和空冷管的热成像图,可以看到局部区域温度异常(显示为红色),可能发生了腐蚀减薄。
图 5 热成像图
6 结论和展望
(1)腐蚀监检测技术为石油石化工业的安全、平稳运行提供了有力保障,愈来愈受到重视。但是每种技术都有其特点和不足,通常需要多种方法联用、相互补充来达到较好的效果;同时,超声衍射时差技术、超声相控阵技术等新技术也在逐步进入市场。
(2)监测技术的在线化仍是未来发展方向。目前油品、工艺冷凝水的分析仍然以实验室分析为主,其在线分析技术存在成本过高、精度不足的问题,相关产品的开发、更新换代仍需投入一定人力物力。
(3)多种技术的联用是建设智能化工厂的要求。借助物联网和RBI技术,构建一套完整的腐蚀数据搜集、分析系统,实现对工艺数据、腐蚀监测数据的实时监控,智能判断设备的运行状态,及时预警并提供解决方案;配合自动加注等防腐技术,完成腐蚀问题的智能化“治疗”。
免责声明:本网站所转载的文字、图片与视频资料版权归原创作者所有,如果涉及侵权,请第一时间联系本网删除。
相关文章
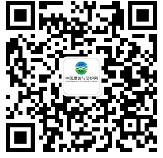
官方微信
《腐蚀与防护网电子期刊》征订启事
- 投稿联系:编辑部
- 电话:010-62316606-806
- 邮箱:fsfhzy666@163.com
- 腐蚀与防护网官方QQ群:140808414
点击排行
PPT新闻
“海洋金属”——钛合金在舰船的
点击数:8170
腐蚀与“海上丝绸之路”
点击数:6494