摘要
电镀技术常用来对已破损的零件进行修复与再制造,然而其耐磨性及耐腐蚀性能需要进一步改善。在电镀技术的基础上向镀液中添加不同浓度的 CeCl3 化合物(0、0.5、1、1.5 g / L)制备出复合镀层以探究其对电镀层性能的影响。结果表明: 在镀液中添加 CeCl3 化合物会使复合镀层中铁晶粒呈现较好的择优取向性;随着镀液中 CeCl3 化合物浓度的逐渐提升,复合镀层的显微硬度、耐磨性、耐腐蚀性均呈现出先提高后减弱的状态;当镀液中 CeCl3 化合物浓度为 0.5g / L 时,复合镀层的表面结构更为均匀、镀层中铁晶粒的排列更加致密,其显微硬度达到 611.4 HV,具有最佳的耐磨性和耐腐蚀性能。研究成果表明镀液中添加稀土 CeCl3 化合物可以大幅度提高镀层的耐腐蚀性,并在一定程度上提高镀层的耐磨性,可为实际生产中提高镀铁层的耐磨性及耐腐蚀性能提供理论指导。
关键词: 电镀 ; 复合镀层 ; 梯度浓度 ; 显微硬度 ; 耐磨性 ; 耐腐蚀性
0 前言
在远洋运输行业中,许多船舶机械零部件及船舶设备,如船舶柴油机活塞环、曲轴、轴瓦在经过长时间工作后,不可避免地会发生磨损,造成船舶设备的失效,这会极大地影响船舶运行过程中的安全性。所以,采用高效、成本较低的手段对船舶机械零部件进行强化处理是必不可少的一环,可以达到减少零件磨损和磨损后修复的作用[1]。常见的表面修复手段及修复工艺有离子注入、渗氮、渗碳或碳氮共渗等以及钢铁表面淬火、热喷涂、物理气相沉积、化学气相沉积、激光熔覆等。但是,它们都存在一定的缺点,镀铁技术与它们相比,具有明显的优势,它的沉积效率较高、成本较低,对环境污染较小,尤其在钢铁表面进行镀铁,由于两者晶格属性相同,可以制备出与基体结合强度很高的镀层。为了降低资源的消耗率,提高设备的使用寿命,可以从两方面进行改善:一是提高船舶零部件材料的耐用性,二是提高受损零部件的修复率。其中有关镀铁的表面处理技术作为成熟的工艺广泛地应用于再制造领域,并且创造了可观的社会价值和经济效益。低温无刻蚀镀铁技术是一种常见的机械零部件修复技术,在维修受损的机械零部件和需要对一些特殊材料的表面预处理时发挥着至关重要的作用[2]。该技术目前主要应用于对受损发动机曲轴、凸轮轴、传动轴、液压支柱等重要零部件的修复过程中[3]。随着科学技术的进步,传统的镀铁层已经不能满足现代工业的要求,许多研究人员通过在电镀液中加入SiC、Al2O3、MoS等制备出性能优良的多元合金镀层,使其具有优良的物化性能[4-6]。电镀技术具有效率高、成本低、操作简单、环境友好等优点,适用于复合镀层的制备[7-8]。
近期研究成果表明,在镀液中加入稀土元素改变镀液的性质[9],可以制备出性能更为优越的复合镀层。稀土元素的原子半径较大、电子结构为特殊的4f层、电负性较低和化学性能更为活泼的优点,较少的添加量即可以达到显著的改良效果,被誉为 “优异的多功能添加剂”[10]。而稀土氯化物CeCl3 因其具有独特的氧化性和极强的吸附性能,可作为添加盐应用于镀层的强化中[11]。目前稀土添加剂主要应用于镀镍与镀铬的研究中,在镀铁中相关研究较少。由于Ce盐可以较好的溶于镀液中,对镀液性能的影响较小,因此本文采用在镀液中添加不同浓度CeCl3 (0、0.5、1、1.5g/L) 化合物对复合镀层表面形貌与性能的影响,并对复合镀层的耐磨性、耐腐蚀性能进行研究,为复合镀铁层的发展提供更多理论参考。
1 试验材料与方法
基体材料为120mm×10mm×6mm的45# 钢,主要化学组成(质量分数/%)为:C(碳)0.42%~0.50%, Si(硅)0.170%~0.37%,Mn(锰)0.50%~0.80%, Cr(铬)≤0.25%,S(硫)≤0.035%,P(磷) ≤ 0.035 %,Ni(镍)≤0.30%,Cu(铜)≤0.25%, Fe(铁)余量[12]。所添加化合物为CeCl3·7H2O,浓度分别为0、0.5、1、1.5g/L。在电镀试验进行前,需对45# 钢进行前处理,试样表面依次使用金相砂纸进行打磨,经无水乙醇超声清洗15min后放入烘干箱进行烘干,最后放入密封袋里以供使用。本次试验使用的电镀槽为50L的玻璃槽,电镀液为自制镀液,镀液主要成分为FeCl2·4H2O[13],在电镀前需将镀液活化,并维持其pH值为1左右,温度在20~35℃,电镀过程分为5个阶段:交流活化预处理、交流起镀、不对称交流、小直流电镀、大直流电镀。表1列出了在电镀过程中5个阶段的工艺参数。
表1 电镀工艺参数
利用线切割机将电镀后的试样割成13mm× 3mm× 2mm的试样。切割后的试样经过200~800目的砂纸逐级打磨,直至表面光滑平整之后,使用马尔文帕科Empyrean智能X射线衍射仪(XRD) 对镀层进行物相分析,扫描速度为2(°)/min,衍射角范围为0°~90°,加速电压为40kV,管电流为30mA。将切割后的镀层试样进行镶嵌,对界面打磨抛光后采用德国卡尔蔡司(ZEISS)的扫描电子显微镜(SEM)及EDS对试样表面进行微观形貌观察,确定其元素分布。使用Cratos W50全自动显微硬度测试仪对镀层进行硬度测试,在镀层表面选取三个点,载荷为1N,载荷时间持续10s每个试样取三个点进行测试取平均值,使用Thermo Kalpha X射线电子能谱仪(XPS)对镀层元素化合价态进行分析,使用自制往复式摩擦磨损试验机测试复合镀层的摩擦力、抗黏着情况及磨损质量损失。在进行摩擦磨损试验前,使用200~800目砂纸对试样进行逐级打磨,保证所有试验试样镀层表面粗糙度为20 μm的平面。摩擦磨损试验采用直径为5mm、硬度为600HV以上的440C不锈钢销子作为摩擦副,在复合镀层表面做线性往复运动。试验机频率为40Hz,在进行摩擦磨损试验时载荷为10MPa,供油量为0.07mL/min,冲程为60mm,磨损时间为7h。采用电化学工作站测试复合镀层的极化曲线和阻抗谱的测量。试验试样的工作面积为1cm2,工作环境为3.5%的NaCl溶液,参比电极为饱和氯化钾电极,辅助电极为铂电极,扫描速度为10mV/s。
2 结果与讨论
2.1 镀层的形貌分析
图1 为不同浓度CeCl3 化合物所制备的复合镀层的表面形貌。由图1可见,采用电镀技术制备的镀层均呈现条纹结构。图1a为未掺杂CeCl3 化合物的镀层。由图可以看出,未加入CeCl3 化合物的镀层表面粗糙,存在裂痕,且镀层表面有凹坑与凸起[14]。这是由于在电沉积的过程中,基体与镀层间存在一定的渗氢现象,即氢气在镀层表面不断沉积形成氢气泡,造成金属间晶格畸变,使镀层中内应力增大,造成镀层表面缺陷[15]。当镀液中加入不同浓度的CeCl3 盐后的表面形貌分别如图1b~1d,可以看出,复合镀层的微观形貌有了一定程度的改变,镀层表面裂纹、气孔等缺陷减少,致密性得到大幅度提高。对比图1b、 1c和1d可知,镀液中CeCl3 盐浓度为0.5g/L的镀层表面结构致密,铁晶粒呈规律状紧密排列且晶粒间没有明显分界线。而继续增加镀液中CeCl3 化合物的浓度,镀层表面的致密性有所下降,且镀层表面出现凹坑、凸起和裂纹。图1的结果表明,在镀液中添加一定浓度的CeCl3 盐可以明显抑制电镀过程中的渗氢现象,从而提高镀层的表面质量。
图1 不同CeCl3 浓度下镀层的表面形貌
图2 为在镀液中添加不同浓度CeCl3 制备的镀层的截面形貌。由图2可以看出,镀液中CeCl3 浓度为0g/L时,镀层截面出现气孔与裂痕,且与基体结合存在一定缝隙,结合强度较差,随着镀液中CeCl3 浓度在一定浓度范围内逐渐提升,镀层截面结构致密,且与基体结合较好,未出现明显的分界线,且表面无明显的裂痕及剥脱区域出现。分析认为,由于Ce3+ 具有特殊的4f电子结构,其在镀液中可以在一定程度上抑制Fe2+ 的还原反应,提高阴极的电位,同时,Ce3+ 易吸附在镀层表面的活性点处,Ce3+ 的原子半径相对较大,可以抑制Fe晶体的形成和长大,起到细化晶粒的作用。而随着CeCl3 的逐渐加入,镀液中的Ce3+ 的含量逐渐提升,当其达到一定浓度以后,Ce离子抑制析氢的作用愈发明显,H+ 较难形成H2 析出,反而与Fe离子共同沉积进入镀层,使镀层中内应力增加,进而导致镀层表面形成裂痕、镀层与基体的结合强度变差。综合分析认为,在镀液中添加0.5g/L的CeCl3 化合物可以起到抑制电镀过程中的渗氢并阻止Fe晶体长大的作用,而当镀液中CeCl3 浓度高于0.5g/L时,抑制渗氢现象过于明显,镀层的表面、截面形貌反而变差。
图2 不同CeCl3 浓度下镀层的截面形貌
2.2 镀层的物相结构和成分分析
图3 为不同CeCl3 浓度下镀层的XRD图谱。从图中可以看出镀层在2θ 为44.67°、65.00°、 82.17°附近出现三处特征衍射峰,镀液中CeCl3 浓度为0g/L时镀层最高峰峰值较低,主要延Fe(110)、(200)、(211) 三个方向生长,在镀液中添加CeCl3 化合物后,镀层中Fe元素在三个取向上的峰强发生明显变化,各个衍射峰强度呈现出先提高后降低的趋势,在镀液中CeCl3 浓度为0.5g/L时,镀层的峰值最高,而当镀液中CeCl3 浓度达到1.5g/L时,镀层的峰值有一定程度的下降,但仍优于普通镀层。镀层中Fe晶粒的平均粒径可以采Debye-Scherrer方程[16-17]估算:
λ 可由Cu-k 1靶材的波长所得到,β 可以从XRD的最强峰的峰宽(FWHM)计算得到。随着镀液中CeCl3 浓度的逐渐提升,其镀层的晶粒尺寸分别为87、19、51、51nm。CeCl3 的加入可以使镀层的铁晶粒发生明显的细化。分析认为镀液中CeCl3 作为表面活性元素,易吸附在镀层晶体的活性点上如镀层的“生长点”或“生长线”处,可以有效抑制镀层中Fe晶粒的生长,起到超强的细化晶粒的作用,而镀液中Ce3+ 的含量过高时,会抑制镀液中Fe2+ 的沉积,且稀土离子之间的相互吸附会导致镀层的分布不均,影响镀层的质量,CeCl3 带来的优势反而不明显。
图3 不同CeCl3 浓度下镀层的XRD图谱
图4 为镀液中不同浓度CeCl3 化合物浓度制备的镀层经过面扫描后的EDS图谱。可以看出,所有能谱中出现了C、O、Fe元素,且在镀液中加入适量浓度的CeCl3 化合物后,镀层表面的能谱皆出现了Ce元素峰,且Fe元素峰有明显的提高 (图4b~4d)。这说明在基体表面成功制备出含有Ce元素的复合镀层,且Ce元素在镀层表面起到了明显的改善作用。当镀液中CeCl3 浓度为0.5g/L时,复合镀层表面Ce元素峰最强,且Fe元素峰强度也最高,说明复合镀层中的Ce元素起到了较好的改善作用。但当镀液中的CeCl3 浓度继续提高时,复合镀层表面Ce元素峰与Fe元素峰皆有一定程度减小。
图4 不同CeCl3 浓度下镀层的EDS能谱
图5 为本文根据XPS图谱对含有CeCl3 的复合镀层的化学成分及键合结构型作进一步分析的结果。可以看出,向镀液中添加不同浓度的CeCl3 化合物,发现复合镀层表面图谱中已经出现了Ce元素特征峰。图谱中不同浓度的Ce3d的XPS分谱如图5所示,V和U对应自旋分裂轨道3d5/2和3d3/2 [18-19]。分谱可以分为两组特征峰,分别对应Ce的 +3和 +4价态。在904.8eV和885.6eV出现的被标记为U' 和V' 的峰是Ce3+ 的特征峰,其他标记为U、U''、U''' 和V、V''、V''' 则对应Ce4+[14],这表明镀液中的CeCl3 随着沉积反应的进行在镀层中形成CeO2 与Ce2O3 两种化合物。Fe2p的分谱中可以分离出4个较为明显的有效峰,它们的形成分别与Fe2+ (710.9eV为Fe2+2p3/2和723.6eV为Fe2+2p3/2)和Fe3+(716.3eV为Fe3+ 2p3/2和730.0eV为Fe3+2p1/2)有关。
图5 不同CeCl3 浓度下镀层的XPS图谱
通过对比图5a与图5b,镀液中CeCl3 浓度为0.5g/L时,Ce元素峰值强度更高,波形更为明显,且Ce4+ 化合物含量更多。对比图5c与图5d可以看出,镀液中未加入CeCl3 所制备的镀层中Fe3+ 化合物含量更多,通过向镀液中添加CeCl3,镀层中的Fe3+ 化合物含量明显减少。分析认为Ce元素处在元素周期表的第三副族,具有较大的电荷数,可以将镀液中的Fe3+ 还原成Fe2+,阻止其与阴极区附近的OH- 结合形成Fe(OH)3 沉积在镀层中,从而提高镀层质量。
2.3 镀层的显微硬度
试验测得未加入CeCl3 化合物的镀层显微硬度为517.8HV,由图6镀层的显微硬度图可以看出,镀液中添加CeCl3 所制备的镀层硬度,随着镀液中CeCl3 化合物浓度的增加呈现出先提高后降低的趋势,其硬度处于530~600HV,与普通镀层相比得到小幅度提高。当镀液中CeCl3 化合物浓度为0.5g/L时,镀层的平均显微硬度最大,为611.4HV,相比于未加入CeCl3 的镀层有接近18.05%的提高,有一定的提升效果。但当CeCl3 化合物浓度达到1g/L时,镀层的质量变差,显微硬度有所下降,但仍优于普通镀层。
图6 不同CeCl3 浓度下镀层的显微硬度
图7 为镀液电导率,随着镀液中CeCl3 化合物浓度的提升表现出先迅速提高后小幅度降低的趋势。分析其原因,可能是Ce原子较为活泼,具有较强的活动性,当Ce原子内部电子轨道未被填满时,对镀液中游离的电子具有较强的吸附能力,可以起到导电的作用,从而提高镀液的电导率、镀层的沉积速率,在相同时间内镀层厚度更大,且Ce原子在一定程度上可以抑制镀层中铁晶粒的生长,细化晶粒[20]。而镀层边界所聚集的Ce离子与其他元素形成稀土化合物,可以在镀层的边界起到黏结的作用,有效提高镀层的强度与硬度。但镀层中Ce离子的包覆能力有限,当镀液中的Ce离子达到一定浓度后,镀液中的电导率变化趋于平缓,镀液中Fe离子的沉积速率基本稳定,镀层中的Ce离子便不能有效抑制镀层中铁晶粒的生长,反而会使镀层中铁晶粒变粗,镀层的硬度变小,镀层的质量降低[21]。
图7 不同CeCl3 浓度下镀液的电导率
2.4 镀层的耐磨性
表2 列示了镀液中加入不同浓度CeCl3 化合物所制备的复合镀层经过摩擦磨损后质量损失,通过激光共聚焦表征不同CeCl3 浓度的复合镀层的磨痕及其三维形貌如图8、9所示。
表2 摩擦磨损质量损失
图8 不同CeCl3 浓度下镀层磨痕的三维形貌
图9 不同CeCl3 浓度下镀层的磨痕形貌
由表2可以看出,镀层进行7h摩擦磨损试验后,镀层的质量损失随着镀液中CeCl3 化合物浓度的提升呈现出先减小后增加的趋势,当镀液中CeCl3 化合物浓度为0.5g/L时,镀层的磨损质量损失最小,为0.17g,镀液中CeCl3 化合物浓度为1.5g/L时,复合镀层的磨损质量损失增加到0.41g,但仍小于普通镀铁层。由图9a可以看出,当镀液中未添加CeCl3 化合物时,镀层在磨损后出现烧蚀现象,磨损形式以黏着磨损为主。这是因为未加入CeCl3 的镀层表面较为粗糙,局部镀层在摩擦力的作用下发生塑性变形,表面的一些裂纹、凸起在摩擦磨损过程中会被剪切,从镀层表面剥离,在镀层与对磨件间发生黏着磨损,造成镀层局部脱落,在长期切削应力的作用下,镀层不足以承受外加载荷,最终因疲劳磨损而脱离基体。在摩擦磨损的过程中会产生热量,镀层在摩擦热的作用下发生软化,当温度过高时,镀层会发生烧蚀,使磨痕变黑。而镀液中添加适量浓度的CeCl3 化合物后,镀层表面局部脱落及塑性变形的现象减轻,镀层的磨损形式由最开始的黏着磨损转化为磨粒磨损。镀层表面经7h摩擦磨损后未出现明显的剥落,镀层的耐磨性能得到明显的提高。而当镀液中CeCl3 为0.5g/L时,表面仅出现由磨粒磨损造成的轻微划痕且划痕最浅,如图9b所示。
镀液中的CeCl3 可以起到细化晶粒[22]的作用,且会使镀层中铁晶粒的排列更加规则,呈现择优取向性,使得镀层中铁晶粒排列更为均匀致密,且因为Ce离子原子半径较大,可以填补在镀层中铁晶粒的缺陷相,减少镀层表面的缺陷及裂痕,提高镀层的质量。而Archard定律表明,镀层的摩擦磨损性能与其硬度成正比,镀层表面硬度的提高对镀层的耐磨性极为有利[23]。但随着镀液中CeCl3 浓度的继续提升,Ce离子的存在反而会抑制镀液中Fe离子的沉积,使镀层中铁晶粒分布不均匀,镀层内应力集中,镀层易产生裂痕剥落,磨削现象更加严重,镀层的耐磨性也会随之降低。
2.5 镀层的耐腐蚀性能
图10 为经过电镀所制备的试样在3.5%NaCl溶液中的Tafel极化曲线,利用Tafel外推法可以计算电化学腐蚀相关特征参数如表3所示。由图10和表3可以清晰地看出,镀液中添加CeCl3 化合物后,镀层的腐蚀电位正移,腐蚀电流密度降低,镀层的耐腐蚀性能得到提高;并且随着镀液中CeCl3 化合物浓度的逐渐增加,镀层的抗腐蚀性能呈现先提高后降低的趋势,镀液中CeCl3 化合物浓度为0.5g/L时镀层的耐腐性能达到最佳,腐蚀电位从-1.027V提高至-0.780V,腐蚀电流密度由116降低到73.86 μA·cm-2。当镀液中CeCl3 浓度增加到1g/L时,镀层的表面质量下降,开始出现凹坑与裂痕,腐蚀电流密度增大,但仍优于未添加CeCl3 化合物的镀层。因此,镀液中添加CeCl3 化合物所制备的复合镀层拥有更加优越的耐腐蚀性能[24]。
图10 不同CeCl3 浓度下镀层的极化曲线
表3 极化曲线参数值
进一步地,采用电化学阻抗谱(EIS)法对不同浓度样品镀层的腐蚀电化学性质进行了比较。图11是不同浓度样品镀层的Nyquist阻抗谱图(Nyquist Plot),Zre为阻抗值的实部,Zim为阻抗值的虚部,所有Nyquist曲线存在高频下的半圆,而半圆的直径即表示电荷转移电阻(R p),从 R p的大小能够得出样品耐腐蚀性的强弱。基本的规律是:R p越大,即圆弧的直径越大,则样品的耐腐蚀性越好。为了更加具体地比较不同浓度样品镀层的耐腐蚀性能,进一步用Z-view软件对Nyquist图进行拟合,可以得到确切的阻抗数值,采用的等效电路模型如图11插图所示,其中,R s 和 R p分别代表溶液阻抗和电荷转移阻抗,CPE代表常相位角元件[25]。表4列出了根据拟合结果计算得到的各个元件的参数值。
图11 不同CeCl3 浓度下镀层的交流阻抗谱
表4 等效电路参数值
结果表明,镀液中CeCl3 浓度为0g/L所制备的镀层具有最小的 R p,只有565.0 ,表明不添加CeCl3 化合物时,镀层的防腐蚀性能不理想。 0.5g/L的样品具有最大的 R p,高达942.3 ,表明在这个添加浓度下,复合镀层的内阻较大,电荷传递过程容易受阻,不容易发生腐蚀反应,即添加了CeCl3 化合物后,镀层的防腐蚀性能显著提高了。随着CeCl3 含量的进一步升高,复合镀层的 R p 值逐渐降低,在1.5g/L的样品中,复合镀层具有较小的 R p,为663.2 。
综合结果表明:本试验采用0.5g/L的CeCl3 添加进入镀层后,可以显著提高镀层的耐腐蚀性能,这主要是因为CeCl3 的添加使得镀层的表面缺陷位置减少,镀层中铁晶粒的排列更加规则,镀层表面更加致密,在3.5%NaCl溶液中暴露腐蚀区域较少;镀液中Ce离子可以有效抑制镀液中H+ 与Fe3+ 的沉积,因此可以有效抑制在电镀过程中的渗氢反应,阻止Fe(OH)3 夹杂在镀层中[26];夹杂在镀层中的Ce离子可以使镀层具有更好的择优取向性能,镀层内部的电位差减小,使得镀层的腐蚀阻力有所增大,因此镀层的电化学腐蚀倾向降低。但是,当镀液中CeCl3 浓度超过0.5g/L的时候,较高浓度的CeCl3 可能会形成胶状的氢氧化物而沉淀,破坏了金属离子的有序沉积,镀层的缺陷位置暴露出来,因此耐腐蚀性能反而降低了。
3 结论
(1)镀液中的CeCl3 可以起到细化晶粒的作用,使镀层的显微硬度大幅度提升。当镀液中CeCl3 化合物浓度为0.5g/L时,复合镀层的显微硬度最大,为611.4HV。
(2)复合镀层经过7h的摩擦磨损后的磨痕宽度、深度随着镀液中CeCl3 化合物浓度的增加呈现出先降低后升高的规律。镀液中未添加CeCl3 化合物所制备的镀层发生较为严重的黏着磨损,添加适量的CeCl3 化合物后,镀层的耐磨性得到大幅提升,镀液中CeCl3 化合物浓度为0.5g/L时,复合镀层的耐磨性最佳。
(3)与单纯镀铁层相比,添加适量浓度CeCl3 化合物的复合镀层腐蚀电位更高,腐蚀电流密度较低,电荷转移电阻更大,复合镀层具有更好的耐腐蚀性能。当镀液中CeCl3 化合物浓度为0.5g/L时,复合镀层的耐腐蚀性能最佳。稀土组分的引入为电镀技术提供了新思路。
参考文献: 略
免责声明:本网站所转载的文字、图片与视频资料版权归原创作者所有,如果涉及侵权,请第一时间联系本网删除。
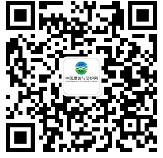
官方微信
《腐蚀与防护网电子期刊》征订启事
- 投稿联系:编辑部
- 电话:010-62316606-806
- 邮箱:fsfhzy666@163.com
- 腐蚀与防护网官方QQ群:140808414