0 前言
金属腐蚀是金属在服役过程中,与周围腐蚀介质发生化学或电化学反应而失效的过程[1-2]。我国国家工程院侯保荣院士在“我国腐蚀状况及控制战略研究”重大咨询项目报告指出,我国腐蚀成本约占我国GDP的3.34%,由金属腐蚀带来的直接和间接经济损失远远大于由火灾、旱灾、地震、台风和水灾等其他自然灾害的总和。其中海洋环境是最为严酷的自然腐蚀环境,海洋腐蚀损失约占总腐蚀损失的1/3左右。
大气腐蚀环境是金属材料接触最多的环境介质,约有80%的金属构件在大气环境中服役[3-4]。我国有1.8万多km的海岸线,金属材料多处于海洋大气腐蚀环境中,潮湿水汽和腐蚀性介质会吸附在金属表面并形成一层薄液膜,这层薄液膜是金属发生电化学腐蚀反应的必要条件。而海洋大气中的气象因素直接影响着金属在大气区的腐蚀速率,主要包括含盐粒子量、相对湿度、温度、日照时间和腐蚀性气体等因素[5-6]。其中含盐粒子量和腐蚀性气体对金属在海洋大气成分中的腐蚀影响最大。具体而言,各种因素的作用如下:
(1)含盐粒子量。在海洋大气区,空气中含有大量的卤盐,当卤盐粒子沉积到金属表面后,可以吸附大气中的水蒸气形成薄液膜电解液,卤盐中的阴阳离子可以构成离子通道,加快金属腐蚀,同时,氯离子还可以破坏金属的钝化膜及致密的腐蚀产物膜,大大降低金属的耐蚀性能。
(2)相对湿度。金属在海洋大气区的腐蚀反应主要是一种薄液膜下的电化学反应,大气中水蒸气在金属表面凝聚而生成薄液膜和空气中氧气通过薄液膜变成溶解氧是发生大气腐蚀的两个基本条件。其中,薄液膜的厚度对金属的腐蚀速率影响最大,一般情况下,大气的相对湿度越大,薄液膜的厚度越厚。
(3)日照时间。日照时间的长短可以影响金属表面薄液膜的厚度。日照时间较长时,薄液膜的厚度降低甚至消失,使金属腐蚀的总量减少。太阳光中的紫外线也会对碳钢金属腐蚀速率产生一定影响,紫外辐照强度越大,碳钢表面锈层厚度增加,金属表面粗糙度增大,同时碳钢主要腐蚀产物FeOOH的晶型也随着紫外辐照强度的变化而发生变化。
(4)温度。海洋大气区的温度对金属表面水蒸汽的凝聚、薄液膜的厚度、薄液膜的电阻以及阴极还原过程中溶解氧的含量及变化产生直接影响。此外,温度还影响着海洋大气区的湿度,进而决定金属表面薄液膜的厚度及其溶解氧浓度。当相对湿度大于金属的临界相对湿度时,气温的影响就十分显著,温度每增加10℃,金属的腐蚀反应速度增大约2倍;当海洋大气相对湿度低于金属临界相对湿度时,气温对海洋大气腐蚀的影响较小。
(5)腐蚀性气体。在海洋工业大气腐蚀环境中,酸性气体(主要为氮氧化物和硫氧化物)吸附在金属表面的薄液膜中,不仅会导致金属发生酸性溶解,也会破坏金属的钝化膜和腐蚀产物膜,加快金属的腐蚀速率[7-10]。
在沿海地区的输电塔处于苛刻海洋大气腐蚀环境中,长期经受海洋大气中水汽、氧气和多种复杂盐分的腐蚀。根据GB/T19292.1—2018中对大气腐蚀环境的分类,滨海地区的大气腐蚀等级可达C5级,对碳钢、锌、铜和铝等金属均具有严重腐蚀作用,尤其是对碳钢的腐蚀速率可达80~200μm/a。在这种苛刻海洋大气腐蚀环境下,对输电塔进行涂层防护既是延长输电铁塔服役寿命的必要措施,也能降低腐蚀导致的经济损失和安全隐患。
目前在电力系统中对输电铁塔主要采用单组分冷喷锌防腐涂料。尽管冷喷锌防腐涂料具有施工方便,成本低等优点,但其在输电铁塔镀锌层上的附着力差,也无法进行带锈施工,不能满足输电铁塔高空作业时带锈涂装的要求。
本文针对输电铁塔在苛刻海洋工业大气腐蚀环境下出现镀锌层快速腐蚀失效和铁塔涂装相对困难的难题,研制出一种低表面处理石墨烯改性重防腐涂料体系,具体包括低表面处理石墨烯防腐底漆,环氧石墨烯阻隔中间漆和聚氨酯耐候面漆。通过实验室性能测试、环境考核试验和现场示范工程涂装,并每隔6个月对服役涂层进行防护性能评价。结果表明,研制的石墨烯改性重防腐涂料对输电铁塔在苛刻海洋大气腐蚀环境下的综合防护寿命预计可达10年以上。
1 试验部分
1.1 涂层研制
石墨烯防腐底漆研制:以环氧树脂E20作为涂料的主要成膜物质,聚酰胺为固化剂,环氧磷酸酯和多聚磷酸铝为铁锈转化剂。取25~35g环氧树脂E20于分散机中,将二甲苯、正丁醇以一定的比例混合并搅拌均匀后作为涂料的稀释剂,加入15~20g稀释剂将树脂充分溶解。将1g石墨烯(GO)、0.02g石墨烯分散剂、0.5~1.5g消泡剂、5~10g环氧磷酸酯和多聚磷酸铝以及35~55g填料(由膨润土、氧化铁红和滑石粉组成)加入至上述已溶解的树脂溶液中,充分搅拌并研磨直至50μm细度,即制得低表面处理石墨烯防腐底漆。
环氧石墨烯阻隔中间漆:以环氧树脂E20和环氧树脂E44作为涂料的主要成膜物质,改性胺为固化剂。取20~30g混合环氧树脂于分散机中,然后将二甲苯、正丁醇以7∶3质量比混合并搅拌均匀即作为涂料的稀释剂,加入15~20g稀释剂将树脂充分溶解。将0.5g石墨烯、0.01g石墨烯分散剂、0.5~1.5g流平剂以及30~60g填料(由绢云母、硫酸钡和滑石粉组成)加入至上述已溶解的树脂溶液中,充分搅拌并研磨至80μm细度,即制得环氧石墨烯阻隔中间漆。
聚氨酯耐候面漆:以纯丙烯酸树脂为主要成膜物质,异氰酸酯为固化剂。取30~40g纯丙烯酸树脂和10~20g三甲苯于分散机中,再添加50~70g紫外光吸收助剂(由包膜金红石型钛白粉、沉淀硫酸钡和片状铝粉组成),然后加入5~10g聚酰胺蜡和0.1g分散剂BYK392,研磨至50μm细度后,添加流平剂和消泡剂,用搅拌机分散均匀,即得聚氨酯耐候面漆。
1.2 涂层性能检测和环境暴晒试验
在实验室内按照国标检测方法对漆膜基本性能和防腐性能进行性能检测。其中,对低表面处理石墨烯防腐底漆、环氧石墨烯阻隔中间漆和聚氨酯耐候面漆主要考察以下性能:①施工性能:细度(GB/T1724)、固含量(GB/T1725)、干膜时间(GB/T1728);②物理性能:附着力(GB/T5210)、柔韧性(GB/T1731)、抗冲击性(GB/T1732);③耐化学性能:耐盐水浸泡和耐酸碱浸泡性能(GB/T1763)。而对石墨烯改性重防腐三层复合涂层体系,主要考察复合涂层体系的服役性能,如附着力(GB/T5210)、耐水冷凝(GB/T13893.2)、耐盐雾(GB/T1771)、耐候性(GB/T1865)、耐循环老化性能(ISO 12944-9),以及自然环境下的耐久性能。
自然环境下耐久性能采用曝晒试验方法如下:在实验室制备用于曝晒试验的涂层样板,然后将复合涂层放置到位于海南、宁波的大气腐蚀实验站进行外场大气曝晒试验。在一定曝晒周期后取回试样,实验室内实时评价石墨烯改性重防腐涂料的环境服役性能,并根据检测结果指导配方的优化升级。
1.3 涂层示范工程应用和服役寿命评价
将定型石墨烯改性重防腐涂料对宁波市北仑区的国网宁波供电公司北坞2321线10级输电铁塔进行示范涂装,每级输电铁塔质量约20t,每级输电铁塔涂装面积约500m2。宁波市北仑区属于典型的海洋工业大气腐蚀环境,有大型发电厂、石油炼化装置和炼钢厂,输电铁塔服役后表面镀锌层腐蚀明显,部分铁塔甚至出现镀锌层腐蚀穿孔现象[11],涂装重防腐涂料对保障输电铁塔的安全稳定运行尤为重要。输电铁塔防腐施工属于高空作业,无法进行基材喷砂和打磨处理,钢丝刷简单清污后,直接涂装石墨烯防腐底漆。防腐施工工艺详见表1。
表 1 输电铁塔的防腐施工工艺
采用《ISO 4628色漆和清漆涂层性能试验后的评级方法》对已经涂装好的输电铁塔进行服役性能检测,检测间隔时间为6个月,石墨烯改性重防腐涂料的涂层评级包括涂层变色失光、粉化、开裂、起泡、长霉、生锈、剥落等7个指标。
2 结果与讨论
2.1 石墨烯重防腐涂层性能评价
研制的低表面处理石墨烯防腐底漆直接喷涂在腐蚀后的镀锌基材上,进行附着力测试。采用压缩空气喷涂,底漆干膜厚度为80μm,拉拔仪为PosiTestAT-MAdhesionTester。石墨烯防腐底漆在13.15MPa压力下从镀锌基材表面剥离(图1a),镀锌基材上仍有环氧涂料(图1b),断裂位于高固体份环氧涂料内部,说明设计的低表面处理石墨烯防腐底漆与镀锌基材结合良好,漆膜中添加的环氧磷酸酯和多聚磷酸铝可与镀锌层表面腐蚀产物发生铁锈转化反应,并形成一层致密的漆膜[12-13]。通过5次平行测试,防腐涂层在镀锌钢板上拉拔附着力为11.33~13.79MPa。同时在马口铁上对底漆的漆膜基本性能(外观、百格附着力、柔韧性、抗冲击)进行了测试,底漆漆膜基本性能测试结果见表2。
图 1 石墨烯防腐底漆拉拔附着力测试
表 2 低表面处理石墨烯防腐底漆性能参数
关于石墨烯改性防腐涂层的研究表明,均匀分散在环氧中间漆中的二维层状石墨烯可以提高漆膜的致密性和耐水性能。为了评估不同含量石墨烯对复合涂层耐腐蚀性能及其抗腐蚀性介质渗透性能的影响,将涂层浸入质量分数为3.5%的NaCl溶液中进行电化学测试,研究不同浸泡时间下涂层腐蚀性能和抗渗透能力的变化[14]。石墨烯复合涂层的Bode、Bode-Phase和Nyquist曲线如图2所示。显然,石墨烯能显著增强涂层的防腐性能。但在石墨烯质量分数为1.00%时,由于涂层内部石墨烯(GO)与环氧基质(EP)之间存在界面相容性问题,耐腐蚀性能反而降低。进一步通过ZSimpWin软件对涂层电化学结果进行拟合,R(QR)型电路可作为腐蚀介质到达基体之前的拟合电路模型,R(QR)(QR)型电路可作为腐蚀介质到达基体后的拟合电路模型[15]。在浸泡35d后各涂层体系的电化学拟合结果如表3所示,其中RC为涂层电容,QC为涂层电阻,Rct为基体电荷转移电阻,Qdl为基体电荷转移产生的双电层电容。根据拟合结果可知,纯环氧涂层和石墨烯质量分数为0.25%的环氧涂层在质量分数为3.50%的NaCl溶液中浸泡35d后已被NaCl溶液完全渗透,使得两者的电化学阻抗谱中出现了代表基体腐蚀的第二个时间常数及对应的Rct和Qdl值。而石墨烯质量分数为0.50%和1.00%的环氧涂层即使经过35d浸泡后仍然具有良好的阻隔作用,阻抗谱中只有一个容抗弧,并且石墨烯质量分数为0.50%的环氧涂层在浸泡35d后涂层电阻RC值达到4.26GΩ·cm2,相比于石墨烯质量分数为1.00%的环氧涂层RC值(1.36GΩ·cm2)提高了约3倍,表明加入石墨烯质量分数在0.50%时对环氧涂层阻隔性能和防腐效果具有更明显的提升。
图 2 涂层在质量分数为 3.5%的 NaCl 溶液中浸泡不同时间的电化学测试结果[14]
表 3 涂层在质量分数为 3.5%的 NaCl 溶液中 浸泡 35 d 后的电化学参数
根据 Brasher-Kingsbury 公式(式(1))可计算涂层在不同浸泡阶段的吸水率大小(图 3)。
式中,XV(%)代表涂层中水的体积分数,Cc(0)和Cc(t)分别代表涂层在初始时间和浸泡时间达t时的电容。在腐蚀性介质中浸泡35d后,加入石墨烯质量分数为0.25%、0.50%和1.00%的各环氧涂层吸水率大小分别为4.98±0.10、2.60±0.08和3.31±0.09,较纯环氧涂层(6.42±0.19)分别降低22.4%、59.5%和48.4%。结果表明,添加均匀分散的石墨烯能显著增强涂层的抗腐蚀性介质渗透能力。这归因于涂层中高纵横比纳米片的平行排列,充分发挥了纳米片的阻隔作用,显著延长了腐蚀性介质的扩散路径[16]。而且,随着均匀分散的石墨烯含量的增加,涂层抗腐蚀性介质的渗透能力越强。但过多石墨烯片的添加容易引起界面相容性问题发生,使得涂层阻隔作用减弱,抗渗透能力反而降低。因此,添加0.5%质量分数平行排列石墨烯的复合涂层展现出优异的物理屏蔽效果和抗腐蚀性介质渗透能力[17-18],所制备的中间漆漆膜基本性能测试结果见表4。
图 3 石墨烯复合涂层在质量分数为 3.5%的 NaCl 溶液中浸泡不同时间后的吸水率[14]
表 4 环氧石墨烯阻隔中间漆性能参数
聚氨酯耐候面漆主要起屏蔽和颜色美观功能,因此主要考察其耐老化性能。通过GB/T1865《色漆和清漆人工气候老化和人工辐射暴露》试验对面漆进行人工加速耐老化测试,面漆老化1440h后,漆膜无起泡、锈蚀、开裂和脱落现象,漆膜变色1级,失光1级。面漆漆膜基本性能测试结果见表5。
表 5 聚氨酯耐候面漆性能参数
同时,根据ISO 9223中C5级大气腐蚀环境特征,对底漆、中间漆和面漆复合涂层的综合防护性能进行测试,测试项目包括附着力、耐水凝性、耐盐雾、耐老化和耐盐雾循环老化。其中耐盐雾循环老化的测试照片见图4,复合涂层在划线处有锈迹,但划线处腐蚀扩展小于2mm,未划线处涂层完整,没有发生明显腐蚀迹象。复合涂层的其他性能测试结果见表6。测试结果表明,研制的石墨烯改性重防腐涂料体系满足C5级涂料要求,可用于苛刻海洋大气腐蚀环境的涂装。
图 4 石墨烯改性重防腐涂料的耐盐雾循环老化的测试照片
表 6 石墨烯改性重防腐复合涂层性能参数
2.2 石墨烯重防腐涂层外场大气曝晒试验
对研制的石墨烯改性重防腐涂料分别在典型热带海洋大气腐蚀环境和海洋工业大气腐蚀环境进行环境考核试验,试验地点位于文昌某基地和浙江宁波北仑区的电网材料大气土壤腐蚀实验站,截至目前涂层已经挂样5年,详见图5。通过ISO 4682《色漆和清漆涂层老化的评级方法》每隔6个月对涂层的防护性能进行评价,发现大气曝晒5年后,位于文昌和宁波的两个大气曝晒试验站的石墨烯改性重防腐涂料的变色、粉化、开裂、起泡、长霉、生锈、剥落情况见表7,石墨烯改性重防腐涂料在海洋工业大气腐蚀环境曝晒5年后,面漆出现轻微变色现象,涂层的综合防护等级为最高级0级;在热带海洋大气腐蚀环境中曝晒5年后,出现变色和粉化现象,涂层的综合防护等级为1级,说明在强紫外辐照区域,聚氨酯面漆的耐老化性能有待提高,建议采用耐候性强的氟碳面漆。
图 5 环境曝晒试验基地
表 7 石墨烯改性重防腐涂层大气曝晒试验结果
2.3 石墨烯重防腐涂层示范涂装
对研制好的石墨烯重防腐涂层在国网宁波供电公司北坞2321线10级输电铁塔示范涂装,涂装铁塔总质量约150t,采用四道施工工艺,即涂第一道石墨烯防腐底漆,涂第二道石墨烯中间漆,涂第三道耐候面漆,涂第四道耐候面漆,总膜厚不低于260μm,具体工艺要求如下。
(1)对铁塔进行手工钢丝刷清除表面附着物,主要为尘土和树枝等。
(2)采用石墨烯底漆(1道,涂膜厚度约80μm)+石墨烯中间漆(1道,涂膜厚度约100μm)+耐候面漆(2道,每道涂膜厚度约40μm)体系;涂层总厚度≥280μm,检测每道漆膜的干膜厚度和附着力,检测合格后进行下一道工序。
(3)每道涂料的涂装间隔不能小于 8 h,一般 24 h 后再涂覆下一道漆。
(4)湿度大于 RH85,温度低于 5 ℃时,停止 施工,雨天禁止施工。
由于铁塔构造特殊性和高空施工作业,涂装工人需有高空作业证,并有严格安全防护措施,铁塔施工目前还是采用人工刷涂方式,涂装效果见图 6。
图 6 石墨烯重防腐涂料在输电铁塔上涂装效果图
2.4 石墨烯重防腐涂层服役性能评价
石墨烯改性重防腐涂料在铁塔上涂装竣工时间为2016年8月,后续每隔6个月对漆膜的防护性能进行评价,评价指标主要包括漆膜光色、色差和附着力,由于采用人工刷涂方式,漆膜膜厚不均匀,总体膜厚都达到施工设计要求,漆膜各项指标检测结果见表8。其中2021年3月对北坞2321线06级铁塔表面涂层的附着力现场测试照片见图7。涂层服役54个月后,漆膜的光泽度逐渐降低,色差△E逐渐增大,说明面漆涂层逐渐老化。铁塔整体没有出现漆膜脱落、长霉和鼓泡现象,但出现轻微变色现象,变色为1级,部分铁塔的潮湿底部,漆膜表面出现长青苔现象。但复合涂层的百格附着力在0~1级,拉拔附着力8.56~11.37MPa,说明设计的石墨烯改性重防腐涂层对输电铁塔的综合防护性能良好。
表 8 石墨烯改性重防腐涂层在 6#和 8#铁塔上性能测试结果
图 7 国网宁波北坞 2321 线 06 级铁塔漆膜现场测试照片(检测时间:2021 年 3 月)
根据ISO 12944《色漆和清漆钢结构防腐涂层保护体系》规定的腐蚀环境,膜厚和服役寿命的关系(在海洋大气腐蚀环境C5-M下,长效防护涂层服役寿命达到10年以上,其总膜厚≥280μm),以及JT/T722《公路桥梁钢结构防腐涂装技术条件》对漆膜防护年限与漆膜耐老化性能的要求(复合涂层耐盐雾和耐老化≥3000h),并结合大气曝晒试验和铁塔涂层现场检测结果[19],预计研制的石墨烯改性重防腐涂料对输电铁塔在苛刻海洋大气腐蚀环境下的综合防护寿命可达10年以上[20-21]。
3 结论
(1)研制了一种石墨烯改性重防腐涂层体系,包括低表面处理石墨烯防腐底漆、环氧石墨烯阻隔中间漆和聚氨酯耐候面漆,在实验室性能测试中表现出良好的耐久性能。
(2)石墨烯改性重防腐涂层体系的实际服役性能与实验室耐久性能加速测试的结果相符,在输电铁塔上的防护寿命可达 10 年以上,具有优异的长效防护能力。
(3)石墨烯改性重防腐涂层体系中聚氨酯面漆在曝晒和实际服役过程中表现出变色和光泽度降低,需要进一步提升其耐老化性。
参考文献
[1] 魏宝明.金属腐蚀理论及其应用[M].北京:化学工业出版社,2008. WEI Baoming.Theory and application of metal corrosion[M].Beijing:Chemical Industry Press,2008.(in Chinese)
[2] 刘雨薇.碳钢在南沙大气环境中的腐蚀行为与机理研究[D].合肥:中国科学技术大学,2020. LIU Yuwei.Corrosion behavior and mechanism of carbon steel in Nansha atmosphere[D].Hefei:University of Science and Technology of China,2020.(in Chinese)
[3] 陈新彦,陈大明,陈旭,等.热带海洋大气环境中耐候钢腐蚀特征与机理的研究[J].腐蚀科学与防护技术,2018,30(2):149-155. CHEN Xinyan,CHEN Daming,CHEN Xu,et al.Research on corrosion characteristics and mechanism of weathering steel in tropical ocean atmospheric environment[J].Corrosion Science and Protection Technology,2018,30(2):149-155.(in Chinese)
[4] LIU shuan,SUN Huyuan,SUN Lijuan,et al.Effects of pH and Cl- concentration on corrosion behavior of the galvanized steel in simulated rust layer solution[J].Corrosion Science,2012,65:520-527
[5] 刘栓,周开河,方云辉,等.环境因素对纯Zn在饱和 Zn(OH)2 溶液中腐蚀行为的影响 I-Cl-浓度和pH值[J].中国腐蚀与防护学报,2016,36(6):522-528. LIU Shuan,ZHOU Kaihe,FANG Yunhui,et al.Influence of environmental factors on the corrosion behavior of pure Zn in saturated Zn(OH)2 solution I-Cl- concentration and pH value[J].Journal of Chinese Society for Corrosion and protection,2016,36(6):522-528.(in Chinese)
[6] 周开河,方云辉,徐孝忠,等.环境因素对纯Zn在饱和 Zn(OH)2溶液中腐蚀行为的影响 II——温度和溶解氧浓度[J].中国腐蚀与防护学报,2016,36(6):529-534. ZHOU Kaihe,FANG Yunhui,XU Xiaozhong,et al.The influence of environmental factors on the corrosion behavior of pure Zn in saturated Zn(OH)2 solution II— temperature and dissolved oxygen concentration[J].Journal of Chinese Society for Corrosion and protection,2016,36(6):529-534.(in Chinese)
[7] LIU Z J,WANG W,WANGJ,et al.Study of corrosion behavior of carbon steel under seawater film using the wire beam electrode method[J].Corrosion Science,2014,80:523-527.
[8] XIN S S,LI M C.Electrochemical corrosion characteristics of type 316L stainless steel in hot concentrated seawater[J].Corrosion Science,2014,81:96-101.
[9] LIU W M,ZHOU Q J,LI L S,et al.Effect of alloy element on corrosion behavior of the huge crude oil storage tank steel in seawater[J].Journal of Alloys and Compounds,2014,598:198-204.
[10] YUAN S J,LIANG B,ZHAO Y,et al.Surface chemistry and corrosion behaviour of 304 stainless steel in simulated seawater containing inorganic sulphide and sulphatereducing bacteria[J].Corrosion Science,2013,74:353-366.
[11] 刘栓,周开河,方云辉,等.石墨烯重防腐涂层在国网输电铁塔防护的应用研究[J].中国材料进展[J],2017,36(6):442-447. LIU Shuan,ZHOU Kaihe,FANG Yunhui,et al.Research on the application of graphene heavy-duty anticorrosive coating in the protection of transmission towers of the State Grid[J].Progress in Chinese Materials[J],2017,36(6):442-447.(in Chinese)
[12] 刘栓,周开河,吴跃斌,等.石墨烯改性重防腐涂料在世界最高输电铁塔的防腐应用[J].腐蚀科学与防护技术,2019,31(1):114-120. LIU Shuan ZHOU Kaihe,WU Yuebin,et al.Anticorrosion application of graphene modified heavy-duty anti-corrosion coating in the world’s tallest transmission tower[J].Corrosion Science and Protection Technology,2019,31(1):114-120.(in Chinese)
[13] 丁纪恒,刘栓,顾林,等.环氧磷酸酯/水性环氧涂层的耐蚀性能[J].中国表面工程,2015,28(2):126-131. DING Jiheng,LIU Shuan,GU Lin,et al.Corrosion resistance of epoxy phosphate/waterborne epoxy coating[J].China Surface Engineering,2015,28(2):126-131.(in Chinese)
[14] ZHU X B,YAN Q Q,LI C C,et al.Self-alignment of cationic graphene oxide nanosheets for anticorrosive reinforcement of epoxy coatings[J].Chemical Engineering Journal,2020,389:124435.
[15] ZHU X B,ZHAOHC,WANGLP,et al.Bioinspired ultrathin graphene nanosheets sandwiched between epoxy layers for high performance of anticorrosion coatings[J].Chemical Engineering Journal,2021,410:128301.
[16] 王玉琼,刘栓,刘兆平,等.石墨烯掺杂水性环氧树脂的隔水和防护性能[J].电镀与涂饰,2015,34(6):314-320. WANG Yuqiong,LIU Shuan,LIU Zhaoping,et al.Water barrier and protective properties of graphene-doped waterborne epoxy resin[J].Plating & Finishing,2015,34(6):314-320.(in Chinese)
[17] LIU S,GU L,ZHAO H C,et al.Corrosion resistance of graphene-reinforced waterborne epoxy coatings[J].Journal of Materials Science & Technology,2016,32:425-431.
[18] GU L,LIU S,ZHAO H C,et al.Facile preparation of water-dispersible graphene sheets stabilized by carboxylated oligoanilines and their anticorrosion coatings[J].ACS Applied Materials and Interfaces,2015,7:17641-17648.
[19] 张晓东,赵钺,郭燕芬,等.FEVE 涂层的老化与服役寿命预测研究[J].涂料工业,2013,43(5):62-65. ZHANG Xiaodong,ZHAO Yue,GUO Yanfen,et al.Aging and service life prediction research of FEVE Coating[J].Paint Industry,2013,43(5):62-65.(in Chinese)
[20] 陈群志,康献海,刘健光,等.军用飞机腐蚀防护与日历寿命研究[J].中国表面工程,2010,23(4):1-6 CHEN Qunzhi,KANG Xianhai,LIU Jianguang,et al.Research on corrosion protection and calendar life of military aircraft[J].China Surface Engineering,2010,23(4):1-6.(in Chinese)
[21] 关瑞辰.船舶涂层服役性能评价及管理系统的设计与开发[M].北京:北京化工大学,2009. GUAN Rruichen.Design and development of service performance evaluation and management system of ship coating[M].Beijing:Beijing University of Chemical Technology,2009.(in Chinese)
免责声明:本网站所转载的文字、图片与视频资料版权归原创作者所有,如果涉及侵权,请第一时间联系本网删除。
-
标签: 海洋工业大气腐蚀环境, 镀锌输电铁塔, 防护机理 , 石墨烯改性重防腐涂料
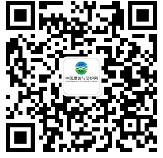
官方微信
《腐蚀与防护网电子期刊》征订启事
- 投稿联系:编辑部
- 电话:010-62316606-806
- 邮箱:fsfhzy666@163.com
- 腐蚀与防护网官方QQ群:140808414