摘要:目的提高水利机械常用ZG06Cr13Ni4Mo 马氏体不锈钢的抗汽蚀、冲蚀性能。方法采用超高速激光熔覆技术在ZG06Cr13Ni4Mo 马氏体不锈钢基体上制备Stellite 6 涂层。用X 射线衍射仪(XRD)分析涂层物相。用扫描电子显微镜(SEM)及能谱(EDS)研究涂层组织结构特征。用HV-1000 型显微硬度计测试了涂层的硬度分布。用超声振动汽蚀试验设备研究了涂层抗汽蚀性能。用喷射型冲蚀磨损试验机研究了涂层的抗冲蚀性能。通过SEM 分析试样表面的汽蚀、冲蚀形貌。结果STELLITE 6 涂层厚度约为400 μm,主要由FCC 结构的γ-Co 枝晶固溶体与Cr23C6 共晶碳化物组成。涂层致密程度较高,涂层中Co、Cr 的质量分数分别为55.6%、27.6%,完美地继承了粉末的原始成分。Stellite 6 涂层的显微硬度为570HV0.1,与不锈钢基体相比提升了2.3 倍,热影响区深度仅为70 μm。随着超声振动汽蚀试验周期的延长,涂层与不锈钢失重线性增加,冲蚀24 h 后涂层的损失量为1.1 mg,不锈钢的损失量为8.0 mg。经过180 s 的小角度(30°)冲蚀试验后,Stellite 6 涂层的损失量为9.1 mg,不锈钢的损失量为13.5 mg。结论超高速激光熔覆Stellite 6涂层很好地保留了熔覆层粉末的原始成分,涂层组织结构致密、稀释率低、热影响区窄,高硬涂层显著提高了水利机械常用ZG06Cr13Ni4Mo 马氏体不锈钢的抗汽蚀及冲蚀性能。
关键词:超高速激光熔覆;Stellite 6 涂层;显微结构;汽蚀;冲蚀
水利机械的各种不锈钢部件在水下复杂多相流状态下容易受到汽蚀损伤,同时水中的泥沙还会磨削固壁表面,对零部件产生汽蚀与冲蚀联合作用的破坏,使得其使用寿命缩短,运行效率降低,从而容易导致停机维修,存在较大的安全风险和经济损失[1]。因此,汽蚀、冲蚀成为当前水利机械急需解决的技术问题之一。在满足结构设计、运行条件两方面前提下,制备抗汽蚀、冲蚀性能良好的防护涂层成为防止水利机械材料破坏的关键所在[2]。
目前,材料表面防护技术主要有电镀、热喷涂、离子注入、激光熔覆等方法。其中,使用热喷涂、电镀方法制备的涂层与基体的结合为机械结合,结合力不高,涂层不够致密,存在一定的孔隙率,因此涂层的抗汽蚀、冲蚀性能较差[3]。离子注入由于其改性层较薄,在泥沙冲刷和水流空化汽蚀联合作用下很快损失掉,因此其提高材料抗汽蚀、冲蚀性能的作用有限[4]。激光熔覆与传统表面加工工艺相比,具有能量密度高、加工精度高且可控性好、涂层与基体为冶金结合等优点。工艺恰当时,激光熔覆层的稀释率低,可以较好地保留熔覆材料的原始成分[5]。但是,传统激光熔覆扫描速度慢,涂层制备成本较高。扫描速率增加时,传统激光熔覆层会出现带状组织、大尺寸孔隙,且晶粒生长具有明显的取向性,涂层性能下降[5]。2017 年,德国弗劳恩霍夫激光研究所(FraunhoferILT)与德国亚琛联合科技公司(ACunity)提出了超高速激光熔覆技术[6-7]。与传统激光熔覆不同,高速熔覆时,送粉器将粉末均匀地送入激光光束,粉末在到达基体前已经被加热至熔融状态[8]。因此,超高速激光熔覆具备效率更高、涂层稀释率更低、对基体热输入更小等优点[9-12]。该技术很好地解决了传统激光熔覆技术存在的问题,是潜在的用于制备高性能抗汽蚀、冲蚀涂层的先进技术。
近年来,Stellite 6 合金以其良好的高温性能和较好的耐蚀耐磨性能[13],常被用于制备水轮机抗汽蚀合金涂层[14]、汽轮机叶片表面的耐水蚀涂层[15]。目前,主要采用超音速火焰喷涂与传统激光熔覆制备Stellite 6 合金涂层,尚未出现关于超高速激光熔覆Stellite 6 合金涂层的报道。因此,在大幅提升生产效率的同时,超高速激光熔覆制备的Stellite 6 涂层组织结构,以及涂层是否满足叶片等工件的耐汽蚀性能需求目前尚不清楚。
水轮机叶片需要长期承受高压冲击、磨损和侵蚀,通常选用综合性能较好的ZG06Cr13Ni4Mo 马氏体不锈钢作为叶片材料。基于此,本工作采用超高速激光熔覆技术,在ZG06Cr13Ni4Mo 马氏体不锈钢基材表面制备Stellite 6 涂层,研究了涂层微观组织特征,以及对水利机械常用ZG06Cr13Ni4Mo 马氏体不锈钢的抗汽蚀、冲蚀性能的提升作用。
1 试验
1.1 涂层制备
基材为ZG06Cr13Ni4Mo 马氏体不锈钢,熔覆前使用酒精清洗基材表面,去除油污。熔覆材料为Stellite 6(粒度15~45 μm)合金粉末,如图1 所示,Stellite 6 粉末为球形,能够保证较好的流动性。熔覆前将粉末置于120 ℃烘箱中烘烤30 min,去除粉末中的水分。基体与熔覆粉末成分如表1 所示。采用最大输出功率为2.5 kW 的RFL-A2500D 半导体激光器以及自行设计的超高速激光熔覆环形同轴送粉头(粉末利用率超过85%)开展超高速激光熔覆试验。激光器光斑输出为直径2 mm 的圆形光斑。采用ZB-80F 双桶送粉器送粉,送粉气采用Ar 气(纯度>99.9%)。采用FANUC 六轴联动机器人带动熔覆头按照设定程序移动,熔覆工艺参数如表2 所示。
图1 粉末形貌
表1 基体与合金粉末的成分
表 2 超高速激光熔覆工艺参数
1.2 结构表征及性能测试
将Stellite 6 的熔覆试样切割成5 mm×5 mm×2 mm 的小块,在酒精中超声清洗10 min 后,放入120 ℃烘箱中烘烤20 min,冷却至室温后使用冷镶胶制样并打磨抛光。将抛光后的试样使用王水[V(HCl)∶V(HNO3)=3∶1]腐蚀20 s,而后放入酒精中超声清洗5 min。
采用 Bruker D8 ADVANCE A25 型X 射线衍射仪(XRD)分析涂层物相,扫描角度为10~90°,扫描速度为10 ( ° )/min。采用与S-3400 型SEM 及配套的能谱仪(EDS)表征涂层的组织形貌与成分分布。依据GB/T 4340.1—2009 测试涂层及基体的显微维氏硬度,采用HV-1000 型显微硬度计,沿层深方向每隔50 μm 测1 次显微硬度,试验载荷为0.981 N,保载时间为15 s。
采用广州新栋力超声电子设备有限公司生产的NP-BSD-01-20-844 型超声波伸缩振动汽蚀试验设备进行汽蚀试验。试样尺寸为?16 mm×10 mm。试验前使用SiC 砂纸将试样表面打磨至平滑。设备试验功率为1.2 kW,试验温度为(25±3)℃,试验所用水为去离子水。试验在室温下进行,试样浸没在水中的深度约为3 mm,每隔一段时间将汽蚀试样取出,烘干后使用精度为0.1 mg 的分析天平称重,绘制汽蚀失重曲线。汽蚀结束后使用日立S-3400 型扫描电子显微镜观察汽蚀形貌,分析汽蚀机理。
采用自制的喷射型冲蚀磨损试验机进行30°下的冲蚀试验。将试样切割成25 mm×20 mm×4 mm 的长方体,试验前使用SiC 砂纸将试样表面打磨至平滑。选用粒径为150 μm 的不规则Al2O3 沙粒,沙粒流量为1 g/s,每隔30 s 将冲蚀试样取出,放入酒精中超声清洗5 min,烘干后使用精度为0.1 mg 的分析天平称量,绘制冲蚀失重曲线。冲蚀结束后使用日立S-3400型扫描电子显微镜观察冲蚀形貌,分析冲蚀机理。
2 结果及分析
2.1 涂层显微组织结构
Stellite 6 涂层腐蚀后的显微组织结构如图2 所示。由图2a 可知,涂层组织均匀致密,厚度约为400 μm,未出现明显的气孔、裂纹等缺陷,涂层质量良好。熔覆层表面没有明显的起伏,起伏低于10 μm,表面平整度高,这表明熔覆焊道之间的搭接效果较好。涂层与基体为冶金结合,界面结合良好(图2b)。涂层/基体界面至涂层顶部的组织结构由以平面晶和枝状晶为主逐渐转变为以树枝晶和胞状晶为主。这是由于激光熔覆时,熔池深度方向的温度梯度与冷却速度差异较大,因此熔覆组织会出现较为明显的分层现象。由快速凝固理论[16-17]可知,熔体的凝固方式及凝固后的组织形貌由形状因子G/R 决定,凝固后的组织尺寸由冷却速率决定。熔池凝固时,由于与基体冷金属接触,温度梯度很大,界面处瞬时结晶速度很小,因而出现冶金结合层,呈现无特征的平面状结晶。随着结晶过程的进行,固-液逐步向熔池中部(图2c)与顶部(图2d)推进,温度梯度逐渐减小而凝固速度逐渐增大,并出现较为明显的成分过冷现象,因而出现树枝晶与少量的胞状晶。未凝固的液态金属在已凝固的枝晶间重新形核并充满整个空间,形成细小的共晶组织。
图 2 Stellite 6 涂层不同位置的显微组织结构
对涂层不同位置的元素分布进行EDS 分析如表3 所示,其中A 点为涂层枝晶组织,B 点为涂层共晶组织。由表3 可知,涂层中Co、Cr 的质量分数分别为55.6%、27.57%,与粉末的原始成分相比,变化量均在1.5%以内。超高速激光熔覆技术的原理决定了基体元素与涂层的互扩散能够得到有效抑制[18],粉末的化学成分能够比较完美地继承到涂层。另外,涂层中的枝晶A 与共晶B 的化学成分存在明显差异,枝晶A 中富含Co,而共晶B 与枝晶A 相比,Cr 的含量更高,这与传统激光熔覆工艺所制备的涂层成分偏析趋势一致[15]。
表 3 Stellite 6 涂层不同位置的主要化学成分
2.2 涂层物相分析
超高速激光熔覆Stellite 6 涂层的XRD 图谱如图3 所示。从图3 中可以看出,Stellite 6 涂层主要由FCC结构的γ-Co 与Cr23C6 组成。熔池在凝固过程中,作为溶质的Fe、Cr 等合金元素溶入Co 晶格,形成置换固溶体。作为高熔点、高硬度的碳化物,Cr23C6 在熔池冷却过程中优先在晶界和枝晶间析出,并且还能与γ-Co 固溶体发生共晶转变,形成共晶体[19]。Cr23C6的析出特性决定了其在涂层中存在弥散分布特征,其高硬度特性能够提升涂层硬度,起到弥散强化的作用,进而提升涂层的耐磨性能。同时,研究表明,Cr23C6 的晶界析出特性还能达到抑制涂层晶粒长大的作用[20]。
图 3 Stellite 6 涂层的XRD 图谱
γ-Co 固溶体发生共晶转变,形成共晶体[19]。Cr23C6的析出特性决定了其在涂层中存在弥散分布特征,其高硬度特性能够提升涂层硬度,起到弥散强化的作用,进而提升涂层的耐磨性能。同时,研究表明,Cr23C6 的晶界析出特性还能达到抑制涂层晶粒长大的作用[20]。
2.3 涂层硬度
图4 为Stellite 6 涂层的显微硬度分布图。其中从左到右分别为涂层、热影响区及基体的硬度分布曲线。Stellite 6 涂层的平均硬度为570HV0.1,基体的平均硬度为249HV0.1,涂层硬度约为基体硬度的2.3倍。涂层的高硬度除了与材质本身有关外,还与制备工艺息息相关。涂层在凝固过程中会析出Cr23C6 强化相,Fe、Cr 也会固溶于Co 中形成固溶强化相[21],二者会显著提高涂层的显微硬度。另外,基于超高速激光熔覆快速冷却特征,Cr23C6 抑制晶粒生长而形成细晶,诱发细晶强化。
图 4 Stellite 6 涂层的显微硬度分布
此外,由于超高速激光熔覆显著降低了基体的热输入,基体的热影响区仅为70 μm 左右,与传统激光熔覆200 μm[22-23]以上的热影响区相比,超高速激光熔覆的热输入显著降低,可有效防止基材性能弱化。在用于薄壁部件表面熔覆时,能够有效控制基材的热变形,实现薄板材料低变形熔覆。
2.4 涂层抗汽蚀性能
经过24 h 的超声振动汽蚀试验后,不锈钢基体与Stellite 6 涂层的累计汽蚀失重曲线如图5 所示。其中,不锈钢的累计损失量达到8.0 mg,Stellite 6 涂层的累计损失量为1.1 mg,Stellite 6 涂层的累计损失量仅为基体的13%。高速激光熔覆在基体制备Stellite 6涂层后,工件抗汽蚀能力提升7 倍以上。对比图中2条曲线可知,随着汽蚀时间的延长,不锈钢与涂层的失重均线性增加,不同的是Stellite 6 涂层的失重速率为不锈钢的1/7。
图5 基体与Stellite 6 涂层的累计汽蚀失重
经历 24 h 汽蚀试验后,除了边缘区域外,基体表面大部分区域都产生了明显的汽蚀损伤,如图6 所示。其中,中心区域的汽蚀损伤最严重,出现了明显的汽蚀坑。其主要原因为冲击力在试样中心最大,向四周辐射递减。由图6c 和图6d 可知,基体中心汽蚀区域呈现出明显的蜂窝状汽蚀形貌,同时汽蚀坑呈现出较为明显的塑性断裂特征。基体ZG06Cr13Ni4Mo为低碳马氏体不锈钢,其室温组织主要由高硬度的板条马氏体与较软的铁素体等组成。由于马氏体硬度较高,抵抗冲击的能力较强,空泡溃灭产生的冲击力不易造成剥落,而铁素体硬度低,在冲击力的作用下容易剥落[24]。因此,不锈钢表面产生明显的浮凸形貌。另外,由于力学性能区别较大,在空泡溃灭产生的冲击作用下马氏体与铁素体在界面处易产生应力集中[25-26]。当应力大于材料的屈服强度时微裂纹形成,微裂纹的扩展与合并形成汽蚀孔洞。
经历 24 h 的汽蚀后,Stellite 6 涂层表面主要发生了塑性变形,在低倍下观察不到明显的汽蚀痕迹,在高倍下可以看到稀疏而弥散分布的微小汽蚀坑(图7c),表现出优良的抗汽蚀性能。通过图4 可知,Stellite6 涂层硬度约为基体硬度的2.3 倍,硬度的提升有助于Stellite 6 涂层提高抗汽蚀性能。同时,相较于ZG06Cr13Ni4Mo 马氏体不锈钢,Stellite 6 涂层的显微组织主要为高硬度的Cr23C6 相弥散分布在γ-Co 中形成的共晶体,并呈现致密的定向凝固枝晶特征,其在空泡溃灭时产生的能量冲击下物相不易剥落[27]。对于 Stellite 6 涂层,经历24 h 的汽蚀后,其表面在低倍下观察不到明显的汽蚀痕迹,在高倍下可以看到稀疏、弥散分布的微小汽蚀坑(图7c),表现出优良的抗汽蚀性能。由前述讨论可知,Stellite 6 涂层均匀致密,无孔隙、裂纹等缺陷,有效地避免汽蚀过程中缺陷引起的应力集中,有助于涂层抗汽蚀性能的发挥。由图3 可看出,涂层主要由γ-Co 与Cr23C6等碳化物组成。γ-Co 较软,在空泡溃灭所产生的冲击作用下首先发生塑性变形,随后塑性变形在Cr23C6等碳化物边界累积。因此,在汽蚀过程中,γ-Co 与Cr23C6 等碳化物的界面处会产生较高的应力集中,当应力超过其强度后,裂纹萌生、扩展引起碳化物剥落[28-29],形成如图7 所示的汽蚀坑。研究表明[30],汽蚀能够诱发马氏体相变,促使γ-Co(FCC)向ε-Co(HCP)转变,而相变能降低应力集中。此外,由于密排六方晶型结构容易产生孪晶,所以ε-Co 的出现不但能够有效耗散汽蚀过程中的冲击能,而且孪晶还可以将晶粒分成若干小片,限制了位错的自由程,对Stellite 6涂层有较为明显的强化作用[31]。同时,相变过程中引起的体积膨胀,可在材料表面产生压应力层,阻止微裂纹的形核和扩展[32]。
图 6 ZG06Cr13Ni4Mo 马氏体不锈钢基体汽蚀24 h 后的表面形貌
图 7 Stellite 6 涂层汽蚀24 h 后的表面形貌
由图 4 可以看出,Stellite 6 涂层的平均硬度为570HV0.1,基体的平均硬度为249HV0.1,涂层硬度约为基体硬度的2.3 倍。此外,由于γ-Co 为奥氏体相,层错能较低,拥有较多的滑移系且位错的滑移与传播都比较容易。因此,在汽蚀的冲击作用下易发生塑性变形,产生大量的形变位错,随着变形的累积,位错缠结与塞积等现象不断加剧,位错运动困难,从而导致变形阻力增大,涂层硬度增加[29,31]。同时,随着汽蚀的进行,高硬的ε-Co 相体积分数增加,也会提升涂层硬度。在三者的共同作用下,汽蚀过程中Stellite 6 涂层的硬度远高于不锈钢基体。因此,Stellite6 涂层拥有更优异的抗汽蚀能力。
2.5 涂层抗冲蚀性能
30°冲蚀角度下,ZG06Cr13Ni4Mo 马氏体不锈钢与Stellite 6 涂层的累计失重曲线如图8 所示。由图8可以看出,在30°冲蚀角度下,经过180 s 的冲蚀后,基体的冲蚀损失量为13.5 mg,Stellite 6 涂层的冲蚀损失量为9.1 mg,Stellite 6 涂层的冲蚀损失量为基体的67%,表明在30°的小角度冲蚀条件下,Stellite 6涂层拥有更好的抗冲蚀性能。
图8 基体与Stellite 6 涂层的累计失重(30°冲蚀角度)
图9 冲蚀后试样的表面形貌
30°冲蚀角度下,不锈钢基体与Stellite 6 涂层的表面形貌如图9 所示。可以看出,基体与Stellite 6涂层的冲蚀形貌相似,二者的冲蚀表面都呈现出波浪状的褶皱并与冲蚀介质的流动方向一致。高硬的Al2O3 砂粒可看作刚性粒子,在30°下以足够的动能撞击试样表面,使材料表面发生微切削,形成犁沟,此时材料受到挤压将在犁沟两侧翻转隆起,随着Al2O3 的不断冲击,材料表面形成了明显的犁沟切削特征。此时,基体与Stellite 6 涂层的磨损主要以切削模型为主,与Finnie 提出的微切削理论模型相符合[33-34]。对于金属等韧性材料,微切削是主要冲蚀机制,并且在小角度冲蚀时,材料的硬度是决定材料抗冲蚀性能的主要因素[35-36]。Stellite 6 涂层硬度约为基体硬度的2.3 倍,能够抵抗Al2O3 沙粒的切入,减缓其对涂层表面的挤压与切削。此外,Stellite 6 涂层中弥散分布的Cr23C6等高硬碳化物有效阻止了Al2O3 对涂层的挤压与切削,提高了涂层的抗冲蚀性能。同时,Stellite 6 涂层组织结构均匀致密,涂层中不存在孔隙、微裂纹等缺陷,减缓了裂纹的萌生与扩展。因此,Stellite 6 涂层的致密结构、高硬特性及Cr23C6 弥散强化作用,决定了其耐冲蚀能力显著高于马氏体不锈钢基体。
3 结论
1)采用超高速激光熔覆在ZG06Cr13Ni4Mo 马氏体不锈钢基体上制备了厚度约为400 μm 的Stellite6 涂层,涂层致密且与基体呈冶金结合,涂层主要由FCC 结构的γ-Co 枝晶固溶体以及Cr23C6 碳化物组成。
2)采用超高速激光熔覆Stellite 6 涂层的平均硬度值约为570HV0.1,与不锈钢相比提升了2.3 倍。同时,本文参数下超高速激光熔覆Stellite 6 涂层的热影响区约为70 μm。
3)随超声振动汽蚀时间的延长,Stellite 6 涂层与不锈钢失重均线性增加,但Stellite 6 涂层的失重增加率仅为不锈钢的13%。
4)30°冲蚀试验后,Stellite 6 涂层的冲蚀损失量为不锈钢基体的67%,Stellite 6 涂层表现出比基体更佳的抗冲蚀性能。
参考文献:
[1]张小彬, 刘常升, 陈岁元, 等. 不锈钢表面激光熔覆抗空蚀涂层技术研究进展[J]. 材料导报, 2007, 21(10):87-89.ZHANG Xiao-bin, LIU Chang-sheng, CHEN Sui-yuan, et al. Reserch Progress in Anti-Cavitation Laser Cladding Technique for Surface of Stainless Steel[J]. Materials Review, 2007, 21(10):87-89.
[2]王再友, 龙霓东, 朱金华. 抗空蚀材料研究应用进展[J]. 材料开发与应用, 2001, 16(6):34-38.WANG Zai-you, LONG Ni-dong, ZHU Jin-hua. Review on Material Resistant to Cavitation Erosion and Its Application[J]. Development and Application of Materials, 2001, 16(6):34-38.
[3]娄建新, 刘丹, 张旋, 等. 热喷涂FeCrBSiNbW涂层结构演变及空蚀性能[J]. 中国表面工程, 2014, 27(5):74-79.LOU Jian-xin, LIU Dan, ZHANG Xuan, et al. Microstructure Evolution and Cavitation Erosion of the FeCrBSiNbW Coatings Prepared by Arc Spraying Process[J]. China Surface Engineering, 2014, 27(5):74-79.
[4]吴建华, 柴恭纯. 离子注入技术在水轮机材料空蚀改性中的应用[J]. 水利水运科学研究, 1994(3):279-283.WU Jian-hua, CHAI Gong-chun. Effects of Ion Implantation on Surface Modification of Cavitation Damage for Turbine Materials[J]. Journal of Nanjing Hydraulic Research Institute, 1994(3):279-283.
[5]LIU Jian, LI Jia, CHENG Xu, et al. Effect of Dilution and Macrosegregation on Corrosion Resistance of Laser Clad AerMet100 Steel Coating on 300M Steel Substrate[J]. Surface and Coatings Technology, 2017, 325:352-359.
[6]LOU Li-yan, ZHANG Yu, JIA Yun-jie, et al. High Speed Laser Cladded Ti-Cu-NiCoCrAlTaY Burn Resistant Coating and Its Oxidation Behavior[J]. Surface and Coatings Technology, 2020, 392:125697.
[7]SCHOPPHOVEN T, GASSER A, WISSENBACH K, et al. Investigations on Ultra-High-Speed Laser Material Deposition as Alternative for Hard Chrome Plating and Thermal Spraying[J]. Journal of Laser Applications, 2016, 28(2):022501.
[8]董会, 韩燕, 付安庆, 等. 快速激光熔覆Ni/不锈钢堆焊层组织及耐蚀性能研究[J]. 表面技术, 2019, 48(5):21-27.DONG Hui, HAN Yan, FU An-qing, et al. Microstructure and Corrosion Resistance of Ni/Stainless Steel Surfacing Layer Deposited via High-Speed Laser Cladding[J]. Surface Technology, 2019, 48(5):21-27.
[9]娄丽艳, 李成新, 张煜, 等. 低功率超高速激光熔覆FeCr合金薄涂层微观结构与表面形貌演化[J]. 燕山大学学报, 2020, 44(2):116-124.LOU Li-yan, LI Cheng-xin, ZHANG Yu, et al. Microstructure and Surface Morphology Evolution of FeCr Alloy Thin Coatings Deposited by Ultra-High Speed Laser Cladding with Low Laser Power[J]. Journal of Yanshan University, 2020, 44(2):116-124.
[10]XU Qing-long, ZHANG Yu, LIU Sen-hui, et al. High- Temperature Oxidation Behavior of CuAlNiCrFe High- Entropy Alloy Bond Coats Deposited Using High-Speed Laser Cladding Process[J]. Surface and Coatings Technology, 2020, 398:126093.
[11]李俐群, 申发明, 周远东, 等. 超高速激光熔覆与常规激光熔覆431不锈钢涂层微观组织和耐蚀性的对比[J]. 中国激光, 2019, 46(10):1002010.LI Li-qun, SHEN Fa-ming, ZHOU Yuan-dong, et al. Comparison of Microstructure and Corrosion Resistance of 431 Stainless Steel Coatings Prepared by Extreme High-Speed Laser Cladding and Conventional Laser Cladding[J]. Chinese Journal of Lasers, 2019, 46(10):1002010.
[12]李朝晖, 李美艳, 韩彬, 等. 高压柱塞高速激光熔覆镍基合金涂层组织和耐磨性[J]. 表面技术, 2020, 49(10):45-54.LI Zhao-hui, LI Mei-yan, HAN Bin, et al. High-Pressure Plunger High-Speed Laser Cladding Nickel-Based Alloy Coating Structure and Wear Resistance[J]. Surface Technology, 2020, 49(10):45-54.
[13]李丽, 孙峰, 张尧成. 固溶处理对激光熔覆Stellite 6合金涂层性能的影响[J]. 表面技术, 2017, 46(1):78-81.LI Li, SUN Feng, ZHANG Yao-cheng. Effect of Solution Treatment on the Performance of Laser Cladding of Stellite 6 Alloy Coating[J]. Surface Technology, 2017, 46(1):78-81.
[14]许宏伟, 虞鸿江, 赵明, 等. 水轮机抗汽蚀合金涂层性能评价[J]. 腐蚀与防护, 2018, 39(8):613-617.XU Hong-wei, YU Hong-jiang, ZHAO Ming, et al. Evaluation of Properties of Anti-Cavitation Alloy Coatings on Hydraulic Turbine[J]. Corrosion & Protection, 2018, 39(8):613-617.
[15]任超, 李铸国, 疏达, 等. 17-4PH不锈钢表面激光熔覆Stellite 6涂层组织及耐水蚀性能[J]. 中国激光, 2017, 44(4):0402010.REN Chao, LI Zhu-guo, SHU Da, et al. Microstructure and Water Erosion Resistance Property of Stellite 6 Coating by Laser Cladding on 17-4PH Stainless Steel Surface[J]. Chinese Journal of Lasers, 2017, 44(4):0402010.
[16]李明喜, 何宜柱, 孙国雄. Co基合金激光熔覆层组织及近表面结晶方向[J]. 东南大学学报(自然科学版), 2002, 32(6):932-935.LI Ming-xi, HE Yi-zhu, SUN Guo-xiong. Microstructure and Crystallization Direction of Laser Cladding Co-Based Alloy[J]. Journal of Southeast Univwrsity (Natural Science Edition), 2002, 32(6):932-935.
[17]张晓东, 董世运, 徐滨士, 等. St6钴基合金激光熔覆层显微组织及冲击磨料磨损性能[J]. 应用激光, 2011, 31(1):82-85.ZHANG Xiao-dong, DONG Shi-yun, XU Bin-shi, et al. Microstructure and Impact Abrasive Wear Resistance of the St6 Cobalt-Based Alloy Laser Cladding Layer[J]. Applied Laser, 2011, 31(1):82-85.
[18]WANG Hong-yu, ZUO Dun-wen, SUN Yu-li, et al. Microstructure of Nanometer Al2O3 Dispersion Strengthened Ni- Based High-Temperature Protective Coatings by Laser Cladding[J]. Transactions of Nonferrous Metals Society of China, 2009, 19(3):586-591.
[19]斯松华, 袁小敏, 何宜柱. 激光熔覆钴基合金涂层的组织结构[J]. 激光杂志, 2002, 23(4):58-59.SI Song-hua, YUAN Xiao-min, HE Yi-zhu. Microstructure of Laser Cladding Co- Based Alloy Coating[J]. Laser Journal, 2002, 23(4):58-59.
[20]覃怀鹏, 陈海涛, 郎宇平, 等. 非金属夹杂物对439M铁素体不锈钢耐点蚀性能的影响[J]. 热加工工艺, 2016, 45(10):89-92, 96.QIN Huai-peng, CHEN Hai-tao, LANG Yu-ping, et al. Effects of Non-Metallic Inclusions on Pitting Corrosion Resistance of 439M Ferritic Stainless Steel[J]. Hot Working Technology, 2016, 45(10):89-92, 96.
[21]ZHANG Hui, HE Yi-zhu, PAN Ye, et al. Synthesis and Characterization of NiCoFeCrAl3 High Entropy Alloy Coating by Laser Cladding[J]. Advanced Materials Research, 2010, 97-101:1408-1411.
[22]LIU Hong-xi, ZHANG Xiao-wei, JIANG Ye-hua, et al. Microstructure and High Temperature Oxidation Resistance of In-Situ Synthesized TiN/Ti3Al Intermetallic Composite Coatings on Ti6Al4V Alloy by Laser Cladding Process[J]. Journal of Alloys and Compounds, 2016, 670:268-274.
[23]LIU Z, CHAN K C, LIU L, et al. Bioactive Calcium Titanate Coatings on a Zr-Based Bulk Metallic Glass by Laser Cladding[J]. Materials Letters, 2012, 82:67-70.
[24]DI V CUPPARI M G, SOUZA R M, SINATORA A. Effect of Hard Second Phase on Cavitation Erosion of Fe-Cr-Ni- C Alloys[J]. Wear, 2005, 258(1-4):596-603.
[25]柳伟, 郑玉贵, 刘常升, 等. Cr-Mn-N奥氏体-铁素体不锈钢的空蚀行为[J]. 金属学报, 2003, 39(1):85-88.LIU Wei, ZHENG Yu-gui, LIU Chang-sheng, et al. Cavitation Erosion Behavior of Cr-Mn-N Austenite-Ferrite Stainless Steel[J]. Acta Metallrugica Sinica, 2003, 39(1):85-88.
[26]张小彬, 刘常升, 朱杰, 等. 大型水轮机叶片马氏体不锈钢的超声空蚀行为[J]. 东北大学学报, 2006, 27(12):1335-1338.ZHANG Xiao-bin, LIU Chang-sheng, ZHU Jie, et al. Cavitation Erosion Behavior of Martensitic Stainless Steel for Hydraulic Turbine Blades[J]. Journal of Northeastern University, 2006, 27(12):1335-1338.
[27]鄂猛, 胡红祥, 国旭明, 等. 钴基和镍基涂层的微观组织及空蚀性能[J]. 材料热处理学报, 2018, 39(1):90-96.E Meng, HU Hong-xiang, GUO Xu-ming, et al. Microstructure and Cavitation Erosion Resistance of Cobalt-Based and Nickel-Based Coatings[J]. Transactions of Materials and Heat Treatment, 2018, 39(1):90-96.
[28]张小彬, 臧辰峰, 陈岁元, 等. CrNiMo不锈钢激光熔覆NiCrSiB涂层空蚀行为[J]. 中国有色金属学报, 2008, 18(6):1064-1069.ZHANG Xiao-bin, ZANG Chen-feng, CHEN Sui-yuan, et al. Cavitation Erosion Behaviour of NiCrSiB Coatings on CrNiMo Stainless Steel by Laser Cladding[J]. The Chinese Journal of Nonferrous Metals, 2008, 18(6):1064-1069.
[29]雷玉成, 李涛, 秦敏明, 等. 304不锈钢TIG熔覆钴合金涂层的耐空蚀性能[J]. 焊接学报, 2011, 32(7):9-12.LEI Yu-cheng, LI Tao, QIN Min-ming, et al. Cavitation Erosion Resistance of Co Alloy Coating on 304 Stainless Steel by TIG Cladding[J]. Transactions of the China Welding Institution, 2011, 32(7):9-12.
[30]WOODFORD D A. Cavitation-Erosion-Induced Phase Transformations in Alloys[J]. Metallurgical Transactions, 1972, 3(5):1137-1145.
[31]秦承鹏, 郑玉贵. 17-4PH不锈钢表面激光熔覆钴基合金涂层的空蚀行为研究[J]. 腐蚀科学与防护技术, 2011, 23(3):209-213.QIN Cheng-peng, ZHENG Yu-gui. Cavitation Erosion Behavior of a Laser Clad Co-Based Alloy on 17-4PH Stainless Steel[J]. Corrosion Science and Protection Technology, 2011, 23(3):209-213.
[32]国旭明, 郑玉贵, 姚治铭. CrMnB堆焊合金抗空蚀和冲刷磨损性能的研究[J]. 金属学报, 2002, 38(9):936-940.GUO Xu-ming, ZHENG Yu-gui, YAO Zhi-ming. Cavitation Erosion and Erosive Wear Resistance of CrMnB Overlayers[J]. Acta Metallrugica Sinica, 2002, 38(9):936-940.
[33]FINNIE I. Some Observations on the Erosion of Ductile Metals[J]. Wear, 1972, 19(1):81-90.
[34]FINNIE I, MCFADDEN D H. On the Velocity Dependence of the Erosion of Ductile Metals by Solid Particles at Low Angles of Incidence[J]. Wear, 1978, 48(1):181-190.
[35]潘牧, 罗志平. 材料的冲蚀问题[J]. 材料科学与工程, 1999, 17(3):92-96.PAN Mu, LUO Zhi-ping. Erosion of Materials[J]. Materials Science and Engineering, 1999, 17(3):92-96.
[36]姜心, 张来斌, 樊建春, 等. 冲蚀角度对40CrNi2Mo材料冲蚀磨损性能的影响[J]. 润滑与密封, 2012, 37(6):24-26.JIANG Xin, ZHANG Lai-bin, FAN Jian-chun, et al. Effect of Impact Angle on Erosive Resistance of 40CrNi2Mo[J]. Lubrication Engineering, 2012, 37(6):24-26.
免责声明:本网站所转载的文字、图片与视频资料版权归原创作者所有,如果涉及侵权,请第一时间联系本网删除。
-
标签: 超高速激光熔覆, Stellite 6涂层, 显微结构, 汽蚀, 冲蚀
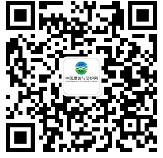
官方微信
《腐蚀与防护网电子期刊》征订启事
- 投稿联系:编辑部
- 电话:010-62316606-806
- 邮箱:fsfhzy666@163.com
- 腐蚀与防护网官方QQ群:140808414