摘 要:高温金属防护涂层在先进航空发动机上有着广泛应用,其通过生成表面保护性氧化膜为发动机热端部件提供保护,以提高热端部件的抗高温氧化腐蚀能力,延长热端部件的服役寿命。微量活性元素由于能降低涂层材料的高温氧化速率,提高涂层表面氧化膜的粘附性而被广泛用于高温防护涂层的改性上,特别是用于超高温(≥1200 ℃)金属涂层潜在应用材料NiAl 的改性上。但是截至目前,由于活性元素效应的影响因素复杂,相关作用模型并不完善,人们对活性元素效应的微观作用机理还存在较大的争论。从活性元素促进元素的选择性氧化、降低氧化膜生长速率和提高氧化膜粘附性等角度出发,综述了活性元素改性在高温金属防护涂层领域的研究进展,特别是针对以氧化铝形成合金为代表的金属防护涂层材料。重点分析了活性元素改性对氧化膜微观结构、生长机制、界面孔洞、内应力等的影响以及活性元素与杂质元素(如C 和S)之间的交互作用。最后,对今后的研究工作进行了展望,希望在原子尺度进行更深入、更细致的研究,为超高温金属防护涂层的发展提供理论指导。
关键词:高温金属防护涂层;氧化铝形成合金;高温氧化;活性元素效应;作用机理
提高关键热端部件用镍基高温合金的承温能力对于发展高推重比先进航空发动机至关重要。然而,目前研制的高温合金已接近其承温极限,仅仅通过合金设计难以满足高温及恶劣环境下的应用需求,因此表面涂覆高温防护涂层十分必要。高温防护涂层技术作为先进航空发动机的关键技术之一,可进一步降低发动机热端部件的表面温度,对提高发动机热端部件的抗高温氧化腐蚀性能,延长热端部件服役寿命发挥着重要作用。目前,高温防护涂层,尤其是高温金属防护涂层,已经在航空航天、石油化工、船舶、能源等领域得到了广泛应用[1-2]。
众所周知,涂层表面生成保护性氧化膜是金属防护涂层为基体提供保护性的关键,其中,α-Al2O3 是比较典型的保护性氧化膜,它可以在1000 ℃以上起到良好的保护作用。通常将高温下表面能够形成完整、致密Al2O3 的合金称为氧化铝形成合金,如NiCrAl、FeCrAl、CoCrAl 等,它们是高温金属防护涂层的常用材料。为了提高这些合金表面氧化膜的抗剥落性能,通常在氧化铝形成合金中添加Y、Hf 等活性元素,形成如NiCrAlY、FeCrAlY、CoCrAlY 等合金。另外,随着高性能航空发动机的发展,热端部件工作温度不断提高,对涂层高温防护性能也提出了更高的要求。对金属涂层而言,迫切需要发展超高温、长寿命、抗氧化的涂层材料。而NiAl 金属间化合物被认为是极具前景的超高温金属涂层材料,但是其循环氧化寿命不高,氧化膜容易剥落[3-9]。研究发现,活性元素改性可以显著改善合金及涂层的抗高温氧化腐蚀性能,降低氧化膜生长速率,提高氧化膜的粘附性[10-16],因此引起了人们极大的关注。近年来,研究人员针对活性元素改性进行了大量的研究。虽然取得了显著成果,但活性元素的微观作用机理还存在较大的争议,相关基础研究还有待进一步突破。因此本文以具有代表性的高温金属防护涂层材料——氧化铝形成合金(如NiAl)为例,综述了国内外活性元素改性在高温金属防护涂层领域的研究进展,重点介绍了活性元素效应及其作用机理的最新成果,希望对后续的研究起到借鉴和指导作用。
1 活性元素效应
活性元素(Reactive element, RE)是指氧亲和元素,包括所有的稀土元素(Sc、Y 和La 系元素)以及Hf、Zr、Ti 等。活性元素在高温氧化方面的作用最早由Pfeil[17]发现,之后人们针对这一现象进行了大量研究。Whittle 和Stringer[18]总结已有的研究成果,于1980 年首次提出“活性元素效应”这一概念,并将活性元素效应总结为以下几点(最初主要针对氧化铬形成合金,后来发现同样适用于氧化铝形成合金): 1)促进氧化膜形成元素的选择性氧化;2)改变氧化膜生长机制;3)抑制氧化膜/合金界面孔洞的形成;4)降低氧化膜生长速率,提高氧化膜的粘附性。其中,1)、2)、3)涉及的效应归根结底表现在对氧化膜生长速率和粘附性的影响上,因此,此后有关活性元素作用机理的研究主要集中在阐明活性元素如何降低氧化膜生长速率和提高氧化膜的粘附性上。
针对活性元素的作用机理,研究者已经提出了多种作用模型,包括氧化物“钉扎”模型[19-20]、“硫效应”模型[21-22]和动力学偏聚模型[23]等。随后,各种先进的分析表征技术的发展应用(如二次离子质谱(SIMS)、场发射扫描透射电子显微镜(FEG-STEM)等)为这些模型提供了实验数据上的支撑,促进了人们对活性元素效应的理解。然而,随着研究范围的进一步扩大,人们发现,活性元素的作用效果复杂多变,受到活性元素种类、添加量、添加方式、服役温度、基体相组成等诸多因素的影响,已经建立的模型都存在一定的局限性,通常只能在特定环境下解释某种活性元素的作用效果。比如动力学偏聚模型,一般用于解释氧化铝体系中活性元素对氧化膜生长速率的影响,而对氧化铬体系中的活性元素效应难以给出合理的解释。由此可见,活性元素对合金高温氧化行为的影响十分复杂,明确活性元素的微观作用机制、建立统一的活性元素作用模型仍然是当前研究的热点。
2 活性元素对选择性氧化的影响
大量研究结果表明,氧化铝形成合金中添加活性元素(及其氧化物),可以促进氧化膜形成元素Al的选择性氧化[24-25],这样一方面降低了形成保护性氧化膜所需的临界Al 含量,另一方面促进了保护性氧化膜的快速形成,减少了合金基体中的内氧化物形成。然而,近年来的研究发现,不同于活性元素的其他效应,选择性氧化效应的前提是要合金晶粒发生细化。Pint 等[26]在改性Fe-Al 合金的研究中发现,合金晶粒尺寸不变,即使添加活性元素也不会促进Al 的选择性氧化,而通过掺杂使得合金晶粒发生明显细化时,形成保护性氧化膜所需的临界Al 含量也随之显著降低。此外,一些表面改性技术(如添加活性元素氧化物、活性元素离子注入等)没有显著改善合金的显微结构,因而也不会促进Al 的选择性氧化[24]。由此可见,活性元素促进选择性氧化与合金晶粒尺寸的细化有关,而非添加活性元素产生的化学效应。关于活性元素与氧化膜晶粒尺寸之间的关系,早期研究认为,高温下活性元素氧化物的形成提供了成膜元素氧化的形核位点,促进了细晶氧化膜的形成[27]。但是,不仅是活性元素,其他第二相颗粒或表面缺陷活性元素离子在氧化膜晶界偏聚是影响氧化膜内元素传输机制,进而影响氧化膜生长机制及降低氧化膜生长速率的关键。Pint 等[10,23]针对活性元素改性FeCrAl 和NiAl 等合金的氧化过程进行了大量的研究,在已有研究成果的基础上提出了“动力学偏聚”理论。该理论认为,氧化过程中活性元素离子在氧化膜内并非静态,而是倾向于在氧化学势梯度的作用下,向氧化膜/合金界面以及氧化膜晶界偏聚,并沿氧化膜晶界向外扩散。因此氧化一定时间后,活性元素氧化物将在氧化膜表面形核、长大(如图2)[23],这一结果已被实验证实[38-40]。由于活性元素离子与金属阳离子有相同的扩散路径,且离子尺寸更大、扩散更慢,也会产生类似的“形核效应”。在随后的氧化过程中,这种细晶结构就主要依赖于活性元素所产生的“溶质拖曳”效应。该效应认为,添加了活性元素(包括活性元素氧化物)的合金,氧化过程中活性元素离子会在氧化膜晶界偏聚,可以钉扎晶界,阻碍晶界迁移,从而抑制晶粒长大,细化晶粒,同时产生更多的亚晶界,为Al 提供更多短路扩散的通道[10,28-29],促进保护性氧化膜的快速形成。
3 活性元素对氧化膜微观结构及生长速率的影响
1984 年,Ramanarayanan 等[30]利用带X 射线能谱的透射电子显微镜(TEM-EDXA)观察到活性元素在氧化膜晶界偏聚,之后人们针对这一现象进行了大量研究。国内外研究者利用高分辨扫描透射电子显微镜(HR-STEM)、二次离子质谱(SIMS)、电子能量损失谱(EELS)等先进的表征技术手段,在多种合金体系中均检测到活性元素在氧化膜晶界以及氧化膜/合金界面的偏聚[31-36](如图1),并证明了活性元素只能以离子形式偏聚于氧化膜晶界,而非第二相颗粒[37]。
图1 Hf 改性NiAl 合金(1100 ℃氧化100 h)后的氧化膜截面TEM 图[36]
图2 动力学偏聚理论示意图[23]
因而可以有效抑制金属阳离子的外扩散。与此相反,O 的吸附位点及扩散路径与之完全不同,因此活性元素对O 的内扩散影响不大[41]。在活性元素的作用下,Al2O3 膜的生长机制由Al 向外和O 向内扩散同时进行转变为以O 向内扩散为主,这导致氧化膜微观结构从等轴晶向柱状晶的转变[15,42](如图3 所示)以及氧化膜生长速率的降低[43-44]。
氧化膜微观结构的改变与氧化膜生长机制密切相关。未改性合金Al2O3 膜的生长以O 向内和Al 向外双向扩散为主,新的氧化物在氧化膜晶界形核,除向外生长成为脊外,同时横向生长,最终形成等轴晶。而活性元素改性合金,表面氧化膜转变为外层等轴晶加内层柱状晶的双层结构。这是由于活性元素离子晶界偏聚直接抑制了Al 离子的外扩散,使氧化膜生长以O 离子向内扩散为主,其横向生长受到抑制,形成柱状晶。
图3 活性元素改性β-NiAl 合金(1200 ℃循环氧化100 h)后的氧化膜断口形貌[15]
除氧化膜微观结构外,活性元素改性对氧化膜生长速率也有显著影响。相比于其他掺杂元素(如Y、Zr 等),NiAl、FeAl 等合金中掺杂Hf,可以更为显著地降低Al2O3 膜生长速率,抛物线速率常数降低可达10 倍左右[12,45]。研究发现,氧化膜生长速率与掺杂活性元素的外扩散行为密切相关。一般认为,离子半径较小的活性元素(如Ti 等),在氧化膜晶界扩散较快,对Al 离子的阻挡效应较弱[46];而离子半径较大的活性元素(如Hf、Zr、Y 等),由于沿氧化膜晶界扩散较慢,可以更有效地阻碍Al 离子的外扩散过程,降低氧化膜生长速率[11-12],但也有反常现象。郭洪波等[15]对比了几种活性元素改性NiAl 的高温循环氧化行为,如图4 所示,掺杂离子半径最大的La 反而加速了合金氧化,氧化膜生长速率甚至高于未改性NiAl 合金,而离子半径较小的Hf、Zr,其改性的合金氧化增重却比半径较大的Dy、Y 改性的合金氧化增重要小。由此可见,氧化膜生长速率与活性元素离子半径之间的关系不能简单地用动力学偏聚理论解释,活性元素离子对Al 离子的阻碍作用除简单的物理阻挡作用外,必然存在某种化学交互作用。因此,Pint 等[47]提出“有效离子半径”的概念,将活性元素离子对Al 离子电子结构、扩散激活能等可能的影响考虑在内,用以描述“阻挡效应”的强度。利用这一概念可以很好地解释不同活性元素对NiAl 合金氧化膜生长速率影响程度的不同。但是截至目前,活性元素离子对Al 离子的化学阻挡效应还没有明确的解释。
图4 活性元素改性β-NiAl 合金1200 ℃循环氧化
4 活性元素对氧化膜粘附性的影响
针对活性元素效应,另外一个被广泛关注的问题就是对氧化膜粘附性的改善。目前的研究认为,高温氧化过程中,活性元素改善Al2O3 膜粘附性的机制主要有以下几个方面[48-50]:1)抑制氧化膜/合金界面孔洞的形核与长大;2)在氧化膜/合金界面形成氧化物栓,提高氧化膜与合金接触面积;3)缓解氧化膜褶皱;4)直接参与氧化膜/合金界面成键,提高界面键合能力。其中,1)是研究者认识较深入的一种活性元素作用机制,2)、3)的作用机制尚存在较大争议。下面针对这4 种活性元素对氧化膜粘附性的改善机制进行详细介绍。
氧化膜/合金界面孔洞的形成降低了氧化膜与合金基体的有效接触面积,导致氧化膜极易剥落。研究人员针对界面孔洞的形成机理进行了比较系统的研究[51-53],目前提出的比较有代表性的模型,如空位沉积模型,认为高温氧化过程中,由于氧化和元素扩散,氧化膜/合金界面产生大量的阳离子空位(柯肯达尔空位),这些空位不断地在界面沉积长大,最终形成较大的孔洞。在氧化铝形成合金中,活性元素改性可以有效抑制界面孔洞的形成,提高氧化膜的粘附性,相关结果在Whittle 和Stringer 的综述以及其他人的研究中都有提及[18,54-55]。关于活性元素的作用机理,空位沉积模型认为合金中活性元素形成的氧化物可以作为空位沉积源,减少界面处空位的聚集和孔洞的形成,从而提高氧化膜的结合强度。另外也有研究指出,活性元素离子在界面的偏聚抑制了阳离子的外扩散,通过改变合金基体中元素的扩散速率,弱化了柯肯达尔效应,从而抑制了空位沉积所导致的界面孔洞的形核[52]。除空位沉积模型外,越来越多的研究表明,杂质元素(如S 等)对氧化膜的粘附性有显著的负作用,而空位沉积模型无法解释这种杂质元素对氧化膜粘附性的作用。俄歇电子能谱(AES)表明[56],S 倾向于偏聚在氧化膜/合金界面,包括结合紧密的界面以及界面处孔洞表面。这种杂质元素的界面偏聚削弱了界面强度,促进了界面孔洞的生长,最终导致氧化膜的快速剥落[22]。Hou、Pint 和Jiang 等[52-53,57-58]通过大量研究证明了这一结果,他们结合第一性原理计算,发现S 的存在确实会削弱氧化膜/合金界面的结合强度,并通过降低界面孔洞的形核能,促进孔洞的生长。添加活性元素后,界面S 等杂质元素的偏聚可以得到显著改善,界面孔洞随之大大减少。Lees 等[59]据此提出了活性元素的“硫效应”模型。该模型认为,活性元素能够与S 形成稳定的硫化物,并将S 钉扎在合金内部,避免了S 在界面的偏聚和由此产生的有害作用。但是也有研究指出,RE-S 化合物的存在并非是改善氧化膜粘附性的必要条件,经氧化物弥散强化(ODS)的FeCrAl 合金中并未发现S 被活性元素捕获的现象,但表面氧化膜同样表现出良好的粘附性[23]。因此,研究者提出,除活性元素对S 的钉扎作用外,活性元素离子向氧化膜/合金界面的偏聚,会占据S的偏聚位置,减小S 向界面偏聚的驱动力,从而改善杂质元素S 的界面偏聚情况[41,57],抑制界面孔洞的形成,提高氧化膜粘附性。然而,近来的研究表明,即使合金中不含S 等杂质,氧化膜仍然容易剥落[60],这表明S 的偏聚并不一定是引起氧化膜剥落的直接原因。因此,有关硫效应的研究还有待进一步深入。除界面孔洞因素外,界面氧化物栓的形成也是影响氧化膜粘附性的重要因素。早在20 世纪70 年代,英国利物浦大学的Allam 等[19,20,61]发现在氧化铝形成合金中添加活性元素,高温氧化时这些活性元素会在氧化膜/合金界面处形成氧化物栓,并深入合金基体中,对氧化膜起到“钉扎”作用,从而显著提高氧化膜抗剥落的能力,据此提出了氧化物“钉扎”模型。该模型认为在氧化初期,由于活性元素本身与氧亲和力大,合金中析出的活性元素也会快速参与氧化形成富活性元素的复合氧化物,这些氧化物是O 的快速扩散通道。随着氧化的进行,复合氧化物快速深入合金中,当活性元素析出物消耗殆尽时,沿着复合氧化物扩散进入的O 会与周围合金发生反应,生成Al2O3,最终形成以活性元素氧化物为“核”。Al2O3 为“壳”的氧化物栓,对氧化膜/合金界面进行钉扎,提高氧化膜粘附性。但是氧化物“钉扎”模型目前仍存在较大争议,因为有研究发现,经氧化物弥散强化(ODS)的氧化铝形成合金氧化时,虽然没有形成氧化物栓,却同样表现出优异的抗氧化性[62],表明氧化物“钉扎”效应并非是改善氧化膜粘附性的必要条件。而且研究认为,“钉扎”的有效性取决于氧化物栓的大小和分布,粗大的氧化物栓反而会引起应力集中,成为裂纹源,加速氧化膜的剥落[12]。因此,研究如何有效控制氧化物栓的形成,保证合适的形貌和密度,以利于提高氧化膜抗剥落性能将是一个重要方向。
除以上作用外,活性元素改性还可以缓解氧化膜的褶皱,从而提高氧化膜的粘附性。氧化膜褶皱的产生一般是由氧化膜内累积的残余应力导致,包括氧化膜/合金界面的热不匹配应力、氧化膜生长应力以及相变应力等[63-64]。褶皱一旦产生,很容易造成氧化膜内裂纹的萌生和扩展以及氧化膜/合金界面的分离。一些数值模拟研究认为,提高粘结层的屈服强度可以有效减小氧化膜的屈曲变形,延长热障涂层体系的服役寿命[65-66]。然而,粘结层屈服强度或者说抗蠕变性能的提高往往是以牺牲抗氧化性能为代价,使粘结层难以满足高温应用的需求。而活性元素改性可以很好地解决这一问题。郭洪波等[15,67]针对活性元素改性NiAl 合金进行了系统的研究,发现活性元素改性可以有效缓解氧化膜褶皱情况(如图5 所示),同时保证合金的抗高温循环氧化性能。他们认为活性元素改性可以降低氧化膜的生长速率,延缓θ-Al2O3 向α-Al2O3 的相转变,从而缓解氧化膜内应力的累积,抑制氧化膜褶皱的产生[68]。另一方面,活性元素易氧化形成氧化物,并弥散分布在氧化膜内,细化晶粒,可以有效改善氧化膜的力学性能,也有利于缓解氧化膜褶皱的产生[44]。此外,有研究认为,提高活性元素与杂质元素C 的比例可以改善氧化膜的褶皱情况。这是由于界面杂质元素C 的偏聚会加剧氧化膜褶皱,加入活性元素形成稳定碳化物,可以将C 固定在合金内部,从而缓解氧化膜褶皱,提高氧化膜的抗剥落性能[69]。目前,研究者对引起氧化膜褶皱的残余应力产生原因认识不统一,无法确定热不匹配应力、氧化膜生长应力、相变应力等各自所占的残余应力比重,而且对杂质元素C 影响氧化膜褶皱的作用机理尚不明确,因此活性元素在改善氧化膜褶皱方面的作用也有待深入。
图5 活性元素改性β-NiAl 合金1200 ℃循环氧化15 h 后的氧化膜褶皱曲线[15]
随着计算模拟方法在活性元素改性研究上的应用,近些年来,研究者认为活性元素在氧化膜/合金界面偏聚的同时,也会直接参与界面的成键,从而提高界面键合能力。例如,郭洪波等[70-71]采用第一性原理计算,发现活性元素Dy 在Al2O3/NiAl 合金界面直接参与了成键,每个Dy 形成了1 个Dy─Ni 金属键和4 个Dy—O 离子键(如图6 所示),相比未改性的Al2O3/NiAl 界面,成键数量和键强均明显增加,因此界面键合得到强化,氧化膜粘附性得到改善。当然,这一点还需要有效的实验证据证明。
5 结语
新一代高推重比航空发动机对发展超高温、长寿命金属防护涂层提出了迫切要求,开发1200 ℃以上、长时间抗高温氧化的金属防护涂层材料成为当前亟须解决的关键问题。微量活性元素改性对于促进保护性氧化膜形成元素的选择性氧化、降低氧化膜生长速率、提高氧化膜粘附性具有显著的效果,引起了国内外学者的广泛关注。研究人员在大量实验的基础上,针对活性元素的作用机理提出了多种模型,但这些模型均存在一定的局限性,目前对于活性元素的作用机理还存在很大的争议。
因此,为了更好地理解活性元素效应并加以应用,必须从原子尺度上进行更深入的研究。比如:阐明活性元素与合金基体元素、微观缺陷等的交互作用机制;结合高分辨电镜、第一性原理计算等,揭示活性元素对氧化膜形核生长、氧化膜/合金界面微观结构的影响机理等。通过研究,需要建立统一、普遍适用的活性元素作用模型以及活性元素选择依据,为发展超高温金属防护涂层提供关键理论支撑。
参考文献:
[1]王心悦, 辛丽, 韦华, 等. 高温防护涂层研究进展[J]. 腐蚀科学与防护技术, 2013, 25(3): 175-183.
WANG Xin-yue, XIN Li, WEI Hua, et al. Progress of high-temperature protective coatings[J]. Corrosion scie-nce and protection technology, 2013, 25(3): 175-183.
[2]郭洪波, 宫声凯, 徐惠彬. 先进航空发动机热障涂层技术研究进展[J]. 中国材料进展, 2009, 28(9): 18-26.
GUO Hong-bo, GONG Sheng-kai, XU Hui-bin. Progress in thermal barrier coatings for advanced aeroengines[J]. Materials China, 2009, 28(9): 18-26.
[3]MIRACLE D B. The physical and mechanical properties of NiAl[J]. Acta metallurgica et materialia, 1993, 41(3): 649-684.
[4]SIVAKUMAR R, MORDIKE B L. High temperature coatings for gas turbine blades: A review[J]. Surface and coatings technology, 1989, 37(2): 139-160.
[5]HAYNES J A, PINT B A, ZHANG Y, et al. Comparison of the cyclic oxidation behavior of β-NiAl, β-NiPtAl and γ-γ′ NiPtAl coatings on various superalloys[J]. Surface and coatings technology, 2007, 202(4): 730-734.
[6]HAMADI S, BACOS M P, POULAIN M, et al. Oxidation of a Zr-doped NiAl bondcoat thermochemically deposited on a nickel-based superalloy[J]. High temperature technology, 2009, 26(2): 195-198.
[7]XIE L, DORFMAN M R, CIPITRIA A, et al. Properties and performance of high-purity thermal barrier coatings [J]. Journal of thermal spray technology, 2007, 16(5/6): 804-808.
[8]PADTURE N P, GELL M, JORDAN E H. Thermal barrier coatings for gas-turbine engine applications[J]. Science, 2002, 296(5566): 280-284.
[9]NAUMENKO D, PILLAI R, CHYRKIN A, et al. Over-view on recent developments of bondcoats for plasma- sprayed thermal barrier coatings[J]. Journal of thermal spray technology, 2017, 26(8): 1743-1757.
[10]PINT B, GARRATT-REED A, HOBBS L. The reactive element effect in commercial ODS FeCrAI alloys[J]. Materials at high temperatures, 1995, 13(1): 3-16.
[11]PINT B A. Optimization of reactive-element additions to improve oxidation performance of alumina-forming alloys[J]. Journal of the American Ceramic Society, 2003, 86(4): 686-695.
[12]PINT B A. Progress in understanding the reactive element effect since the Whittle and Stringer literature review [C]// Proc John Stringer Symposium on High Temperature Corrosion. USA: ASM International Materials Park, Ohio, 2003: 9-19.
[13]HOU P Y. The reactive element effect-past, present and future[C]//Materials science forum. Switzerland: Trans Tech Publications, 2011: 39-44.
[14]SONG P, NAUMENKO D, VASSEN R, et al. Effect of oxygen content in NiCoCrAlY bondcoat on the lifetimes of EB-PVD and APS thermal barrier coatings[J]. Surface and coatings technology, 2013, 221: 207-213.
[15]LI D Q, GUO H B, WANG D, et al. Cyclic oxidation of β-NiAl with various reactive element dopants at 1200 ℃[J]. Corrosion science, 2013, 66: 125-135.
[16]PINT B A, HAYNES J A, BESMANN T M. Effect of Hf and Y alloy additions on aluminide coating performance [J]. Surface and coatings technology, 2010, 204(20): 3287-3293.
[17]PFEIL L B. Improvement in heat-resisting alloys: UK, 459848[P]. 1937-01-11.
[18]WHITTLE D P, STRINGER J. Improvements in high temperature oxidation resistance by additions of reactive elements or oxide dispersions[J]. Philosophical transac-tions of the Royal Society of London, 1980, 295(1413): 309-329.
[19]ALLAM I M, WHITTLE D P, STRINGER J. The oxi-dation behavior of CoCrAl systems containing active element additions[J]. Oxidation of metals, 1978, 12(1): 35-66.
[20]ALLAM I M, WHITTLE D P, STRINGER J. Improve-ments in oxidation resistance by dispersed oxide add-ition: Al2O3-forming alloys[J]. Oxidation of metals, 1979, 13 (4): 381-401.
21]FUNKENBUSCH A, SMEGGIL J, BORNSTEIN N. Reactive element-sulfur interaction and oxide scale adherence [J]. Metallurgical transactions A, 1985, 16(6): 1164-1166.
[22]LEES D G. On the reasons for the effects of dispersions of stable oxides and additions of reactive elements on the adhesion and growth-mechanisms of chromia and alumina scales-the "sulfur effect"[J]. Oxidation of metals, 1987, 27(1/2): 75-81.
[23]PINT B A. Experimental observations in support of the dynamic-segregation theory to explain the reactive-ele-ment effect[J]. Oxidation of metals, 1996, 45(1/2): 1-37.
[24]HOU P, STRINGER J. The effect of reactive element additions on the selective oxidation, growth and adhesion of chromia scales[J]. Materials science and engineering: A, 1995, 202(1/2): 1-10.
[25]HOU P, STRINGER J. The influence of ion-implanted yttrium on the selective oxidation of chromium in Co- 25wt.% Cr[J]. Oxidation of metals, 1988, 29(1/2): 45-73.
[26]PINT B, LEIBOWITZ J, DEVAN J. The effect of an oxide dispersion on the critical Al content in Fe-Al alloys [J]. Oxidation of metals, 1999, 51(1/2): 181-197.
[27]STRINGER J, WILCOX B A, JAFFEE R I. The high- temperature oxidation of nickel-20 wt.% chromium alloys containing dispersed oxide phases[J]. Oxidation of metals, 1972, 5(1): 11-47.
[28]GUO H B, WANG X Y, JI L I, et al. Effects of Dy on cyc-lic oxidation resistance of NiAl alloy[J]. Transactions of Nonferrous Metals Society of China, 2009, 19(5): 1185- 1189.
[29]NANNI P, STODDART C T H, HONDROS E D. Grain boundary segregation and sintering in alumina[J]. Materials chemistry, 1976, 1(4): 297-320.
[30]RAMANARAYANAN T, RAGHAVAN M, PETKOVIC-LUTON R. The characteristics of alumina scales formed on Fe-based yttria-dispersed alloys[J]. Journal of the Ele-ctrochemical Society, 1984, 131(4): 923-931.
[31]PINT B A, MORE K L. Characterization of alumina interfaces in TBC systems[J]. Journal of materials science, 2009, 44(7): 1676-1686.
[32]CHEN Y M, REED R C, MARQUIS E A. Interfacial sol-ute segregation in the thermally grown oxide of thermal barrier coating structures[J]. Oxidation of metals, 2014, 82(5/6): 457-467.
[33]SWADŹBA R, SWADŹBA L, WIEDERMANN J, et al. Characterization of alumina scales grown on a 2nd generation single crystal Ni superalloy during isothermal oxidation at 1050, 1100 and 1150 °C[J]. Oxidation of metals, 2014, 82(3/4): 195-208.
[34]UNOCIC K A, PINT B A. Oxidation behavior of co- doped NiCrAl alloys in dry and wet air[J]. Surface and coatings technology, 2013, 237: 8-15.
[35]UNOCIC K A, PINT B A. Effect of water vapor on thermally grown alumina scales on bond coatings[J]. Surface and coatings technology, 2013, 215: 30-38.
[36]PINT B A, MORE K L, WRIGHT I G, et al. Charac-terization of thermally cycled alumina scales[J]. Materials at high temperatures, 2000, 17(1): 165-171.
[37]PINT B A, GARRATT-REED A J, HOBBS L W. Possible role of the oxygen potential gradient in enhancing diffusion of foreign ions on α-Al2O3 grain boundaries[J]. Journal of the American Ceramic Society, 1998, 81(2): 305- 314.
[38]PINT B A, ALEXANDER K B. Grain boundary segre-gation of cation dopants in α-Al2O3 scales[J]. Journal of the electrochemical society, 1998, 145(6): 1819-1829.
[39]GUO H B, LI D Q, ZHENG L, et al. Effect of co-doping of two reactive elements on alumina scale growth of β- NiAl at 1200 ℃[J]. Corrosion science, 2014, 88: 197-208.
[40]LI C, SONG P, KHAN A, et al. Influence of water vapour on the HfO2 distribution within the oxide layer on CoNiCrAlHf alloys[J]. Journal of alloys and compounds, 2018, 739: 690-699.
[41]MARINO K A, CARTER E A. Atomic-scale insight and design principles for turbine engine thermal barrier coa-tings from theory[J]. Proceedings of the national aca-demy of sciences of the United States of America, 2011, 108 (14): 5480-5487.
[42]GALMARINI S, ASCHAUER U, BOWEN P, et al. Ato-mistic simulation of Y-doped α-alumina interfaces[J]. Journal of the American Ceramic Society, 2008, 91(11): 3643-3651.
[43]HE J, ZHANG Z, PENG H, et al. The role of Dy and Hf doping on oxidation behavior of two-phase (γ′+β) Ni-Al alloys[J]. Corrosion science, 2015, 98: 699-707.
[44]GUO H B, WANG D, PENG H, et al. Effect of Sm, Gd, Yb, Sc and Nd as reactive elements on oxidation beha-viour of β-NiAl at 1200 ℃[J]. Corrosion science, 2014, 78: 369-377.
[45]PINT B A. The role of chemical composition on the oxidation performance of aluminide coatings[J]. Surface and coatings technology, 2004, 188: 71-78.
[46]PINT B A, UNOCIC K A. Ionic segregation on grain boundaries in thermally grown alumina scales[J]. Materials at high temperatures, 2012, 29(3): 257-263.
[47]PINT B A, MORE K, TORTORELLI P, et al. Optimizing the imperfect oxidation performance of iron aluminides [C]//Materials science forum. Switzerland: Trans Tech Publications, 2001: 411-418.
[48]HOU P Y, PRIIMAK K. Interfacial segregation, pore formation, and scale adhesion on NiAl alloys[J]. Oxidation of metals, 2005, 63(1/2): 113-130.
[49]TOLPYGO V K, CLARKE D R. Surface rumpling of a (Ni,Pt) Al bond coat induced by cyclic oxidation[J]. Acta materialia, 2000, 48(13): 3283-3293.
[50]PINT B A, WRIGHT I G, LEE W Y, et al. Substrate and bond coat compositions: Factors affecting alumina scale adhesion[J]. Materials science and engineering: A, 1998, 245(2): 201-211.
[51]TIEN J K, PETTIT F S. Mechanism of oxide adherence on Fe-25Cr-4Al (Y or Sc) alloys[J]. Metallurgical trans-actions, 1972, 3(6): 1587-1599.
[52]PINT B A. On the formation of interfacial and internal voids in α-Al2O3 scales[J]. Oxidation of metals, 1997, 48(3): 303-328.
[53]GESMUNDO F, HOU P Y. Analysis of pore formation at oxide-alloy interfaces—II: Theoretical treatment of va-cancy condensation for immobile interfaces[J]. Oxidation of metals, 2003, 59(1/2): 63-81.
[54]NAUMENKO D, PINT B A, QUADAKKERS W J. Current thoughts on reactive element effects in alumina- forming systems: In memory of John Stringer[J]. Oxid-ation of metals, 2016, 86(1/2): 1-43.
[55]GUO H B, ZHANG T, WANG S X, et al. Effect of Dy on oxide scale adhesion of NiAl coatings at 1200 ℃[J]. Corrosion science, 2011, 53(6): 2228-2232.
[56]HOU P Y, STRINGER J. Oxide scale adhesion and impurity segregation at the scale/metal interface[J]. Oxi-dation of metals, 1992, 38(5/6): 323-345.
[57]HOU P Y. Segregation phenomena at thermally grown Al2O3/alloy interfaces[J]. Annual review of materials research, 2008, 38(38): 275-298.
[58]JIANG Y, SMITH J R, EVANS A G. First principles assessment of metal/oxide interface adhesion[J]. Applied physics letters, 2008, 92(14): 245414.
[59]HOU P Y. Segregation behavior at TGO/bondcoat inter-faces[J]. Journal of materials science, 2009, 44(7): 1711- 1725.
[60]HOU P Y, IZUMI T, GLEESON B. Sulfur segregation at Al2O3/γ-Νi+γ′-Ni3Al interfaces: Effects of Pt, Cr and Hf additions[J]. Oxidation of metals, 2009, 72(1/2): 109-124.
[61]MENNICKE C, HE M Y, CLARKE D R, et al. The role of secondary oxide inclusions ("pegs") on the spalling resistance of oxide films[J]. Acta materialia, 2000, 48(11): 2941-2949.
[62]PINT B A, HOBBS L W. The oxidation behavior of Y2O3- dispersed β-NiAl[J]. Oxidation of metals, 2004, 61(3/4): 273-292.
[63]TOLPYGO V K, CLARKE D R. On the rumpling mec-hanism in nickel-aluminide coatings: Part I: An experi-mental assessment[J]. Acta materialia, 2004, 52(17): 5115- 5127.
[64]PENNEFATHER R C, BOONE D H. Mechanical deg-radation of coating systems in high-temperature cyclic oxidation[J]. Surface and coatings technology, 1995, 76: 47-52.
[65]KARLSSON A M, EVANS A G. A numerical model for the cyclic instability of thermally grown oxides in thermal barrier systems[J]. Acta materialia, 2001, 49(10): 1793- 1804.
[66]KARLSSON A M, LEVI C G, EVANS A G. A model study of displacement instabilities during cyclic oxidation [J]. Acta materialia, 2002, 50(6): 1263-1273.
[67]GUO H B, WANG X Y, GONG S K. Effects of Dy on the microstructure and spallation failure of the alumina scales grown on NiAl[J]. International journal of modern physics B, 2010, 24(15/16): 3149-3154.
[68]YANG L Y, ZHENG L, GUO H B. The residual stress of oxide scales grown on Ni-Al alloys doped with minor Dy and Y[J]. Corrosion science, 2016, 112: 542-551.
[69]PINT B A, SCHNEIBEL J H. The effect of carbon and reactive element dopants on oxidation lifetime of FeAl[J]. Scripta materialia, 2005, 52(12): 1199-1204.
[70]ZHANG Z, ZHANG R F, LEGUT D, et al. Pinning effect of reactive elements on adhesion energy and adhesive strength of incoherent Al2O3/NiAl interface[J]. Physical chemistry chemical physics, 2016, 18(33): 22864-22873.
[71]ZHANG T, GUO H B, GONG S K, et al. Effects of Dy on the adherence of Al2O3/NiAl interface: A combined first- principles and experimental studies[J]. Corrosion science, 2013, 66(1): 59-66.
免责声明:本网站所转载的文字、图片与视频资料版权归原创作者所有,如果涉及侵权,请第一时间联系本网删除。
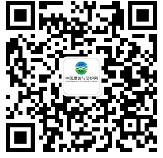
官方微信
《腐蚀与防护网电子期刊》征订启事
- 投稿联系:编辑部
- 电话:010-62316606-806
- 邮箱:fsfhzy666@163.com
- 腐蚀与防护网官方QQ群:140808414