摘要: 采用多弧离子镀技术制备了不同调制比的交替多元多层Zr/CrAlSiN复合涂层,通过交替沉积与间歇性接近不同靶材相结合的方法获得了Zr/[Al(Si)N/CrN] “层中层”结构,并对复合涂层的力学性能、无腐蚀时的摩擦磨损性能、无摩擦磨损时的腐蚀性能及海水环境中的腐蚀磨损性能进行了研究。结果表明:该结构设计对涂层生长缺陷具有明显的抑制和修复作用;随着CrAlSiN层厚度比例增大,调制比为1∶6时Zr/[Al(Si)N/CrN]涂层的综合力学性能最佳;由于CrAlSiN层具有多层Al(Si)N/CrN结构,增加CrAlSiN层厚度比例增加了复合涂层横向界面,从而提升了涂层腐蚀性环境中的阻隔作用,因此CrAlSiN层厚度比例的增加既可以提升无摩擦磨损时涂层的耐腐蚀性能,又可提升涂层摩擦开动后的耐腐蚀性能,并进一步降低涂层腐蚀和磨损的相互促进作用;当调制比为1∶6和1∶8时,Zr/[Al(Si)N/CrN]涂层在海水环境中展现出了较好的抗腐蚀磨损性能。
关键词: Zr/[Al(Si)N/CrN]涂层 ; “层中层”结构 ; 海水环境 ; 腐蚀磨损特性
腐蚀与磨损耦合作用所引发的腐蚀磨损损伤远大于单一腐蚀损伤或单一磨损损伤,是国防武器系统、海洋工程装备、化工机械装置、流体传动系统等装备系统中腐蚀性环境齿轮、轴承、阀门、管件以及其它特种机械运动部件表面失效的主要形式,也是相关装备系统可靠服役所长期面临的重大挑战[1]。研究[2-4]表明,金属元素与N之间的共价键不仅可以使金属氮化物基涂层具备较高的力学性能,而且还可以赋予金属氮化物基涂层良好的化学惰性和抗氧化性,从而使得金属氮化物基涂层在腐蚀磨损工况条件下表现出优异的耐磨性与耐蚀性,特别是腐蚀与磨损的弱交互性。因此,以共价键为主要结合形式的金属氮化物基涂层已逐渐被认为是苛刻环境下抗腐蚀磨损表面防护最佳的技术途径之一。
现有的抗腐蚀磨损组成结构设计方法研究主要集中在多元设计和多层设计。对于金属氮化物基涂层的多元设计,主要是在TiN、CrN、ZrN等二元金属氮化物 (MeN) 基础上,通过引入多个元素构造多元复合涂层Me(X)N以获得更加优异的抗腐蚀磨损特性,已发展的多元设计理论有多元合金化效应[5]、多相复合协同效应[6]、高熵合金鸡尾酒效应[7]、纳米晶镶嵌非晶强化效应[8]、硬质相与软质相平衡效应[9]以及摩擦化学表面减摩耐磨效应[10]等。对于金属氮化物基涂层的多层设计,主要是在单层金属氮化物涂层Me(X)N涂层基础上,通过设计多个亚层构造多层复合涂层Me(X)N/Me(Y)N以获得更加优异的抗腐蚀磨损特性,已发展的多元设计理论有过渡层双亲和作用[11]、梯度转变层缓冲作用[12]、纳米多层晶粒细化作用[13]、横向界面腐蚀因子阻隔作用[14]、多层界面位错运动钉扎作用[15]以及软硬交替裂纹抑制作用[16]等。但是,不管是多元设计理论还是多层设计理论,大都基于理想的材料结构,忽略了金属氮化物基涂层物理气相沉积制备过程中不可避免地产生的柱状晶间隙、金属液滴、随机空洞等生长缺陷,特别是对于物理气相沉积技术中最具工业生产意义的电弧离子镀技术,其各种生长缺陷特征更加明显。这些生长缺陷在腐蚀与磨损的耦合作用下极易萌生裂纹并扩展,形成腐蚀通道,诱发涂层剥落。生长缺陷诱导腐蚀磨损加剧现象是长期制约金属氮化物基涂层实际服役过程中抗腐蚀磨损防护作用的瓶颈。虽然多元设计可采用延长沉积时间以增加涂层厚度或加大轰击能量以提高致密程度等手段来抑制各类生长缺陷,但多层设计更是可采用引入横向界面以打断柱状生长或进行交替沉积以覆盖早生缺陷等手段来修复各类生长缺陷。相对而言,在控制生长缺陷对金属氮化物基涂层抗腐蚀磨损性能不利影响方面,多层设计的缺陷修复作用比多元设计的缺陷抑制作用更有效,因此在多元设计基础上发展多层设计是近年来提高金属氮化物基涂层抗腐蚀磨损性能主要的发展方向。
为此,本文制备了具有“层中层”结构特征的多元多层Zr/[Al(Si)N/CrN]涂层,重点研究了所制备涂层在人工海水环境中的腐蚀磨损性能,为发展高性能抗腐蚀磨损金属氮化物基涂层材料提供理论基础和设计依据。
1 实验方法
选用单晶硅片和尺寸规格为30 mm×20 mm×2 mm的316L不锈钢为基底样片同炉制备涂层,单晶硅片表面涂层用于结构测试,不锈钢片表面涂层用于性能测试。选用多弧离子镀镀膜设备 (Hauzer Flexicoat 850),利用锆靶 (纯度99.9%)、铬靶 (纯度99.5%) 和质量比为Al∶Si=8∶2的铝硅靶,在基底表面通过交替沉积与间歇性接近不同靶材相结合的方法沉积制备Zr/CrAlSiN多元多层涂层。
采用交替沉积的办法构造金属亚层Zr与陶瓷亚层CrAlSiN的交替多层结构,Zr层通过一列高纯Zr靶在氩气气氛中沉积制备,陶瓷亚层CrAlSiN通过同时开启一列AlSi复合靶和一列高纯Cr靶在氮气气氛中沉积制备,采用多重旋转方式控制基体间歇性接近AlSi靶或Cr靶,构造陶瓷亚层中子层Al(Si)N和子层CrN交替多层结构,最终获得具有“层中层”结构特征的Zr/[Al(Si)N/CrN]多元多层涂层。
通过改变交替沉积时间,改变Zr与[Al(Si)N/CrN]层的调制比分别为近似1∶1、1∶2、1∶4、1∶6、1∶8。保持多重旋转方式的速度恒定,确保CrAlSiN层中Al(Si)N/CrN多层结构调制比不变。在制备涂层之前,基底样片先在丙酮中,然后在无水乙醇溶液中超声清洗,每次时间为20 min,完成后用干燥氮气吹干。所有样品装入镀膜腔室至背底真空抽至4.0×10-5 mbar后,首先用Ar+刻蚀表面以去除样品表面附着的杂质及氧化层,偏压分别设定为-900,-1100和-1200 V,每种偏压刻蚀时间为2 min。随后进入镀膜程序,真空腔体温度保持在400 ℃。第一层沉积的为纯Zr过渡层,设定Ar气流量为350 sccm,纯Zr靶电流为70 A,基底负偏压20 V,沉积时间为10 min。随后沉积 [Al(Si)N/CrN]多层结构,主要工艺参数为:氮气流量600 sccm,Cr靶电流60 A,AlSi靶电流60 A,基底负偏压40 V,样品架的旋转速度为3 r/min。两个步骤交替循环,获得Zr/[Al(Si)N/CrN]多层涂层。Zr层与[Al(Si)N/CrN]层不同调制比沉积时间参数如表1所示。
表1 不同调制比Zr/CrAlSiN多层涂层沉积时间及循环次数参数
采用Bruker D8 ADVANCE DAVINCI型X射线衍射 (XRD) 对所制备的所有涂层的物相结构进行表征,使用Cu Kα射线,波长为0.15418 nm,测试条件为40 kV,40 mA,掠入射角为2°,以4°/min的速度扫描,角度从20°到90°。利用RTEC UP-Lambda型三维轮廓仪 (3D-P) 观察表面三维形貌特征和粗糙度。所有涂层的表面结构由EVO18扫描电镜 (SEM) 表征,截面结构用S4800场发射扫描电子显微镜 (FESEM) 表征。涂层的微观结构进一步用Tecnai F20高分辨率透射电子显微镜 (HRTEM) 表征,结合选区电子衍射 (SAED) 获得涂层结构信息。
涂层的显微硬度 (H) 和弹性模量 (E) 由纳米压痕测试仪 (MTS Nano Indenter G200) 测试,压入深度设定为涂层厚度的10%,每个样品选择6个不同区域压入,获得压入深度-力卸载曲线,通过处理得到涂层的硬度和弹性模量。涂层与基底的结合强度由划痕测试系统评估 (CSM Revetest),该仪器压头为带有半径为0.2 mm尖端的锥形金刚石,锥角为120°,划痕长度为3 mm,力的加载时长为60 s,光学显微镜与SEM观察相结合表征划痕形貌特征。采用往复式摩擦磨损试验机测试涂层在大气环境中的摩擦学性能,摩擦对偶球选用的是6 mm的YG6球,载荷为1 N,频率为2 Hz,振幅为5 mm,时间为30 min。摩擦实验结束后,通过观察磨痕轮廓,并利用K=V/FS等式计算涂层的磨损率,其中V为磨痕体积,F为载荷,S为滑动总距离。采用CHI-660E电化学工作站,三电极系统测试涂层在海水环境中无摩擦运动时的电化学腐蚀行为,对电极为铂丝电极,参比电极为饱和甘汞电极,工作电极为沉积有涂层的316L不锈钢基底样片,暴露面积为1 cm2,海水环境为采用ASTM D1141-98标准配置的人工海水,极化曲线测试的扫描速率为0.1 V/s,电化学阻抗谱测试的频率范围为在至105~10-2 Hz,测试前样品提前在人工海水中浸泡15~20 min,根据电化学阻抗谱测试结果通过ZSimpWin软件分析拟合得到等效模拟电路模型。
利用腐蚀磨损试验装置测试涂层在海水环境中的腐蚀磨损耦合作用,包括在摩擦条件下的电化学行为以及在腐蚀作用下的摩擦磨损性能。测试采用三电极体系,对电极为铂丝电极,参比电极为饱和甘汞电极,工作电极为沉积有涂层的316L不锈钢基底样片,采用按照ASTM D1141-98标准配置的人工海水模拟海水环境。摩擦试验的参数为:载荷5 N,频率2 Hz,振幅5 mm,直径6 mm的YG6球为摩擦对偶。实验前,涂层样品提前在人工海水中浸泡15~20 min。在涂层的极化曲线测试中,首先进行10 min开路电位测试以达到稳定状态,再开动摩擦试验机持续30 min并记录极化曲线。在腐蚀磨损耦合测试中,同样提前10 min不开动摩擦试验机稳定涂层,后在摩擦条件下持续60 min并记录开路电位和摩擦系数,摩擦停止后继续记录10 min开路电位,观察涂层在摩擦开动前、中、后开路电位的演变情况。在腐蚀磨损耦合结束后观察实验所得磨损轨道的微观形貌及磨痕轮廓,并计算涂层的磨损率K。
2 结果与讨论
2.1 涂层结构
图1为不同调制比交替多层Zr/CrAlSiN涂层截面形貌和表面形貌。从截面形貌中可以看出所制备的涂层具有清晰明显的多层结构,打断了涂层柱状生长特征,并且多层结构致密且均匀。通过控制总沉积时间获得具有可比性的厚度相似涂层,经测量可得调制比为1∶1、1∶2、1∶4、1∶6、1∶8的交替多层Zr/CrAlSiN涂层厚度分别为5.2、5.3、5.0、5.4和4.9 μm。从表面形貌可以看出,不同调制比的涂层都有多弧离子镀涂层的生长特点,即在涂层的生长结构中普遍存在液滴和孔洞等缺陷,事实上截面形貌中局部也可以看出液滴和孔洞特征。进一步对比发现,尽管调制比为1∶4、1∶6和1∶8的涂层表面局部仍然分布有较大颗粒特征,但总体上颗粒特征与调制周期为1∶1和1∶2涂层相比明显减少。以上形貌特点主要是因为靶材在沉积过程中受热产生的液滴,部分液滴在高能离子轰击时脱落则又会产生孔洞,而沉积过程中快速加热冷却也会导致局部收缩从而形成孔洞。增加CrAlSiN层厚度比例,涂层缺陷数量和尺寸均有所减少,涂层生长缺陷的随厚度增加而逐步放大现象得以有所抑制。进一步放大调制比为1∶1的涂层截面结构,如图2所示,可以清晰看出来所制备的Zr/CrAlSiN为典型“层中层”结构,CrAlSiN涂层内部仍然为多层结构,这种“层中层”结构不仅能够通过打断柱状生长而抑制纵向间隙,更是能够对涂层中的液滴和孔洞等生长缺陷起到良好修复作用。从三维轮廓扫描获得调制比为1∶1、1∶2、1∶4、1∶6、1∶8涂层粗糙度Ra分别是0.241、0.202、0.078、0.139和0.072 μm,可见从调制比为1∶4的涂层开始涂层表面粗糙度有明显减小,并且调制比为1∶4和1∶8的涂层粗糙度小于0.1 μm。由于SEM形貌显示调制比为1∶4、1∶6和1∶8涂层表面形貌并没有特别明显的区别,因此调制比1∶6时的粗糙度超过0.1有可能是由于涂层制备过程中靶材受热产生液滴的随机性所致,或是由于相对调制周期1∶4和1∶8的涂层更厚而对生长缺陷放大作用较强所致。总体上,这种结构以及粗糙度变化情况说明改变多层涂层调制比可以调控涂层质量,增加CrAlSiN层厚度比例可以有效抑制涂层缺陷长大,并可对涂层生长缺陷起到效果更加显著的修复作用。
图1 不同调制比多层Zr/CrAlSiN涂层的截面形貌和表面形貌
图2 多层涂层中生长缺陷的修复
图3为不同调制比多层Zr/CrAlSiN涂层的XRD图。可以看出涂层中有明显的Zr、AlN和CrN的衍射峰,均为多晶结构。进一步确定涂层中的物相结构,分别为:六方结构Zr的 面,六方结构AlN的
面以及立方结构CrN的 (002)、(022)、(222) 面。对比不同调制比XRD图发现,调制比并未改变复合涂层物相结构。调制比1∶1条件下CrN(222) 面信号较弱,可能与此事金属Zr层相对较厚有关。随着CrAlSiN层厚度比例增加:Zr (
) 等物相峰有轻微宽化,预示着金属Zr层晶粒尺寸的减小;同时CrN(222) 信号逐渐增强,这种现象则与CrN含量增加有关。为了进一步剖析涂层的微观结构和物相信息,对调制比为1∶1的交替多层Zr/CrAlSiN涂层进行了HRTEM分析,如图4所示。图4a中较暗的部分为Zr层,有分层且亮度高一些的部分为CrAlSiN层,涂层呈现明显的“层中层”结构特征。图4b为HAADF图像以及不同位置的元素分布情况,可以观察到涂层的“层中层”结构。对比元素分布结果,证实CrAlSiN层中为CrN/AlSiN交替多层。图4c为CrAlSiN层的高分辨图像和选区电子衍射图像,除了XRD表明的物相结构外,证实涂层中还存在:Zr的 (
面,XRD并未检测出明显此类信号峰说明相关结构含量较少。此外,从高分辨图像中可以看出,不同层间物相结构位向关系清晰,层间界面结合良好。无论是XRD分析还是HRTEM分析,均未见含Si的物相结构,考虑到采用AlSi靶进行电弧离子镀沉积将毫无疑问地在涂层中引入Si,并且从元素分析上也已经证实Si出现在了AlN层位置,因此推测Si将有可能以固溶态存在于AlN结构中,本文所制备的Zr/CrAlSiN涂层应为Zr层与CrAlSiN层交替的“层中层”Zr/[Al(Si)N/CrN]结构。
图3 不同调制比多层Zr/CrAlSiN涂层的XRD图谱
图4 调制比为1:1多层Zr/CrAlSiN涂层的HRTEM图
2.2 涂层力学性能
图5为不同调制比多层Zr/CrAlSiN涂层的硬度和弹性模量随深度变化曲线。可以看出,涂层的硬度曲线和弹性模量随深度变化趋势相同。压入测试开始时,涂层硬度和弹性模量受到涂层表面杂质或者氧化层的影响均偏大,在压入深度增大到涂层总厚度的1/8~1/10之后渐渐下降达到一个较为稳定的数值。对于硬质涂层力学性能测试,为尽量降低基底对测试结构的影响,通常取厚度1/8~1/10处数值作为代表。为此,在本论文研究过程中亦取该阶段数值进行统计以代表不同涂层可比较的硬度和弹性模量,如表2所示。由表可知,随着涂层调制比的增大,涂层硬度增大,在调制比为1∶6时达到最大,随后又减小。调制比为1∶4 (21.72 GPa) 和1∶6 (23.01 GPa) 涂层的硬度较大。Verma等[17]研究认为,多层涂层中高弹性模量的材料厚度增加,低弹性模量的材料厚度降低会使涂层的硬度增高,金属氮化物层的弹性模量远大于金属层,因此随着调制比的增大,涂层的硬度逐渐增大。但是调制比为1∶8的涂层硬度小于调制比为1∶6和1∶4的涂层,很有可能是因为多层涂层的硬度提升还与层与层之间的界面的共格、外延生长提高了界面的结合强度,阻止了位错的滑移有很大关系[18]。调制比为1∶8的涂层很有可能因为CrAlSiN层调制比较大,使得Zr层厚度相较于CrAlSiN层厚度较小,界面之间的结合力较弱,因此涂层的硬度和弹性模量减小。关于不同调制比交替多层Zr/CrAlSiN涂层的硬弹比:H/E的数值随着调制比的增大而增大,调制比为1∶4和1∶6时最大,H/E的数值都为0.063,且调制比为1∶2 (0.059) 和1∶8 (0.058) 的涂层该值较为接近;对于H3/E2的值,调制比为1∶1的涂层该数值明显小于其他涂层,调制比为1∶6的涂层的值最大。
图5 多层Zr/CrAlSiN涂层硬度和弹性模量
表2 不同调制比多层Zr/CrAlSiN涂层硬度、弹性模量和硬弹比
图6为不同调制比多层Zr/CrAlSiN涂层划痕测试声发射 (AE) 信号变化情况。可以看出,涂层声信号起始波动点按照1∶1、1∶2、1∶4、1∶6、1∶8顺序依次先提前,后延后,再提前。这意味着随CrAlSiN厚度间增加涂层随划痕加载力增加易开裂倾向逐渐先提前,后延后,再提前。从声信号上判断调制比1∶6涂层结合力最好。图7为不同调制比多层Zr/CrAlSiN涂层的划痕形貌,结合光学显微镜宏观形貌以及不同阶段划痕SEM形貌。对比划痕加载末端,不同涂层呈现出了相似的表界面形貌,此时不仅光学形貌观察中出现白亮特征,SEM形貌观察中亦出现大量金属粘着特征,预示着涂层已经发生大面积破坏。对比划痕加载15 N前后特征,不同涂层划痕表界面呈现出了不同特征,这个阶段也是不同涂层划痕声信号差异较大的位置。对于调制比1∶1涂层,尽管声信号不明显,但此时涂层划痕内部已经出现较多裂纹,相对而言裂纹比较细密,这主要是由于涂层中的金属层比例较大,涂层机械强度较低所致。随着脆性硬质结构CrAlSiN层比例增加和韧性结构Zr层比例逐渐减小,涂层整体脆性增加,划痕内部裂纹特征逐渐变得粗大化。调制比为1∶4的涂层裂纹较少,但划痕边缘涂层有碎裂情况,还出现了明显的片状剥落情况,正是由于涂层韧性下降所致。随着涂层硬质结构CrAlSiN层继续增加,涂层机械强度得以逐步提升,承载能力增强,表现出较高抗划擦能力,如图7d所示调制比为1∶6时涂层划痕内部产生少量的细微裂纹,划痕边缘的碎裂情况也较为轻微。当调制比为1∶8时,涂层划痕边缘也有一定的碎裂情况,划痕内部有少量片状裂纹,同时划痕内也有少量磨料磨损的痕迹和磨屑。涂层划痕测试的结果与涂层硬度和弹性模量关系密切,结合力测试的优劣与硬度、弹性模量的优劣顺序一致,所有涂层中,调制比为1∶6涂层的结合力较好,说明此时涂层综合机械性能最佳。
图6 不同调制比多层Zr/CrAlSiN涂层划痕测试声发射信号
图7 不同调制比多层Zr/CrAlSiN涂层的划痕形貌
2.3 无腐蚀时的摩擦磨损性能
图8为不同调制比多层Zr/CrAlSiN涂层在没有腐蚀作用情况下,大气干摩擦工况的摩擦系数。可以看出调制比为1∶1的涂层在300 s后开始有明显波动且一直升高,调制比为1∶2涂层在500 s后摩擦系数波动减小。调制比为1∶4的涂层在摩擦系数稳定前的跑合期则很短,随后可以观察到缓慢上升的曲线。调制比为1∶6的涂层的摩擦系数曲线则一直表现为缓慢上升的趋势,但是总体曲线为所有涂层中最低的。调制比为1∶8的涂层在200 s前上升较为缓慢,但是在实验200 s后摩擦系数上升明显,并在900 s后摩擦系数开始超过调制比为1∶4的涂层。图9是不同调制比多层Zr/CrAlSiN涂层摩擦系数、磨损率和3D磨损形貌图,其中折线图为摩擦系数,柱状图为磨损率,柱状图上方插入的为涂层磨痕的3D形貌图,彩色坐标轴代表涂层的高度尺。可以看出:调制比为1∶1、1∶2、1∶4、1∶6、1∶8涂层的摩擦系数分别为0.689、0.527、0.538、0.410、0.542;调制比1∶1、1∶2、1∶4、1∶6、1∶8涂层的磨损率分别为6.20×10-4、4.18×10-4、8.75×10-5、5.55×10-5、8.53×10-5 mm3/(N·m)。1∶1和1∶2涂层摩擦和磨损较为剧烈,磨损率其他涂层大一个数量级,原因在于这两个涂层的硬度和弹性模量都较其他涂层较小,另外摩擦性能除了与摩擦过程中的磨料磨损有关,还与涂层的粗糙度有一定的关系,调制比为1∶1和1∶2的涂层粗糙度都在0.2 μm以上。调制比1∶4、1∶6、1∶8的涂层中,1∶6涂层的摩擦系数最低而且磨损率最小,但是该涂层的粗糙度大于另外两种涂层,这很有可能是因为该涂层硬弹比H3/E2的值为三种涂层中最大,呈现出较低的界面剪切粘滞作用以及较高的抵抗摩擦剪切破坏能力。对比调制比为1∶4和1∶8的涂层,较低的硬度、弹性模量、H/E值以及H3/E2值是的调制比为1∶8的涂层摩擦粘滞作用更强且更容易磨损破坏,因而呈现出了更高的摩擦系数和磨损率。从柱状图上方的磨痕3D图中也可以看出,调制比为1∶1和1∶2的涂层磨损较为严重,涂层已被磨穿,而调制比为1∶4、1∶6、和1∶8的涂层磨痕明显较浅,涂层没有被磨穿。
图8 不同调制比多层Zr/CrAlSiN涂层摩擦曲线
图9 不同调制比多层Zr/CrAlSiN涂层摩擦系数、磨损率及磨损形貌
2.4 无摩擦磨损时的腐蚀性能
图10为不同调制比多层Zr/CrAlSiN涂层在腐蚀性海水环境中的静态极化曲线,根据极化曲线得到不同涂层的电化学参数如表3所示。可以看出,不同调制比涂层样品Icorr对应1∶1、1∶2、1∶4、1∶8的顺序依次减小,在调制比为1∶6时有所升高,说明涂层在海水环境中的耐腐蚀性能总体上是随CrAlSiN层厚度比例增加而逐渐增强,调制比为1∶6时涂层的耐蚀性略低于调制比为1∶4的涂层。Ecorr的变化趋势也与Icorr趋势一致,涂层的腐蚀电位越正,代表被腐蚀的倾向越小。这主要是因为CrAlSiN层中也呈现多层结构,所以随着CrAlSiN层厚度的增加,涂层的总层数也在不断增加,对腐蚀介质有很好的阻隔作用。调制比为1∶6的涂层耐腐蚀性能相对调制比为1∶4和1∶8涂层略有下降的原因很有可能是因为此时粗糙度加大原因所致。有研究表明涂层的腐蚀速率除了收涂层内部的结构影响以外,腐蚀反应最初发生在涂层表面的缺陷中,涂层表面的缺陷越多,腐蚀速率也就越活跃[19]。
图10 不同调制比多层Zr/CrAlSiN涂层的极化曲线
表3 不同调制比多层Zr/CrAlSiN涂层的电化学数据
图11a,b为不同调制比涂层电化学阻抗谱 (EIS) 测试所得到的Nyquist和Bode图。可以看出调制比为1∶8和1∶4的涂层容抗弧半径较为接近,接下来大小次序为1∶6、1∶2、1∶1,说明调制比为1∶8和1∶4的涂层的耐腐蚀性能较好,和极化曲线结果相符合。接下来对EIS测试数据进行了电路的拟合以获得定量的数据,图11c为交替多层Zr/CrAlSiN涂层EIS测试数据所拟合的等效电路图,该电路图可表示为R(Q(R(QR))),所有拟合电路所得的参数总结在表4中。R(Q(R(QR))) 为多层涂层常用电路,物理意义清晰,电路中Rs表示人造海水的电阻,Rc,Qc,Rct,Qdl分别代表涂层电阻,涂层电容,电荷转移电阻和双层电容[20,21]。在该电路中,采用恒相位元件Q(CPE) 代替电容,即Qc,是在电路拟合中专用的非理想电容,CPE与阻抗的关系为:ZCPE=Q-1(jω)-n。其中n值为频率-阻抗的拟合参数,代表CPE较纯电容C的偏离情况;j=(-1)1/2,ω为角频率。n值始终介于0.5~1之间,该现象是由于涂层样品的不均匀性,一般认为工作电极表面粗糙度增大时,CPE更偏离理想的纯电容,电极越粗糙,n值越远离1。当n=0.5时,CPE代表Warburg阻抗,当n=0、1时CPE分别代表简单电阻器和理想电容器。并且Qc是由于涂层内部成分不均匀产生,Qdl则是与涂层表面的不均匀性有关[22,23]。从表5中可以得到不同调制比Rct值的大小顺序依次为1∶8、1∶4、1∶6、1∶2、1∶1,并且调制比为1∶8、1∶4、1∶6的Rct值与1∶2、1∶1涂层比较大了一个数量级。这说明调制比为1∶4、1∶8涂层在静态无摩擦条件下具有最好的海水环境耐蚀性能,调制比为1∶6的涂层海水环境具有较好的耐蚀性能,调制比为1∶2和1∶1的涂层海水环境耐蚀性较差。EIS的实验结果与极化曲线测试相符合,同样可以用涂层总层数增加的多界面效应以及粗糙度变化规律解释[24]。
图11 不同调制比多层Zr/CrAlSiN涂层的EIS曲线及模拟电路
表4 交替多层Zr/CrAlSiN涂层等效电路图拟合参数
表5 不同调制比多层Zr/CrAlSiN涂层摩擦条件下电化学数据
2.5 海水环境腐蚀磨损性能
为了评估不同调制比多层Zr/CrAlSiN涂层的腐蚀磨损性能,在海水环境中对涂层进行了摩擦条件下的极化曲线和开路电位曲线测试。图12为不同调制比多层Zr/CrAlSiN涂层在摩擦条件下的极化曲线,由极化曲线所得到的电化学数据总结在表5中。因为摩擦的影响,不同涂层的极化曲线在测试过程中均呈现出较为明显的波动现象。从极化曲线中所得到的不同调制比涂层的腐蚀电流密度从小到大的次序依次:1∶8、1∶6、1∶4、1∶2、1∶1。在摩擦条件下,调制比为1∶8的涂层的腐蚀速率最小,并且腐蚀电位最正,说明被腐蚀的倾向最小,表现出了最好的耐腐蚀性能。这种情况说明,在摩擦开动过程中,随着调制比的增大,涂层耐腐蚀性能增加,展现出了多层涂层总层数增加对摩擦腐蚀性能的提升效果。在静态腐蚀情况下调制比为1∶4涂层的耐腐蚀性能比1∶6涂层好,而在摩擦条件下该情况没有再出现,很有可能是因为摩擦破坏了涂层的表面,使得1∶4涂层因表面粗糙度较小的优势减弱。从摩擦条件下的极化曲线数据来看,调制比为1∶8、1∶6的涂层相对表现出较好的耐腐蚀性能。
图12 不同调制比多层Zr/CrAlSiN涂层在摩擦条件下的极化曲线
图13是不同调制比交替多层Zr/CrAlSiN涂层在海水环境中的摩擦系数曲线和开路电位曲线,涂层的摩擦系数、磨损率和磨痕3D形貌如图14所示。涂层的开路电位与涂层腐蚀倾向有关,一般情况下,涂层的开路电位越正,被腐蚀的倾向就越小。从图13a中摩擦前、中、后的开路电位演变情况可以看出,在摩擦开动后,所有涂层开路电位与摩擦开动前相比都有大幅度的电位降低,这是由于涂层表面钝化膜在摩擦的作用下被破坏,出现了新的表面,具有较高的电化学活性,通常称之为摩擦引起的表面活化[25]。另外该现象也与摩擦过程中样品中金属离子的释放有关[26]。随后涂层开路电位的波动减小,在较小的范围内变化,达到一个较为稳定的状态,该现象与摩擦持续破坏表面钝化膜、机械钝化、和电化学钝化之间的动态平衡有关,在摩擦结束后,因为摩擦对涂层表面钝化膜的破坏停止,涂层开路电位开始进入另一个稳定阶段[27]。在摩擦开动前,调制比为1∶8的涂层有着最正的开路电位,摩擦时电位较为稳定,1∶6涂层在摩擦时电位在缓慢上升,当实验进行到2500 s时,开路电位开始比1:8的涂层更正。对应从图4b不同调制比交替多层Zr/CrAlSiN涂层摩擦系数曲线中可以看出,调制比为1∶1和1∶2涂层的摩擦系数曲线变化趋势较为类似,1∶6和1∶8涂层的曲线变化趋势较为类似,1∶4涂层的摩擦系数曲线则有较大的波动。调制比为1∶1、1∶2、1∶4、1∶6、1∶8涂层的摩擦系数依次为:0.279、0.341、0.304、0.174、0.167。从调制比为1∶6的涂层开始,摩擦系数明显减小。调制比为1∶1和1∶2涂层的摩擦系数曲线开始时都在短期内降低,随后逐渐升高达到一个相对稳定的状态,其原因很有可能时因为涂层的粗糙度较大,摩擦刚开始时摩擦系数较大,在表面被破坏后,摩擦系数降低到最小值,随后因为涂层损坏和摩擦产生的磨屑导致的磨屑磨损,使得摩擦系数逐渐升高,随后到达一个相对稳定的阶段。调制比为1∶6和1∶8涂层的摩擦系数曲线从摩擦开动后摩擦系数逐渐升高,到达最高值后很快减小到达一个较低的稳定状态。而调制比为1:4的涂层总体上摩擦系数曲线呈现下降阶段,但稳定期不明显,摩擦系数曲线波动较大。调制比为1∶1、1∶2、1∶4、1∶6、1∶8涂层的磨损率依次为:7.82×10-5、1.21×10-5、9.89×10-6、6.94×10-6和2.56×10-6 mm3/(N·m),随着涂层调制比的增大,涂层磨损率逐渐减小。
图13 不同调制比多层Zr/CrAlSiN涂层在人工海水中的开路电位和摩擦系数
图14 不同调制比Zr/CrAlSiN涂层在人工海水中的摩擦系数、磨损率及磨损形貌
图15是不同调制比交替多层Zr/CrAlSiN涂层在海水环境中磨痕的形貌以及摩擦接表界面EDS分析。可以看出,调制比为1∶1和1∶2涂层在磨痕内部都有由磨屑磨损造成的犁沟,并且1∶1涂层还存在着明显的由腐蚀作用造成的点蚀坑,点蚀现象主要是由于海水中氯离子对涂层的破坏造成的,并且摩擦过程中,腐蚀性离子沿着涂层的裂纹和缺陷进入涂层内部形成原电池,加剧涂层的腐蚀作用[28]。调制比为1∶1和1∶2涂层摩擦表界面的EDS分析结果中都观察到基底元素Fe,这主要是由于磨痕深度较深,检测到了基体信号。结合较高的摩擦系数,说明调制比为1∶1和1∶2涂层腐蚀与磨损相互促进作用明显,抗腐蚀磨损性能相对较差。调制比为1∶4涂层的磨痕中没有出现明显的磨屑磨损造成的犁沟,磨痕内也没有发现明显的磨屑,但是磨痕表面有少量涂层片状裂纹出现,但是EDS元素分析结果中没有基底元素出现,都为人工海水中的元素成分。从摩擦曲线波动情况来看,调制比为1∶4涂层的腐蚀与磨损相互作用仍然比较大。调制比为1∶6和1∶8涂层的磨痕相比较于前三种涂层,宽度明显减小,都没有明显的磨粒磨损犁沟痕迹出现,且EDS检基体信号干扰较弱,说明磨痕深度也较浅,腐蚀磨损相互促进作用明显降低。结合涂层在人工海水环境中的摩擦学行为分析和在摩擦条件下的开路电位演变情况可以知道,调制比为1∶6和1∶8涂层具有较好的抗腐蚀磨损性能。抗腐蚀磨损性能依靠涂层的耐腐蚀性能和耐摩擦性能相互影响,调制比为1∶6的涂层因为具有良好的机械强度和耐摩擦性能,因此在摩擦进行一段时间后表现出最正的开路电位值,开路电位测试的结果与极化曲线一致。除此之外,因为CrAlSiN层中化学物与海水发生的化学反应产生的润滑物质,增加为CrAlSiN层厚度比例相当于增加Si等元素的摩擦化学作用,有利于生产更多有润滑作用的界面产物,促使涂层的海水环境摩擦系数降低,抗腐蚀磨损性能增强[29,30]。综合来看,多层Zr/CrAlSiN涂层增加的CrAlSiN厚度比例在调控涂层力学性能和干摩擦性能的同时,提高涂层静态抗腐蚀性能和摩擦开动后的抗腐蚀磨损性能,最终使得具有“层中层”结构的Zr/[Al(Si)N/CrN]涂层抗腐蚀磨损性能得以提升。尽管调制比为1∶8的涂层在海水环境呈现出了最低的磨损率,但考虑到调制比为1∶6的涂层与调制比为1∶8的涂层略高的磨损率、相似的耐蚀性以及更好的综合机械性能,可以认为调制比为1∶6的涂层在海水环境将呈现出最好的抗腐蚀磨损综合防护性能。
图15 不同调制比多层Zr/CrAlSiN涂层磨痕形貌图
3 结论
采用多弧离子镀技术制备了调制比分别为1∶1、1∶2、1∶4、1∶6、1∶8的交替多层Zr/CrAlSiN涂层,通过交替沉积与间歇性接近不同靶材相结合的方法最终获得了具有“层中层”结构特征的Zr/[Al(Si)N/CrN]多元多层涂层,该“层中层”结构设计对涂层生长缺陷具有明显的抑制和修复作用。随着CrAlSiN层厚度比例增大,涂层的硬度和弹性模量呈现增大趋势,并在调制比为1∶6时出现拐点。随CrAlSiN层厚度增加,涂层硬度增大,但涂层韧性降低,促使涂层的结合力逐渐降低后有所升高,随后再次降低,调制比为1∶6时涂层综合力学性能最佳。随着涂层力学性能的变化,涂层在无腐蚀工况条件下耐磨性能在调制比为1∶6也最好。由于CrAlSiN层具有多层Al(Si)N/CrN结构,增加CrAlSiN层厚度比例相当于增加复合涂层横向界面,提升涂层腐蚀性环境中的阻隔作用,因此CrAlSiN层厚度比例的增加既可以提升无摩擦磨损时涂层的耐腐蚀性能又可提升涂层摩擦开动后涂层耐腐蚀性能,并进一步降低涂层腐蚀和磨损的相互促进作用。综合考虑,调制比为1∶6和1∶8的涂层在海水环境中展现出了较好的抗腐蚀磨损性能。
参考文献
1 Jiang X X, Li S Z, Li S. Corrosive Wear of Metals [M]. Beijing: Chemical Industry Press, 2003
1 姜晓霞, 李诗卓, 李曙. 金属的腐蚀磨损 [M]. 北京: 化学工业出版社, 2003
2 Jhi S H, Ihm J, Louie S G, et al. Electronic mechanism of hardness enhancement in transition-metal carbonitrides [J]. Nature, 1999, 399: 132
3 Kumar D D, Kumard N, Kalaiselvam S, et al. Wear resistant super-hard multilayer transition metal-nitride coatings [J]. Surf. Interfaces, 2017, 7: 74
4 Shan L, Wang Y X, Zhang Y R, et al. Tribocorrosion behaviors of PVD CrN coated stainless steel in seawater [J]. Wear, 2016, 362-363: 97
5 Deng J X, Wu F F, Lian Y S, et al. Erosion wear of CrN, TiN, CrAlN, and TiAlN PVD nitride coatings [J]. Int. J. Refract. Met. Hard Mater., 2012, 35: 10
6 Ye Y W, Wang Y X, Chen H, et al. Doping carbon to improve the tribological performance of CrN coatings in seawater [J]. Tribol. Int., 2015, 90: 362
7 Cui P P, Li W, Liu P, et al. Effects of nitrogen content on microstructures and mechanical properties of (AlCrTiZrHf) N high-entropy alloy nitride films [J]. J. Alloy. Compd., 2020, 834: 155063
8 Fu Y Q, Zhou F, Wang Q Z, et al. Electrochemical and tribocorrosion performances of CrMoSiCN coating on Ti-6Al-4V titanium alloy in artificial seawater [J]. Corros. Sci., 2020, 165: 108385
9 Ma F L, Li J L, Zeng Z X, et al. Tribocorrosion behavior in artificial seawater and anti-microbiologically influenced corrosion properties of TiSiN-Cu coating on F690 steel [J]. J. Mater. Sci. Technol., 2019, 35: 448
10 Wu Z W, Zhou F, Chen K M, et al. Friction and wear properties of CrSiCN coatings with low carbon content as sliding against SiC and steel balls in water [J]. Tribol. Int., 2016, 94: 176
11 Chang Y Y, Yang Y J, Weng S Y. Effect of interlayer design on the mechanical properties of AlTiCrN and multilayered AlTiCrN/TiSiN hard coatings [J]. Surf. Coat. Technol., 2020, 389: 125637
12 Cui W F, Qin G W, Duan J Z, et al. A graded nano-TiN coating on biomedical Ti alloy: Low friction coefficient, good bonding and biocompatibility [J]. Mater. Sci. Eng., 2017, 71C: 520
13 Li G, Zhang L, Cai F, et al. Characterization and corrosion behaviors of TiN/TiAlN multilayer coatings by ion source enhanced hybrid arc ion plating [J]. Surf. Coat. Technol., 2019, 366: 355
14 Escobar C, Villarreal M, Caicedo J C, et al. Diagnostic of corrosion-erosion evolution for [Hf-Nitrides/V-Nitrides]n structures [J]. Thin Solid Films, 2013, 545: 194
15 Teles V C, de Mello J D B, da Silva W M. Abrasive wear of multilayered/gradient CrAlSiN PVD coatings: Effect of interface roughness and of superficial flaws [J]. Wear, 2017, 376/377: 1691
16 Cai F, Zhang J M, Wang J M, et al. Improved adhesion and erosion wear performance of CrSiN/Cr multi-layer coatings on Ti alloy by inserting ductile Cr layers [J]. Tribol. Int., 2021, 153: 106657
17 Verma N, Jayaram V. Role of interface curvature on stress distribution under indentation for ZrN/Zr multilayer coating [J]. Thin Solid Films, 2014, 571: 283
18 Zhang J J, Wang M X, Yang J, et al. Enhancing mechanical and tribological performance of multilayered CrN/ZrN coatings [J]. Surf. Coat. Technol., 2007, 201: 5186
19 Merl D K, Panjan P, ?ekada M, et al. The corrosion behavior of Cr-(C,N) PVD hard coatings deposited on various substrates [J]. Electrochim. Acta, 2004, 49: 1527
20 Kameneva A, Corrosion Kichigin V., wear, and friction behavior of a number of multilayer two-, three- and multicomponent nitride coatings on different substrates, depending on the phase and elemental composition gradient [J]. Appl. Surf. Sci., 2019, 489: 165
21 Rosalbino F, Angelini E, Macciò D, et al. Application of EIS to assess the effect of rare earths small addition on the corrosion behaviour of Zn-5%Al (Galfan) alloy in neutral aerated sodium chloride solution [J]. Electrochim. Acta, 2009, 54: 1204
22 Pajkossy T. Impedance spectroscopy at interfaces of metals and aqueous solutions—Surface roughness, CPE and related issues [J]. Solid State Ionics, 2005, 176: 1997
23 Liu C L, Chu P K, Lin G Q, et al. Effects of Ti/TiN multilayer on corrosion resistance of nickel-titanium orthodontic brackets in artificial saliva [J]. Corros. Sci., 2007, 49: 3783
24 Guan X Y, Wang Y X, Zhang G G, et al. Microstructures and properties of Zr/CrN multilayer coatings fabricated by multi-arc ion plating [J]. Tribol. Int., 2017, 106: 78
25 Zhang Y, Yin X Y, Yan F Y. Effect of halide concentration on tribocorrosion behaviour of 304SS in artificial seawater [J]. Corros. Sci., 2015, 99: 272
26 Espallargas N, Torres C, Mu?oz A I. A metal ion release study of CoCrMo exposed to corrosion and tribocorrosion conditions in simulated body fluids [J]. Wear, 2015, 332/333: 669
27 Yan Y, Neville A, Dowson D, et al. Effect of metallic nanoparticles on the biotribocorrosion behaviour of Metal-on-Metal hip prostheses [J]. Wear, 2009, 267: 683
28 Tang B, Li Y M, Qin L, et al. Study on fretting wear behaviour of CrN coatings by IBED [J]. Trans. Mater. Heat Treat., 2005, 26(3): 58
28 唐宾, 李咏梅, 秦林等. 离子束增强沉积CrN膜层及其微动摩擦学性能研究 [J]. 材料热处理学报, 2005, 26(3): 58
29 Luo F, Gao K W, Tao C H, et al. Tribological behavior of chromium oxide coatings under dry friction and water lubrication conditions [J]. Mater. Res. Appl., 2009, 3: 14
29 罗飞, 高克玮, 陶春虎等. 干摩擦及水润滑下氧化铬陶瓷薄膜的摩擦学性能 [J]. 材料研究与应用, 2009, 3: 14
免责声明:本网站所转载的文字、图片与视频资料版权归原创作者所有,如果涉及侵权,请第一时间联系本网删除。
-
标签: Zr/[Al(Si)N/CrN]涂层, “层中层”结构, 海水环境, 腐蚀磨损特性
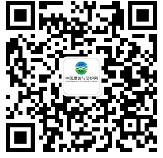
官方微信
《腐蚀与防护网电子期刊》征订启事
- 投稿联系:编辑部
- 电话:010-62316606-806
- 邮箱:fsfhzy666@163.com
- 腐蚀与防护网官方QQ群:140808414