随着使用年限的增长,飞机金属结构受到环境影响而产生腐蚀的问题日益突出。腐蚀会削弱结构的承力面积,降低材料的抗疲劳性能,进而影响飞行安全和寿命指标。当前,国内外已经开展了大量材料的腐蚀/疲劳试验,得到了各种材料在不同腐蚀环境下的寿命退化规律,形成了两种常用的评估飞机结构腐蚀疲劳关键件剩余寿命的方法:一种是从微观角度采用电化学腐蚀方法的点蚀和剥蚀模型[1-7],如Sriaman和pidapati[1]提出的同时考虑腐蚀环境和疲劳加载的裂纹形成和扩展的全寿命模型,Merati[2]提出的三阶段腐蚀疲劳裂纹计算方法,Wang等[3]提出的点蚀疲劳寿命概率评估方法,Dolly等[4]采用断裂力学方法提出的点蚀疲劳寿命衰减模型,vander Walde和Hillberry[5]提出的腐蚀形核导致早期疲劳裂纹扩展的寿命评估方法,Chubb等[6]提出的剥蚀寿命计算方法等;另一种则是从宏观角度考虑腐蚀环境影响的名义应力法,如刘文珽等[8-9]对某型飞机结构延寿时采用的腐蚀影响系数法,国内张福泽[10]、李玉海[11]、崔常京[12]、张有宏[13]、陈跃良[14]等在不同试验条件下测定LY12CZ铝合金的腐蚀变化规律及疲劳性能衰减规律等。上述方法在分析金属材料的腐蚀损伤、预测结构材料的剩余寿命工作中发挥了重要作用。但是,上述两种方法主要是采用预腐蚀/疲劳或腐蚀疲劳共同作用的试验方法,而较少考虑腐蚀/疲劳交替作用下结构寿命的退化状况。
事实上,飞机结构在使用过程中经历的应该是一种典型的“地面腐蚀+空中疲劳”的交替过程,即地面停放时受到机场环境的腐蚀作用、空中飞行时产生疲劳的过程(3000m以上高空的腐蚀影响很小,可以忽略)。陈群志等[15]采用周期浸润加速腐蚀试验与疲劳试验相结合的方法,研究了特定条件下疲劳载荷与腐蚀环境交替作用对某型飞机机翼主梁疲劳寿命的影响,但只给出了在一种载荷与腐蚀交替情况下的试验结论。杨晓华等[16]初步提出了交替作用下的腐蚀/疲劳累积迟滞模型,但是需要试验的进一步验证。范超华[17]通过试验发现腐蚀/疲劳交替作用下铝合金试样的寿命分布可以用正态分布描述。Menan和Henaff[18-19]在研究了频率和盐溶液对2024铝合金腐蚀疲劳裂纹扩展行为影响的基础上,发现交替浸泡不同于持久浸泡(即预腐蚀),并指出了进一步研究交替腐蚀/疲劳的必要性。
针对国内外较少研究腐蚀/疲劳交替作用下飞机金属材料疲劳寿命的退化规律,本文在模拟了飞机结构经历的“地面腐蚀+空中疲劳”载荷/环境历程的基础上,提出了一种腐蚀/疲劳交替作用下的疲劳寿命计算方法。首先,以飞机上常用的2A12-T4铝合金材料制成标准试样进行预腐蚀/疲劳试验,并模拟试样经历腐蚀/疲劳交替作用,计算得到了理论疲劳寿命,发现其偏于保守。随后,在分析腐蚀/疲劳交替作用的基础上,采用回归算法,提出基于均匀分布耦合损伤形式的疲劳寿命计算模型;并分别采用Bp、Elman神经网络算法进行验证。通过对比4组不同加载水平下的预测结果与试验结果,发现本文提出的均匀分布耦合损伤模型可以较好地计算腐蚀/疲劳交替作用下铝合金试样的疲劳寿命。进一步通过计算与试验对比分析了交替方式从21万次/3天变化至21万次/1天时试样的疲劳寿命值,结果表明:均匀分布耦合模型也可以用于加载循环与腐蚀周期组合发生变化时的疲劳寿命预测,具有较好的适用性。
1试验安排与结果
试验所用材料为2A12-T4铝合金板材,板厚为2mm,轧制方向取材,屈服强度为325Mpa,断裂强度为470Mpa,按照HB5143-9《金属室温拉伸试验方法》要求加工,试样尺寸及单面腐蚀区域如图1所示。
图1试样尺寸及单面腐蚀区域
本文分别进行了预腐蚀/疲劳和腐蚀/疲劳交替两种试验。预腐蚀/疲劳试验是指仅对试样进行一次预腐蚀试验而后进行疲劳试验至试样断裂;腐蚀/疲劳交替试验采用多轮交替方式进行,以21万次/3天为例,其加载过程为腐蚀3天+疲劳21万次+腐蚀3天+疲劳21万次+腐蚀3天……交替至试样最后一次疲劳断裂为止,得到其总疲劳循环次数。
腐蚀试验在盐雾腐蚀试验箱中进行,恒温35℃,EXCO溶液局部浸泡,腐蚀试验完成后加速吹干试样,随后进行疲劳试验。疲劳试验在室温条件下进行。疲劳试验设备为MTS810500kN疲劳试验机。加载条件:应力比为0.6,最大应力为294Mpa,正弦波。试验完成后,取断裂部位发生在腐蚀区域的试样寿命记为有效数据,每组试验均取4个有效数据。
假设疲劳试验结果服从对数正态分布[8,17],则试样的中值疲劳寿命为
式中:N50(t)为腐蚀试样的中值疲劳寿命;mt为预腐蚀t天的有效试样个数;Ni(t)为第i件试样的疲劳寿命。
根据式(1),分别计算得到每组试样在经历预腐蚀/疲劳试验和腐蚀/疲劳交替试验后的中值疲劳寿命与离差,如表1和表2所示。
表1预腐蚀/疲劳试验结果
表2腐蚀/疲劳交替试验结果
2 腐蚀/疲劳交替寿命计算方法
2.1 基于预腐蚀/疲劳试验的交替寿命计算
根据Miner线性累积损伤理论,重复加载条件下总循环次数达到1时,试样失效。
式中:ni为某级应力水平下的加载循环数;k为应力水平的种类;Ni为该级应力水平下发生破坏所需的循环次数。
模拟使用环境下飞机结构承受的腐蚀/疲劳交替过程,结合式(2),采用式(3)计算每个组别的交替寿命。
式中:ΔNi为第i次疲劳加载的循环数;n为总交替循环次数。
经历不同预腐蚀天数的试样的中值疲劳寿命可由表1拟合得到,如式(4)所示,其置信度为0.958,拟合结果较好。
以预腐蚀天数为2天的一组试样为例,模拟交替方式为140000次/2天的试样所经历的疲劳/腐蚀作用,采用式(3)和式(4)依次计算其预期的受载历程所得到的相对损伤量。
计算发现,当试样模拟的第4轮疲劳试验还未达到140000次的预计疲劳循环数时,总累积损伤就达到1。假设第4轮实际完成N4次循环,则由
可以得到N4=108863次。由此,该组试样的预期总疲劳循环次数为
140000+140000+140000+108863=528863
采用上述方法,依次计算得到不同交替周期下试样的交替疲劳寿命,与试验得到的实际值进行比较,结果如图2所示。
图2 理论交替疲劳寿命与实际试验值对比
从图2中可以看出,采用预腐蚀/疲劳试验所模拟得到的腐蚀/疲劳交替寿命预测值均小于真实的试验值,而且误差较大。为了减少误差,本文进一步提出了更为精确的计算模型。
2.2 腐蚀/疲劳交替寿命计算模型
飞机结构在真实服役过程中承受的载荷/环境历程应该是一种典型的多轮腐蚀/疲劳交替过程,即“地面腐蚀+空中疲劳”,如图3所示。交替过程主要由3个阶段组成:①腐蚀过程,飞机金属材料由于地面停放腐蚀导致承力面减小,抗疲劳性能下降;②疲劳过程,空中飞行过程产生的疲劳损伤;③耦合损伤过程,在起飞/降落时飞机结构由于腐蚀介质的侵入导致的短时间腐蚀以及由于地面停放卸载而导致的低载锻炼效应[20],本文统称其为耦合损伤效应。
图3 飞机金属结构经历的载荷/环境历程
根据图3,综合式(2)和式(3),腐蚀/疲劳交替寿命可采用式(5)计算。
式中:Dci为第i次腐蚀造成的当量损伤;Dfi为第i次疲劳造成的当量损伤;E(Dfi,Dci)为第i次腐蚀/疲劳交替过程中的耦合损伤;m为总腐蚀次数;n为总疲劳次数;l为总交替次数;η为总损伤量,考虑到疲劳卸载效应及腐蚀短时间残留影响,η应大于1[20],但是由于国内外目前仍无分析腐蚀/疲劳交替耦合损伤的定量计算方法[16,19],结合本文的试验安排,仍假定η=1成立,以便于对交替过程中的耦合损伤进行定量分析。同时,根据表2的试验安排,式(5)中m=n=l成立,即试样共经历n次腐蚀/疲劳交替过程。
当前,国内外开展了大量的预腐蚀/疲劳试验[1-14]来测定不同预腐蚀天数后材料疲劳性能的下降。由表1可知,腐蚀所造成的试样疲劳性能下降的Dc可以由式(6)计算。
式中:N50(t)N0为目前工程上常用的腐蚀影响系数,即C(t)曲线,它反映经历加速腐蚀t天后(模拟自然环境作用X年)试样的中值疲劳寿命与完好试样寿命的比值;N0为完好试样的中值疲劳寿命。
由此,式(5)可以进一步表示为
式中:N50[(i-1)×t]为交替周期为t天试样第i次腐蚀前的中值疲劳寿命,N50(i×t)为第i次腐蚀后的中值疲劳寿命,它们均可由式(4)计算得到;Nfi为第i次加载的疲劳循环次数。
考虑加载循环趋于零或未发生腐蚀,即耦合损伤为零的极端情况,可以得到两种极限寿命:①纯腐蚀的极限寿命可根据结构静强度要求计算得到,参见文献[21];②纯疲劳的极限寿命即无腐蚀条件下的疲劳寿命,可参考文中表1首行。
2.3 Bp与Elman神经网络计算模型
鉴于交替试验的复杂性,可以采用具有较好非线性映射能力的神经网络算法来对不同加载方式下的中值疲劳寿命值进行分析预测。
输入向量选为表2中所示的加载循环数、交替周期;输出向量选为表2中对应的疲劳寿命值。由于表2中的加载循环与交替周期相差较大,为消除数据奇异性的影响,训练前分别按照加载循环、交替次数和疲劳寿命进行归一化处理。以表2中疲劳寿命的归一化为例,其处理方法为每组加载方式对应的疲劳寿命值与表2中最大寿命值的比值。
1)Bp网络
训练参数设定如下:输入层神经元个数为11,输出层神经元个数为1,中间层神经元个数为23,网络中间层传递函数采用S型正切函数tan-sig;输出层采用其对数函数logsig。
其中,S型正切函数tansig为
正切函数的对数函数logsig为
将表2中经过归一化的数据代入Bp网络中进行训练,计算表明在训练至350次时,误差稳定在0.0005左右,精度可以满足应用要求。
2)Elman网络
训练参数设定如下:输入层神经元个数为11,输出层神经元个数为1,隐含层神经元个数为11。
将表2中经过归一化的数据代入Elman网络中进行训练,发现在训练至160次时,误差稳定在0.002左右,精度可以满足应用要求。
3 计算与验证
根据表2的试验安排,本文假设腐蚀/疲劳交替作用下的耦合损伤服从均匀分布,即每个交替过程的耦合损伤相等:
结合表1、表2和式(7),可以计算得到不同交替过程对应的耦合损伤。进一步结合式(10),采用回归算法,建立以加载循环Nfi和交替周期t同耦合损伤f之间的函数关系为
其置信度为0.9995,相关系数R=0.9883。
开展4种交替加载方式下的腐蚀/疲劳试验,计算得到其中值疲劳寿命与离差,记入表3。同时,将加载循环次数和交替周期分别代入基于均匀分布的耦合损伤计算模型和神经网络模型进行计算,得到的疲劳寿命与误差记入表3。
表33 种模型计算的疲劳寿命与实际值对比
由表3可见,上述3种计算方法得到的疲劳寿命值与真实值相差最大不超过7%,误差较小。计算表明,本文提出的均匀分布耦合损伤模型可以较准确地计算腐蚀/疲劳交替作用下2A12-T4铝合金试样疲劳性能的变化规律。
值得注意的是,本文在交替试验过程中,并未观察到铝合金试样发生剥蚀现象,点蚀仍然起主要作用,即本文的模型在点蚀阶段是适用的,在剥蚀阶段的适用性仍需要进一步地探讨。如图4所示,交替方式为6万次/2天试样的断口形貌,其中存在由点蚀坑引起的两个疲劳源。
此外,本文主要分析计算了等幅谱与EXCO溶液浸泡条件下的耦合损伤,未来应进一步采用飞机真实使用载荷谱与环境谱进行试验,研究确定等幅谱与真实载荷谱、溶液浸泡与环境谱之间的当量关系,从而将本文的试验结果与模型应用到飞机结构的实际寿命监控中。
图4 交替方式6万次/2天试样断口的SEM形貌
4 应用分析
事实上,飞机在使用过程中,停放时间和疲劳过程是动态的、变化的,即本文所采用的疲劳加载循环与腐蚀周期的组合也应是变化的才更接近于飞机的实际使用状况。式(11)给出了其交替过程中的损伤计算方式,在计算变化的交替加载时是否仍然适用需要试验验证。为此,结合式(7)和式(11),采用均匀耦合损伤模型计算了交替方式从21万次/3天变化至21万次/1天时试样的疲劳寿命,并与试验结果进行了对比,试验条件与上文一致,结果如表4和图5所示。加载方式分别为:①交替21万次/3天至断裂;②交替21万次/3天两次+交替21万次/2天一次至断裂;③交替21万次/3天一次+交替21万次/2天两次至断裂;④交替21万次/2天至断裂;⑤交替21万次/2天两次+交替21万次/1天一次至断裂;⑥交替21万次/2天一次+交替21万次/1天三次至断裂;⑦交替21万次/1天至断裂.
表4 交替方式从21万次/3天变化至21万次/1天时2A12-T4铝合金试样疲劳寿命与日历寿命
图5 交替方式从21万次/3天变化至21万次/1天时疲劳寿命与日历使用时间的关系
从表4和图5可以看出:①随着交替天数逐渐变短,试样实际所达到的疲劳寿命值逐渐增大,日历使用时间逐渐变短。这与实际使用情况是相符的,即如果飞机的停放时间较短,腐蚀对其疲劳性能的削减就小,疲劳性能的利用程度相应地就大;②通过对比实际试验结果与模型计算结果,发现本文提出的均匀分布耦合计算模型可以较准确地计算腐蚀天数与疲劳加载组合发生变化时试样的疲劳寿命;③在交替方式从21万次/3天变化至21万次/1天时,随着交替过程中腐蚀天数的缩短,疲劳寿命值逐渐增大,通过均匀分布耦合模型计算得到在达到总疲劳699708次循环时,日历寿命值为8.8068天。上述计算结果和试验结果对比表明,本文提出的均匀分布耦合损伤模型可以为分析计算使用环境下飞机结构的剩余寿命提供参考。
5 结论
根据飞机结构经历的“地面腐蚀+空中疲劳”载荷/环境历程,提出了一种基于均匀分布耦合损伤形式的腐蚀/疲劳交替寿命计算模型,可以用来计算不同加载方式下的腐蚀/疲劳交替寿命。
1)以2A12-T4铝合金试样预腐蚀/疲劳试验为基础,发现其在模拟计算腐蚀/疲劳交替时计算得到的疲劳寿命值偏于保守,理论计算值同真实试验结果相比,误差较大。
2)采用回归算法,构建以疲劳加载循环数和腐蚀周期为变量的均匀分布耦合损伤计算方法,建立腐蚀/疲劳交替寿命计算模型;并分别采用Bp和Elman神经网络算法进行验证,结果表明均匀分布耦合损伤模型的计算结果与真实值误差较小。
3)在均匀分布耦合模型的基础上,分析了不同疲劳加载与腐蚀天数组合下的2A12-T4铝合金试样疲劳寿命的变化规律。以交替方式从21万次/3天变化至21万次/1天的计算值与试验值为例,发现随着交替过程中腐蚀天数的缩短,疲劳寿命值增大,在达到总疲劳699708次循环时,日历使用时间为8.8068天。计算结果和试验值对比表明,本文提出的均匀分布耦合损伤计算模型可以用来计算疲劳加载与腐蚀天数发生变化时铝合金试样的疲劳寿命,具有较好的适用性。
参考文献
[1]Sriaman M R , pidapati R M .Life prediction of aircraft aluminum subjected to pitting corrosion under fatigue con-dition.Journal of Aircraft , 2009,46(4):1253-1259.
[2] Merati A. A study of nucleation and fatigue behavior of an aerospace aluminium alloy 2024-T3. International Journal of Fatigue, 2005, 27(10): 33-44.
[3] Wang Q Y, Kawagoishi N, Chen Q,et al. Evaluation of the probability distribution of pitting corrosion fatigue life in aircraft materials. Acta Mechanica Sinica, 2003, 19 (3): 247-252.
[4] Dolley EJ, LeeB, WeR P. The effect of pitting corrosion on fatigue life. Fatigue & Fracture of Engineering Materi- als &. Structures, 2000, 23(7): 555-560.
[5] van der Walde K, Hillberry B M. Initiation and shape of development of corrosion nucleated fatigue cracking. In- ternational Journal of Fatigue, 2007, 29(10): 1269-1281.
[6] Chubb J P,Morad T A,Hockenhull B S,et al. The effect of exfoliation corrosion on the fracture and fatigue behavior of 7178-T6 aluminium. International Journal of Fatigue,1995,17(1): 49-54.
[7] Min L, Bombardier Y, Renaud G. Probabilistic risk anal- ysis for aircraft structures with limited in service dama- ges.28th International Congress of the Aeronautical Sci- ences, 2012: 1-11.
[8] Liu W T,Li Y H. Aircraft structure calendar life evolurtion technology. Beijing: Aeronautic Industry Press, 2004. (in Chinese) 刘文蜓,李玉海,飞机结构日历寿命体系评定技术.北京:航空工业出版社,2004.
[9] He X F, Liu W T, Jjiang D B. Method for fatigue test of aircraft structures considering corrosion influence. Journal of Beijing University of Aeronautics and Astronautics, 2003,29(1): 20-22. (in Chinese) . 贺小帆,刘文斑,蒋东滨,一种考虑腐蚀影响的飞机结构疲劳试验方法,北京航空航天大学学报,2003,29(1):20-22.
[10] ZhangF Z, Tan W D, Song J, et al. Effect of corrosion temperature on fatigue life of aircraft. Acta Aeronautica et Astronautica Sinica, 2004, 25(5): 473- 475. (in Chinese) 张福泽,谭卫东,宋军,等.腐蚀温度对‘飞机疲劳寿命的影响.航空学报,2004, 25(5): 473-475.
[11] Li Y H, HeXF, Chen Q z, et al. Investigation and variable rule for corrosion depth of aluminum specimen. Journal of Beijing University of Aeronautics and Astronautics, 2002,28 (1): 98-101. (in Chinese) 李玉海,贺小帆,陈群志,等.铝合金试件腐蚀深度分布特性及变化规律研究.北京航空航天大学学报,2002, 28 (1): 98-101.
[12] CuiCJ, Chen QZ, Wang Y Y, et al. Corrosion behavior of LY12CZ aluminum alloy in a laboratory simulated at mospheric environment of one airport. Corrosion Science and Projection Technology, 2009, 21(3): 291-294. (in Chinese)崔常京,陈群志,王逾涯,等.模拟某机场大气环境下 LY12CZ铝合金的腐蚀行为及其当量关系的建立,腐蚀科学与防护技术,2009, 21(3): 291-294.
[13] Zhang Y H. The corrosion damage and its effect on life of aircraft structure. Xi' an: Northwestern Polytechnical University, 2007. (in Chinese) 张有宏.飞机结构的腐蚀损伤及其对寿命的影响.西安:西北工业大学,2007.
[14] Chen Y L, JinP, LinDX, et al. Naval aircraft structure corrosion control and strength evaluation. Beijing: National Defence Industry Press, 2009. (in Chinese) 陈跃良,金平,林典雄,等.海军飞机结构腐蚀控制及强度评估.北京:国防工业出版社,2009.
[15] Chen Q Z, Yang R Q, LiG Y, et al. Influence of corrosion on fatigue life of 30CrMnSiNi2A steel structure. Equipment Environment Engineering,2007, 4(5): 7-10. in Chinese) 陈群志,杨瑞琴,李国元,等.腐蚀对30CrMnSiNi2A钢结构疲劳寿命的影响.装备环境工程,2007, 4(5): 7-10.
[16] YangX H, Yao W X, Chen Y L. Research calendar life of aircraft structure considering the effects of calendar envi- ronment. Chinese Journal of Applied Mechanics, 2002, 19 (3): 157- 159. (in Chinese) 杨晓华,姚卫星,陈跃良.考虑日历环境影响的结构日历寿命研究.应用力学学报,2002, 19(3): 157-159.
[17] Fan C H. Study on some crtical problem for single air-craft structure life sureillance. Xi' an: Air Force Engi-neering University, 2010. (in Chinese) 范超华。“飞机结构单机寿命监控若干关键问题研究。西安:空军工程大学,2010.
[18] Menan F, Henaff G. Influence of frequency and exposure to a saline solution on the corrosion fatigue crack growth behavior of aluminum alloy 2024. International Journal of Fatigue, 2009,31(33): 1684-1695.
[19] Menan F, Henaff G. Synergistic action of fatigue and corrosion during crack growth in the 2024 aluminium alloy. Procedia Engineering,2010, 2(3): 1441-1450.
[20] Xie L Y, Lv W G, Shi Z F. Experimental study on fatigue damage under two level loading. Journal of Mechanical Strength, 1994,16(3): 589- -594. (in Chinese) 谢里阳,吕文阁,师照峰.两级载荷作用下疲劳损伤状态的实验研究.机械强度,1994, 16(3): 589-594.
[21] Zhang H W, He Y T, Wu L M, et al. Corrosion/ fatigue alternative life predicting methodology for aircraft metal structures in consideration of static stress. Chinese Journal of Applied Mechanics, 2012, 29(5): 589 -594. ( in Chinese) 张海威,何宇廷,伍黎明,等.考虑静强度要求的飞机金属结构腐蚀/疲劳交替寿命预测方法.应用力学学报,2012,29(5): 589- 594.
免责声明:本网站所转载的文字、图片与视频资料版权归原创作者所有,如果涉及侵权,请第一时间联系本网删除。
-
标签: 腐蚀, 疲劳, 神经网络, 均匀分布, 2A12-T4铝合金
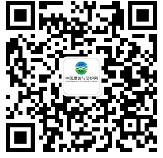
官方微信
《中国腐蚀与防护网电子期刊》征订启事
- 投稿联系:编辑部
- 电话:010-62316606-806
- 邮箱:fsfhzy666@163.com
- 中国腐蚀与防护网官方QQ群:140808414