相控阵超声波探伤技术是通过控制换能器阵列中各阵元的激励(或接收)脉冲的时间延迟,改变由各阵元发射(或接收)声波到达(或来自)物体内某点时的相位关系,实现聚焦点和声束方位的变化,完成声成像的技术,与常规A型脉冲反射式超声波探伤技术相比优势明显,主要体现为相控阵超声波探伤覆盖检测范围大,可记录数据和图像,缺陷尺寸测量更精确。为控制钢材内部质量,研究人员单位于2013年陆续上线两台自动化相控阵水浸超声波圆钢探伤设备,可实现?(15~100) mm 钢棒材的内部探伤。随着不断摸索优化调整探伤参数,在多年的使用过程中,两台机器检验发现了一些探伤不合格波形。超声波探伤不合格材料的判定,决定着纠正及预防措施是否合理有效。而实际工作中许多不合格波形的特征不明显或者同一批不合格棒材混杂多种缺陷,仅依赖波形和探伤经验来判定是不充分的。目前国内对相控阵检测技术的研究多集中在探伤波形、波形变化及与常规超声等的比较方面进行论述,较少涉及波形不合格钢材的低倍、金相等理化检验分析,而这些工作也是探伤技术人员需要深入了解与分析的。来自东北特钢集团抚顺特殊钢股份有限公司的刘桂江、刘希儒、佟峂等研究人员将实际生产检验中出现的探伤不合格相控阵波形与便携式A型超声波探伤信号、酸浸低倍组织、光学显微组织及扫描电镜形貌等分析结果结合起来,建立不合格波形与缺陷的对照数据库及系统的缺陷检验分析流程,这对缺陷的判定、不合格材料的分析及整改预防均有指导意义。
1 探伤不合格的典型波形信息
选取了几种典型探伤不合格试样,其钢种、棒材规格尺寸及BIS PA 15-100相控阵探伤参数分别如表1所示。
表1 探伤不合格试样的相关参数
1号试样不合格位置集中在钢材端部,局部连续反射,横波无异常;2号试样在横波、纵波同一位置发现不合格反射,可根据此特征判断钢材近皮下位置存在反射;3号试样为单支或局部的连续反射,各探头同时报警,报警信号高高扬起,通常判断为缩孔;4号试样波形多点反射局部连续,整体探伤噪声较高,常出现在高合金比的不锈钢模具钢材中。各品种主要生产工艺均为电炉冶炼→炉外精炼→真空脱气→连铸→连轧,探伤标准均为GB/T 4162—2008《锻轧钢棒超声检测方法》的B级,探伤测试使用试样棒均为与探伤钢材同尺寸的试样棒。
2 金相检验
2.1 低倍组织
相控阵探伤过程中,发现纵波不合格后,设备自动分选至不合格收集区,并标记特殊标识,在辊道上使用便携式A型超声波探伤仪进行定位和确认,并在需要取低倍组织试片处作标记,钢材下线后取样并进行低倍组织检验。1~4号试样探伤不合格的低倍组织形貌如图1所示。
图1 探伤不合格试样的低倍检验形貌
1号试样的近中心及半径1/2位置可见明显发状裂纹,可评定为白点0.5级,2号试样可评定为内部夹杂,3号试样可评定为缩孔0.5级,4号试样可评定为中心偏析1级。
2.2 显微组织
在进行酸浸低倍检验后,在低倍缺陷处取样进行高倍金相检验,以进一步确定缺陷性质和产生原因。以上4种不合格试样的典型高倍形貌如图2~图5所示。
图2 1号试样的显微组织形貌
图3 2号试样缺陷的微观形貌
图4 3号试样缺陷的微观形貌
图5 4号试样的显微组织形貌
图2中1号试样显微组织为铁素体+珠光体,基体局部偏析,裂纹出现在偏析处,试样上存在非平衡组织。由图3可见,2号试样棒材横向有大颗粒夹杂物;由图4可见3号试样连铸坯尾坯有残余缩孔的孔洞状缺陷;由图5可见4号试样白色碳化物偏析,钢材心部组织呈密集网状沿晶开裂,开裂裂纹周边已氧化并有氧化物质点。
2.3 缺陷综合分析
1号试样相控阵探伤出现典型不合格波形的钢材缺陷多集中在钢材两端部,不合格支数比例较少,A型超声波探伤仪定位时可见方向性,低倍组织显示为近中心及半径1/2位置明显裂纹,裂纹细长,高倍下裂纹内部及两侧无明显氧化、脱碳,裂纹应力感强,呈锯齿状,综合以上信息判断缺陷为钢材白点裂纹,白点裂纹的产生主要与钢中氢含量及钢材的冷却条件相关,经调查本例中钢材采用缓冷坑坑冷,同批次钢材无探伤不合格,而堆冷钢材发生端部探伤不合格,是因为个别钢材端部受风后冷却较快氢来不及逸出而形成白点裂纹。
2号试样相控阵探伤出现典型不合格波形,存在横、纵波同时报警波形,A型超声波探伤仪定位时有近表皮不合格反射,不合格支数比例较少,高、低倍组织可见内部有夹杂物,经扫描电镜及能谱分析,确定了夹杂物的主要成分为铝、镁的氧化物及硫化钙,能谱分析结果见表2。
表2 2号试样夹杂物的能谱分析结果(质量分数)
调取生产记录,发现连铸过程中尾炉存在人工手动捣流现象,分析认为夹杂物由连铸水口堆积物脱落进入钢坯内形成。
3号试样相控阵探伤不合格显示为整支或半支连续不合格,A型超声波探伤仪定位时见底波下降现象,低倍组织显示孔洞状缺陷,钢材不合格支数与连铸机流数接近,高倍显示裂纹内部无明显氧化、脱碳现象,综合连铸尾坯切除长度略短等信息判断不合格缺陷的产生原因为残余缩孔。
4号试样相控阵探伤不合格波形为密集多点及局部连续状反射,A型超声波探伤仪反射均位于钢材中心位置,低倍组织无开裂性缺陷,钢材中心偏析0.5级,沿中心黑心处取纵向样,高倍可见碳化物聚集情况,局部形成沿晶网状开裂,属于过烧引起的裂纹。该钢材加热温度为(1210±10)℃,调取生产加热曲线可知,存在温度超过1270℃的温度段,属于连续加热炉操作人员对坯料装炉位置判断不准确,合炉加热不当,晶界过烧熔化形成的裂纹,白色碳化物是局部偏析造成。
3 缺陷判定流程
经过上述不合格波形产生原因的分析,在缺陷判定时工艺人员首先应对不同品种、不同冶炼加工工艺路线、不同时期(季节)等钢材易出现缺陷有全面的了解,并按照“相控阵探伤发现不合格波形→便携A型脉冲反射式探伤仪定位取样→低倍检验→光学高倍检验→扫描电镜能谱分析”的判定流程进行分析。
对于以上典型不合格的相控阵探伤波形,可以根据经验制作特征波形与缺陷的对照,并据此培训相关技术人员和操作人员,这样可以快速和直观地对不合格钢材进行初步判定,有利于钢材的快速周转流动。技术质量工作者不能仅凭超声探伤不合格波形的经验一刀切地判废,也不能放任流动,而要健全不合格品种的缺陷判定流程,重视金相检验的判定功能并结合电镜能谱等进行综合分析。不合格典型波形特征与缺陷的对照,也需要进行大量的试验积累,在一定试验数据积累的基础上,才有可能实现不合格探伤波形与缺陷产生的原因快速对照。
4 结束语
(1) 通过对上述4种钢材典型不合格探伤波形产生原因的分析,发现不合格钢材在生产过程均存在一定异常或违规,如白点、夹杂、缩孔和过烧等缺陷的产生,这些异常处于现有检测手段之外且系统前期未对此类过程风险进行充分识别,造成最终探伤不合格。
(2) 要弄清钢材出现不合格波形的原因,不能只局限于对探伤波形的定性及探伤工艺参数等分析,进行钢材的低倍、金相组织等理化检验分析也是必不可少的。
(3) 进行探伤不合格试验分析时可参考缺陷判定文件,同时关注生产工艺执行情况,建立工艺参数可追溯性系统,建立全流程的不合格波形分析数据库。这对后续生产提供技术指导、有效地发挥相控阵超声波探伤检验的作用有很大帮助。
免责声明:本网站所转载的文字、图片与视频资料版权归原创作者所有,如果涉及侵权,请第一时间联系本网删除。
相关文章
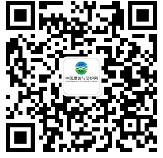
官方微信
《中国腐蚀与防护网电子期刊》征订启事
- 投稿联系:编辑部
- 电话:010-62316606-806
- 邮箱:fsfhzy666@163.com
- 中国腐蚀与防护网官方QQ群:140808414
点击排行
PPT新闻
“海洋金属”——钛合金在舰船的
点击数:7426
腐蚀与“海上丝绸之路”
点击数:5955