0 引言
镁合金具有质轻、导热性好、比强度高、机械性能优等特点,被誉为21 世纪最具发展潜力的金属材料[1],但是镁合金耐腐蚀性和耐磨性差限制了其的广泛应用。 人们通过表面改性的方法在镁合金及其工件表面构建防护涂层以提高镁合金的综合性能。 传统的镁合金表面处理技术包括表面改性技术、表面涂覆技术、复合表面工程技术。 目前,常见的镁合金表面涂层主要包括化学防腐涂层(制备方法包括:化学转化[2]、电镀/化学镀[3]、阳极氧化[4]、微弧氧化[5] 等)和物理防腐涂层( 制备方法包括: 有机/聚合物涂覆[6]、激光表面改性[7]、气相沉积[8]、表面渗层处理[9]等)。 在这些技术中,微弧氧化处理技术由于其生产率和经济效率高、绿色环保、膜层性能优异深受人们的青睐。
微弧氧化( Micro-oxidation,MAO) 又称等离子体电解氧化( Plasma electrolytic oxidation,PEO),由传统的阳极氧化发展而来,是依靠弧光放电瞬间产生高温高压,经过等离子体化学、电化学、热化学、扩散变化、高温相变等一系列反应,从而在Al、Ti、Mg、Nb、Zr、Ta等阀金属基体表面原位生长以基体为主的具有特殊结构和性能的陶瓷膜[10]。 微弧氧化过程受到合金成分、电解液[11] 和电参数[12] 等多种因素影响,而电解液是其中最主要的影响因素。 目前,微弧氧化电解液对微弧氧化过程的影响研究主要集中在电解液的种类和添加剂的选择两个方面。
采用微弧氧化在镁合金表面构建陶瓷防护膜的过程中,传统方法多采用水溶液体系,该体系中制备的膜层以氧化物特别是MgO相为主[13-15],但有相关研究表明,MgF2 膜层的耐腐蚀性和生物相容性要优于MgO膜层[16-17]。 目前,在镁合金表面制备MgF2 膜层的传统方法主要是在HF的水溶液中进行低温化学热处理,该方法耗时长且膜层厚度难以控制[17-18]。 近年来,有人在NH4HF2 熔融盐中采用微弧氧化方法制备了MgF2 膜层, 但其工艺过程需要较高的温度(150℃)且制备的膜层较薄[19]。 作者前期开展了常温环境下在NH4F-EG溶液中微弧氧化制备MgF2 膜的研究,获得了结构均匀、厚度较大的膜层[20]。 大量研究工作表明:在电解液中添加Al2O3[21]、 TiO2[22]、 ZrO2[23]、 SiO2[24]、SiC[25-27]等纳米颗粒可以改善微弧氧化膜层的性能。 纳米SiC具有耐高温、硬度高、耐磨性好等优点常作为增强相材料应用于微弧氧化处理[28-30]。 文中以NH4F-EG为基础电解液体系,选择纳米SiC颗粒作为微弧氧化法制备MgF2膜层的增强相改性材料,考察了不同浓度纳米SiC颗粒对MgF2 微弧氧化膜层微观结构、组成和耐腐蚀性能的影响。
1 试验与方法
1.1 膜层的制备
选用尺寸为25 mm×25 mm×5 mm的AZ31镁合金作为微弧氧化试验的基体材料,其化学组成(以质量分数计,%) 为Al 2.85,Zn 0.75,Mn0.62,Si 0.025,Mg余量。 微弧氧化制备MgF2 膜层的电解液为NH4F-EG(质量比为8 ∶100) 组成的混合液,在此体系中添加2.5、5 和7.5 g/L的SiC,探究不同浓度SiC对MgF2 膜的影响。
采用JHMAO200H型双极性脉冲电源对AZ31 镁合金进行微弧氧化处理,试样作为阳极,螺旋形不锈钢冷却管作为阴极,氧化槽中通过不断机械搅拌和通入冷却水使电解液温度恒定在20~40℃。 试验前,样品表面依次经过120、240、600、1000、3000 和5000 号砂纸打磨抛光至Ra≈0.25 μm,丙酮除油,蒸馏水冲洗,冷风吹干备用。
微弧氧化过程采用恒流法,电流密度 j +=6 A/dm2,j -=6 A/dm2,电源频率100 Hz,占空比20%,正负脉冲个数比1 ∶ 5, 氧化处理时间15 min,对正负电压的变化进行实时记录。 试验后,对样品进行清洗吹干。 样品分别记为空白组AZ31(Substrate)、不含SiC微弧氧化组(P-0)、含SiC微弧氧化组(P-2.5、P-5.0、P-7.5)。
1.2 膜层的结构测试及性能表征
使用透射电子显微镜( TEM, Tecnai G2TF20)观察纳米SiC颗粒的二维微观形貌。 使用激光动态散射仪(Nano ZS 3600)测定含SiC纳米颗粒的电解液的Zeta电位和粒径分布。 使用扫描电子扫描电镜(SEM,JSM-5600LV,JEOL)和配备的电子能谱仪(EDS,KEVER)测定微弧氧化膜的微观组织、元素成分及含量。
使用X射线衍射仪(XRD,Rigaku D/MAX-2400)分析微弧氧化膜的物相组成,测试所用的XRD参数如下: Cu靶, 管电流60 mA, 管电压40 mV, 掠射角3°, 步长0.02°, 扫描速率10°/min,2θ 范围为20°~80°。
使用数字型涡流测厚仪(MINITEST 1100)测量微弧氧化膜的厚度。 使用电化学工作站测定耐腐蚀性(Autolab PGSTAT302 N,Metrohm),测试温度为20~25℃,样品的暴露面积为1 cm2,3.5%的NaCl溶液为腐蚀介质,样品为工作电极,Pt片为对电极, 含有饱和KCl溶液的Ag/AgCl电极为参比电极。 在动电位极化曲线测试之前,试样先在溶液中测试30 min的开路电位至电位稳定,极化曲线测试范围(相对于开路电位)为-0.6~1.3 V,扫描速率为1 mV/s;阻抗谱测试过程中施加相对于开路电位10 mV的交流扰动信号,扫描频率范围0.01~105 Hz。
2 结果与讨论
2.1 SiC的粒径和Zeta电位
试验所使用的纳米SiC颗粒的粒径约为20~50 nm(图1( a))。 将纳米SiC颗粒分散到NH4F-EG电解液(5 g/L SiC)持续搅拌6 h后静置(图1(b)),结果发现:静置24 h后SiC的沉降效果不明显,这说明SiC在该电解液中能长期稳定分散,为后续SiC进入MgF2 膜层提供了条件。
图1 SiC纳米颗粒的微观形貌和SiC在电解液中(5 g/LSiC)的静置试验照片
使用激光动态散射仪对5 g/L SiC的电解液测试3 次,取平均值,获得粒径分布(图2( a) 和Zeta电位(图2(b))。 电解液中纳米SiC粒子的粒径分布为160 nm,Zeta电位为-24 mV,证明纳
图2 5 g/L SiC在电解液中的粒径分布和Zeta电位
米SiC颗粒在电解液中带负电且分散效果良好。在微弧氧化过程中,有利于向阳极迁移并吸附到阳极表面上,在机械搅拌[31] 和电泳沉积[32-33] 的作用下随火花放电沉积进入膜层。
2.2 SiC含量对MgF2 膜层电压-时间曲线的影响
图3 给出了AZ31 镁合金在不同SiC浓度的电解液中进行微弧氧化的电压-时间曲线图。 微弧氧化成膜过程是一个“成膜-击穿-熔化-烧结-再成膜”多次循环的过程[34]。 在微弧氧化初期(StageⅠ),电压随时间的延长呈线性增大的趋势,4 条曲线基本重合,说明在微弧氧化初期纳米SiC对电压基本没有影响,这是因为刚开始通电后,阳极表面没有电火花产生,首先在基体表面生成一层阳极钝化膜,为微弧氧化处理提供必要条件,试样表面电阻增大,电解液基本不与基体反应,故SiC对电压的影响动没有体现出来。
在微弧氧化中期(StageⅡ),电压随时间的延长缓慢增大,阳极表面局部击穿放电产生小火花,且随着SiC含量的增加,增长速率减小,造成这种现象的原因如下:① 纳米SiC分散在溶液中,其较高的表面能决定其具有较强的吸附能力,可以吸附电解质中的负离子形成带负电的胶粒,在机械搅拌和电泳沉积的作用下向阳极移动,吸附在电极表面,增加了传质电阻[35];② 纳米SiC吸附溶液中的带电粒子,降低带电粒子的移动性,导致电解液的电导率降低。 在微弧氧化后期(StageⅢ)电压随时间的延长增长非常缓慢,此时膜层达到了一定的厚度,初始时阳极表面产生均匀放电的弧光,膜层均匀生长,后期阳极表面的微弧数目随反应进行逐步减少,微弧跳动性减弱,火花放电分布不均匀,呈现局部聚集状态,整个膜层在相对薄弱区域生长,最终促进膜层表现为整体均匀性的增厚。此过程膜层生长缓慢,只需要稍高的电压来维持恒定的电流密度,所以电压增长缓慢。
图4 给出了SiC含量对溶液电导率、微弧氧化过程起弧电压、终止电压的影响。 相关研究表明,微弧氧化的起弧电压和电解液电导率有关[36],电解液的电导率越低则起弧电压越小,随着溶液中SiC含量的增加,溶液的电导率减小,故起弧电压降低,控制电压降低,终止电压降低。
图3 AZ31 镁合金在不同SiC浓度电解液中微弧氧化过程的电压-时间响应曲线
图4 SiC浓度对微弧氧化初始电压和终止电压的影响
2.3 SiC含量对MgF2 膜层结构与组成的影响
图5 给出了不同SiC含量下制备的MgF2 膜的表面形貌及元素组成。 因为掺入的SiC颗粒尺寸太小,很难通过SEM区分出膜层中的SiC纳米颗粒和周围陶瓷相, 根据试验结果可知(EDS),未添加SiC的膜层中无Si元素,随着SiC浓度的增加,膜层中的Si和C含量增加,表明微弧氧化过程中SiC顺利进入膜层内部[30, 37]。 由
图5 不同SiC浓度下所得MgF2 膜层的表面微观形貌和EDS元素组成
表面形貌图可知,由于微弧放电作用,膜层表面为密集分布的微孔结构。 随着溶液中SiC含量的增加,膜层微孔直径减小,微孔尺寸的减小与电压的减小密切相关,电压减小导致放电程度减缓,钝化膜击穿减弱,熔融物冷却减少,微孔尺寸减小。 由EDS分析可知,未添加SiC的MgF2 膜主要由Mg、F、Al、O元素组成,添加SiC的MgF2膜则由Mg、F、Al、O、Si、C元素组成。 随着电解液中SiC含量的增加,膜层中Si、C含量增加,表明纳米SiC颗粒在微弧放电过程中在机械搅拌和电泳沉积的作用下被熔融物包覆进入膜层,遇冷凝固成为陶瓷层的一部分,导致膜层的孔隙率减小,致密度增加。
图6 给出了不同SiC含量下制备MgF2 膜的截面形貌。 由截面形貌可知,未添加纳米SiC颗粒时,膜层内部存在大小不一的孔洞,随着电解液中SiC含量的增加,膜层致密度提高,厚度减小,这是由于纳米SiC颗粒随熔融物凝固被包覆进入膜层内部,膜层缺陷减少,使得孔隙率降低。
图6 不同SiC浓度下所得MgF2 膜层的截面微观形貌
图7 给出了P-5.0 样品内部元素分布情况。截面的主要元素分析说明SiC进入膜层内部且分布均匀。 纳米SiC颗粒内外分布均匀的原因可能如下:反应初期,带负电的纳米SiC胶粒被吸附在阳极表面;反应中期随熔融物包裹进入膜层;反应后期在机械搅拌的作用下沉积进入微孔
图7 P-5.0 试样截面形貌及主要元素分布
和附着于表面。 厚度减小可以归因于:惰性SiC的加入使微弧氧化过程的电压降低,减慢了反应过程,阻碍了膜层生长。
图8 给出了不同SiC含量下制备MgF2 膜层的X射线衍射图谱。 由图可知, 膜层主要由MgF2 组成,图谱中Mg相的存在主要是由于膜层结构疏松多孔且厚度较薄,X射线穿透膜层到达基体造成的。 随着SiC含量的增加,MgF2 的衍射峰增强,Mg的峰减弱,这是由于随着SiC含量的增加,膜层致密性增加导致的。 因SiC含量较少,故无对应特征峰。
为了进一步分析Mg-SiC复合膜层中Si元素和Mg元素的存在状态,我们对P-5.0 样品进行了XPS分析。 图9 给出了P-5.0 样品的Mg 1s和Si 2p的XPS精细谱。 谱图说明Mg元素在膜层中主要以MgF2 相[38] 存在,Si元素的Si 2p可以分解为100.0 eV的SiC峰[39] 和104.0 eV的
图8 不同SiC浓度下所得MgF2 膜层的XRD图谱
SiO2 峰[40],这表明在高温放电时,极少部分的SiC熔融并与电解液反应生成SiO2,SiC被氧化程度比较小,并不能通过XRD检测到SiO2 相。
图9 P-5.0 试样的Mg 1s和Si 2p的XPS精细谱
2.4 SiC含量对MgF2 膜层耐腐蚀性能的影响
图10 给出了不同SiC含量下制备的MgF2膜层在3.5%NaCl溶液中测得的动电位极化曲线。 通过外推法可以获得与腐蚀相关的参数:自腐蚀电位(E corr)、腐蚀电流密度( I corr)、阳极/阴极塔菲尔常数( b a 和 b c),表1 为相应的拟合结果,根据相关参数计算极化电阻(R p)。 自腐蚀电位反映了膜层发生腐蚀的热力学倾向和难易程度,腐蚀电流密度反映了膜层的实际腐蚀速率。 一般的,膜层的腐蚀电位越正,腐蚀电流密度越小,极化电阻越小说明膜层的耐腐蚀性能越好。
图10 不同SiC浓度下所得MgF2 膜层的动电位极化曲线
由图10 可知,相对于基体材料来说,膜层的腐蚀电位正移,腐蚀电流密度减小,涂层的阴极和阳极反应过程受到明显的抑制,腐蚀抗力增加。 点蚀电位反映了合金表面钝化膜被击穿的难易程度。 由图10 可知,所有膜层的极化曲线阳极分支均出现明显的钝化区和点蚀电位,这是由于膜层在电化学腐蚀过程中产生的腐蚀产物沉积在膜层表面,隔断了合金基体与溶液的接触,减缓了合金阳极的溶解速率,阻碍了腐蚀的进行。 反映了明显的点蚀击穿的特性。 随着SiC含量的增强,点蚀电位正移,膜层的点蚀特性得到了一定程度的改善,说明膜层SiC的增加有助于提高膜层的耐腐蚀性能。
综上可知,经过微弧氧化处理的样品耐腐蚀性能显著提高,且随着溶液中SiC含量的增加,膜层的耐腐蚀性先增加后减小。 由于膜层的耐腐蚀性取决于膜层的物相组成、厚度和致密度等因素,膜层越厚、孔隙率越小、膜耐蚀相越多,膜层耐蚀性越好。 由SEM图可知,随着电解液中SiC含量的增加,膜层中耐蚀相SiC含量增加,膜层厚度减小、致密度先增加后减小。 增强相SiC分散在膜层中阻碍了腐蚀性Cl- 的渗入[41],在5 g/L达到最佳的抗腐蚀性能,P-5 试样具有最好的耐腐蚀性。
表1 与动电位极化曲线相关的电化学参数
图11 给出了不同SiC含量下制备得MgF2膜层在3.5%NaCl溶液中测得的电化学阻抗谱和等效电路图。 由图11 可知,所有试样的Nyquist图由三段圆弧组成,即高频和中频段的容抗弧及低频段的感抗弧。 高频容抗弧反映了试样表面最初生成的钝化膜,与电荷的转移电阻相关;中频容抗弧反映了双电层的电荷转移,与腐蚀产物和试样表面的接触电阻相关[42];低频感抗弧与法拉第过程和镁合金的溶解相关[43-45]。 高频区的容抗弧孔径越大,说明膜层的阻抗越大;中频区的容抗弧孔径越大,说明生成的陶瓷膜耐腐蚀性越好[46]。
Nyquist图的弧半径大小反映了腐蚀电阻的大小,Bode图中| Z |f→0 的值用来评价样品的抗腐蚀性能[47]。 随着SiC含量的增加,容抗弧半径先变大后变小, | Z |f=0.01 Hz 值先增加后减小,膜层的耐性能先增大后减小。 利用ZSimpWin软件拟合等效电路图,得到相关的拟合参数(表2)。 因为陶瓷膜表面疏松多孔造成电流分布不均匀导致弥散效应的产生,采用常相位角元素代替双层电容。 拟合模型中,Rs 为溶液电阻,R1 为样品表面的腐蚀产物膜电阻,R2 为电荷转移电阻,CPE1-T、CPE2-T为常相位角元件,R3 为感抗电阻,L 为电感元件。 镁合金基体和P-0 样品的等效图相同(图10(d1)),P-2.5、P-5.0、P-7.5 样品的等效电路图相同(图10( d2)),等效电路图的差异表明其腐蚀机理的不同,这种差异和膜层中引入第二物相有关。
由表2 中拟合参数可知: 随着SiC含量的增加,R2 增大表明电荷转移阻碍增大,腐蚀过程越难以发生,结合SEM可以推断,纳米SiC颗粒增加了膜层的耐蚀相且使膜层孔隙率减小,电化学腐蚀过程中,电偶腐蚀位点数目减少,合金趋于发生均匀性腐蚀,腐蚀程度减轻。 R1 增大表明SiC的添加可以提高膜层的稳定性,提高合金耐蚀性。 电化学阻抗结果和动电位极化曲线结果一致表明P-5.0 试样具有最好的耐蚀性。
图11 不同SiC浓度下所得MgF2 膜层的电化学阻抗谱和等效电路图
表2 从电化学阻抗谱等效电路中获得的等效元器件参数
3 结论
(1) 在NH4F-EG电解液中添加纳米SiC颗粒,可以在AZ31 镁合金表面制备出含SiC的MgF2-SiC膜层。
(2)随着电解液中SiC浓度的增加,膜层变得致密平整,孔隙率和厚度均减小。
(3)极化曲线和阻抗测试表明,与MgF2 膜层相比,MgF2-SiC膜层的耐腐蚀性能显著提高。 随着溶液中纳米SiC含量的增加,MgF2-SiC膜层的耐腐蚀性先增大后减小,当溶液浓度为5 g/L时,膜层表现出最优的耐腐蚀性能。
参考文献
[1] GRAY J E,LUAN B L.Protective coatings on magnesium and its alloys-a critical review[J].Cheminform,2002,336(1):88-113.
[2] SHARMA A K.Chromate conversion coatings for magnesiumlithium alloys[J].Metal Finishing,1989,87(2):73.
[3] 王梅,刘建睿,沈淑娟,等.镁合金表面处理技术的发展现状[J].铸造技术,2006,27(3):295-298.
WANG M,LIU J R,SHEN S J,et al.Progress of magnesium alloy surface treatment technology[J].Casting Technology,2006,27(3):295-298(in Chinese).
[4] 张永君,严川伟,楼翰一,等.镁及镁合金阳极氧化技术进展[J].腐蚀科学与防护技术,2001,13(4):214-217.
ZHANG Y J,YAN C W,LOU H Y,et al.Progress on anodizing technology for magnesium and its alloys [J].Corrosion Science and Protection Techonlogy,2001,13(4):214-217.
[5] TIMOSHENKO A V,MAGUROVA Y V.Investigation of plasma electrolytic oxidation processes of magnesium alloy MA2-1 under pulse polarisation modes[J].Surface & Coatings Technology,2005,199(2):135-140.
[6] TRUONG V T,LAI P K,MOORE B T,et al.Corrosion protection of magnesium by electroactive polypyrrole/paint coatings [J].Synthetic Metals,2000,110(1):7-15.
[7] JUN Y,SUN G P,JIA S S.Characterization and wear resistance of laser surface melting AZ91D alloy[J].Journal of Alloys and Compounds,2008,455(1):142-147.
[8] YAMAUCHI N,DEMIZU K,UEDA N,et al.Friction and wear of DLC films on magnesium alloy[J].Surface & Coatings Technology,2005,193(1):277-282.
[9] SHIGEMATSU I,NAKAMURA M,SAITOU N,et al.Surface treatment of AZ91D magnesium alloy by aluminum diffusion coating[J].Journal of Materials Science Letters,2000,19(6):473-475.
[10] YEROKHIN A L,SNIZHKO L O,GUREVINA N L,et al.Discharge characterization in plasma electrolytic oxidation of aluminium [J].Journal of Physics D Applied Physics,2003,36(17):2110-2120.
[11] DUAN H,YAN C,WANG F.Effect of electrolyte additives on performance of plasma electrolytic oxidation films formed on magnesium alloy AZ91D [J].Electrochimica Acta,2007,52(11):3785-3793.
[12] JIANG Y,YU Z,XIA Q,et al.Structure and corrosion resistance of PEO ceramic coatings on AZ91D Mg alloy under three kinds of power modes [J].International Journal of Applied Ceramic Technology,2013,10(5):310-317.
[13] EZHILSELVI V,NITHIN J,BALARAJU J N,et al.The influence of current density on the morphology and corrosion properties of MAO coatings on AZ31B magnesium alloy[J].Surface & Coatings Technology,2016,288:221-229.
[14] CAI J S,CAO F H,CHANG L,et al.The preparation and corrosion behaviors of MAO coating on AZ91D with rare earth conversion precursor film [J].Applied Surface Science,2011,257(8):3804-3811.
[15] WILKE B M,ZHANG L,LI W P,et al.Corrosion performance of MAO coatings on AZ31 Mg alloy in simulated body fluid vs.Earle's balance salt solution[J].Applied Surface Science,2016,363:328-337.
[16] SUN W,ZHANG G D,TAN L L,et al.The fluoride coated AZ31B magnesium alloy improves corrosion resistance and stimulates bone formation in rabbit model[J].Materials Science & Engineering C Materials for Biological Applications,2016,63:506-511.
[17] CHIU K Y,WONG M H,CHENG F T,et al.Characterization and corrosion studies of fluoride conversion coating on degradable Mg implants[J].Surface & Coatings Technology,2007,202(3):590-598.
[18] CHEN X B,BIRBILIS N,ABBOTT T B.Review of corrosion-resistant conversion coatings for magnesium and its alloys [J].Corrosion Science Section,2011,67(3):0350051-03500516.
[19] JIANG H B,WU G S,LEE S B,et al.Achieving controllable degradation of a biomedical magnesium alloy by anodizing in molten ammonium bifluoride [J].Surface & Coatings Technology,2017,313:282-287.
[20] 梁军,齐玉明,彭振军.一种非水电解液体系中的微弧氧化方法:201811302684.5[P].2018-12-18.
LIANG J,QI Y M,PENG Z J.Micro-arc oxidation method in non-aqueous electrolyte system:201811302684.5 [ P ].2018-12-18.
[21] LI X J,LUAN B L.Discovery of Al2O3 particles incorporation mechanism in plasma electrolytic oxidation of AM60B magnesium alloy[J].Materials Letters,2012,86(12):88-91.
[22] LI H X,SONG R G,JI Z G.Effects of nano-additive TiO2 on performance of micro-arc oxidation coatings formed on 6063 aluminum alloy[J].Transactions of Nonferrous Metals Society of China,2013,23(2):406-411.
[23] ZHONG Y S,SHI L P,LI M W,et al.Characterization and thermal shock behavior of composite ceramic coating doped with ZrO2 particles on TC4 by micro-arc oxidation[J].Applied Surface Science,2014,311(9):158-163.
[24] LU X P,BLAWERT C,HUANG Y,et al.Plasma electrolytic oxidation coatings on Mg alloy with addition of SiO2 particles[J].Electrochimica Acta,2016,187:20-33.
[25] 常海,郭雪刚,文磊,等.SiC 纳米颗粒对TC4钛合金微弧氧化涂层组织结构及耐蚀性能的影响[J].材料工程,2019,47(3):109-115.
CHANG H,GUO X G,WEN L,et al.Effect of SiC nanoparticles on microstructure and corrosion resistance of microarc oxidation coating on TC4 titanium alloy [J].Materials Engineering,2019,47(3):109-115(in Chinese).
[26] 薛文斌.SiC 颗粒增强体对铝基复合材料微弧氧化膜生长的影响[J].金属学报,2006,42(4):350-354.
XUE W B.Effect of SiC particle reinforcement on the growth of micro-arc oxidation coating of aluminum matrix composites[J].Journal of Metals,2006,42(4):350-354(in Chinese).
[27] 杨斌,金莹,郭雪刚,等.SiC 纳米颗粒对TA2微弧氧化涂层组织结构及耐蚀性能的影响机制[J].稀有金属材料与工程,2018,47(12):3754-3760.
YANG B,JIN Y,GUO X G,et al.Effect of SiC nanoparticles on microstructure and corrosion resistance of micro-arc oxidation coating on TA2 titanium alloy[J].Rare Metal Materials and Engineering,2018,47(12):3754-3760(in Chinese).
[28] BUTYAGIN P I,KHOKHRYAKOV Y V,MAMAEV A I.Microplasma systems for creating coatings on aluminium alloys[J].Materials Letters,2003,57(11):1748-1751.
[29] WANG S Y,SI N C,XIA Y P,et al.Influence of nano-SiC on microstructure and property of MAO coating formed on AZ91D magnesium alloy [J].Transactions of Nonferrous Metals Society of China,2015,25(6):1926-1934.
[30] YU L,CAO J H,CHENG Y L.An improvement of the wear and corrosion resistances of AZ31 magnesium alloy by plasma electrolytic oxidation in a silicate-hexametaphosphate electrolyte with the suspension of SiC nanoparticles[J].Surface &Coatings Technology,2015,276:266-278.
[31] KIM Y H,LEE T G,LIM G Y.An experimental study on mechanical properties of fiber reinforced high performance concrete with high temperature[J].Materials & Structures,2013,46(4):607-620.
[32] SHIN K R,KO Y G,SHIN D H.Surface characteristics of ZrO2-containing oxide layer in titanium by plasma electrolytic oxidation in K4P2O7 electrolyte [J].Journal of Alloys & Compounds,2012,536(1):226-230.
[33] LEE K M,KO Y G,SHIN D H.Incorporation of carbon nanotubes into micro-coatings film formed on aluminum alloy via plasma electrolytic oxidation [J].Materials Letters,2011,65(14):2269-2273.
[34] KHASELEV O,WEISS D,YAHALOM J.Anodizing of pure magnesium in KOH-Aluminate Solution under sparking[J].Journal of the Electrochemical Society,1999,146(5):1757-1761.
[35] YANG S K,CAI W P,ZENG H B,et al.Ultrafine β-SiC quantum dots fabricated by laser ablation in reactive liquid at room temperature and their violet emission [J].Journal of Materials Chemistry,2009,19(38):7119-7123.
[36] IKONOPISOV S.Theory of electrical breakdown during formation of barrier anodic films [J].Electrochimica Acta,1977,22(10):1077-1082.
[37] ARRABAL R,MOHEDANO M,MATYKINA E,et al.Characterization and wear behaviour of PEO coatings on 6082-T6 aluminium alloy with incorporated α-Al2O3 particles[J].Surface & Coatings Technology,2015,269(1):64-73.
[38] WOJCIECHOWSKA M,HABER J,?OMNICKI S,et al.Structure and catalytic activity of double oxide system:CuCr-O supported on MgF2 [J].Journal of Molecular Catalysis A:Chemical,1999,141(1):155-170.
[39] WANG Y Q,WANG X J,GONG W X,et al.Effect of SiC particles on microarc oxidation process of magnesium matrix composites[J].Applied Surface Science,2013,283:906-913.
[40] FUKUDA H,MATSUMOTO Y.Formation of Ti-Si composite oxide films on Mg-Al-Zn alloy by electrophoretic deposition and anodization[J].Electrochimica Acta,2005,50(27):5329-5333.
[41] PING W,TING W,HAO P,et al.Effect of NaAlO2 concentrations on the properties of micro-arc oxidation coatings on pure titanium[J].Materials Letters,2016,170:171-174.
[42] HA H Y,KANG J Y,KIM S G,et al.Influences of metallurgical factors on the corrosion behaviour of extruded binary Mg-Sn alloys[J].Corrosion Science,2014,82:369-379.
[43] WANG W D,HAN J J,YANG X,et al.Novel biocompatible magnesium alloys design with nutrient alloying elements Si,Ca and Sr:Structure and properties characterization[J].Materials Science and Engineering:B,2016,214:26-36.
[44] BARIL G,PEBERE N.The corrosion of pure magnesium in aerated and deaerated sodium sulphate solutions[J].Corrosion Science,2001,43(3):471-484.
[45] WEN Z H,WU C J,DAI C S,et al.Corrosion behaviors of Mg and its alloys with different Al contents in a modified simulated body fluid [J].Journal of Alloys & Compounds,2009,488(1):392-399.
[46] SHI Z,SONG G L,ATRENS A.Corrosion resistance of anodised single-phase Mg alloys[J].Surface & Coatings Technology,2006,201(1):492-503.
[47] NISHIKATA A,YAMASHITA Y,KATAYAMA H,et al.An electrochemical impedance study on atmospheric corrosion of steels in a cyclic wet-dry condition [J].Corrosion Science,1995,37(12):2059-2069.
免责声明:本网站所转载的文字、图片与视频资料版权归原创作者所有,如果涉及侵权,请第一时间联系本网删除。
-
标签: 微弧氧化, 纳米 SiC MgF2 膜层, AZ31 镁合金, 耐腐蚀性能
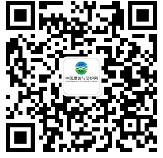
官方微信
《中国腐蚀与防护网电子期刊》征订启事
- 投稿联系:编辑部
- 电话:010-62316606-806
- 邮箱:fsfhzy666@163.com
- 中国腐蚀与防护网官方QQ群:140808414