摘要
利用OLI Analyzer Studio软件,模拟海底管线管内NACE A和管外3.5%NaCl腐蚀环境,计算合金元素添加量对X70海底管线钢腐蚀速率的影响规律。在保证X70海底管线钢力学性能前提下,设计成分并轧制含0.003%Mg和无Mg的X70MOS实验钢。运用电化学测试技术和NACE TM 0284-2016标准,研究和评估X70MOS实验钢和常规X70海底管线钢的耐蚀性能和抗HIC性能。结果表明,Mg处理钢在NACE A溶液中较无Mg处理钢、X70海底管线钢腐蚀速率分别降低14.3%和73.3%,在3.5%NaCl溶液中分别降低52.8%和80.4%。Mg处理钢HIC敏感性较无Mg处理钢、X70海底管线钢大大降低,满足NACE标准规定值。X70MOS钢研制中使用0.003% Mg处理不仅可以降低合金成本,而且具有提高耐蚀性和抗HIC性能作用。
关键词: X70MOS钢 ; Mg处理 ; 成分设计 ; 耐蚀性能
随着海洋油气田不断深入开发,输送的石油和天然气中多含有H2S等酸性气体,这种湿H2S环境会导致海底管线钢发生氢致开裂 (HIC) 和硫化物应力开裂 (SSCC) 破坏[1-3]。为此,人们开发了抗酸管线钢用于含有H2S等酸性气体的油气输送。现今,抗酸性海底管线钢大规模应用的最高强度级别为X65钢级,为满足我国海洋油气田的深海、长距离、高压、大流量、抗酸性油气输送要求,开发X70级抗酸性海底管线钢 (X70MOS) 具有重要意义。
海底管线钢在管内湿H2S环境中和管外海洋环境中均遭受着化学和电化学腐蚀导致的管壁减薄,另外在管内湿H2S环境中还遭受严重的H2S腐蚀[4,5]。研究表明[6,7],海底管线钢的耐蚀性与合金元素及夹杂物密切相关,在规定含量范围内提高Cu、Cr、Ni、Mo等合金元素含量均有助于提高钢的耐蚀性。由于耐蚀合金的价格普遍较高,特别是Ni、Mo等贵金属的加入,使海底管线钢生产成本大幅增加。钢中夹杂物一方面是均匀腐蚀的起点,其尺寸、数量、分布均与海底管线钢耐均匀腐蚀性能相关[8];另一方面是强的氢陷阱,夹杂物尺寸越大、数量越多,对氢的捕获效率越高,HIC敏感性越高[9,10]。研究表明[11-13],Mg处理能够迅速生成氧化镁而降低钢中氧含量,钢液中大量细小的氧化镁颗粒将成为后续析出的其它夹杂物的形核质点,相应地在钢中获得更多更细小的夹杂物。我们课题组前期研究[14]也表明,Mg处理可以通过细化夹杂物而大大改善钢的抗HIC性能。然而,目前大量研究主要关注Mg处理对管线钢夹杂物的变质效果,而在Mg处理对海底管线钢管内、管外耐蚀性能及抗HIC性能影响方面的研究较少见到相关报道。
本文利用OLI Analyzer Studio软件模拟管线钢管内NACE A和管外3.5%NaCl服役环境,计算合金元素添加量对X70海底管线钢均匀腐蚀速率的影响规律。在保证X70海底管线钢力学性能前提下,考虑成本因素设计及轧制Mg处理的低合金含量实验钢以及无Mg处理的高合金含量实验钢。运用电化学测试技术和NACE TM 0284-2016标准实验,研究其耐蚀性能和抗HIC性能,并与常规X70海底管线钢进行对比分析,以期为X70MOS钢开发提供理论依据和数据支持。
1 实验方法
采用OLI Analyzer Studio软件开展管线钢管内和管外腐蚀速率模拟计算,以X70海底管线钢为研究对象,腐蚀介质为NACE A (5%NaCl+0.5% CH3COOH) 和3.5% (质量分数) NaCl,温度为25 ℃。将模拟计算条件输入模拟计算软件,即可建管内、管外腐蚀体系模型。令腐蚀体系模型的其它因素不变,只改变单一合金元素含量,计算Cu、Cr、Ni、Mo等合金元素添加量对X70海底管线钢腐蚀速率影响规律。
按设计成分冶炼实验钢,经中频真空感应炉冶炼后铸锭。将铸锭加热至1150 ℃,采用相同的热机械控制轧制工艺 (TMCP) 和快速冷却工艺,经过7道次轧制成12 mm厚钢板,获得X70MOS钢。
电化学测试分别在NACE A和3.5%NaCl溶液中进行,试样表面用1000#砂纸打磨。无水乙醇清洗脱脂,测试面积为1 cm2。三电极体系,饱和甘汞为参比电极 (SCE)、铂电极为辅助电极。电化学测试系统由Solartron 1280Z电化学工作站及SAI测试软件组成,如图1所示。
图1 电化学测试系统
实验开始后先进行30 min开路电位 (OCP) 测量,然后进行电化学阻抗谱 (EIS) 测试。电化学阻抗谱交流幅值5 mV,频率范围为1.04~10-1 Hz。最后进行动电位极化曲线测量,测试初始电位设为-0.2 V (vs OCP),终止电位设为0.5 V (vs OCP),扫描速率设为0.5 mV/s。电化学测试后,使用SAI软件对获得的极化曲线Tafel活性区以及EIS曲线进行拟合。
HIC敏感性测试按照NACE TM 0284-2016标准的规定进行,试样尺寸为100 mm×20 mm×12 mm,如图2所示。试样表面用1000#砂纸打磨,无水乙醇清洗脱脂。实验溶液为NACE A溶液 (5%NaCl+0.5%CH3COOH),溶液初始pH为2.62。恒温水槽控制溶液温度为25 ℃。实验时先通入氮气1 h除氧,通入H2S气体达到饱和,此时pH为2.75。试验周期为96 h,周期内保持通入容器中的H2S气体正压,实验结束后测得溶液pH为3.31。
图2 试样尺寸 (mm) 及观察截面示意图
试样取出后四等份切割,观察3个截面,如图2所示。对截面进行金相磨抛,在金相显微镜下检查截面出现的裂纹长度及宽度,在距离外表面1 mm以内的裂纹不做统计,然后按下式计算裂纹长度率 (CLR)、裂纹宽度率 (CTR) 和裂纹敏感率 (CSR):
式中,a为裂纹长度,mm;b为裂纹厚度,mm;W为试样宽度,mm;T为试样厚度,mm。
用Olympus-GX71光学显微镜观察金相组织和夹杂物,金相组织观察前使用5% (体积分数) 硝酸酒精腐蚀磨抛好的样品。用Quanta 400扫描电子显微镜 (SEM) 观察磨抛好的样品夹杂物,并统计60个2000倍视场下夹杂物的尺寸和数量。HIC试验后使用SEM观察HIC裂纹扩展情况,使用Oxford能谱仪 (EDS) 分析夹杂物成分。
2 实验结果
2.1 腐蚀模拟计算结果
合金元素添加量与X70海底管线钢腐蚀速率关系曲线如图3所示。从图中可见,在NACE A溶液中,X70海底管线钢腐蚀速率随着Cr、Ni含量的增加而快速下降后趋缓,但是随着Cu、Mo含量的增加而呈缓慢下降趋势,这表明在NACE A溶液中,Cu、Mo添加量对X70海底管线钢耐蚀性影响较小。在3.5%NaCl溶液中,X70海底管线钢腐蚀速率随着Cu、Cr、Ni、Mo含量的增加而快速下降后趋缓。在相同的合金含量下,X70海底管线钢在NACE A溶液中的腐蚀速率远高于在3.5%NaCl溶液中的,这表明海底管线在管内的均匀腐蚀较管外的严重。
图3 合金元素添加量与X70海底管线钢腐蚀速率关系曲线
2.2 实验钢成分设计及制备
根据模拟计算结果可知,添加Cu、Cr、Ni、Mo等合金元素有利于提高X70海底管线钢在管内、外服役环境中的耐均匀腐蚀性能,但是Cu、Mo对管内服役环境中耐均匀腐蚀性能影响较小。由于Cu增加一方面会增加管线钢组织偏析风险,提高其管内环境HIC敏感性;另一方面Cu会引起钢的热脆。因此,考虑生产成本因素,设计无Cu,低Cr、Ni、Mo,0.003%Mg的实验钢,编号为1#试样,设计添加Cu、Cr、Ni、Mo,无Mg处理的实验钢,编号为2#试样,并采用宝武集团武钢有限公司生产的X70海底管线钢作为对比钢,编号为3#试样。3种钢的主要化学成分如表1所示。3种钢力学性能均满足API 5L标准对X70级别海底管线钢的要求,如表2所示。
表1 3种钢主要化学成分
表2 3种钢力学性能
2.3 显微组织观察与夹杂物分析
3种钢金相组织照片如图4a~c所示。1#、2#试样组织均为贝氏体组织,晶粒度分别为12级和15级。3#试样为铁素体+珠光体组织,晶粒度11级。相比于1#试样,添加较高合金元素的2#试样晶粒更加细小。而对比钢3#试样Mn含量较高且合金含量较低,晶粒较粗大。
图4 3种钢金相组织及钢夹杂照片
图4d~f给出了3种钢非金属夹杂物宏观照片。1#试样夹杂物评级为细系D0.5,2#试样夹杂物评级为粗系D1.5和细系D1,3#试样夹杂物评级为细系D1。图5为3种钢夹杂物类型、数量、尺寸分布统计图。从结果看出,相比无Mg处理的2#、3#试样,1#试样夹杂物细小呈弥散分布,表明Mg处理具有细化、分散夹杂物作用。
图5 3种钢夹杂物类型、数量、尺寸统计
2.4 3种钢均匀腐蚀速率
3种钢在不同腐蚀介质中动电位极化曲线如图6所示。可以看出,在NACE A和3.5%NaCl溶液中3种钢阳极均为金属活性溶解过程,而在NACE A溶液中3种钢阴极为氢去极化过程,在3.5%NaCl溶液中阴极为氧去极化过程。对极化曲线Tafel活性区进行拟合,并利用Faraday定律将腐蚀电流密度转换为以深度指标表示的腐蚀速率,转换公式如下:
图6 3种钢在不同腐蚀介质中动电位极化曲线
式中,v为腐蚀速率,mm/a;M为金属的克原子量,g;n为金属的原子价;ρ为金属的密度,g/cm2;Icorr为腐蚀电流密度,μA/cm3。
获得极化曲线Tafel活性区拟合参数及计算得腐蚀速率如表3所示。从表3可知,两种溶液中3种钢的自腐蚀电位依次降低,腐蚀电流密度和腐蚀速率依次增大。在NACE A溶液中3种钢的腐蚀速率分别为0.772、0.901和2.890 mm/a,1#试样较2#、3#试样腐蚀速率分别降低14.3%、73.3%。在3.5%NaCl溶液中3种钢的腐蚀速率分别为0.094、0.199 和0.480 mm/a,1#试样较2#、3#试样腐蚀速率分别降低52.8%、80.4%。
表3 极化曲线Tafel活性区拟合参数及计算得腐蚀速率
3种钢在不同腐蚀介质中的Nyquist曲线如图7所示。从图中可以看出,在NACE A和3.5%NaCl溶液中3种钢Nyquist曲线高频区为容抗弧,低频区为感抗弧。高频容抗弧表明电极表面存在一定覆盖度的腐蚀产物膜,低频感抗弧表明离子在电极表面的吸附及点蚀形核。1#、2#、3#试样容抗弧半径表现为依次减小,表明电极表面的腐蚀程度依次加剧,这与极化曲线的分析结果是一致的。
图7 3种钢在不同腐蚀介质中的Nyquist曲线及拟合电路
为了进一步探索3种钢的耐蚀性差异原因,利用等效电路Rs(QRp(LRL)) 对图7中Nyquist曲线数据进行拟合,拟合电路如图7c所示。其Rs为溶液电阻,Q为常相位角元件 (界面电容),Rp为电极表面极化电阻,L为吸附产生的感抗,RL为吸附层电阻。拟合参数如表4所示。从结果可以看出,1#、2#、3#试样在NACE A和3.5%NaCl溶液中电极表面的极化电阻Rp依次减小,电极表面与溶液间的界面电容Q依次增大,阻抗值依次减小。EIS测得Rp依次减小、界面电容Q依次增大与极化曲线测得腐蚀电流密度依次增大相对应,表明1#、2#、3#试样耐蚀性依次降低。
表4 3种钢的Nyquist曲线拟合参数
2.5 3种钢试样HIC敏感性
HIC试样宏观表面形貌如图8所示。虽然3种钢试样放大100倍未观察到内部裂纹,CLR、CTR和CSR均为0,但在2#、3#试样表面观察到大量氢鼓泡,表明除1#试样外,2#、3#试样HIC敏感性较高。
图8 HIC试样宏观表面形貌
为进一步确认引起氢鼓泡的原因,利用SEM观察氢鼓泡截面形貌,如图9所示。从图中可以看出,氢鼓泡下存在多条裂纹,越靠近试样表面,裂纹开裂幅度越大。EDS能谱分析结果表明裂纹内部夹杂物主要成分均为Al2O3。这表明氢鼓泡和裂纹的产生与Al2O3夹杂物密切相关,这在后面会详细讨论。
图9 氢鼓泡下截面形貌图及能谱图
3 分析与讨论
Mg具有很强的脱氧能力,能够迅速形成临界形核半径较小的MgO。根据非均匀形核机理,钢液中大量细小的MgO颗粒成为夹杂物的形核质点,从而在钢中形成大量细小且弥散分布的复合夹杂物[11-13]。钢中非金属夹杂物是腐蚀的主要诱发源,非金属夹杂物与钢基体界面处铁原子的排列紊杂,处于高能状态,热力学稳定性较差,易发生溶解破坏[15]。而且非金属夹杂物与钢基体电位差较大,构成腐蚀原电池,非金属夹杂物作为活性阴极,其面积越大,腐蚀越容易发生[8]。细小的非金属夹杂物与钢基体的界面较小,且作为活性阴极的面积较小,有利于提高钢的耐蚀性。本研究中Mg处理1#试样中均为复合夹杂物,呈细小弥散分布,而无Mg处理的2#、3#试样中夹杂物尺寸、级别较高 (图7)。测得其在管内和管外服役环境中极化电阻较高和界面电容较小,腐蚀速率较小。因此,0.003%Mg处理钢较无Mg处理钢和X70海底管线钢耐均匀腐蚀性能高。
另外,由氢压理论[9]可知,氢在钢中的扩散过程主要受钢中氢陷阱的影响,钢中的非金属夹杂物是不可逆氢陷阱,能够吸附大量的氢原子。而夹杂物呈细小弥散分布可以分散氢压,从而改善钢的抗HIC性能[9,16]。在本研究中,未使用Mg处理的2#、3#试样,夹杂物级别较高 (图4d~f和5),出现了氢鼓泡 (图8),且氢鼓泡与钢中大颗粒Al2O3有关 (图9)。而经Mg处理后的1#试样,夹杂物呈细小弥散分布,未出现氢鼓泡。这表明Mg处理是通过改善管线钢中夹杂物尺寸、分布进而减少钢中氢的聚集,降低HIC敏感性。
综上所述,Mg处理改善了钢中夹杂物尺寸、分布,在降低合金元素的添加量同时提高了钢的耐均匀腐蚀和抗HIC性能。因此,在X70MOS钢研制中使用0.03%Mg处理不仅可以降低合金成本,而且具有提高耐蚀性作用。
4 结论
(1) Mg处理钢在NACE A溶液中较无Mg处理钢、X70海底管线钢腐蚀速率分别降低14.3%、73.3%,在3.5%NaCl溶液中分别降低52.8%、80.4%。
(2) Mg处理钢CLR、CTR和CSR均为0,且无氢鼓泡,HIC敏感性较无Mg处理钢、X70海底管线钢低。
(3) Mg处理钢中夹杂物呈细小弥散分布,提高了钢在管内和管外服役环境中的极化电阻,降低了界面电容,并且减少了钢中氢的聚集,分散了氢压,使其具有较高的耐蚀性和抗HIC性能。
参考文献
1 Gan L J, Huang F, Zhao X Y, et al. Hydrogen trapping and hydrogen induced cracking of welded X100 pipeline steel in H2S environments [J]. Int. J. Hydrogen Energy, 2018, 43: 2293
2 Huang F, Liu J, Deng Z J, et al. Effect of microstructure and inclusions on hydrogen induced cracking susceptibility and hydrogen trapping efficiency of X120 pipeline steel [J]. Mater. Sci. Eng., 2010, 527A: 6997
3 Peng Z X, Liu J, Huang F, et al. Effect of submicron-scale MnS inclusions on hydrogen trapping and HIC susceptibility of X70 pipeline steels [J]. Steel Res. Int., 2018, 89: 1700566
4 Wei W R, Liang Y, Hou J, et al. Localization of steel pipe used for natural gas transportation in south china sea [J]. Welded Pipe Tube, 2015, 38(3): 24
4 魏伟荣, 梁羽, 侯静等. 南海深水天然气输送海底管线钢管的国产化 [J]. 焊管, 2015, 38(3): 24
5 Wu W, Liu Z Y, Li X G, et al. Electrochemical characteristic and stress corrosion behavior of API X70 high-strength pipeline steel under a simulated disbonded coating in an artificial seawater environment [J]. J. Electroanal. Chem., 2019, 845: 92
6 Zafar M N, Rihan R, Al-Hadhrami L. Evaluation of the corrosion resistance of SA-543 and X65 steels in emulsions containing H2S and CO2 using a novel emulsion flow loop [J]. Corros. Sci., 2015, 94: 275
7 Wu H B, Liu Y T, Wang L D, et al. Influence of Cr Content on microstructures and acid corrosion properties of X120 grade pipeline steel [J]. J. Mater. Eng., 2013, (9): 32
7 武会宾, 刘跃庭, 王立东等. Cr含量对X120级管线钢组织及耐酸性腐蚀性能的影响 [J]. 材料工程, 2013, (9): 32
8 Zhang C Y, Chen X Q, Chen D B, et al. Research of pitting susceptibility in low carbon steels and mechanism of pitting initiation [J]. J. Chin. Soc. Corros. Prot., 2001, 21: 265
8 张春亚, 陈学群, 陈德斌等. 不同低碳钢的点蚀诱发敏感性及诱发机理研究 [J]. 中国腐蚀与防护学报, 2001, 21: 265
9 Qu Y M, Huang F, Liu J, et al. Influence of microstructure on hydrogen induced cracks susceptibility and hydrogen trapping efficiency for X80 pipeline steel [J]. Chin. J. Mater. Res., 2010, 24: 508
9 曲炎淼, 黄峰, 刘静等. 显微组织对X80钢氢致裂纹敏感性和氢捕获效率的影响 [J]. 材料研究学报, 2010, 24: 508
10 Findley K O, O’Brien M K, Nako H. Critical assessment 17: mechanisms of hydrogen induced cracking in pipeline steels [J]. Mater. Sci. Technol, 2015, 31: 1673
11 Wang R Z, Yang J, Zhu K, et al. Comparison between the results of oxide metallurgy with Ca deoxidation and Mg deoxidation [J]. Steelmaking, 2016, 32(3): 50
11 王睿之, 杨健, 祝凯等. 钙脱氧和镁脱氧的氧化物冶金工艺效果对比 [J]. 炼钢, 2016, 32(3): 50
12 Kimura S, Nakajima K, Mizoguchi S. Behavior of alumina-magnesia complex inclusions and magnesia inclusions on the surface of molten low-carbon steels [J]. Metall. Mater. Trans., 2001, 32B: 79
13 Yang J, Yamasaki T, Kuwabara M. Behavior of inclusions in deoxidation process of molten steel with in situ produced Mg vapor [J]. ISIJ Int., 2007, 47: 699
14 Peng Z X, Liu J, Huang F, et al. Comparative study of non-metallic inclusions on the critical size for HIC initiation and its influence on hydrogen trapping [J]. Int. J. Hydrogen Energy, 2020, 45: 12616
15 Wang L W, Xin J C, Chen L J, et al. Influence of inclusions on initiation of pitting corrosion and stress corrosion cracking of X70 steel in near-neutral pH environment [J]. Corros. Sci., 2019, 147: 108
16 Huang F, Li X G, Liu J, et al. Hydrogen-induced cracking susceptibility and hydrogen trapping efficiency of different microstructure X80 pipeline steel [J]. J. Mater. Sci., 2011, 46: 715
免责声明:本网站所转载的文字、图片与视频资料版权归原创作者所有,如果涉及侵权,请第一时间联系本网删除。
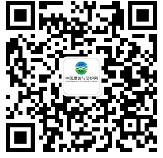
官方微信
《中国腐蚀与防护网电子期刊》征订启事
- 投稿联系:编辑部
- 电话:010-62316606-806
- 邮箱:fsfhzy666@163.com
- 中国腐蚀与防护网官方QQ群:140808414