摘要
通过固溶处理得到含有不同占比和元素含量组成相的2002双相不锈钢试样,采用恒电位极化、动电位扫描和表面形貌分析,研究并探讨了组织配分对点蚀萌生及扩展规律及机理的影响。结果表明,随着固溶温度升高,主要合金元素向γ相聚集,α相含量增加,但耐蚀性下降,点蚀更倾向于在弱相α相上萌生,2002双相不锈钢整体点蚀抗性降低。点蚀发生时具有蕾丝花边形貌,蕾丝盖下的点蚀坑具有浅而宽的碟形特征。2002双相不锈钢点蚀抗性越好,点蚀坑越容易沿宽度方向扩展,对深度方向的扩展影响不大。
关键词: 双相不锈钢 ; 组织配分 ; 点蚀萌生 ; 点蚀扩展
双相不锈钢具有优异的力学性能和耐腐蚀性能,在石油、化工、天然气和海洋工程等众多领域得到了广泛的应用[1-3]。点蚀是双相不锈钢在高腐蚀性环境服役过程中主要的腐蚀失效形式之一。双相不锈钢由铁素体和奥氏体组成,两个组成相的占比和耐蚀性等会对点蚀的萌生和发展产生影响。研究[4]表明,2205双相不锈钢随着固溶处理温度的提高,铁素体相的比例上升,奥氏体相的比例下降,耐腐蚀性能较好的固溶处理温度区间为1050~1075 ℃。韩冬[5]在固溶处理对2304双相不锈钢两相的耐蚀性能影响时研究表明,固溶温度在1050 ℃以下时试样整体耐点蚀性能被弱相奥氏体相所限制,在1050 ℃以上时被弱相铁素体相所限制。可见,热处理通过改变双相不锈钢中铁素体和奥氏体相的占比和耐蚀性对整体点蚀抗性产生影响。
经济型双相不锈钢是双相不锈钢未来发展的趋势之一[6]。与普通双相不锈钢类似,热处理对经济型双相不锈钢的耐点蚀性能同样影响显著。张丽华[7]对2101双相不锈钢两相耐蚀性能的研究表明,在1000~1300 ℃的固溶温度范围内,试样耐点蚀性能被弱相铁素体相所限制,结合对1000 ℃下两相比例相差较大的考虑,选定1050 ℃为最佳固溶处理温度。Guo等[8]研究了不同冷却速率对2002双相不锈钢模拟热影响区组织演变和耐点蚀性能的影响,在800~1350 ℃范围内,随着冷却速率从100 ℃/s降低到10 ℃/s,CPT和点蚀电位随之提升,即点蚀抗性增大。
目前,对于经济型双相不锈钢中组成相影响点蚀的研究多关注于组织配分后的整体点蚀抗性,如点蚀电位、临界点蚀温度等的变化规律,或者是夹杂物、析出相等第二相引发点蚀萌生的机制。而关于组成相对点蚀萌生及扩展规律和机制的影响的研究较少。因此,本文通过固溶处理得到含有不同占比和元素含量的组成相的2002双相不锈钢试样,采用恒电位极化、动电位扫描和表面形貌分析,研究并探讨了组织配分对点蚀萌生及扩展规律及机理的影响,有助于深入了解经济型双相不锈钢的点蚀萌生及扩展机制,对经济型双相不锈钢的开发及应用提供基础数据支持。
1 实验方法
实验材料为宝武集团提供的2002双相不锈钢热轧板,其化学成分 (质量分数,%) 为:C 0.019,Si 0.48,Mn 4.52,P 0.024,S 0.009,Cu 0.19,Cr 20.21,Mo 0.01,Ni 2.04,Fe余量。3种试样分别为2002双相不锈钢的原始热轧试样 (1#试样) 和分别在1100 ℃ (2#试样) 及1200 ℃ (3#试样) 固溶处理30 min后水淬试样。
试样经线切割成?11.3的圆片状,在样品的非工作面焊接铜导线,并用环氧树脂进行冷镶封装,留出1 cm2的工作面。用180~2000#砂纸进行研磨,再用2.5 μm金刚石研磨膏抛光至镜面,然后置于酒精溶液中进行超声波振荡清洗、冷风吹干。
电化学实验通过CS310电化学工作站进行测试,三电极系统,其中2002双相不锈钢作为工作电极,Pt片作对电极,饱和甘汞电极 (SCE) 用作参比电极。实验中溶液温度由水浴锅控制在 (30±1) ℃。
点蚀电位测定根据GB/T 17899-1999进行。在3.5% (质量分数) NaCl溶液中通入高纯N2 30 min除去溶解氧,随后将工作电极在NaCl溶液中稳定30 min后进行阳极扫描,极化范围为-0.5~+1.5 V (若无特别说明,文中电位均相对于SCE),扫描速率0.33 mV/s,当电流密度达到100 μA/cm2时所对应的电位为点蚀电位Epit。
恒电位极化实验时,将工作电极在-0.9 V电位下极化3 min以除去电极表面的钝化膜,再在NaCl溶液中稳定30 min后进行恒电位极化实验。对于点蚀密度统计实验,极化参数设定为0.8 V下极化15 s,以产生尺寸较小、数量较多的点蚀坑。对于点蚀微观形貌观察实验,极化参数设定为1 V下极化5 s,以产生尺寸较大而数量较少的点蚀坑。
利用超景深三维显微系统 (VHX-5000) 对腐刻 (30%NaOH溶液,3 V恒电位极化3 s) 后的2002双相不锈钢试样的金相组织进行观察,对恒电位极化后的2002双相不锈钢中点蚀坑的密度和尺寸进行统计分析,采用统计软件Image-Pro-Plus6.0对铁素体和奥氏体两相比例进行统计。利用扫描电镜 (FEI Nova 400 Nano,SEM) 能谱分析附件 (EDS) 对2002双相不锈钢中铁素体和奥氏体中合金元素含量进行分析。
2 实验结果
2.1 金相组织观察和元素分布
图1为2002双相不锈钢的原始热轧试样 (1#试样) 和分别在1100 ℃ (2#试样) 及1200 ℃ (3#试样) 固溶处理30 min后水淬试样的金相组织图。2002双相不锈钢由铁素体 (α相) 和奥氏体 (γ相) 两相组成,随着固溶温度的提高,α相含量逐渐增加,γ相含量逐渐减少。
图1 3种2002双相不锈钢试样金相组织
表1为3种2002双相不锈钢试样α和γ两相占比和主要元素分布。可以看到,相较于1#原始试样,经过固溶处理后的2#和3#试样,α相占比从53.3%上升至57.4%和68.4%,而γ相占比从46.7%下降至42.6%和31.6%。同时,α相中Cr和Mo含量下降,而γ相中Cr、Mo和N含量则上升。
表1 3种2002双相不锈钢试样α和γ两相占比和主要元素分布
2.2 点蚀电位测试
图2为3种2002双相不锈钢试样阳极极化曲线。可以看到,1#试样点蚀电位最高,为0.317 V。固溶处理后的2#和3#试样点蚀电位下降至0.283和-0.028 V。从-0.15到0.1 V极化电位区间的局部放大图 (图2b) 中看到,1#和2#试样的极化电流较为稳定,可以观察到明显的亚稳态点蚀电流峰。1#试样的极化电流基本稳定在1 μA/cm2,而2#试样的极化电流则呈现缓慢增长的趋势。3#试样尽管也存在电流的上升与回复过程,但由于极化电流上升非常显著,使得电流峰不太明显。
图2 3种2002双相不锈钢试样阳极极化曲线
2.3 点蚀密度统计
图3为3种2002双相不锈钢试样恒电位极化后的点蚀密度统计结果。可以看到,1#试样中α和γ两相上的点蚀密度分别为12.33和8.87个/mm2。固溶处理后,2#和3#试样中α相上的点蚀密度上升至14.68和19.21个/mm2,而γ相上的点蚀密度则下降至6.79和4.97个/mm2。
图3 2002双相不锈钢试样恒电位极化后的点蚀形貌和点蚀密度
2.4 点蚀尺寸统计
图4为3种2002双相不锈钢试样恒电位极化后的点蚀尺寸统计结果。可以看到,1#试样点蚀坑平均直径为46.52 μm,固溶处理后的2#和3#试样点蚀坑平均直径则逐渐下降至40.13和36.04 μm,3种试样的平均点蚀深度差别不大,均为10 μm左右,而点蚀坑的深径比分别为0.22、0.24和0.28。
图4 2002双相不锈钢试样恒电位极化后的点蚀形貌和三维尺寸
3 讨论
3.1 组织配分对2002双相不锈钢点蚀萌生的影响
根据表1和图3的实验结果可知,2002双相不锈钢经过固溶处理后组织发生配分,产生两个明显变化:一是相较于原始的1#试样,2#和3#试样中α相占比增大,γ相占比减小;二是α相中的Cr和Mo含量 (质量分数) 减少,N含量保持不变 (在α相中饱和),γ相中Cr、Mo和N含量增大。元素含量变化对不锈钢耐蚀性的影响可用耐点蚀当量 (PREN) 来进行衡量,其值可由下式计算[9]:
式中,WCr、WMo和WN分别为Cr、Mo和N的质量分数。计算得到不同试样中α和γ相的PREN值如图5所示。1#试样中α和γ相的PREN值仅相差0.55 (2.3%),可认为近似相等,两相的占比接近 (1∶1.14);而2#和3#试样中α相占比增大,但其PREN值下降,γ相占比下降,但其PREN值上升。两相PREN值分别相差了1.86 (7.8%) 和4.41 (18.9%)。这说明固溶处理使得合金元素在两相中重新分配,结果导致α相占比增大但耐蚀性下降。3种2002双相不锈钢试样恒电位极化后的点蚀密度统计结果 (图3) 也证实了这一点。随着α相占比的增大,其点蚀密度由12.33个/mm2增长到14.68和19.21个/mm2;同时,随着γ相占比的减小,其点蚀密度由8.87下降到6.79和4.97个/mm2。
图5 3种2002双相不锈钢试样中α和γ相的PREN值
正是由于固溶处理后2002双相不锈钢中的弱相 (α相) 变得更弱,使得点蚀更容易在α相上萌生。α相占比的增大使得双相不锈钢整体的耐点蚀性能下降。因此,原始1#试样的点蚀电位从0.317 V下降至固溶处理的2#和3#试样的0.283和-0.028 V。
3.2 组织配分对2002双相不锈钢点蚀扩展的影响
2002双相不锈钢在恒电位极化后,表面出现蕾丝花边盖的特征腐蚀形貌 (图6)。这一现象已有很多相关研究[10-14]。一般认为,点蚀萌生后,蚀坑内溶解的金属离子浓度C0由坑底向坑口方向降低,并在靠近坑口处的急剧下降。在蚀坑表面的金属离子浓度都低于活性溶解所需的最低溶度C* (临界金属离子浓度) ,此时,坑壁处于钝化状态。而金属离子浓度向蚀坑深度方向迅速提高,达到饱和溶度Csat后FeCl2沉淀生成 (图7a) ,使得点蚀坑在深度方向的扩展速度减缓。由于金属离子浓度由坑底向坑口方向形成浓度梯度,将溶液中金属离子浓度达到C*的各处连接可得到一条C*线 (图7a),高于C*线的区域,金属离子浓度C0<C*,坑壁处于钝化状态;低于C*线的区域,金属离子浓度C*<C0<Csat;坑壁处于活性溶解状态。但FeCl2沉淀的生成阻碍了蚀坑向深度方向发展,只有蚀坑的侧壁能够快速溶解,于是蚀坑向宽度方向快速发展。当蚀坑侧壁溶解导致原始蚀坑附近出现新的蚀坑后 (图7b),高浓度的金属离子向坑外扩散,靠近坑口处的坑壁钝化,蚀坑再次向宽度方向发展。这一过程不断循环最终得到了表面覆有蕾丝盖的宽而浅的碟形点蚀坑 (图7c)。
图6 两种试样在恒电位极化后表面蕾丝花边形貌
图7 蕾丝盖形成示意图
由点蚀尺寸统计 (图4) 可知,经过恒电位极化后,1#原始试样和固溶处理后2#和3#试样,点蚀坑的平均点蚀深度差别不大,但平均直径逐渐下降。有研究通过建立时间和蚀坑深度变化的模型发现蚀坑深度方向的扩展与时间的平方根呈线性关系[16]。其定量关系可由下式表示:
式中,Xd为蚀坑深度;t为时间;Csat为溶液中金属离子的饱和浓度;Csolid为金属原子浓度 (金属密度除以平均摩尔质量);D0为Fe2+在20 ℃时的扩散系数;T0为293.15 (K);T为溶液温度 (K)。
2002双相不锈钢进行固溶处理后,只改变了α和γ两相的占比以及合金元素在两相中的分布,并不会改变溶液中金属离子的饱和浓度Csat和金属原子浓度Csolid。据此可以认为,对于1#、2#和3#试样,式 (2) 中的各个参数都未发生改变。因此,恒电位极化相同时间后,3种试样的点蚀坑深度接近,均为10 μm左右 (图4)。
点蚀坑宽度方向的发展速率与蚀坑内金属离子的浓度分布相关。当试样的耐蚀性较差时 (3#试样),相同的极化条件下蚀坑内会溶解出更多的金属离子,使得C*线向坑口处移动 (图8),导致蚀坑在宽度方向扩展后,在靠近原始蚀坑附近出现新的蚀坑;对耐蚀性较好的试样 (1#试样),C*线更靠近坑底,更倾向于在远离原始蚀坑附近出现新的蚀坑;蚀坑内活化-钝化过程经过多次循环后,1#试样点蚀坑平均直径最大,为46.52 μm左右,而3#试样点蚀坑平均直径最小,为36.04 μm左右。
图8 不同耐蚀性试样蚀坑横向扩展示意图
由以上讨论可知,点蚀坑深度方向的发展主要和Csat、Csolid、D0和T相关,而宽度方向发展则取决于蚀坑溶液中金属离子的分布。固溶处理并不会改变Csat、Csolid、D0和T,但却显著改变了试样的耐蚀性,导致溶液中的金属离子浓度分布的改变。因此,3种试样点蚀坑的深度基本一致,而蚀坑在宽度方向的发展随耐蚀性下降变慢。
4 结论
(1) 固溶处理改变了2002双相不锈钢中α相和γ相的比例和合金元素在两相中的分布。随着固溶温度升高,α相含量增加,主要合金元素向γ相中聚集,导致α相PREN值下降,2002双相不锈钢的点蚀电位下降,点蚀抗性降低。
(2) 随着固溶温度升高,α相上点蚀密度增大,而γ相上点蚀密度减小,点蚀更倾向于在弱相α相上萌生。
(3) 2002双相不锈钢发生点蚀时呈现出蕾丝盖的腐蚀形貌,蕾丝盖下的点蚀坑具有浅而宽的碟形特征。试样的耐蚀性越好,点蚀坑越容易向宽度方向发展,对深度方向的发展影响不大。
参考文献
1 Wu D C, Han P D. Effects of moderate temperature aging treatment on corrosion resistance of SAF2304 duplex stainless steel [J]. J. Chin. Soc. Corros. Prot., 2020, 40: 51
1 武栋才, 韩培德. 中温时效处理对SAF2304双相不锈钢耐蚀性的影响 [J]. 中国腐蚀与防护学报, 2020, 40: 51
2 Tong H S, Sun Y H, Su Y J, et al. Investigation on Hydrogen-induced cracking behavior of 2205 duplex stainless steel used for marine structure [J]. J. Chin. Soc. Corros. Prot., 2019, 39: 130
2 童海生, 孙彦辉, 宿彦京等. 海工结构用2205双相不锈钢氢致开裂行为研究 [J]. 中国腐蚀与防护学报, 2019, 39: 130
3 Pang X G, Liu R Q, Wang W T, et al. Effect of aging temperature on microstructure and corrosion resistance of S32750 super duplex stainless steel in hydrofluoric acid [J]. J. Chin. Soc. Corros. Prot., 2017, 37: 519
3 逄旭光, 刘润青, 王文涛等. 时效温度对S32750超级双相不锈钢组织和抗氢氟酸腐蚀性能的影响 [J]. 中国腐蚀与防护学报, 2017, 37: 519
4 Yang Y Z. Investigatating pitting and crevice corrosion behavior of nickel conservation duplex stainless steel [D]. Shanghai: Fudan University, 2013
4 杨雁泽. 资源节约型双相不锈钢点蚀和缝隙腐蚀行为研究 [D]. 上海: 复旦大学, 2013
5 Han D. Investigation on the mechanism of localized electrochemical corrosion behavior of duplex stainless steel [D]. Shanghai: Fudan University, 2012
5 韩冬. 双相不锈钢局部电化学失效行为与机理的研究 [D]. 上海: 复旦大学, 2012
6 Zhang L H, Zhang W, Jiang Y M, et al. Influence of annealing treatment on the corrosion resistance of lean duplex stainless steel 2101 [J]. Electrochim. Acta, 2009, 54: 5387
7 Zhang L H. Study on the corrosion behavior of economical duplex stainless steel 2101 [D]. Shanghai: Fudan University, 2013
7 张丽华. 经济型双相不锈钢2101的腐蚀行为研究 [D]. 上海: 复旦大学, 2010
8 Guo Y J, Sun T Y, Hu J C, et al. Microstructure evolution and pitting corrosion resistance of the Gleeble-simulated heat-affected zone of a newly developed lean duplex stainless steel 2002 [J]. J. Alloy. Compd., 2016, 658: 1031
9 Feng H, Song Z G, Wu X H, et al. Relationship between selective corrosion behavior and duplex structure of 022Cr25Ni7Mo4N duplex stainless steel [J]. J. Chin. Soc. Corros. Prot., 2019, 39: 138
9 丰涵, 宋志刚, 吴晓涵等. 022Cr25Ni7Mo4N双相不锈钢选择性腐蚀行为与两相组织的关系研究 [J]. 中国腐蚀与防护学报, 2019, 39: 138
10 Ernst P, Laycock N J, Moayed M H, et al. The mechanism of lacy cover formation in pitting [J]. Corros. Sci., 1997, 39: 1133
11 Ernst P, Newman R C. Pit growth studies in stainless steel foils. I. Introduction and pit growth kinetics [J]. Corros. Sci., 2002, 44: 927
12 Ernst P, Newman R C. Pit growth studies in stainless steel foils. II. Effect of temperature, chloride concentration and sulphate addition [J]. Corros. Sci., 2002, 44: 943
13 Chen Z G, Zhang G F, Bobaru F. The Influence of passive film damage on pitting corrosion [J]. J. Electrochem. Soc., 2016, 163: C19
14 Scheiner S, Hellmich C. Stable pitting corrosion of stainless steel as diffusion-controlled dissolution process with a sharp moving electrode boundary [J]. Corros. Sci., 2007, 49: 319
免责声明:本网站所转载的文字、图片与视频资料版权归原创作者所有,如果涉及侵权,请第一时间联系本网删除。
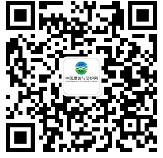
官方微信
《中国腐蚀与防护网电子期刊》征订启事
- 投稿联系:编辑部
- 电话:010-62316606-806
- 邮箱:fsfhzy666@163.com
- 中国腐蚀与防护网官方QQ群:140808414