摘要
利用透射电镜、能谱仪、激光共聚焦显微镜和X射线衍射仪分析了喷丸处理后TC4钛合金的表面形貌和粗糙度;采用动电位极化曲线、电化学阻抗谱和Mott-Schottky曲线对喷丸处理前后的TC4钛合金在3.5%NaCl溶液中的耐蚀性进行了分析。结果表明,与少量喷丸残留物相比,表面粗糙度对耐蚀性影响较大。抛光后的TC4钛合金腐蚀电流密度最低,容抗弧半径最大,钝化膜缺陷最少,耐蚀性最强。喷丸处理后,铸钢丸喷丸表面的钝化膜最稳定,耐蚀性相对较高。因此,光滑表面有助于形成均匀的钝化膜层,增加TC4钛合金的耐蚀性。
关键词: TC4钛合金 ; 喷丸处理 ; 表面状态 ; 粗糙度 ; 耐蚀性
钛合金因其良好的综合性能,已经被广泛应用于航空航天、海洋、医疗等领域[1]。TC4 (Ti6Al4V) 是一种α+β双相钛合金,含有6% (质量分数,下同) 的α相稳定元素Al和4%的β相稳定元素V[2],约占目前所用钛合金产品的60%。目前,国内TC4钛合金正在被研究用于汽轮机叶片,成为代替马氏体耐热不锈钢和沉淀硬化不锈钢的材料[3],期望减少末级叶片的腐蚀破坏问题,延长寿命。但钛合金表面也存在硬度低、耐磨性及高温抗氧化性差等缺点,限制了其进一步应用。为了使钛合金零部件能够在复杂的环境下正常服役,采用表面改性处理来提高钛合金的表面性能被越来越多的研究者所重视。其中,喷丸处理已成为TC4钛合金结构件重要的表面处理方法[4]。
喷丸处理通过使高能量的弹丸不断撞击钛合金表面,产生剧烈塑性变形,起伏程度增大,粗糙度发生变化,同时也引入了大量位错和晶界,使钛合金表面晶粒纳米化[5]。由于沿晶界的扩散系数比在晶粒内和沿位错管道的扩散系数大得多,因此晶界大大促进了原子的扩散[6,7],使表面钝化膜快速形成,有利于耐蚀性的提高。但钛合金的耐腐蚀性能还与表面状态有关,喷丸处理造成的表面粗糙度过大以及喷丸过程中残留在表面的弹丸碎屑都会使材料的耐蚀性能恶化[8]。
目前,对钛合金进行喷丸处理的研究更多集中于疲劳性能。李康等[9]研究了湿喷丸技术对TC4钛合金疲劳寿命的影响。张聪惠等[10]通过超声波喷丸处理提高了TC4钛合金的疲劳极限。黄宇等[11]研究了深冷激光喷丸对TC6钛合金振动疲劳寿命的影响。Tan等[12]研究了TC17合金叶片在集成制造工艺条件下的表面完整性和疲劳性能。Soyama等[13]通过空化喷丸、激光喷丸和颗粒喷丸对Ti6Al4V钛合金处理的平面弯曲疲劳实验,阐明了增材制造Ti6Al4V疲劳强度提高的机理。在利用喷丸处理改善钛合金的耐蚀性方面,报道较少,特别是缺乏关于喷丸后表面状态对钛合金耐腐蚀性能影响的研究。本工作分别采用铸钢丸喷丸、玻璃丸喷丸和铸钢丸与玻璃丸复合喷丸对TC4钛合金表面进行处理,通过在3.5% (质量分数) NaCl溶液中的电化学实验,探讨了喷丸处理后表面状态对TC4钛合金的耐蚀性影响。
1 实验方法
试样材料为TC4钛合金 (Ti6Al4V),主要化学成分 (质量分数,%):Al 6.24,V 4.01,Fe 0.20,Si 0.12,C 0.03,N 0.02,H 0.0021,O 0.14,Ti余量。TC4钛合金试样的尺寸为15 mm×15 mm×10 mm,用SiC砂纸由粗到细打磨至2000#后,用1.5 μm的金刚石抛光膏抛光,经无水乙醇、去离子水去油、去污后,吹干待用。喷丸处理采用气动式喷丸机喷丸,喷丸介质为铸钢丸,以及玻璃丸,覆盖率均大于100%。喷丸方式有铸钢丸喷丸处理 (CSSP),玻璃丸喷丸处理 (GSP),以及铸钢丸与玻璃丸复合喷丸处理 (CSP)。
利用场发射扫描电镜 (FE-SEM,Thermo Fisher APREO) 观察分析喷丸处理后的表面形貌,并用其配备的电子能谱仪 (EDS),对喷丸处理前后的试样表面进行成分分析。
采用LEXT-OLS5000激光共聚焦显微镜 (CLSM) 观察分析喷丸处理前后TC4钛合金的表面三维形貌、表面比表面积和粗糙度轮廓线,选取轮廓线各个点绝对值的算术平均值Ra、均方根Rq和剖面的平均最大高度Rz来表征TC4钛合金表面粗糙度。每个试样选6个区域测试,然后取平均值,测量前用无水乙醇清洗试样以去除表面污染。
利用X射线衍射仪 (XRD,Bruker D8 Advance) 对喷丸后TC4钛合金表面进行物相成分分析,采用Cu靶,Kα波长0.15418 nm,管电压40 kV,管电流为40 mA,2θ扫描角度范围20°~80°,扫描步长0.1°,每步停留0.15 s。
电化学测试采用Zahner zennium电化学工作站,所用电解质为3.5%NaCl溶液,实验温度为23 ℃。测试采用三电极体系,饱和甘汞电极 (SCE) 为参比电极,铂片为辅助电极,硅胶封装的TC4钛合金为工作电极。
测试前TC4钛合金先在3.5%NaCl溶液中浸泡2 h,待开路电位稳定后进行电化学测试。电化学阻抗谱 (EIS) 测试频率范围为105~10-2 Hz,交流扰动电压为10 mV,使用ZSimpWin软件对数据进行拟合分析。动电位极化测试的电位扫描范围为-0.5 (vs.OCP)~+2 V (vs.SCE),扫速1 mV/s。在实验选定的2种钝化膜成膜电位下 (+1.1和+1.3 V) 下恒电位极化3 h后,进行Mott-Schottky测试,由高电位向低电位扫描,即测试区间从成膜电位扫描至-1.2 V (vs.SCE),测试频率为1 kHz,步长为25 mV,交流信号为10 mV。
2 结果与讨论
2.1 表面形貌分析
图1为TC4钛合金抛光后的表面形貌。可以看出,喷丸前TC4钛合金表面光滑平整,没有缺陷。图2a和b为TC4钛合金铸钢丸喷丸处理后的表面形貌。可以看到,高能量铸钢丸撞击产生凹坑,但凹坑较浅,凹坑的周边由于弹丸撞击而有翘起的现象。图2c和d与图2e和f分别是玻璃丸喷丸和复合喷丸后的表面形貌,与铸钢丸喷丸相比,凹坑变小,但弹丸撞击的凹坑密度明显增大,试样表面起伏比较大,出现许多翘起来的褶皱,甚至存在一定程度的起皮。这是因为玻璃丸在撞击TC4钛合金表面时,许多凹坑相互挤压,凹坑周围出现翘起来的褶皱;同时产生一定的微裂纹,微裂纹不断交叉和扩展,使翘起来的褶皱形成起皮[14]。除此之外,还可以看到,玻璃丸和复合喷丸TC4钛合金表面分布有大量的黑色团状喷丸残留物。
图1 喷丸前TC4钛合金表面形貌
图2 TC4钛合金经铸钢丸喷丸、玻璃丸喷丸和复合喷丸处理后的表面形貌
图3为TC4钛合金喷丸处理前后表面三维形貌图。图中出现局部的凸起 (红色区域) 和凹坑 (蓝色区域),更能直观表现喷丸处理后弹丸冲击TC4钛合金试样表面形成的高低起伏的形貌特征。图2所示TC4钛合金经铸钢丸喷丸、玻璃丸喷丸和复合喷丸处理后表面的最大高度差分别为3.377、11.081、14.224和17.348 μm,说明铸钢丸、玻璃丸和复合喷丸处理造成的表面起伏程度逐渐增大。
图3 TC4钛合金经铸钢丸喷丸、玻璃丸喷丸和复合喷丸处理后表面三维形貌图
表1为TC4钛合金的表面粗糙度参数以及比表面积。可以看出,抛光后的TC4钛合金粗糙度Ra最小,为0.059 μm;铸钢丸喷丸、玻璃丸喷丸和复合喷丸处理后的粗糙度Ra分别为0.550、0.602和0.676 μm,表面粗糙度参数依次增大,这与图3所得结论一致。随着表面粗糙度的增大,比表面积也在增大,表明TC4钛合金与腐蚀介质接触的有效真实面积越大,会导致腐蚀速率增大[15,16]。除此之外,粗糙度过大也会造成表面损伤,引起应力集中,萌生微裂纹,不利于表面性能的提高[10]。表面粗糙度对材料钝化层的形成也起着重要作用,一般来说,光滑的表面比粗糙的表面具有更好的耐腐蚀性[17]。
表1 未处理的TC4钛合金及经铸钢丸喷丸、玻璃丸喷丸和复合喷丸处理的表面粗糙度与比表面积
2.2 表面成分分析
图4是TC4钛合金及经铸钢丸喷丸、玻璃丸喷丸和复合喷丸处理后的EDS结果。可知,TC4钛合金表面在铸钢丸喷丸处理后Fe含量有所增加,复合喷丸处理后Fe含量略微下降,但仍高于TC4钛合金与玻璃丸喷丸处理试样,表明在铸钢丸基础上进行玻璃丸喷丸,可以起到降低铸钢丸喷丸残留物含量的作用。除此之外,在玻璃丸喷丸与复合喷丸处理之后,TC4钛合金表面O、Si显著增加,Ti、V含量随之下降。结合对TC4钛合金表面的粗糙度分析,表明在玻璃丸喷丸过程中,由于玻璃丸撞击产生的凹坑分布更均匀,玻璃丸的碎屑嵌入了试样表面,引入了O和Si,喷丸残留物的覆盖面更大,使得能谱仪检测到的Ti、V含量下降。所以,在铸钢丸喷丸处理的基础上进行玻璃丸喷丸处理,虽然可以起到降低铸钢丸喷丸残留物含量的作用,但也引入了新的玻璃丸喷丸残留物。
图4 未处理的TC4钛合金及经喷丸处理的表面EDS结果
2.3 XRD谱分析
图5为喷丸处理前后TC4钛合金表面的XRD谱。可以观察到,Ti的密排六方紧密堆积 (hcp) 晶体结构,以及体心立方 (bcc) 晶体结构所对应的衍射峰,尖锐、强烈的峰证实了该合金高度的结晶性。XRD谱没有出现其他物相的衍射峰。由EDS分析可知是因为包括喷丸残留元素在内的其他元素含量相对较少。与未表面处理的TC4钛合金相比,喷丸后TC4钛合金的X射线Bragg衍射峰未发生明显的变化。利用Scherrer-Wilson方程,可以近似计算出TC4钛合金、经铸钢丸喷丸、玻璃丸喷丸和复合喷丸处理后的平均晶粒尺寸,分别为154,166,180和152 nm。表明与未处理的TC4钛合金相比,TC4钛合金经喷丸处理后,平均晶粒尺寸未发生明显变化,所用喷丸工艺对TC4钛合金的表层影响有限。所以,喷丸处理后TC4钛合金的耐蚀性主要由表面状态决定。
图5 未处理的TC4钛合金及喷丸处理后TC4钛合金的XRD谱
2.4 动电位极化测试
图6为4种试样在3.5%NaCl溶液中的动电位极化曲线。可见,4种TC4钛合金的极化曲线上没有明显的活化—钝化过渡,在很宽的电位区间内,试样保持较低的阳极电流密度,表明喷丸处理前后TC4钛合金都能自发钝化[18],而且喷丸处理后的TC4钛合金在3.5%NaCl溶液中的极化曲线走势基本一致。根据Tafel曲线外推法拟合出的相关电化学参数如表2所示。
图6 未处理的TC4钛合金及喷丸处理TC4钛合金在3.5%NaCl溶液中的动电位极化曲线
表2 TC4钛合金基材及喷丸处理后在3.5%NaCl溶液中的动电位极化测试拟合结果
表2显示了TC4钛合金的腐蚀电位Ecorr,腐蚀电流密度Icorr,钝化电流密度Ipass。可见,喷丸处理使TC4钛合金的腐蚀电位正移,但腐蚀电流密度却增大。Ecorr只能反映发生腐蚀的倾向,并不能说明腐蚀速率的快慢[19]。而电极材料的腐蚀速率与腐蚀电流密度相关,腐蚀电流密度越大,腐蚀速率越快[20]。所以,TC4钛合金在喷丸处理后,Icorr增大,耐蚀性降低,而且铸钢丸喷丸、玻璃丸喷丸、复合喷丸的耐蚀性依次降低。从Ipass来看,TC4钛合金喷丸处理后,Ipass增大,表明光滑表面的钝化膜稳定性更高[17]。喷丸处理之后,铸钢丸喷丸处理后的TC4钛合金的Ipass较低,说明铸钢丸喷丸处理TC4钛合金表面形成的钝化膜相对稳定一些,铸钢丸喷丸残留物没有对耐蚀性造成影响。
2.5 电化学阻抗测试
图7是TC4钛合金在3.5%NaCl溶液中电化学阻抗测试得到的Nyquist图和Bode图。Nyquist图中的容抗弧半径正比于耐蚀性,即容抗弧越大,耐蚀性越好。Bode图中的高频区反映出TC4钛合金与腐蚀溶液界面的腐蚀特性,中、低频区反映出TC4钛合金的特性[21],低频区阻抗的幅值可以直接说明TC4钛合金的耐蚀性优劣,阻抗幅值越大,耐蚀性能越好[22]。由图可知,4种TC4钛合金的阻抗模值|Z|、相位角θ随频率的变化趋势大致相同,lg|Z|-lg f曲线在中低频区表现为一段斜率接近-1的直线,phase-lg f曲线在中低频区呈现出相位角很宽的平台,表明TC4钛合金有很强的耐蚀性[23]。未处理的TC4钛合金的容抗弧半径大于喷丸处理后的,表明TC4钛合金的耐蚀性能优于喷丸处理后的TC4钛合金,喷丸处理后的TC4钛合金中铸钢丸喷丸的容抗弧较大,进一步证明铸钢丸喷丸的耐蚀性较好,Bode图中低频区的阻抗幅值大小也可以说明这一点。
图7 未处理的TC4钛合金及喷丸处理TC4钛合金在3.5%NaCl溶液中的电化学阻抗谱
图8为TC4钛合金在3.5%NaCl液中的等效电路图,拟合结果见表3。其中,Rs表示参比电极与试样表面之间溶液电阻;Q和n是常相位角元件的两个参数,Q为常相位角元件 (CPE),n为CPE常数,-1<n<1。用常相位角元件Q代替纯电容,主要是体系处于非理想状态,试样表面存在弥散效应。n值和试样的表面粗糙度有关,n越大,说明试样表面钝化膜越致密,更能有效地阻挡腐蚀介质,降低试样的腐蚀速率[24]。一般也认为,钛的钝化膜是分层存在的[25],分为疏松结构的外层和致密的内层阻挡层[18]。所以,Q1、R1和Q2、R2分别表示钝化膜外部多孔层和内部致密层的电容和电阻。
图8 未处理的TC4钛合金及喷丸处理TC4钛合金在3.5%NaCl溶液中的等效拟合电路图
表3 未处理的TC4钛合金及喷丸处理后在3.5%NaCl溶液中的电化学阻抗拟合分析结果
通过表3可知,电化学阻抗的拟合误差值 (χ2) 为10-5数量级,处于误差范围之内,说明使用的等效电路模型符合要求。TC4钛合金的钝化膜外层电阻R1均远小于R2,表明TC4钛合金的耐蚀性能主要取决于钝化膜内部致密层,而外部疏松多孔层对耐腐蚀性的贡献较小[18]。表中抛光后的TC4钛合金的R2最大,表明其耐蚀性最好;其次是铸钢丸喷丸、玻璃丸喷丸和复合喷丸处理TC4钛合金,耐蚀性按顺序依次减小。另外,喷丸处理后,铸钢丸喷丸TC4钛合金表面致密层的弥散系数n2相对较大,表明铸钢丸喷丸后表面的钝化膜更加稳定,有更好的自我修复能力,这与极化曲线结论一致。
2.6 Mott-Schottky测试
材料表面形成的钝化膜通常为半导体,其电子性能可以用Mott-Schottky分析进行评价[26]。根据Mott-Schottky理论,金属-电解质界面的电荷分布可以通过钝化膜的空间电荷电容Csc和电极电位E的函数,即Mott-Schottky方程来描述[28]。
对于n型半导体:
对于p型半导体:
式中,Csc为空间电荷电容,εr为钝化膜相对介电常数 (TiO2钝化膜取60[27]),ε0为真空介电常数 (8.854×10-14 F/cm),e为电荷电量 (1.602×10-19 C),Nd和Na分别为施主和受主载流子浓度,A为试样与液体的真实接触面积 (已经测得TC4钛合金喷丸后的比表面积分别为1.076、1.105和1.119,与喷丸前试样表面积2.25 cm2相乘,可得铸钢丸喷丸、玻璃丸喷丸和复合喷丸TC4钛合金的真实面积分别为为2.42、2.49和2.52 cm2),Efb为平带电位,k为Boltzmann常数 (1.38×10-23 J/K),T为热力学温度。室温下kT/e约为25 mV,通常可以忽略不计。
在钝化区内,TC4钛合金表面的主要电化学反应是钝化膜的形成,只要施加一定的钝化电位,表面就能生成阻值很高的钝化膜,并且随电位升高钝化膜会持续生长[28]。所以在动电位极化曲线钝化区间选+1.1和+1.3 V电位,进行恒电位极化成膜,并测试Mott-Schottky曲线。图9为4种TC4钛合金在3.5%NaCl溶液中+1.1和+1.3 V恒电位下测试的Mott-Schottky曲线。由图可知,4种TC4钛合金的Mott-Schottky曲线变化趋势大致相同,都出现两个不同斜率的线性区。高电位区的线性区反映测试材料的介电行为,而低电位区的线性区才代表测试材料的半导体特性[29,30]。图中TC4钛合金Mott-schottky曲线的低电位区斜率为正值,且斜率随成膜电位的增加而增加,表明4种试样表面生成的钝化膜均为n型半导体,即主要载流子为间隙Ti离子和氧空位,钝化膜中的载流子随成膜电位的增加而减少,与Fattah-alhosseini所得结论一致[31]。选取低电位线性区对试样半导体特性进行分析,根据Mott-Schottky 方程计算载流子密度值Nd和平带电位Efb,Nd可以通过1/C2-E曲线的斜率2/(eεrε0kA2) 确定,平带电位Efb可以由1/C2=0求得。
图9 未处理的TC4钛合金及复合喷丸处理后在3.5%NaCl溶液中的Mott-Schottky曲线
图10为未处理的TC4钛合金、铸钢丸喷丸、玻璃丸喷丸和复合喷丸处理后在3.5%NaCl溶液中恒电位极化所形成钝化膜的Nd和Efb。可知,TC4钛合金的Nd最小,喷丸试样中,铸钢丸喷丸后表面生成钝化膜的载流子密度最小。载流子密度越小,意味着钝化膜的缺陷越少,施主密度的降低会抑制电子的转移,进而抑制电化学反应,从而增强了钝化膜的保护能力[32]。随成膜电位的升高,Efb正移,也说明钝化膜对TC4钛合金的保护效果提高[33]。所以,抛光后TC4钛合金形成的钝化膜中具有最少的缺陷,因而保持了较低的Ipass。
图10 未处理的TC4钛合金及喷丸处理后在3.5%NaCl溶液中钝化膜的Nd和Efb
根据以上分析,抛光TC4钛合金生成的钝化膜稳定性强,耐蚀性最高,说明光滑的表面有助于形成均匀的钝化膜层,增加基体的耐蚀性。喷丸处理后,铸钢丸喷丸TC4钛合金的钝化膜耐蚀性最好。结合表面形貌及EDS、XRD分析可知,与少量喷丸残留物相比,喷丸后表面的粗糙度对TC4钛合金的耐蚀性影响更大。由于玻璃丸喷丸和复合喷丸后,TC4钛合金表面粗糙度较大,所以与铸钢丸喷丸相比,耐蚀性降低。
3 结论
(1) 喷丸前抛光的TC4钛合金表面光滑平整,没有缺陷。铸钢丸喷丸TC4钛合金处理后的表面存在凹坑,但凹坑较浅,凹坑的周边由于弹丸撞击而有翘起的现象。与铸钢丸喷丸处理相比,玻璃丸喷丸和复合喷丸后TC4钛合金表面的凹坑变小,但凹坑密度明显增大,表面起伏比较大,出现许多翘起来的褶皱,甚至存在一定程度的起皮。而且喷丸后TC4钛合金表面少量的喷丸残留物,铸钢丸喷丸残留物以Fe为主,玻璃丸喷丸残留物主要是Si,复合喷丸后表面残留物同时含Si和Fe。
(2) 抛光后TC4钛合金的粗糙度Ra最小,为 0.059 μm;喷丸处理后,表面发生塑性形变,粗糙度发生变化,铸钢丸喷丸、玻璃丸喷丸和复合喷丸处理后的粗糙度Ra分别为0.550,0.602和0.676 μm,表面粗糙度参数依次增大。所用喷丸工艺对TC4钛合金表层的影响有限,喷丸处理后TC4钛合金的耐蚀性主要由表面状态决定。
(3) 在3.5%NaCl溶液中,抛光后的TC4钛合金的Icorr最小,致密层的电阻R2最大,形成的钝化膜缺陷较少,因而能够保持较低Ipass,耐蚀性最强。喷丸处理的TC4钛合金中,铸钢丸喷丸处理后的钝化膜最稳定,耐蚀性相对较高。与少量喷丸残留物相比,表面粗糙度的大小对耐蚀性影响较大。所以,光滑的表面有助于形成均匀的钝化膜层,增加TC4钛合金的耐蚀性。
参考文献
1 Prakash C, Singh S, Pruncu C I, et al. Surface modification of Ti-6Al-4V alloy by electrical discharge coating process using partially sintered Ti-Nb electrode [J]. Materials (Basel), 2019, 12: 1006
2 Krawiec H, Vignal V, Schwarzenboeck E, et al. Role of plastic deformation and microstructure in the micro-electrochemical behaviour of Ti-6Al-4V in sodium chloride solution [J]. Electrochim. Acta, 2013, 104: 400
3 Kuang Y Q. Research on the application prospect of titanium alloy on steam turbine blades [J]. Jiangsu Sci. Technol. Inform., 2013, (1): 67
3 匡逸强. 钛合金在汽轮机叶片上的应用前景研究 [J]. 江苏科技信息, 2013, (1): 67
4 Chen G Q, Tian T Y, Zhang X H, et al. Microstructure and fatigue properties of Ti-6Al-4V titanium alloy treated by wet shot peening of ceramic beads [J]. Chin. J. Nonferrous Met., 2013, 23: 122
4 陈国清, 田唐永, 张新华等. Ti-6Al-4V钛合金陶瓷湿喷丸表面强化微观组织与疲劳性能 [J]. 中国有色金属学报, 2013, 23: 122
5 Yang C, Liu Y G, Li M Q. Characteristics and formation mechanisms of defects in surface layer of TC17 subjected to high energy shot peening [J]. Appl. Surf. Sci., 2020, 509: 144711
6 Oh-Ishi K, Edalati K, Kim H S, et al. High-pressure torsion for enhanced atomic diffusion and promoting solid-state reactions in the aluminum-copper system [J]. Acta Mater., 2013, 61: 3482
7 Oudriss A, Creus J, Bouhattate J, et al. Grain size and grain-boundary effects on diffusion and trapping of hydrogen in pure nickel [J]. Acta Mater., 2012, 60: 6814
8 Zhao R, Wu Z, Liu L, et al. Research progress in effect of shot peening on corrosion resistance of metallic materials [J]. Heat Treat. Met., 2018, 43(12): 88
8 赵蓉, 吴忠, 刘磊等. 喷丸对金属材料耐蚀性能影响的研究进展 [J]. 金属热处理, 2018, 43(12): 88
9 Li K, Fu X S, Li Z Q, et al. Fatigue fracture mechanism of Ti-6Al-4V alloy strengthened by wet peening treatment [J]. Rare Met. Mater. Eng., 2017, 46: 3068
9 李康, 付雪松, 李志强等. 湿喷丸强化对TC4合金疲劳断裂机制的影响 [J]. 稀有金属材料与工程, 2017, 46: 3068
10 Zhang C H, Xie G, Song W, et al. Fatigue performance of surface nanocrystallized TC4 [J]. Rare Met. Mater. Eng., 2015, 44: 866
10 张聪惠, 解钢, 宋薇等. 表面纳米化TC4疲劳性能研究 [J]. 稀有金属材料与工程, 2015, 44: 866
11 Huang Y, Zhou J Z, Li J, et al. Effects of cryogenic laser peening on damping characteristics and vibration fatigue life of TC6 titanium alloy [J]. Chin. J. Laser, 2020, 47: 0402011
11 黄宇, 周建忠, 李京等. 深冷激光喷丸对TC6钛合金阻尼特性及振动疲劳寿命的影响 [J]. 中国激光, 2020, 47: 0402011
12 Tan L, Yao C F, Zhang D H, et al. Evolution of surface integrity and fatigue properties after milling, polishing, and shot peening of TC17 alloy blades [J]. Int. J. Fatigue, 2020, 136: 105630
13 Soyama H, Takeo F. Effect of various peening methods on the fatigue properties of titanium Alloy Ti6Al4V manufactured by direct metal laser sintering and electron beam melting [J]. Materials, 2020, 13: 2216
14 Yang L. Analysis of surface roughness and impairment after surface nanocrystallization for HSP [D]. Dalian: Dalian Jiaotong University, 2006
14 杨磊. 高能喷丸表面纳米化后表面粗糙度和损伤的研究 [D]. 大连: 大连交通大学, 2006
15 Lee H S, Kim D S, Jung J S, et al. Influence of peening on the corrosion properties of AISI 304 stainless steel [J]. Corros. Sci., 2009, 51: 2826
16 Hao Y W, Deng B, Zhong C, et al. Effect of surface mechanical attrition treatment on corrosion behavior of 316 stainless steel [J]. J. Iron Steel Res. Int., 2009, 16: 68
17 Chi G F, Yi D Q, Liu H Q. Effect of roughness on electrochemical and pitting corrosion of Ti-6Al-4V alloy in 12 wt.%HCl solution at 35? ℃ [J]. J. Mater. Res. Technol., 2020, 9: 1162
18 Xu J, Bao X K, Jiang S Y. In vitro corrosion resistance of Ta2N nanocrystalline coating in simulated body fluids [J]. Acta Metall. Sin., 2018, 54: 443
18 徐江, 鲍习科, 蒋书运. 纳米晶Ta2N涂层在模拟人体环境中的耐蚀性能研究 [J]. 金属学报, 2018, 54: 443
19 Li X, Dong Y C, Dan Z H, et al. Corrosion behavior of ultrafine grained pure ti processed by equal channel angular pressing [J]. Acta Metall. Sin., 2019, 55: 967
19 李鑫, 董月成, 淡振华等. 等通道角挤压制备超细晶纯Ti的腐蚀性能研究 [J]. 金属学报, 2019, 55: 967
20 Xie F X, He X B, Cao S L, et al. Influence of pore characteristics on microstructure, mechanical properties and corrosion resistance of selective laser sintered porous Ti–Mo alloys for biomedical applications [J]. Electrochim. Acta, 2013, 105: 121
21 Shukla A K, Balasubramaniam R, Bhargava S. Properties of passive film formed on CP titanium, Ti-6Al-4V and Ti-13.4Al-29Nb alloys in simulated human body conditions [J]. Intermetallics, 2005, 13: 631
22 Yang Y J, Zhang X Y, Liu M H. Galvanic corrosion of TB5 titanium alloy of anodic oxidation film [J]. J. Aeronaut. Mater., 2015, 35(5): 57
22 杨勇进, 张晓云, 刘明辉. TB5钛合金脉冲阳极氧化膜电偶腐蚀性能研究 [J]. 航空材料学报, 2015, 35(5): 57
23 Yang F, Wu J P, Guo D Z, et al. Electrochemical corrosion of Ti-Ta alloy in nitric acid [J]. Titanium Ind. Prog., 2018, 35(2): 22
23 杨帆, 吴金平, 郭荻子等. Ti-Ta合金在硝酸中电化学腐蚀研究 [J]. 钛工业进展, 2018, 35(2): 22
24 Shi K Y, Zhang J Z, Zhang Y, et al. Preparation and corrosion resistance of Nb2N coating on TC4 Ti-alloy [J]. J. Chin. Soc. Corros. Prot., 2019, 39: 313
24 史昆玉, 张进中, 张毅等. Nb2N涂层制备及其耐腐蚀性能研究 [J]. 中国腐蚀与防护学报, 2019, 39: 313
25 Wang L, Yi D Q, Liu H Q, et al. Effect of Ru on corrosion behavior of Ti-6Al-4V alloy and its mechanism [J]. J. Chin. Soc. Corros. Prot., 2020, 40: 25
25 王乐, 易丹青, 刘会群等. Ru对Ti-6Al-4V合金腐蚀行为的影响及机理研究 [J]. 中国腐蚀与防护学报, 2020, 40: 25
26 Jiang Z L, Xin D, Middleton H. Investigation on passivity of titanium under steady-state conditions in acidic solutions [J]. Mater. Chem. Phys., 2011, 126: 859
27 Jovic V D, Barsoum M W. Corrosion behavior and passive film characteristics formed on Ti, Ti3SiC2, and Ti4AlN3 in H2SO4 and HCl [J]. J. Electrochem. Soc., 2004, 151: B71
28 Yan S K, Zheng D J, Wei J, et al. Electrochemical activation of passivated pure Titanium in artificial seawater [J]. J. Chin. Soc. Corros. Prot., 2019, 39: 123
28 严少坤, 郑大江, 韦江等. 钝性纯Ti在人工海水中的电化学活化行为研究 [J]. 中国腐蚀与防护学报, 2019, 39: 123
29 Silva R A, Walls M, Rondot B, et al. Electrochemical and microstructural studies of tantalum and its oxide films for biomedical applications in endovascular surgery [J]. J. Mater. Sci.: Mater. Med., 2002, 13: 495
30 Schneider M, Schroth S, Schilm J, et al. Micro-EIS of anodic thin oxide films on titanium for capacitor applications [J]. Electrochim. Acta, 2009, 54: 2663
31 Fattah-Alhosseini A, Imantalab O, Ansari G. The role of grain refinement and film formation potential on the electrochemical behavior of commercial pure titanium in Hank's physiological solution [J]. Mater. Sci. Eng., 2017, 71C: 827
32 Zheng Z J, Gao Y, Gui Y, et al. Corrosion behaviour of nanocrystalline 304 stainless steel prepared by equal channel angular pressing [J]. Corros. Sci., 2012, 54: 60
33 Zhang C H, Song W, Wang Y M, et al. Effect of surface strengthening on corrosion property of Ti-6Al-4V in 3.5%NaCl [J]. Appl. Mech. Mater., 2016, 853: 473
免责声明:本网站所转载的文字、图片与视频资料版权归原创作者所有,如果涉及侵权,请第一时间联系本网删除。
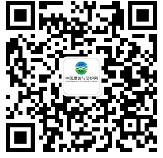
官方微信
《中国腐蚀与防护网电子期刊》征订启事
- 投稿联系:编辑部
- 电话:010-62316606-806
- 邮箱:fsfhzy666@163.com
- 中国腐蚀与防护网官方QQ群:140808414