铝合金的应力腐蚀及案例
铝制焊接容器中使用的铝和铝合金主要有工业高纯铝(LG)、工业纯铝(L)和防锈铝(LF),此外在锻件、棒材螺栓中还有硬铝(LY)和镀铝(LD)等,在航空航天、船舶、桥梁、大型容器、管道、车辆等领域中都广泛使用铝和铝合金结构材料。多用于空分装置的冷箱,包装存储的料仓。在硝酸生产装置中,铝制设备如漂白塔、浓硝贮槽等。小氮肥厂的碳化塔水箱,主要是用纯铝管。
01 铝合金的耐蚀性能
铝的耐蚀性基本上取决于在给定环境中铝的保护膜的稳定性。按介质作用可分为3类:
铝在pH4~8的介质中容易钝化,所以,铝在近中性的水中以及大气中是非常耐蚀的,但当介质中存在某种阴离子时,会产生点蚀等局部腐蚀。
铝耐硫和硫化物(如SO2和H2S)腐蚀,在许多有机酸中耐腐蚀,特别是耐无水醋酸腐蚀,但当含水量大于0.2% 及温度大于50℃时,会发生严重的局部腐蚀。
对于纯铝和低强度铝合金,一般不产生SCC。高强度铝合金则容易产生SCC。例如 Al-Cu-Mg(2000系列)、Al-Mg-Mn(5000系列),Al-Cu、Al-Mn-Si(6000系列),Al-Mg、Al-Mg-Zn 和Al-Zn、Al-Zn- Mg -Cu(7000系列)等强度较高的铝合金等。含铜、镁、锌量高的铝合金SCC敏感性最高。
02 铝合金SCC特征
铝合金的SCC主要发生含在Cl-的水溶液、湿气、某些液态金属、有机溶剂等环境中。铝合金在大气中,特别是海洋大气中和海水中常产生SCC。温度、湿度、Cl-含量越高,pH值越低,则越易发生SCC。此外,在不含Cl-的高温水和蒸气中也会发生SCC。应力升高,SCC敏感性升高。
铝合金在3.5%(mass) NaCl溶液环境中,呈活化状态的表面为腐蚀电池的阳极,氧化膜未受破坏的部分保持钝态为阴极,这样组成的活化-钝化电池,形成了小阳极大阴极,很快产生较深的点腐蚀。腐蚀产物体积膨胀,容易使铝合金因腐蚀产物的楔入效应而形成晶界腐蚀、剥蚀腐蚀乃至SCC。
在NaCl水溶液中,铝合金的SCC有以下几个特征:
a.铝合金的SCC是沿晶的;
b.强度高的铝合金SCC的敏感性大,这种敏感性按照下列铝合金系列的顺序为:7000系列>2000系列>5000系列>6000系列;
c.溶液温度升高和腐蚀性增强都会加大铝合金的SCC敏感性;
d.电化学极化对铝合金的SCC 敏感性有显著的影响,并且阳极极化的作用要比阴极极化强。阳极极化时,其SCC机制以阳极溶解为主,阴极极化时以氢致开裂为主;
e.对于同一系列铝合金,“过时效”处理比“欠时效”处理后的SCC的敏感性要小得多。
03 铝合金SCC机理
滑移-溶解理论及氢脆理论[1]。Al-Li-Cu-Mg合金在NaCl溶液中SCC敏感性与合金在变形过程中的滑移特征有很大的关系。欠时效状态下,粒子与基体间呈非共格关系,在滑移过程中形成平面滑移,滑移分布不均匀,容易破坏钝化膜,增加SCC的敏感性;过时效条件下粒子是半共格的或共格的,形成的滑移分布均匀,不容易破坏钝化膜,因而提高了合金的SCC抗力。
滑移-溶解理论中包括有经典的阳极溶解、氧化膜(钝化膜)撕裂、晶界溶质偏析、裂纹尖端拉伸带不稳定等假说,以及由它们发展出的阳极通道、无沉淀区的优先溶解、晶界上粒子大小与间距以及晶界溶质贫乏、晶界富溶质影响钝化膜等子模式。
a.经典的阳极溶解。
即SCC是由于沿晶界优先腐蚀的结果,溶解的可以是晶界本身或晶界上的强化相,也可以是晶界附近的溶质贫乏区。如图4-210a 所示。在这种假说中假定裂纹尖端的扩展受金属与裂纹中介质间化学反应控制。化学反应是热活化过程,其活化能对应力是敏感的,因此当裂纹尖端应力场比较大时,其化学反应也就比较快。阳极溶解是一个电化学过程,必须具备以下先决条件:
在晶界区域分布有连续不断(或部分连续)阳极段;腐蚀介质的选择性作用;拉伸应力加速阳极部分的溶解,并暴露了新的阳极部分。沿着晶界阳极选择性地溶解伴随形成了显微缺口。当此处应力集中高于材料强度极限时就产生了裂纹的扩展;
b.氧化膜(钝化膜)撕裂。
假定SCC是由于晶界钝化膜撕裂引起的,如图4-210b 所示。高强度铝合金的SCC过程包含有裂纹尖端局部塑性变形、撕裂氧化膜、去除氧化膜和金属表面暴露在腐蚀环境中并产生溶解等几个阶段,如图4-211所示。氧化膜被破坏,而破损处相对其他有膜覆盖的表面来说是阳极,金属原子溶解成为离子,形成沟形裂纹。应力集中于裂纹尖端,使附近区域发生塑性变形。这种情况又反过来加快阳极溶解,阻碍膜的再生。同时在裂纹两边的有效应力很快消失,可以再生成膜又成为阴极。这样裂纹在应力作用下,通过电化学过程继续发展,最终导致金属开裂;
c.“阳极通道”模式。
由于铝合金晶界沉淀或晶界区域与晶内有较大电位差(有人测定达100mV),因此就有许多“阳极通道”,SCC就是沿阳极通道腐蚀的过程。由腐蚀产生的微裂纹,在垂直通道的拉应力作用下局部裂纹尖端产生应力集中。应力的作用是张开裂纹、破坏氧化膜、暴露新鲜表面,然后沿新的阳极通道溶解,如此反复进行即形成了SCC。“阳极通道”虽属经典模式,却很好地解释了热处理与抗SCC之间关系,特别是7075–T73比7075-T6有优越的抗蚀性的原因;
图4-210 铝合金SCC基本理论示意图
图4-211 氧化膜撕裂过程示意图
d.“无沉淀区优先溶解”和“晶界上粒子大小、间距”子模式。
沉淀相之间形成无沉淀区(precipitate-free zone,PFZ),PFZ中的溶质浓度小、强度低,在应力作用下首先滑移,钝化膜被撕裂并使PFZ溶解。Al-Zn-Mg合金中SCC速度受晶界处MgZn2粒子在铝固溶体中的溶解量、迁移速度控制。因此,高强铝合金SCC过程就是应力加速晶界处MgZn2粒子间铝固溶体的溶解过程,晶界上粒子越密,抗SCC性就越差。反之,如粒子大而且间距宽,抗蚀性就好。过时效处理正是为获得后一种显微组织;
e.拉伸带不稳定性。
假定在腐蚀裂纹尖端头部能形成一个很薄、尺寸又很小的“自由带”,它能切断开裂的电桥作用。在拉应力作用下这个带能被拉伸到不稳定程度。如果材料在腐蚀介质中,临界应变值就会大大减小,自由带也就很容易被破坏,抗蚀性下降。
自由带围绕较大的非共格粒子形成,自由带尺寸等于粒子间距或者等于晶界沉淀的间距,当过时效使粒子长大,间距加宽时,这个“自由带”也就加宽,抗SCC性随之提高;
f.晶界区溶质偏析假说。
Cu、Mg和Zn 等对Al的电极电位有明显影响,图4-212为这种影响的示意图。Zn、Mg的加入会使Al 的抗蚀性变差,Al-Zn-Mg 合金在固溶处理、时效之后在距晶界 0.5μm区域会产生溶质元素浓度差。在466℃/0.5h 水淬+180℃/0.5h 时效后,晶界处Zn的浓度几乎与晶内一致,随时效时间加长(180℃/7h)晶界处Zn的浓度减少,因此抗蚀性也就提高。Mg的变化也是如此,只是它对抗蚀性的影响比较小一些。
图4-212 添加元素对纯铝电极电位影响
图4-213 在氯化物溶液中裂纹尖端反应
晶界溶质的偏析对抗蚀性影响不仅在对晶界区域电化学特性的改变,更主要的是影响了氧化膜特性。纯铝氧化膜能有效地抵制氯的离解与穿透,但当各种合金元素进入到氧化膜后就大大降低了它的保护性能。
特别是Mg在中性和弱酸性溶液中比纯铝更容易溶解。因此,能使晶界处Zn、Mg浓度减少的热处理对合金的抗蚀性都有利。在Al-Zn-Mg合金中加入Cr 或Cd 时能使晶界处Zn、Mg 含量明显减少,在PFZ 内形成很陡的浓度变化剖面,因此抗SCC性能明显改善。
g.氢脆理论。
假定SCC是由于材料吸附了氢并弱化了晶界而造成的,如图4-210c所示,化学反应产生H是氢脆的先决条件。当Al在氯化物溶液中,其裂纹尖端的反应如图4-213所示。
在拉伸应力作用下,晶界与表面相交处的水分与铝合金反应生成活性原子H。H原子进入晶格中,沿晶界优先偏聚,导致晶界强度下降引起开裂。当合金经过人工时效处理或者在NaC1 溶液中加入HCl及As2O3时,合金的SCC敏感性增加。HCl使腐蚀电流密度和析氢量增加,H在腐蚀反应过程中进入合金中从而造成金属力学性能降低。
氢对SCC有3种机理:
ⅰ。氢能使晶界的结合强度大大降低,弱化晶界,造成晶间断裂。应力的作用是使金属与氢的交换更容易,并促使氢沿晶界扩散。这种理论能很好地解释在真空中已经氢脆材料在应力作用下能保持一段时间,塑性可以恢复,以及脆化了的试样断裂时有氢逸出等现象;
ⅱ。开裂是由氢压力过高造成的。当裂纹尖端的氢一旦达到临界含量,其压力会使金属机械破环,造成裂纹扩展。当空穴中的原子H形成H2时所产生的压力足以使金属开裂;
ⅲ。氢在晶界处降低晶界溶解的活化能,从而使晶界更容易被溶解。
在不同条件下导致SCC的主要作用机制可能发生变化。环境介质、预渗氢时间和极化电位都对SCC有影响。在干燥空气中不发生SCC,而在潮湿空气中发生SCC。在潮湿空气和阳极极化条件下,铝合金的SCC机理是以阳极溶解为主,氢几乎不起作用;延长预渗氢时间可加速铝合金的SCC。在预渗氢或阴极极化条件下,氢脆起主要作用。
从电位方面考虑,在高于临界电位的极化下,合金的SCC 属阳极溶解型,在足够低(<-l000mV SCE)电位下,合金的SCC属氢脆型,中间电位的SCC 属混合型。
晶界沉淀往往作为阳极,使SCC 伴有晶界沉淀优先溶解的倾向。有人认为7xxx 系列铝合金的SCC 机理包含氢脆,原因是SCC对H渗透具有敏感性。而且,在潮湿环境中预充氢使合金延伸率下降。位错、空穴引起的扭曲晶格、固溶体中的Mg和相沉淀等都是合金中H 的陷阱点。
随着应力强度的增加,SCC扩展时,发生了从阳极溶解到氢脆的过渡转变。温度与KISCC间的关系表明,在裂纹扩展第1阶段,主要以阳极溶解模式为主;在裂纹扩展第2阶段,主要是氢脆为主。
综上所述,铝合金SCC机理最基本的是阳极溶解理论和氢脆理论。前者对解释2xxx系合金的SCC更合适,而对7xxx 系合金多用氢导致开裂理论来说明。
除了铝合金SCC的阳极溶解和氢脆2种机理外,有人还提出一些理论[2]:
a.SCC的无位错区模型。当裂纹尖端应力强度因子(Local Stress Intensity Factor)大于临界值ke 时才会在裂纹尖端发射位错,使裂纹尖端前存在DFZ。在这种力的作用下,裂纹沿晶界而不是沿邻近滑移面扩展;
b.“Mg-H”复合体理论。由于7000系铝合金的SCC裂纹扩展一般沿着晶界进行,因此晶界的化学成分必将对合金的SCC行为有重要的影响。晶界Mg偏析,由于Mg和H相互作用而易形成“Mg-H”复合体,氢在晶界上的偏聚将降低晶界的结合能,从而促进了裂纹的扩展。
04 SCC的影响因素
铝合金SCC特征是晶间破裂,这说明铝合金SCC与晶间腐蚀有关。
a.合金元素。
铝中加入合金元素主要是为了获得较高的力学、物理性能或较好的工艺性能,靠合金化的方法显著提高铝耐蚀性能的可能性较小,一般铝合金的耐蚀性很少能超过纯铝。能使铝强化的元素主要有Cu、Mg、Zn、Mn、Si等;补加的元素有Cr、Fe、Ti等;为特殊目的而少量加入的有Be、Bi、B、Pb、Ni、P、Zn、Sn、Sb等。
铝合金的耐蚀性与合金中各种相的电极电位有很大的关系。一般基体相为阴极相,第二相为阳极相的合金有较高的耐蚀性;若基体相为阳极相,第二相为阴极相,则第二相电极电位越高,数量越多,铝合金腐蚀越严重。铝合金中各种常见相的电极电位列于表4-64。
表4-64 铝合金各相在NaCl-H2O2 溶液中的电极电位
由表中数据可见,与纯铝相比,含锌及镁的固溶体为阳极,而含铜的固溶体为阴极;因此,Al-Mg和 Al-Mn 合金具有较高的耐蚀性,而Al-Cu合金耐蚀性能较差。
高强度铝合金抗SCC能力受化学成分和显微组织控制。如Al-Zn-Mg-(Cu)合金峰值时效敏感性比过时效大,而Al-Cu基合金欠时效比峰值时效易发生SCC。
Mg和Zn的含量越多,晶界沉淀越多,PFZ越窄,则SCC 敏感性越大。
添加微量Sc可提高Al合金的耐剥蚀性和力学性能,含Zr的铝合金可提高抗SCC的性能,Al-Li,Al-Li-Zr,Al-Mg-Li-Zr合金抗SCC的能力都很强。高强铝合金中添加质量分数0.05%~0.15% Zr能促进η′相的析出,合金中含有Sc和Zr可加速Al3(Sc1-x,Zrx)和Al3Sc颗粒沉淀,能提高合金的耐蚀性。T76处理的η相颗粒主要以分开的形式排列在晶界处,PFZ狭窄(20nm~35nm),因此可提高强度性能。
Sc、Ni、Ce的加入能净化微结构,阻碍再结晶;而Ni能促进晶格的生长,因此C912系列合金的抗SCC 性有所提高。
Si与Al的电位虽然相差甚远,但在双相合金中抗蚀性能仍然很好,这是由于有氧存在或在氧化介质中,在合金表面生成有保护性的氧化膜缘故;
b.热处理制度的影响[3,4]。
热处理工艺的不同导致了7000 铝合金组织参数的微小变化,其SCC敏感性会发生大幅度波动。常见的热处理工艺主要有固溶处理、时效处理等,而时效处理对合金SCC敏感性影响较大。
峰值时效的影响。峰值时效后,晶界组织对SCC和剥落腐蚀十分敏感。尤其是在有Cl-存在的情况下,厚件的短横向SCC敏感性十分明显。另外,这种状态下存在着严重的Mg偏析,很有可能是由于Mg-H作用导致合金的SCC敏感性较高。
双级时效的影响。双级时效后合金晶界上分布着断续粗大的沉淀相,而这种相是H的陷阱,减少H在晶界上的偏聚,从而降低了合金的SCC敏感性。但这种粗大的相较大幅度地降低合金的强度、塑性等。因此,双级时效并不是降低铝合金SCC敏感性的理想途径。
回归再时效(Retrogression and Re-aging,RRA)处理的7xxx系列铝合金,晶界内的MgZn2保持精细分布,从而降低SCC 敏感性。
“双峰”时效的影响,第二峰状态下合金SCC敏感性低。
在潮湿空气和溶液环境中7xxx 系列峰时效T651的SCC门槛应力最小,SCC最敏感,欠时效T7651次之,过时效T7351耐SCC最好,但强度却下降约10%;
c.预应变的影响。
时效前进行拉伸或压缩变形可以提高合金的SCC抗力。通常冷变形2.5% SCC抗力会增加3-4倍;
d.外部环境对7000系合金SCC敏感性的影响[4-6]。
通常干燥的气体(如H2、N2、O2、Ar等)或干燥空气都不会引起铝合金的SCC,但水蒸气存在的情况下则不然,在水蒸气中通入O2对SCC敏感性有重要影响,7050-T7451合金的SCC敏感性随着O2含量的增加而提高。
水溶液的影响。蒸馏水对铝合金的SCC几乎没有影响。但是当水溶液中的存在Cl-、Br-和I-等离子时则能加速铝合金在溶液中的SCC的裂纹扩展速率。它们引起的SCC的扩展速率比其他阴离子的高2-3个数量级。一般认为Cl-、Br-和I-能加速缝隙腐蚀和晶间腐蚀从而促进了SCC。在水溶液中很少有阳离子对SCC的裂纹扩展产生影响,但是Hg+和H+离子除外。Hg+能引起较快的晶间腐蚀,而很可能因为Hg沉积而引起SCC,H+能够阻止和防止SCC的阴极保护。
A13+通过水解反应生成AlOH2+,AlOH2+再和Cl-反应,又分别生成A1Cl2+和A1(OH)Cl+,然后它们再反复进行水解反应,随着溶液逐渐呈酸性,裂纹表面生成Al(OH)2Cl 和Al(OH)3·H2O 之类的凝胶体物质。裂纹侧壁上一旦形成这类腐蚀生成物的“盐层”,就会发生钝化,溶解反应只能集中在裂纹尖端,保持了裂纹尖端形状的锐利度,具备了所谓由侧壁抑制溶解的“电化学刀的条件”。这不仅是构成阳极溶解机理的前提条件,而且在氢脆机理中又起到H 的吸附和浓化局部介质集中在裂纹尖端的作用。
pH值,对7050-T7451Al 合金在溶氧的3.5%(mass)NaCl溶液中,pH<4 时,钝化膜遭破坏,不能自动修复,晶间腐蚀将促进裂纹形成和长大;4<pH<10时,将产生点蚀,生成裂纹,增加SCC 敏感性;pH>10时,试样遭受均匀腐蚀,极少发生SCC。然而,在去氧的3.5%(mass)NaCl 溶液中,几乎不发生SCC。
05 防止铝合金SCC措施
a.加入微量Mn、Cr、V、Zr等元素,改善SCC性能;
b.用热处理方法调整铝合金的组织状态,减少Zn、Mg在晶界的偏析以及使晶界沉淀 MgZn2 粗糙,颗粒大,减轻基体中晶界附近H原子聚集。晶界内的MgZn2保持精细分布。从而降低SCC 敏感性;
c.采用滚压或喷丸的方法使表面产生压应力,消除表面残余拉应力;
d.表面涂以保护层,隔离腐蚀介质。
06 高强铝合金的SCC测试方法
SCC实验可按GJB1742[7]附录B“铝镁系合金抗应力腐蚀试验方法”进行。实验介质为3.5%(mass)NaCl溶液,实验温度35℃±1℃。剥落腐蚀按附录A“铝镁合金抗剥落腐蚀试验方法”进行。
实验介质: 1.0M NH4Cl,0.25M NH4NO3,0.01M(NH4)3Cit,3g·L-1 H2O2,pH值调至5.2-5.4。温度65℃,实验时间24h。
a.恒载荷法。
该法的SCC评定指标为SCC寿命,还可求出初始应力对SCC的影响;
b.恒应变法。
按照ASTM G44[8],在3.5%(mass)NaCl 溶液中交替浸渍以评定金属和合金的耐SCC性。试样浸渍10min,然后从溶液中取出停放50min,重复上述步骤直至断裂。铝和铁合金一般需要20-90d甚至更长,由合金在盐水中的耐蚀性而定;
ASTM G64[9]为热处理铝合金耐SCC的分类标准。该标准适用于锻造2xx x,6x xx 和7xx x 系列热处理铝合金。试样按ASTM G44交替浸渍,分4个等级进行评定。ASTM G47[10]为高强铝合金产品SCC敏感性的测定方法,适用于高强2xxx(18%-70%(mass)Cu)和7xxx(0.4%-2.8%(mass)Cu)铝合金产品,特别是短横取向(Short Transverse Direction)拉伸试样在恒应变载荷下测定,C形环试样在3.5%(mass)NaCl溶液中交替浸渍测试,其评定方法为宏观裂纹和金相显微分析;
c.SSRT法。
通常使用的应变速率范围为10-4-10-8s-1,持续拉伸使表面钝化膜反复破裂,出现滑移台阶。然后,裸露金属表面发生活化溶解形成裂纹。
d.电子显微镜辅助分析方法。
用扫描电镜分析断口形貌,评定材料的耐SCC性。利用透射电镜可研究材料微观结构与材料SCC性能之间的关系;
E.电导率方法。
电导率可用于材料分类,热处理状态不同,电导率会发生变化,而热处理条件对材料的SCC有影响,因此,电导率可作为评定材料耐SCC性能的指标之一。此法只是一种正在尝试的评定高强铝合金SCC敏感性的辅助方法,因此一般很少采用这种方法;
f.电化学测试方法。
在氯化物水溶液中,时效Ag-Zn-Mg-Cu合金对沿晶环境所致断裂(Environment assisted Cracking,EAC)是敏感的,裂纹生长与电极电位相关。实验结果表明,裂纹生长速度da/dt 随着应用电极电位(Applied Electrode Potential,APP)的增大而增加。
各种SCC测试方法的评价指标如表4-65所示。
表4-65 SCC测试方法的评价指标
案例1.铝合金管材破裂分析[11]
7075-T6铝合金管材使用数月后,发现少数管材破裂。裂纹由表面开始沿受拉应力方向扩展,当裂纹达到一定尺寸后,扩展方向改为沿管材纵向撕裂(以下称主裂纹),如图4-216a 中(l)区和图4-216b 所示。图4-217为主裂纹的断口,其上可见黑色和灰色相间的带状区在断口的匹配面上对称形分布,表明了裂纹的扩展过程。在断口的起始部分和扩展区,表面均有明显的覆盖物。这种断口特征,与SCC断的特征相同。断口表面覆盖物的能谱分析结果如表4-66,可见,覆盖物中有Cl元素的存在。
图4-216 7075-T6 铝合金管材破裂和表面裂纹形貌
图4-217 断口的匹配面上对称形分布
表4-66 断口上覆盖物能谱分析结果
取未完全断开的主裂纹,在表面、纵向和横向3个显微观察,图4-218a 为管材表面裂纹,为连续不断的腐蚀坑和须状的枝叉,延伸部分是被腐蚀显现出的晶界;图4-218b 为主裂纹纵向显微组织,裂纹在扩展过程中伴随腐蚀产物出现,沿着晶界与挤压金属流变相同的方向延伸;图4-218c为主裂纹横向显微组织,其扩展裂纹呈爪状。主裂纹的三向显微组织反映出SCC特征。
图4-218 裂纹扩展形貌和显微组织
测定挤压管材的应力状态,试样长为340~380 mm。将管材的横截面等分为5个区,由测试数据可知,挤压管材在T6 状态下,表面应力分布很不均匀,有1/5的区城为压应力,其他为拉应力,而且最高达22.9 MPa。这种表面状态具备了产生SCC的力学条件。
研究人员将正在发生SCC的试样,迅速投人液氮中冷冻,然后打开裂缝,缓慢溶化,用试纸检验pH 值的变化,结果裂缝尖端内溶液的pH值为3.5。
案例2.5A06铝合金焊接接头裂纹失效分析[12]
5A06铝合金为Al-Mg系防锈铝,具有较高的强度、化学稳定性和良好的焊接性等特点,是防锈铝合金中的典型合金,在一些需严格防火的压力容器等得到了广泛应用。
某5A06防锈铝合金压力容器产品焊接后使用一段时间出现裂纹,裂纹1为横贯焊缝的长裂纹,裂纹2较短,其长度为从内孔边缘到达焊缝处。为了分析裂纹产生的原因,将产生裂纹的壳体和支柱局部取样后进行分析,见图4-219。壳体材料为轧制成型的铝合板,经过卷圆成型;支柱材料经热挤压成型后机械加工而成。
图4-219 试件装配、焊接及裂纹存在部位示意图
壳体与支柱通过焊接连接在一起,其中包括2条焊缝,如图4-215中的外部焊缝和内部焊缝,两焊缝均采用钨极氩弧焊进行焊接。用手工钨极氩弧焊打底,然后采用钨极氩弧焊进行焊接,焊接电流150~160A,电压12~15V。焊缝余高3mm,焊后采用机械加工的方法去除余高并磨平。内部焊缝不开坡口,焊接电流140~150A,电压12~15V。由于结构的影响,内部焊缝采取断续焊接,焊后未做清理。焊后产品整体进行200℃退火处理。
对壳体材料的横截面和轧制面进行了金相组织分析见图4-220。可见壳体组织较细小,晶粒大小不很均匀,平均晶粒尺寸为5~20μm,并且材料中存在一些夹杂物。支柱金相如图4-221所示,可见支柱组织沿挤压方向存在粗大的带状组织。
对外部焊缝进行金相观察,焊缝宏观照片如图4-222所示,a为外部焊缝的整体形貌、b为焊缝熔合区、c为焊缝组织,由图可以发现焊缝组织细小,较为均匀,热影响区组织较粗大。
图4-220 壳体组织(a)横截面(b)轧制面
图4-221 支柱组织(a)挤压方向粗大的带状组织(b)垂直于挤压方向
图4-222 试件焊缝金相照片(a)焊缝全貌(B)熔合区金相照片(c)焊缝金相照片
裂纹的宏观特征如图4-223所示。发现支柱材料中心孔径缺陷处为裂纹源,向壳体方向发展。裂纹呈断续状,穿过材料中的缺陷部位见图4-224,图4-224e可以发现母材晶界存在析出相,为裂纹扩展提供了有利条件;图4-224f可以发现材料中存在缺陷,裂纹会在缺陷处产生并沿着晶界及缺陷的部位进行扩展
图4-223 裂纹扩展方向
图4-224 裂纹扩展特征
将试件沿裂纹1拉断,断口宏观照片如图4-225。图4-225a中可见截面中大部分为陈旧性裂纹,壳体裂纹已通过外部焊缝,支柱裂纹已扩展至下部边缘。支柱断口存在大量的二次裂纹,见图4-225B,可见支柱断口中存在粗大的纤维状,取向明显。壳体断口较细,焊缝及热影响区断口也均匀细致。
图4-225 断口宏观
图4-226a、b为壳体断口微观形貌,晶间存在大量的微观裂纹,结合强度较低,断面有腐蚀产物存在。图4-226c、d为支柱的微观断口形貌,为粗糙的柱状断口,存在二次裂纹和腐蚀坑存在。图4-226c、f为人为断口的微观形貌,断口中以韧性断裂为主,存在大量的撕裂韧窝。
由宏观和微观断口分析可知,裂纹启裂于支柱内孔边缘夹杂物处,并沿径向扩展,粗大的支柱材料组织,晶间结合强度较低,为裂纹扩展提供了条件。
图4-226 断口微观形貌
支柱所处部位决定了内部焊缝只能断续焊接,存在应力集中。装配过程中,支柱圆弧面与壳体的圆弧面配合出现偏差,造成两试件间距有较大的偏差,焊后产生较大的应力集中。裂纹均起源于焊缝端部,产生微裂纹后,在应力集中的作用下,引起裂纹的扩展。
5A06铝合金焊后在280~305℃进行完全退火,可以消除残余应力。支柱与壳体焊接后,产品整体进行了200℃的退火处理,因此,设备焊接后进行的整体退火温度偏低,未使焊接残余应力彻底释放也会引起裂纹的产生。
参考文献
[1] 赵英涛。铝合金应力腐蚀开裂假定机理的文献综述[J].材料工程,1993,44(9):1-6
[2] 袁劲松,秦熊浦。 铝锂合金的应力腐蚀特征[J].腐蚀与防护,1999, 20(9):389-391
[3] 孙志华,刘明辉,张晓云。时效制度对 Al-Zn-Mg-Cu铝合金应力腐蚀敏感性的影响[J].中国腐蚀与防护学报,2006,26(4):232-236
[4] 陈小明,宋仁国。7000系铝合金应力腐蚀开裂的研究进展[J].腐蚀科学与防护技术,2010,22(2):120-123
[5] 刘继华,李 荻,张佩芬。氢对LC4高强铝合金应力腐蚀断裂的影响[J].中国腐蚀与防护学报,22(5):53-55
[6] 杜爱华,龙晋明,裴和中。等。高强度铝合金应力腐蚀研究进展[J].中国腐蚀与防护学报,2008,28(4):251-256
[7] GJB 1742-1993.舰用LF15、LF16铝合金板材规范[S]
[8] ASTM G44-1999(2013)。Standard Practice for Exposure of Metals and Alloys by Alternate Immersion in Neutral 3.5 % Sodium Chloride Solution[S]
[9] ASTM G64-1999(2013)。Standard Classification of Resistance to Stress-Corrosion Cracking of Heat-Treatable Aluminum Alloys[S]
[10] ASTM G47-2020. Standard Test Method for Determining Susceptibility to Stress-Corrosion Cracking of 2XXX and 7XXX Aluminum Alloy Products[S]
[11] 侯绎,张锡龙。 7075 铝合金T6 状态管材破裂分析[J].轻合金加工技术,2002,30(11):42-45
[12] 张红霞,刘晓晴,闫志峰。等。 5A06铝合金焊接接头裂纹失效分析[J].材料工程,2013,64(3):27-31+37
免责声明:本网站所转载的文字、图片与视频资料版权归原创作者所有,如果涉及侵权,请第一时间联系本网删除。
相关文章
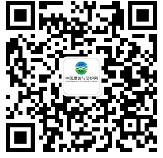
官方微信
《中国腐蚀与防护网电子期刊》征订启事
- 投稿联系:编辑部
- 电话:010-62316606-806
- 邮箱:fsfhzy666@163.com
- 中国腐蚀与防护网官方QQ群:140808414
点击排行
PPT新闻
“海洋金属”——钛合金在舰船的
点击数:7130
腐蚀与“海上丝绸之路”
点击数:5741