摘要
采用电化学工作站和透射电镜等对含硫化物夹杂的铁基非晶合金进行了电化学腐蚀行为及腐蚀形貌分析。结果表明,铁基非晶合金的含硫化物夹杂为Al2S3和Al57Mn12。在FeCl2溶液中表现出明显的钝化现象,腐蚀速率随溶液浓度的升高而升高;夹杂物周围贫Cr区的钝化膜薄弱,是点蚀萌生的位置;Al和Mn在FeCl2溶液中优先溶解使夹杂处形成蚀坑,在较高的浓度下蚀坑中会因自催化效应进一步腐蚀生成次生孔。
关键词: 铁基非晶合金 ; 硫化物夹杂 ; 耐蚀性能 ; 点蚀
非晶合金也称金属玻璃,是一种微观结构短程有序长程无序的复杂结构体系[1,2],能量处在亚稳态,同时拥有玻璃和金属的很多特征而具备优越的力学和物理性能,在科研生产中逐步发展成一种不可或缺的工程材料[3-5]。已发现的块体非晶合金按合金体系有Mg、Zr、Cu、Ni、Fe基等分类[6]。其中铁基非晶合金相比于其他合金具有优异的耐磨性、耐蚀性、硬度和优异的软磁性[7-9],且原材料丰富,制备工艺成熟,是目前应用最广泛的非晶合金之一[10,11]。
在块体铁基非晶合金的研究中,往往通过采用高纯度原材料或添加稀土元素的方法制备大块铁基非晶合金,如Li等[12]采用多组元类金属添加剂的途径,用铁合金、纯铁接近于工业应用条件制备出的Fe67.7C7.0Si3.3B5.5P8.7Cr2.3Mo2.5Al2.0Co1非晶合金,并发现掺杂合金元素的最佳含量与合金的电负性有很大的相关性;Liu等[13]通过添加稀土元素微量合金化研制出12 mm的非晶钢,为了降低生产成本,科研工作者使用廉价工业原料制备铁基非晶合金[14,15]。然而,工业原料中的硫元素会在铁基非晶合金中形成硫化物夹杂,引起非晶合金成分和结构的均匀性变化进而影响其耐蚀性[16]。
化学成分是决定材料腐蚀性能的主要因素,适度添加Cr、Mo、Mn、P等[17]钝化元素能促进合金的自发钝化,进而改善耐蚀性能[18],国内外铁基非晶合金的耐蚀性研究都表明铁基非晶合金的优异耐蚀性与独特的无序结构和均匀的化学成分密切相关[19,20]。Zhang等[21]认为孔隙贯通是导致铁基非晶基体优先腐蚀的主要原因。Botta等[22]和王允等[23]研究表明,块体铁基非晶合金在HCl、NaCl和NaOH溶液中具有良好的抗腐蚀性,且Cr可以提高铁基非晶合金的耐蚀性。Liu等[24]和NaKa等[25]认为P、C、B、Si等类金属元素和稀土元素Y等影响合金表面富Cr保护膜的形成速率。Zhang等[26]观察到非晶涂层点蚀起始点发生于界面层边缘,数量随远离界面层的距离增加而减小,与Cr含量在界面层附近的变化趋势一致。一般认为Cl-是导致铁基非晶合金点蚀的激发剂[27],Li等[28]研究了钝化膜局部击穿理论,表明侵蚀性强的Cl-进入亚稳态蚀坑后吸附和积累,加速氧化膜的局部溶解和击穿。因此,可以确定Cl-则是导致腐蚀发生的因素,Cr是铁基非晶合金耐蚀性的关键元素,类金属元素也是通过影响Cr保护膜的形成影响铁基非晶合金的耐蚀性。
一般认为非金属夹杂物是诱发点蚀的最主要因素[29,30],在国内外铁基材料的研究中,硫化物夹杂影响不锈钢点蚀行为的研究较多,而对铁基非晶合金耐蚀性影响的研究很少,Cl-影响铁基非晶合金耐蚀性的研究主要集中在NaCl溶液方向[27,28],对FeCl2溶液的研究鲜有报道。Wang等[31]认为Cl-和S2-会诱发含氧化物夹杂铁基非晶合金的点蚀;Rossi等[32]检测到不锈钢的含硫夹杂物不受钝化膜覆盖,是潜在的点蚀坑;李丽等[16]认为MnS夹杂物与钢基体间存在缝隙,其诱导点蚀形核包括缝隙腐蚀和夹杂物溶解两个过程;武会宾等[33]发现MnS、TiO2等不同类型夹杂物在酸性环境中优先溶解,且MnS优先溶解,长宽比大的夹杂物优先诱发点蚀。
国内外关于夹杂物对铁基非晶合金腐蚀行为的影响的研究很少,主要集中在不同环境介质中的耐蚀能力和非晶合金成分对腐蚀性能的影响,而没有对点蚀行为的过程和机理进行详细的解释。尽管含硫化物夹杂铁基非晶合金的点蚀行为与不锈钢类似,但其模型需要进一步研究才能明确。
1 实验方法
按照表1的配比采用真空电弧熔炼炉将工业原材料制备为Fe66.6C7.1Si3.3B5.5P8.7Cr2.3Mo2.5Al2.0Co1.0S1.0合金锭,表中所示元素的纯度均在95%以上,每个合金锭在电弧熔炼炉内多次熔炼以保证合金锭成分均匀。采用水冷铜模吸铸法制备直径2 mm的非晶合金棒状样品,利用精密切割机将样品切成长度20 mm左右的若干段。
表1 工业原材料的化学成分[10]
通过X射线衍射仪 (XRD,Beuker-Axs D&ADVANCE,Cu Kα) 对试样结构表征,采用差示扫描量热分析 (DSC,Perkin-Elmer DSC7) 测量铁基非晶合金的DSC曲线,得出非晶的玻璃转变温度和初始结晶温度等。将试样分别在0.5、1、2、4 mol/L的FeCl2溶液中进行浸泡实验,利用扫描电镜 (SEM,S-3400N) 观察浸泡前试样断口处夹杂物的形貌和试样浸泡过程中的形貌变化,浸泡结束后清理表面腐蚀产物,计算试样质量损失,取平均值计算腐蚀速率。利用透射电镜 (TEM,TecnaiG2 F20 S-TWIN) 和能谱仪 (EDS,S-2500C) 分析夹杂物及周围区域的成分变化,通过Digital Micrograph标定电子衍射图分析夹杂物成分。
采用CHI650E电化学工作站对铁基非晶合金试样进行电化学腐蚀实验。三电极系统,辅助电极为Pt、参比电极为饱和甘汞电极SCE、工作电极为待测试样,保持30 min使开路电位保证在一定范围内。测试扫描速率为1 mV/S,分别在不同浓度FeCl2溶液 (0.5、1、2、4 mol/L) 下进行。在不同溶液浓度下选择钝化区间内的电位 (0.5 V) 极化进行3 h的恒电位极化测试,采样周期为200 ms。采用SEM观察1和0.5 mol/L的阳极极化测试后的试样表面腐蚀形貌。把试样浸入1 mol/L的FeCl2溶液中1 h后,通过TEM观察夹杂物溶解后的形貌,并通过能谱仪分析成分变化。
2 实验结果
对铁基非晶合金铸棒的微观结构进行表征,图1的XRD分析显示约在2θ=44°存在一条宽漫散射峰,未出现尖锐的结晶衍射峰;DSC曲线上存在3个明显晶化放热峰,铁基非晶的玻璃转化温度Tg约为480 ℃,初始晶化温度Tx约为510 ℃,表明实验制备的铁基非晶合金铸棒为完全非晶态。
图1 铁基非晶铸棒微观结构分析
试样的微观分析结果如图2所示,非晶基体成形良好,结构致密,无明显晶界;基体灰色衬度均一,漫散射晕环表明基体完全非晶态。但基体间随机分布直径约2 ?m的球形夹杂物,EDS表明含有Al-Mn-S成分,电子衍射存在2套衍射斑点,标定结果为晶面间距0.3025 nm、0.3021 nm的Al2S3和0.7738 nm、0.4647 nm的Al57Mn12。在铁基材料的凝固过程中,S往往以硫化物的形式偏析形成夹杂,如不锈钢中的MnS[16,32],但非晶中较高的Al含量影响了夹杂物的构成成分。根据热化学手册[34]和金属间化合物标准生成焓估算模型[35],MnS、Al2S3和Al57Mn12的标准摩尔生成焓分别为-52.2,-173和-1145.988 kJ/mol,因此相同条件下非晶体系趋向于生成自由能更低、对热更稳定的Al2S3夹杂物。在快速冷却时,剩余的Al趋向于和Mn形成Al57Mn12亚稳相[36],这种亚稳态金属间化合物有利于非晶合金体系保持热力学稳定。
图2 铁基非晶合金微观SEM、TEM形貌及A区基体电子衍射图,B区夹杂物EDS分析及电子衍射图标定
电化学实验表明,不同浓度的动电位极化曲线具有相似的活化区、钝化区和过钝化区,如图3所示。在-750 mV附近时动电位极化曲线均发生代表活性溶解的明显突变,自腐蚀电流由0.5 mol/L的46.77 μA·cm-2增至4 mol/L时的316.22 μA·cm-2,增大了1个数量级。钝化区随浓度增加逐渐变窄,维钝电流Ipass由0.5 mol/L的13.18 μA·cm-2增至4 mol/L时的398.10 μA·cm-2,增大了30倍。电流暂态峰意味着钝化膜的溶解和再钝化,低浓度时暂态峰不明显,浓度为2 mol/L后开始出现显著的电流暂态峰,点蚀电位可以通过暂态峰开始出现时的电位进行判断,由0.5 mol/L的1250 mV逐渐减小为4 mol/L时的80 mV。可见随浓度增加试样整体耐蚀性与抵抗点蚀的能力均降低,电化学实验具体参数如表2所示。
图3 铁基非晶合金在不同浓度FeCl2溶液中的极化曲线
表2 铁基非晶合金在不同浓度的FeCl2溶液中动电位极化实验的电化学参数
取所有试样处于钝化区的0.5 V为初始电位进行恒电位极化测试,初始阶段不同浓度的腐蚀电流均随时间大速率下降,之后维持在相对稳定位置,但浓度为4 mol/L时电流密度显著较大,表明试样在高浓度腐蚀介质中耐蚀能力下降。电流暂态峰代表点蚀,电流瞬变意味着局部钝化膜的破裂导致点蚀的萌生[37],低浓度时恒电位曲线无暂态峰,4 mol/L时出现大量明显暂态峰,极化测试末期的密集暂态峰表明试样在高浓度腐蚀介质中点蚀严重,形式可能为孔隙贯通[21],反映了点蚀的萌生和扩散的早期阶段[38]。
在不同浓度FeCl2溶液中浸泡试样,浸泡初期试样表面活性较高,腐蚀速率较大,试样表面发生钝化后,腐蚀受到抑制,腐蚀速率逐渐下降直至基本稳定 (如图4),随浓度增加试样的腐蚀速率逐渐增大。根据赵阳等[39]的Icorr-v转化关系公式计算腐蚀速率v:
图4 铁基非晶合金在不同浓度FeCl2溶液中的腐蚀速率
式中,Icorr为腐蚀电流密度 (μA·cm-2),n为每摩尔Fe2+转移电子数,M为Fe2+的相对原子质量 (g/mol)。电化学实验作为加速腐蚀实验,通过Icorr计算所得理论腐蚀速率略高于图4所示的浸泡实验腐蚀速率。图5展示了腐蚀形貌的变化,铁基非晶合金表面存在直径约为1 ?m的圆形夹杂物,边缘呈白色亮线与基体分隔开。浸泡过程中表面产生腐蚀产物,白色边缘线消失,夹杂物溶解成为点蚀坑后向周围扩展,每组测试的腐蚀过程基本相同,但4 mol/L时腐蚀产物明显较多。夹杂物为中心的四方形区域是SEM的电子辐照区,一般认为SEM电子辐照后样品耐蚀性会增强[40,41],因此腐蚀初期该区域内未出现点蚀坑的扩展,9 d之后辐照区也开始产生点蚀坑。15 d时试样均出现大面积的点蚀坑,4 mol/L条件下蚀坑密集且数量最多。
图5 铁基非晶合金在不同浓度FeCl2溶液中浸泡后的腐蚀形貌
TEM微观形貌如图6所示,沿A方向线扫描结果表明,夹杂物区存在Al-Mn-S的富集,而Fe、Cr的含量低于基体部分,在夹杂物周围形成贫Cr区域。在4 mol/L的FeCl2溶液中浸泡试样1 h后,基体表面平整度未发生明显变化,半圆形夹杂物的衬度发生明显变化,EDS表明,原本夹杂物中的Al、Mn已被溶解而只残余S,且B区电子衍射呈现漫散射晕环,表明残余夹杂物为非晶态。
图6 在4 mol/L浓度下浸泡1 h后铁基非晶合金微观形貌分析
对动电位阳极极化后的工作电极进行观察,腐蚀形貌如图7所示,可见高浓度时蚀孔数量多于低浓度,且分布密集。在0.5 mol/L时,通过夹杂物及周围基体的部分溶解,蚀孔已达到50 μm;1 mol/L时残余基体进一步溶解,部分蚀孔可达100 μm,蚀孔内部仍未出现二次蚀孔;2 mol/L时残余基体完全溶解,蚀孔中开始出现二次蚀孔;4 mol/L时电极表面平整度严重恶化,蚀孔发生扩展后相互接触,内部存在大量二次蚀孔。可知在低浓度时,蚀孔内壁的Cr等钝化元素可以维持钝化膜的形成和再钝化,而高浓度时,钝化膜的溶解速度大于钝化膜的生成速度,蚀孔内壁成为非晶基体发生进一步点蚀的优先位置[21]。
图7 极化实验后工作电极表面的SEM形貌
3 讨论
金属的腐蚀受金属本身的成分结构和腐蚀介质状态影响。铁基非晶合金的高耐蚀性主要归因于其均匀的化学成分和组织结构[19,20],化学成分均匀无偏析,同时没有晶界和位错等易引发腐蚀的诱因[11],而且Cr、Mo、Mn等钝化元素在表面形成钝化膜[18],P、C、B、Si等类金属元素影响钝化膜的形成速率[24,25],增强了铁基非晶合金的耐蚀性。然而工业原料制备的铁基非晶合金中引入了S,在基体中生成含硫化物的夹杂,破坏了铁基非晶原有的结构均匀性[32];同时S在固态钢中的溶解度远远小于在液态钢中的溶解度,非晶体系快速凝固过程中S倾向于与Al、Mn元素形成夹杂物[42],造成Al-Mn-S在区域内相对富集,Fe、Cr、Mo等相对含量低,严重降低了成分均匀性,使夹杂物成为点蚀诱因[29,30]。点蚀数量与Cr含量在界面层附近分布规律一致[26],铁基非晶中Cr、Mo是影响耐蚀性的关键元素[42,43],一方面Cr、Mo作为钝化元素,其含量直接影响表面钝化膜形成,另一方面Cr含量会增加电化学化学势,Mo可以促进钝化膜溶解后的再形成[11,42],EDS结果也证明夹杂物区域贫Cr,使夹杂物相对于基体具有显著低电势,钝化膜更容易受到腐蚀介质破坏,优先溶解破裂[32],将晶态的夹杂物暴露在腐蚀介质中,引发夹杂物溶解形成点蚀坑[33]。
腐蚀介质的状态也会影响铁基非晶合金的耐蚀性,如侵蚀性Cl-会降低钝化膜的离子电阻,导致钝化膜的化学溶解速度远大于形成钝化膜的速度,从而使钝化膜中Cr、Mo、Fe的氧化物发生溶解,以离子的形式进入溶液中[27,28]。在电化学实验中,随Cl-浓度增加,动电位极化曲线的钝化区变窄,自腐蚀电流Icorr增加,非晶合金的整体耐蚀性下降,高浓度时动电位极化曲线和恒电位极化曲线上都出现了明显的电流暂态峰,非晶合金出现了大量的点蚀。亚稳态点蚀是腐蚀初期的点蚀形式,数量与电流暂态峰呈正相关,归因于点蚀坑内溶解速率对化学成分的依赖性和腐蚀产物的扩散速率[46]。当亚稳态蚀孔因Cr、Mo等钝化元素再钝化作用抑制了溶解,便不足以出现稳定点蚀[44],当腐蚀速率超出非晶合金的再钝化能力,亚稳态蚀坑便转变为稳态点蚀。结合浸泡实验结果可知,腐蚀初期夹杂物优先溶解,腐蚀速率剧增[45],形成稳定点蚀坑后Cr、Mo等钝化元素在表面形成氧化物或氢氧化物钝化膜抑制了进一步腐蚀[17],腐蚀速率趋于平稳。
结合浸泡实验后夹杂物的微观形貌及成分分析,含硫夹杂物中Al和Mn优先溶解使夹杂物处溶解形成点蚀坑,剩余的S以非晶态形式存在。根据电化学原理,点蚀坑内部处于活化状态成为阳极,孔外表面因钝化膜电位较高作为阴极,形成了活化钝化电池使蚀孔加速腐蚀,这与不锈钢的自催化腐蚀现象相似[21]。因此,剩余含硫化物的夹杂完全溶解后,蚀孔内部的腐蚀形式便从晶态夹杂物的溶解转变为基体上亚稳态小孔的萌生。在较低浓度时,Cl-的浓度对钝化膜的加速溶解作用不足以打破亚稳态小孔与稳态小孔的平衡,此时孔内与孔外具有近似的电势,于是孔内未出现次生孔 (图8a,b)。在较高的浓度下,Cl-在蚀孔内大量富集,Cr、Mo等钝化元素的含量不足以维持钝化膜的形成和再钝化,亚稳态小孔出现后便因为自催化效应加速腐蚀,次生孔便在蚀孔内出现并进一步发展 (图8c,d)。
图8 含硫化物夹杂的铁基非晶合金在FeCl2溶液中的点蚀萌生和发展示意图
因此提出如图8所示的铁基非晶点蚀萌生和发展的模型,铁基非晶中随机分布成分为Al2S3和Al57Mn12的球状夹杂物。夹杂物处的贫Cr程度以及夹杂物暴露在外的尺寸共同决定其溶解的优先次序。钝化膜往往以Fe2O3和Cr2O3的形式存在,侵蚀性Cl-对金属具有较强的吸附能力[47,48],发生反应[11]:
阳极:
阴极:
如图8b所示,Fe和Cr以离子形式溶解,导致钝化膜破裂。夹杂物具有更低的电化学势,Al、Mn选择性优先溶解,如图8c。剩余的S以非晶态形式残留,夹杂物的溶解形成点蚀坑,孔内的活化环境与孔外表面的钝化膜存在电位差,形成大阴极小阳极的原电池,自催化加速腐蚀,同时Cl-在蚀孔内的富集抑制了O2与蚀坑内壁基体中钝化元素的接触,进而抑制了再钝化,在夹杂物形成的点蚀孔内部形成如图8d的二次蚀孔。
4 结论
(1) 采用工业原材料制备出的铁基非晶合金中所含的夹杂物为球状Al2S3和Al57Mn12。
(2) 随着FeCl2溶液浓度的增加,铁基非晶合金的耐蚀性下降,自腐蚀电流由2 mol/L的52.48 μA·cm-2增大为4 mol/L时的316.22 μA·cm-2,点蚀在浓度达到1 mol/L时开始萌生,点蚀电位从1 mol/L时的980 mV降为4 mol/L时的80 mV,再钝化能力也随之下降。
(3) 铁基非晶合金的点蚀产生于表面夹杂物周围的贫Cr区,该区钝化膜比较薄弱优先发生溶解。钝化膜破裂后夹杂物中的Al、Mn元素选择性溶解,而残留下的S变成非晶态。Cl-在夹杂物溶解形成后的蚀孔中富集,蚀孔内壁将进一步自催化产生二次蚀孔。
参考文献
1 Chen H S, Formation Turnbull D., stability and structure of palladium-silicon based alloy glasses [J]. Acta Metall., 1969, 17: 1021
2 Wang Y H, Yang Y S. Amorphous Alloys [M]. Beijing: Metallurgical Press, 1989: 135
2 王一禾, 杨膺善. 非晶态合金 [M]. 北京: 冶金工业出版社, 1989: 135
3 Wang G, Xiao P, Huang Z J, et al. Microstructure and wear properties of Fe-based amorphous coatings deposited by high-velocity oxygen fuel spraying [J]. J. Iron Steel Res. Int., 2016, 23: 699
4 Li D Y, Chen X Y, Hui X D, et al. Effect of amorphicity of HVOF sprayed Fe-based coatings on their corrosion performances and contacting osteoblast behavior [J]. Surf. Coat. Technol., 2017, 310: 207
5 Wang W, Zhang C, Xu P, et al. Enhancement of oxidation and wear resistance of Fe-based amorphous coatings by surface modification of feedstock powders [J]. Mater. Des., 2015, 73: 35
6 Wang L Q, Zhai S Q, Ding R, et al. Recent development of bulk amorphous alloys [J]. Found. Technol., 2017, 38: 274
6 王立强, 翟慎秋, 丁锐等. 大块非晶合金研究进展 [J]. 铸造技术, 2017, 38: 274
7 Huang Y. Corrosion resistance and pitting initiation mechanism of Fe-based bulk metallic glass with sulfide inclusions [D]. Nanchang: Nanchang Hangkong University, 2017
7 黄勇. 含硫化物夹杂铁基块体非晶合金耐蚀性能及点蚀萌生机理 [D]. 南昌: 南昌航空大学, 2017
8 Chen Q J, Jiang W, Gao J W. Effect of relative density difference between coating and bulk on Fe-based amorphous alloys corrosion resistance [J]. Chin. J. Nonferrous Met., 2015, 25: 2414
8 陈庆军, 蒋薇, 高霁雯. 涂层与块体致密度差值对铁基非晶合金耐蚀性的影响 [J]. 中国有色金属学报, 2015, 25: 2414
9 Wang A D, Zhao C L, Men H, et al. Fe-based amorphous alloys for wide ribbon production with high Bs and outstanding amorphous forming ability [J]. J. Alloy. Compd., 2015, 630: 209
10 Wang S L, Cheng J C, Li C X, et al. Precipitation of sulfide particle in situ formed in Fe-based bulk metallic glass [J]. Foundry, 2013, 62: 491
10 王善林, 成京昌, 李承勋等. 大块铁基非晶中硫化物析出行为研究 [J]. 铸造, 2013, 62: 491
11 Gong Y B. Fabrication, anti-corrosion and wear-resistance properties of Fe-based amorphous coatings by HVOF [D]. Nanchang: Nanchang Hangkong University, 2017
11 龚玉兵. 铁基非晶涂层HVOF制备及耐蚀耐磨性能研究 [D]. 南昌: 南昌航空大学, 2017
12 Li X, Qin C L, Kato H, et al. Mo microalloying effect on the glass-forming ability, magnetic, mechanical and corrosion properties of (Fe0.76Si0.096B0.084P0.06)100-xMox bulk glassy alloys [J]. J. Alloy. Compd., 2011, 509: 7688
13 Lu Z P, Liu C T, Thompson J R, et al. Structural amorphous steels [J]. Phys. Rev. Lett., 2004, 92: 245503
14 Li H X, Lu Z P, Yi S. Estimation of the glass forming ability of the Fe-based bulk metallic glass Fe68.8C7.0Si3.5B5.0P9.6Cr2.1Mo2.0Al2.0 that contains non-metallic inclusions [J]. Met. Mater. Int., 2009, 15: 7
15 Li H X, Gao J E, Jiao Z B, et al. Glass-forming ability enhanced by proper additions of oxygen in a Fe-based bulk metallic glass [J]. Appl. Phys. Lett., 2009, 95: 161905
16 Li L, Luo X B, Chai F, et al. Effect of sulfur on pitting corrosion behavior of hull steel [J] Contin. Cast., 2017, 42(2): 7
16 李丽, 罗小兵, 柴锋等. 硫质量分数对船体钢诱发点蚀行为的影响研究 [J]. 连铸, 2017, 42(2): 7
17 Wang Y, Zheng Y G, Wang J Q, et al. Passivation behavior of Fe-based amorphous metallic coating in NaCl and H2SO4 solutions [J]. Acta Metall. Sin., 2015, 51: 49
17 王勇, 郑玉贵, 王建强等. 铁基非晶涂层在NaCl和H2SO4溶液中的钝化行为 [J]. 金属学报, 2015, 51: 49
18 Wang L, Chao Y S. Corrosion behaviors of bulk amorphous Fe41Co7Cr15Mo14C15B6Y2 alloy in NaOH solution [J]. J. Funct. Mater., 2010, 41: 1849
18 王莉, 晁月盛. 铁基块体非晶合金在NaOH溶液中的腐蚀行为 [J]. 功能材料, 2010, 41: 1849
19 Guo S F, Pan F S, Zhang H J, et al. Fe-based amorphous coating for corrosion protection of magnesium alloy [J]. Mater. Des., 2016, 108: 624
20 Guo S F, Lai L M, Ding K L, et al. Construction and corrosion behaviour of amorphous coating on magnesium alloy [J]. Surf. Technol., 2019, 48(3): 40
20 郭胜锋, 赖利民, 丁凯露等. 镁合金表面非晶涂层的构筑及其腐蚀行为 [J]. 表面技术, 2019, 48(3): 40
21 Zhang S D, Zhang W L, Wang S G, et al. Characterisation of three-dimensional porosity in an Fe-based amorphous coating and its correlation with corrosion behaviour [J]. Corros. Sci., 2015, 93: 211
22 Botta W J, Berger J E, Kiminami C S, et al. Corrosion resistance of Fe-based amorphous alloys [J]. J. Alloy. Compd., 2014, 586: S105
23 Wang Y, Luo Q, Qiao J, et al. The corrosion behavior of Fe-based amorphous alloy coating in sodium chloride solution [J]. Metall. Funct. Mater., 2015, 22(1): 1
23 王允, 罗强, 焦津等. 铁基非晶合金涂层在氯化钠溶液中的腐蚀行为研究 [J]. 金属功能材料, 2015, 22(1): 1
24 Liu G, An Y L, Guo Z H, et al. Structure and corrosion behavior of iron-based metallic glass coatings prepared by LPPS [J]. Appl. Surf. Sci., 2012, 258: 5380
25 Naka M, Hashimoto K, Masumoto T. Corrosion resistivity of amorphous iron alloys containing chromium [J]. J. Japan Inst. Met., 2004, 38: 835
26 Zhang C, Chan K C, Wu Y, et al. Pitting initiation in Fe-based amorphous coatings [J]. Acta Mater., 2012, 60: 4152
27 Meng Q G, Li J G, Tan N. Effect of PH on corrosion behaviors of Pr60Fe30Al10 BMG and ITS crystalline couterpart in NaCl solution [J]. Rare Met. Mater. Eng., 2007, 36: 71
27 孟庆格, 李建国, 谭宁. pH值对块体非晶Pr60Fe30Al10在NaCl溶液中的腐蚀行为影响 [J]. 稀有金属材料与工程, 2007, 36: 71
28 Li Z, Zhang C, Liu L. Wear behavior and corrosion properties of Fe-based thin film metallic glasses [J]. J. Alloy. Compd., 2015, 650: 127
29 Qin H P, Chen H T, Lang Y P, et al. Mechanism of induced pitting corrosion in 439M ferritic stainless steel [J]. Iron Steel, 2015, 50(9): 81
29 覃怀鹏, 陈海涛, 郎宇平等. 439M铁素体不锈钢点蚀诱发机理 [J]. 钢铁, 2015, 50(9): 81
30 Zhang C Y, Zhang Q, Li J G, et al. Micro-corrosion test research on pitting initiation site of the inclusions of carbon steel and low alloy steel in chlorine ion solution [J]. Metall. Anal., 2014, 34(1): 22
30 张春亚, 张奇, 李继高等. 碳钢及低合金钢在氯离子溶液中夹杂物诱发点蚀位置显微腐蚀实验探讨 [J]. 冶金分析, 2014, 34(1): 22
31 Wang Y, Li M Y, Zhu F, et al. Pitting corrosion mechanism of Cl- and S2- induced by oxide inclusions in Fe-based amorphous metallic coatings [J]. Surf. Coat. Technol., 2020, 385: 125449
32 Rossi A, Elsener B, H?hner G, et al. XPS, AES and ToF-SIMS investigation of surface films and the role of inclusions on pitting corrosion in austenitic stainless steels [J]. Surf. Interface Anal., 2000, 29: 460
33 Wu H B, Wang D, Liang J M, et al. Influence of inclusion on pitting corrosion behavior of low-alloy steel for bottom plates of cargo oil tanks [J]. Trans. Mater. Heat Treat., 2014, 35(12): 172
33 武会宾, 王迪, 梁金明等. 夹杂物对低合金钢在酸性Cl-溶液环境中点蚀行为的影响 [J]. 材料热处理学报, 2014, 35(12): 172
34 Barin I. Thermochemical Data of Pure Substances [M]. Beijing: Science Press, 2003: 1055
34 Barin I. 纯物质热化学数据手册 [M]. 北京: 科学出版社, 2003: 1055
35 Zhao D G, Guo P M, Zhao P. Estimating model of standard enthalpy of intermetallics [J]. J. Central South Univ. (Sci. Technol.), 2011, 42: 1578
35 赵定国, 郭培民, 赵沛. 金属间化合物的标准生成焓估算模型 [J]. 中南大学学报 (自然科学版), 2011, 42: 1578
36 Hu Z L. The formation and mechanical properties of icosahedral quasicrystal in rapidly solidified Al-Mn-(Be) alloy [D]. Harbin: Harbin Institute of Technology, 2013
36 胡仲略. 快速凝固Al-Mn- (Be) 合金准晶形成及力学性能 [D]. 哈尔滨: 哈尔滨工业大学, 2013
37 Burstein G T, Liu C, Souto R M, et al. Origins of pitting corrosion [J]. Corros. Eng. Sci. Technol., 2004, 39: 25
38 Zhang S D, Wang Z M, Chang X C, et al. Identifying the role of nanoscale heterogeneities in pitting behaviour of Al-based metallic glass [J]. Corros. Sci., 2011, 53: 3007
39 Zhao Y, Zhou E Z, Liu Y Z, et al. Comparison of different electrochemical techniques for continuous monitoring of the microbiologically influenced corrosion of 2205 duplex stainless steel by marine Pseudomonas aeruginosa biofilm [J]. Corros. Sci., 2017, 126: 142
40 Jiang N. Beam damage by the induced electric field in transmission electron microscopy [J]. Micron, 2016, 83: 79
41 Zhang H R, Egerton R, Malac M. Electron irradiation damage and color centers of MgO nanocube [J]. Nucl. Instrum. Methods Phys. Res., 2013, 316B: 137
42 Li H X, Xu F G, Wang S L, et al. Effect of molybdenum on electrochemical properties of bulk metallic glass Fe71.2-xC7.0Si3.3B5.5P8.7Cr2.3Al2.0Mox [J]. Foundry, 2010, 59: 145
42 李宏祥, 许凤光, 王善林等. Mo对铁基块体非晶合金Fe71.2-xC7.0Si3.3B5.5P8.7Cr2.3Al2.0Mox腐蚀性能的影响 [J]. 铸造, 2010, 59: 145
43 Guo S F, Chan K C, Xie S H, et al. Novel centimeter-sized Fe-based bulk metallic glass with high corrosion resistance in simulated acid rain and seawater [J]. J. Non-Cryst. Solids, 2013, 369: 29
44 Cao C N. Principles of Electrochemistry of Corrosion [M]. 3rd Ed. Beijing: Chemical Industry Press, 2008: 165
44 曹楚南. 腐蚀电化学原理 [M]. 第3版. 北京: 化学工业出版社, 2008: 165
45 Li Y, Lin H C, Cao C N. Corrosion interface morphology and fractal analysis of amorphous alloys in air [J]. J. Chin. Soc. Corros. Prot., 1998, 18: 257
45 李瑛, 林海潮, 曹楚南. 自然大气中非晶合金腐蚀界面的微观形貌特征与分维数分析 [J]. 中国腐蚀与防护学报, 1998, 18: 257
46 Ernst P, Laycock N J, Moayed M H, et al. The mechanism of lacy cover formation in pitting [J]. Corros. Sci., 1997, 39: 1133
47 Wang Y, Jiang S L, Zheng Y G, et al. Effect of processing parameters on the microstructures and corrosion behaviour of high-velocity oxy-fuel (HVOF) sprayed Fe-based amorphous metallic coatings [J]. Mater. Corros., 2013, 64: 801
48 Zhou Z, Wang L, He D Y, et al. Microstructure and wear resistance of Fe-based amorphous metallic coatings prepared by HVOF thermal spraying [J]. J. Therm. Spray Technol., 2010, 19: 1287
免责声明:本网站所转载的文字、图片与视频资料版权归原创作者所有,如果涉及侵权,请第一时间联系本网删除。
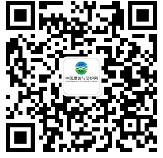
官方微信
《中国腐蚀与防护网电子期刊》征订启事
- 投稿联系:编辑部
- 电话:010-62316606-806
- 邮箱:fsfhzy666@163.com
- 中国腐蚀与防护网官方QQ群:140808414