摘要
使用力学性能测试、轴向力加载疲劳测试、扫描电子显微镜、电化学测试等手段,研究了模拟工业大气环境中Al-Mg-Si合金母材及其焊接接头的腐蚀疲劳特征。结果表明:Al-Mg-Si合金对接焊接接头的力学性能低于母材,而且在模拟工业大气环境中更易腐蚀。焊接接头的腐蚀疲劳敏感性更高,原因是其焊接缺陷处容易成为腐蚀疲劳裂纹优先萌生的区域,最终导致试样在焊缝区域发生疲劳断裂。
关键词: Al-Mg-Si合金 ; 焊接接头 ; 腐蚀疲劳特征 ; 模拟工业大气
随着科技与经济水平的不断进步,高速铁路由于其速度快、效率高等优势成为了当今世界铁路发展的潮流。铝合金因其比重轻、塑性好、比强度高、耐腐蚀能力强等优点[1,2]应用于高铁车体结构中[3-5]。虽然铝合金具有良好的性能,但高铁车体构件材料在交变载荷和跨地域的多变大气环境共同作用下极易发生腐蚀疲劳破坏,其中焊接接头部位由于接头软化及焊接缺陷的存在,如气孔、热裂纹、残余应力等,其发生疲劳断裂的现象尤为突出,常引起突发性、灾难性事故[6-8]。车体结构的腐蚀疲劳问题将是制约高铁安全服役的重要技术瓶颈之一。
目前,国内外针对铝合金及其焊接接头的腐蚀疲劳问题已经进行了一些研究。Genel[9]对AA7075-T6铝合金进行了弯曲疲劳实验,表明由于腐蚀坑的存在,疲劳强度降低了约60%。Pao等[10]研究了高强铝合金7075-T7451搅拌摩擦焊接头在应力比为0.1时的腐蚀疲劳性能,表明焊接接头各区域呈现的腐蚀疲劳性能差异明显,原因是裂纹闭合效应使得热影响区的疲劳裂纹扩展速率低于母材及焊核区域。Czhchowski等[11]研究了5083-H321形变强化铝合金在3.5%NaCl腐蚀溶液中的疲劳性能,结果表明,搅拌摩擦焊焊接接头在盐溶液中裂纹萌生点较空气增多,且溶液中的阳极溶解导致裂纹扩展加速,因此腐蚀疲劳寿命大大缩短。Fonda等[12]研究了5456-H116铝合金焊接接头不同区域的腐蚀疲劳行为,结果表明,热影响区表现出高于母材和焊核的腐蚀疲劳门槛应力值和较低的裂纹扩展速率,该研究结果与Pao等[10]的一致。Sabelkin等[13]通过研究得到了高强度7075-T6铝合金在疲劳载荷下腐蚀坑向裂纹的转变过程。Chanyathunyaroj等[14]研究了6061铝合金在3.5%NaCl环境下的疲劳特性,表明3.5%NaCl环境会引发点蚀,导致裂纹萌生,从而显著降低6061铝合金的疲劳寿命。Cui等[15]针对7B04-T6铝合金也得出了相似的结论。虽然已经对铝合金及其焊接接头的腐蚀疲劳进行了较多研究,但严酷大气腐蚀环境和高铁动载荷条件耦合下铝合金的腐蚀疲劳失效领域仍存在诸多问题有待研究。因此,开展铝合金及其焊接接头在严酷环境下的腐蚀疲劳实验和数据积累具有重要意义。
本文以高铁用Al-Mg-Si合金母材及其对接焊接接头为研究对象,针对其在模拟工业大气环境中的腐蚀疲劳特征进行了研究,以期为相关高速铁路装备的安全服役和设计准则制定提供理论依据与数据支撑。
1 实验方法
实验材料为高铁用Al-Mg-Si合金及其对接焊接接头,供货状态为T6,其化学成分 (质量分数,%) 为:Si 0.64,Mn 0.23,Mg 0.58,Cu 0.081,Ti 0.034,Fe 0.18,Cr 0.17,Zn 0.11,Al余量。在Al-Mg-Si合金焊接接头的焊缝区域截取试样,用SiC砂纸逐级打磨至2000#后,抛光至1 μm粗糙度,用酒精清洗并冷风吹干,用Keller侵蚀液 (2.5 mL HNO3+1.5 mL HCl+1 mL HF+95 mL H2O) 将抛光过的表面侵蚀60s后,使用VHX-2000超景深三维显微系统观察其宏观形貌。
力学性能测试与腐蚀疲劳实验均在MTS Landmark 730型液压伺服疲劳试验机上进行,力学性能测试所用拉伸速率为10-3 s-1。实验前将试样工作段用SiC砂纸逐级打磨至3000#,最终打磨方向与试样轴向平行。实验温度为室温,腐蚀介质为0.01 mol/L的NaHSO3水溶液,pH4.4。实验加载载荷种类为轴向力拉伸,波形为正弦波,应力比 (σmin/σmax) 为0.1,频率为5 Hz。疲劳实验结束后,截取试样工作段,用去离子水清洗,并用除锈液 (HNO3,ρ=1.42 g/ml) 超声去除表面腐蚀产物,最后用酒精进行超声清洗。处理完毕后,在Quanta 250扫描电子显微镜 (SEM) 下结合能谱仪 (EDS) 对试样的疲劳断口形貌进行观察分析。
电化学测试在VersaSTAT3型电化学工作站上进行。将Al-Mg-Si合金母材及焊接接头分别加工为10 mm×10 mm×3 mm的块状电化学试样。将其表面的油污清洗后吹干,在非工作面焊接铜导线后,用环氧树脂密封,只留出1 cm2的工作面积。每次测试前预先用SiC砂纸将封好的样品逐级打磨至2000#,随后用去离子水将工作面冲洗干净,再用无水乙醇除去残留水分、冷风吹干后放入干燥皿中待用。采用三电极体系进行电化学测试,其中Al-Mg-Si合金母材及焊接接头的电化学试样为工作电极,饱和甘汞电极 (SCE) 为参比电极,辅助电极为20 mm×20 mm×0.1 mm的铂片。电化学测试均在室温下完成。测试时开路电位在10 min内变化小于10 mV视为稳定,稳定后进行电化学阻抗谱测试 (EIS) 和动电位极化测试。EIS的交流正弦波幅为10 mV,测试频率为105~10-2 Hz。动电位极化测试的初始电位为-1.2 V (vs SCE),以0.33 mV/s的速率进行正向扫描。每组均进行3次或以上的测试,从而确保实验的准确性。
2 实验结果
2.1 焊接接头整体形貌
图1为进行抛光、侵蚀后的未经实验的Al-Mg-Si合金焊接接头处的整体形貌。由图可知,未经实验的焊接接头试样在抛光侵蚀后,在焊缝区能观察到明显的焊接缺陷,这些缺陷往往会成为腐蚀疲劳裂纹优先萌生的位置,从而导致疲劳开裂。
图1 Al-Mg-Si合金焊接接头宏观形貌
2.2 力学性能
Al-Mg-Si合金母材和焊接接头的拉伸力学性能如图2所示。从图中可知Al-Mg-Si合金母材有明显的屈服点,其屈服强度为290 MPa,抗拉强度为315 MPa,延伸率为28.85%。与母材相比,Al-Mg-Si合金焊接接头无明显的屈服现象,其条件屈服强度为129 MPa,抗拉强度为209 MPa,延伸率为8.03%。从图中可以看出,焊接接头的力学性能较母材明显降低,其屈服强度仅为母材的44.58%,抗拉强度为母材的66.33%。这是因为在焊接过程中,焊接接头区域产生的焊接缺陷会减小材料承载横截面的有效面积和产生应力集中。而且,焊接接头区域本就存在较大的残余应力。这些因素都会降低焊接接头的力学性能,从而对其腐蚀疲劳性能产生一定的影响。
图2 Al-Mg-Si合金母材及焊接接头的应力-应变拉伸曲线
2.3 电化学测试
图3为Al-Mg-Si合金母材及焊接接头在模拟工业大气环境中的极化曲线和电化学阻抗谱测试结果,从图3a中可以看出,对比母材,焊接接头的腐蚀电流显著增加。从Nyquist图 (图3b) 中可知,焊接接头的容抗弧半径较母材有明显下降。容抗弧反映了电极反应阻力的大小,容抗弧越大,电极反应阻力越大,反之越小。故焊接接头在模拟工业大气环境中的电极反应阻力小于母材,与极化曲线的结果相符。而且,能够明显看到阻抗谱低频区存在明显的感抗弧,这可能与试样表面的吸附现象有关。为了进一步比较两者的耐蚀性,对极化曲线的相关数据进行了统计,并对阻抗谱结果进行了拟合,拟合所采用的等效电路如图4所示,并将相关电化学腐蚀参数统计于表1中。图4中各电路参数的物理意义如下:Rs为溶液电阻,Qf为试样表面膜层电容,Rf为试样表面膜层电阻,Qdl为界面双电层电容,Rct为界面电荷转移电阻,RL和L为与吸附过程相关的电阻和电感。由表1可知,Al-Mg-Si合金焊接接头的腐蚀电位Ecorr略低于母材,维钝电流密度Ip高于母材,说明它在模拟工业大气中相较母材更易腐蚀。并且其电荷转移电阻Rct比母材要低,说明界面电化学反应更加活泼。而母材的表面膜层电阻Rf大于焊接接头,表明其表面形成的腐蚀产物膜更加稳定。这些结果均表明,在模拟工业大气环境中,Al-Mg-Si合金焊接接头的腐蚀敏感性比母材要高。
图3 Al-Mg-Si合金母材及焊接接头的极化曲线和电化学阻抗谱
图4 Al-Mg-Si合金母材及焊接接头电化学阻抗谱的拟合电路图
表1 Al-Mg-Si合金母材及焊接接头的电化学腐蚀参数
2.4 腐蚀疲劳行为
对Al-Mg-Si合金及焊接接头进行了腐蚀疲劳实验,结果如图5a所示。在腐蚀环境中一般规定腐蚀疲劳寿命达到106时即视为不会发生断裂[16],由图可知,Al-Mg-Si合金母材在模拟工业大气环境中的疲劳性能要明显优于焊接接头,在峰值应力同为100 MPa时,Al-Mg-Si合金母材在模拟工业大气环境下不会发生断裂,远高于同峰值应力下Al-Mg-Si合金焊接接头的疲劳周次。由于二者的性能差异较大,为了更直观的对两者的疲劳性能进行比较,将横坐标更换为施加的峰值应力与自身屈服强度的比值,并用柱状图进行了表示,结果如图5b所示。从图中可以明显看出,在施加的峰值应力与屈服强度的比值相同时,Al-Mg-Si合金母材的疲劳周次远远高于Al-Mg-Si合金焊接接头。故Al-Mg-Si合金焊接接头在模拟工业大气环境中的腐蚀疲劳性能是低于母材的。
图5 Al-Mg-Si合金母材及焊接接头在模拟工业大气中的疲劳周次-峰值应力柱状图
2.5 腐蚀疲劳宏观形貌
图6为Al-Mg-Si合金母材及焊接接头在模拟工业大气环境中发生腐蚀疲劳断裂后的宏观形貌图。从图中可以看出,母材的腐蚀疲劳断裂位置位于平行段,而焊接接头的断裂位置为焊缝区域,表明焊接接头可能是由于焊缝区域焊接缺陷的存在及焊接残余应力等因素影响导致焊缝区域优先发生腐蚀疲劳裂纹萌生和扩展,最终造成开裂。
图6 Al-Mg-Si合金母材及焊接接头试样在模拟工业大气中腐蚀疲劳实验后的宏观形貌
2.6 腐蚀疲劳微观形貌
通过选取不同峰值应力条件下的铝合金母材及焊接接头腐蚀疲劳断口形貌来进一步研究其腐蚀疲劳行为,如图7所示。从图7a~c中可以看出,Al-Mg-Si合金母材腐蚀疲劳断口特征明显,包括裂纹源、裂纹扩展区及瞬断区3部分。对断口的整体微观形貌进行观察可知 (图7a),腐蚀疲劳裂纹优先萌生于边界处,这是由于边角位置表层处于自由表面,该区域晶粒受到来自周围晶粒的约束很少,当铝合金构件在腐蚀性环境中受到疲劳载荷作用时,晶粒很容易产生滑移,应力集中增强,导致边角位置成为主裂纹源。而且可以看到疲劳裂纹优先萌生于点蚀坑底部,表明阳极溶解作用在腐蚀疲劳裂纹萌生过程中占据重要的作用,一般来说,腐蚀坑一方面会造成应力集中,另一方面也会破坏局部材料的晶粒排列而造成材料力学性能下降[17]。对裂纹扩展区进行放大观察 (图7c),能够看到腐蚀疲劳裂纹扩展平台为典型的放射状花样,表明腐蚀疲劳裂纹是以解理方式进行。
图7 Al-Mg-Si合金母材及焊接接头在150和80 MPa下模拟工业大气环境中腐蚀疲劳断口的微观形貌
图7d~f为Al-Mg-Si合金对接接头在模拟工业大气环境中峰值应力80 MPa下的腐蚀疲劳断口微观形貌,断口同样包括裂纹源、裂纹扩展区及瞬断区3部分。由图可知,腐蚀疲劳裂纹也萌生于边部区域,且萌生区附近有较多焊接缺陷存在。对裂纹源附近区域进行进一步观察 (图7e),可以看到此区域存在较多缺陷如孔洞等。这些缺陷的存在会导致应力集中,从而可能会造成其附近区域在交变载荷作用下塑性形变积累严重,从而形成腐蚀疲劳裂纹并扩展。而且,在裂纹源的焊接缺陷附近可以明显观察到阳极溶解的痕迹,表明焊接缺陷更易被腐蚀介质影响,从而作为阳极优先溶解。通过对裂纹扩展区域观察可见 (图7f),扩展区域仍有较多孔洞,这些都表明焊接质量对腐蚀疲劳性能具有较大的影响。
图8为焊接接头疲劳试样断口的侧面SEM形貌图和EDS分析。图8a为峰值应力为80 MPa时腐蚀疲劳断口的侧面形貌,由图可知,该处存在许多焊接缺陷,且由于缺陷的存在产生了微裂纹。一般情况下,焊缝表面不可避免地会存在着一些材料缺陷,如气孔、夹杂物、粗大的二次相等[7]。而这些缺陷一般情况下会显著增加焊接接头的腐蚀疲劳敏感性[8,18]。许多研究已经表明这些焊接缺陷会成为腐蚀疲劳裂纹的优先萌生点,从而导致焊接接头的腐蚀疲劳寿命相较于母材降低[19,20]。Shahri等[21]用有限元方法模拟了Al-Mg-Si合金焊接接头疲劳裂纹的萌生和扩展,发现焊缝是整个接头的薄弱环节。Liu等[6]也可见由于焊接缺陷的存在,焊接区是整个接头中最薄弱的区域,且缺陷附近的应力集中被认为是微裂纹产生的主要原因。而且,由于点蚀一般萌生于金属表面化学性质与物理性质的不均匀处,如第二相沉淀、非金属夹杂等缺陷部位,所以存在焊接缺陷的区域很容易发生点蚀,从而引起应力集中最终导致疲劳裂纹萌生。由EDS分析 (如图8d和e) 可知,夹杂物为铝合金中较为常见的Al2O3和MgO夹杂物,主要为Al2O3。并且于图8b和c中可以明显地看到,在夹杂物的边缘出现了裂纹萌生的趋势。由于夹杂物与基体有很大差异,它的存在破坏了材料本身的连续性,如同在材料上预制的小缺口一样。而且这些氧化夹杂物一般都较为脆硬,与基体的硬度差别较大,所以在承受疲劳载荷时,裂纹会优先在此形核,形成裂纹源,从而缩短材料的疲劳寿命。已有研究[22]表明,Al2O3夹杂物的存在会使其周围出现微裂纹和高密度的晶格畸变区域,而且由于腐蚀离子会在缝隙中逐渐累积,缝隙中的逐渐酸化会加速腐蚀的发生,从而腐蚀坑逐渐加深,产生应力集中导致疲劳裂纹的萌生和扩展。
图8 Al-Mg-Si合金焊接接头在模拟工业大气中80 MPa下的腐蚀疲劳断口侧面形貌及EDS谱
3 讨论
在空气中,Al-Mg-Si合金表面会产生一层钝化膜,其主要成分为Al(OH)3。从动电位极化曲线结果可知 (图3a),Al-Mg-Si合金在模拟工业大气环境中的电化学行为包括阳极钝化过程和阴极吸氧过程。其中,阳极反应为:
阴极反应为:
但是,由于模拟工业大气环境为酸性环境和HSO3-的存在,材料的腐蚀过程必然会受到影响,有研究证明,HSO3-的存在会促进阴极过程,而且可以将阴极过程由氧扩散控制转变为吸氧和析氢混合控制的模式[23]。模拟工业大气环境中的电化学过程反应式如下:
由腐蚀疲劳寿命结果 (图5) 可知,Al-Mg-Si合金母材和焊接接头在模拟工业大气环境中均具有比较高的腐蚀疲劳敏感性,且焊接接头的敏感性远大于母材。母材的腐蚀疲劳是由钝化膜破裂后的阳极溶解引起的。Al-Mg-Si合金存在一层致密的钝化膜,这层膜相对基体为阴极,由于疲劳产生的滑移台阶的挤出或侵入,覆盖的钝化膜遭到破坏,于是暴露的滑移面相对于大面积作为阴极的氧化膜就成了小阳极,从而就形成了腐蚀电池,膜破裂处不断溶解,形成微裂纹并最终导致疲劳裂纹的萌生。而Al-Mg-Si合金焊接接头的腐蚀疲劳则是主要归因于焊接工艺,由于焊接的质量问题,焊缝区存在着大量的孔洞和夹杂物,其中大部分是Al2O3夹杂物 (图8),在循环载荷作用下,含夹杂物区域的氧化膜不仅要受到疲劳产生的滑移台阶的侵入,还会因为夹杂物产生的应力集中而破裂,从而使基体更多的暴露在腐蚀介质中并发生溶解。前文已经提到,Al2O3夹杂物周围会存在高密度的晶格畸变区域,它会与未畸变区形成腐蚀电池,并作为阳极优先溶解,形成腐蚀坑。故Al2O3夹杂物的存在促进了焊接接头的阳极反应,这也是电化学测试中焊接接头的腐蚀电流要大于母材的原因。随着腐蚀时间的增长,腐蚀坑深度不断增加,腐蚀疲劳微裂纹也会在这些区域形核。同时,HSO3-等腐蚀介质会在腐蚀坑底部形成酸性的封闭环境,从而加速局部阳极溶解,最终导致腐蚀疲劳开裂。除此之外,由前文的力学性能测试可知,这些焊接缺陷的存在产生的残余应力,导致焊缝区的力学性能相比母材较差,从而焊缝区结合力较弱,也会使断裂优先在焊缝区发生。
综上所述,焊接过程中引入的大量焊接缺陷是Al-Mg-Si合金焊接接头腐蚀疲劳性能低于母材的主要原因。因此,在实际生产中应优化成形工艺和焊接工艺,控制焊接缺陷和夹杂物的数量,从而提高材料的腐蚀疲劳性能。
4 结论
(1) Al-Mg-Si合金焊接接头的焊缝区域存在较多焊接缺陷,这些缺陷产生的残余应力会降低焊缝区域的结合力,导致焊缝区的力学性能相比母材较差,且疲劳断裂会优先发生于焊缝区,从而降低焊接接头的腐蚀疲劳性能。
(2) Al-Mg-Si合金焊接接头在模拟工业大气环境中比母材具有更高的腐蚀疲劳敏感性。母材的腐蚀疲劳裂纹萌生于边界处的腐蚀坑,而焊接接头的疲劳裂纹萌生于边部焊接缺陷及夹杂物较多的区域。焊接过程中引入的大量焊接缺陷是Al-Mg-Si合金焊接接头腐蚀疲劳性能低于母材的主要原因。
参考文献
1 Winter L, Hockauf K, Lampke T. High cycle fatigue behavior of the severely plastically deformed 6082 aluminum alloy with an anodic and plasma electrolytic oxide coating [J]. Surf. Coat. Technol., 2018, 349: 576
2 Xu X C, Liu D X, Zhang X H, et al. Mechanical and corrosion fatigue behaviors of gradient structured 7B50-T7751 aluminum alloy processed via ultrasonic surface rolling [J]. J. Mater. Sci. Technol., 2020, 40: 88
3 Costa J D M, Jesus J S, Loureiro A, et al. Fatigue life improvement of MIG welded aluminium T-joints by friction stir processing [J]. Int. J. Fatigue, 2014, 61: 244
4 Dong P, Sun D Q, Li H M. Natural aging behaviour of friction stir welded 6005A-T6 aluminium alloy [J]. Mater. Sci. Eng., 2013, A576: 29
5 Svenningsen G, Lein J E, Bj?rgum A, et al. Effect of low copper content and heat treatment on intergranular corrosion of model AlMgSi alloys [J]. Corros. Sci., 2006, 48: 226
6 Liu H B, Yang S L, Xie C J, et al. Microstructure characterization and mechanism of fatigue crack initiation near pores for 6005A CMT welded joint [J]. Mater. Sci. Eng., 2017, A707: 22
7 Liu F Y, Tan C W, Wu L J, et al. Influence of waveforms on Laser-MIG hybrid welding characteristics of 5052 aluminum alloy assisted by magnetic field [J]. Opt. Laser Technol., 2020, 132: 106508
8 Qiao J N, Lu J X, Wu S K. Fatigue cracking characteristics of fiber Laser-VPTIG hybrid butt welded 7N01P-T4 aluminum alloy [J]. Int. J. Fatigue, 2017, 98: 32
9 Genel K. The effect of pitting on the bending fatigue performance of high-strength aluminum alloy [J]. Scr. Mater., 2007, 57: 297
10 Pao P S, Gill S J, Feng C R, et al. Corrosion-fatigue crack growth in friction stir welded Al 7050 [J]. Scr. Mater., 2001, 45: 605
11 Czechowski M. Low-cycle fatigue of friction stir welded Al-Mg alloys [J]. J. Mater. Process. Technol., 2005, 164/165: 1001
12 Fonda R W, Pao P S, Jones H N, et al. Microstructure, mechanical properties, and corrosion of friction stir welded Al 5456 [J]. Mater. Sci. Eng., 2009, A519: 1
13 Sabelkin V, Mall S, Misak H. Investigation into corrosion pit-to-fatigue crack transition in 7075-T6 aluminum alloy [J]. J. Mater. Eng. Perform., 2017, 26: 2535
14 Chanyathunyaroj K, Phetchcrai S, Laungsopapun G, et al. Fatigue characteristics of 6061 aluminum alloy subject to 3.5%NaCl environment [J]. Int. J. Fatigue, 2020, 133: 105420
15 Cui T F, Liu D X, Cai J, et al. Effect of pre-corrosion and corrosion/fatigue alternation frequency on the fatigue life of 7B04-T6 aluminum alloy [J]. J. Mater. Res., 2016, 31: 3869
16 Xu X X, Liu Z Y, Zhao T L, et al. Corrosion fatigue behavior of Fe-16Mn-0.6C-1.68Al twinning-induced plasticity steel in simulated seawater [J]. Corros. Sci., 2021, 182: 109282
17 Li X D, Mu Z T, Su W G, et al. Corrosion fatigue fracture analysis of 6A02 aluminum alloy [J]. J. Qingdao Univ. Sci. Technol. (Nat. Sci. Ed.), 2013, 34: 285
17 李旭东, 穆志韬, 苏维国等. 6A02铝合金腐蚀疲劳断口分析 [J]. 青岛科技大学学报 (自然科学版), 2013, 34: 285
18 Dickerson T L, Przydatek J. Fatigue of friction stir welds in aluminium alloys that contain root flaws [J]. Int. J. Fatigue, 2003, 25: 1399
19 Costa J D, Ferreira J A M, Borrego L P, et al. Fatigue behaviour of AA6082 friction stir welds under variable loadings [J]. Int. J. Fatigue, 2012, 37: 8
20 Talemi R. A numerical study on effects of randomly distributed subsurface hydrogen pores on fretting fatigue behaviour of aluminium AlSi10Mg [J]. Tribol. Int., 2020, 142: 105997
21 Shahri M M, Sandstr?m R. Fatigue analysis of friction stir welded aluminium profile using critical distance [J]. Int. J. Fatigue, 2010, 32: 302
22 Liu C, Revilla R I, Zhang D W, et al. Role of Al2O3 inclusions on the localized corrosion of Q460NH weathering steel in marine environment [J]. Corros. Sci., 2018, 138: 96
23 Wu W, Liu Z Y, Wang Q Y, et al. Improving the resistance of high-strength steel to SCC in a SO2-polluted marine atmosphere through Nb and Sb microalloying [J]. Corros. Sci., 2020, 170: 108693
免责声明:本网站所转载的文字、图片与视频资料版权归原创作者所有,如果涉及侵权,请第一时间联系本网删除。
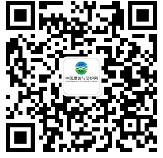
官方微信
《中国腐蚀与防护网电子期刊》征订启事
- 投稿联系:编辑部
- 电话:010-62316606-806
- 邮箱:fsfhzy666@163.com
- 中国腐蚀与防护网官方QQ群:140808414