珠三角地区某陆地原油管道总长约163km,管道直径Φ610mm,管道原防腐蚀层为环氧煤沥青。该管线工程于1997年竣工投用。目前管线年输量约1300万吨/年,是珠三角地区重要的能源通道之一。
管线阴极保护测试桩沿线布置,约每千米1支,全线共计169支。其中:A 段27支测试桩;B段56支测试桩;C 段36支测试桩;D段39支测试桩;E段11支测试桩。
随着埋地时间的延长以及环境条件的变化,土壤的腐蚀性增强,管线会面临越来越严重的腐蚀威胁。同时,近年来珠三角地区油品消耗增加,该输油管道的运行压力长期较高,这对管道的安全运行提出了更高的要求。由此,确保该输油管道全线的阴极保护处于有效状态成为了该管道完整性管理工作的重中之重。
管道原阴极保护方式为沿线以100~500m间隔安装锌/镁阳极,管道运行接近20年时,检测评价发现防腐蚀层出现严重老化,管道沿线阴极保护效果逐年劣化。为确保管道的防腐蚀措施有效、保障管道的安全运行,管理方决定在该管道上追加外加电流阴极保护站,采用外加电流和牺牲阳极联合阴极保护。
01
牺牲阳极阴极保护的效果
防腐蚀层与阴极保护技术联合应用,是目前公认行之有效的防腐蚀措施。阴极保护方法有两类:牺牲阳极法和外加电流法。两者皆通过为被保护结构物提供直流电流对被保护结构物进行极化,从而实现抑制腐蚀的目的。
外加电流方法须使用外部直流电源,将电源负极与被保护结构物相连,电源正极与辅助阳极相连。该方法的优点在于可以输出较大电流且电流可调,受电解质电阻率限制影响小等。
牺牲阳极法是采用镁、锌、铝等电位较负的合金材料与被保护结构物连接在一起,依靠阳极消耗溶解产生的电流使被保护结构物表面产生极化。牺牲阳极法的缺点在于提供的保护电流较小、受电解质电阻率影响较大,且易于消耗殆尽无法继续提供保护。
两种阴极保护方法联合应用可以解决单一牺牲阳极保护法的阴极保护有效性下降问题,该方法在业界已经有了成功应用的经验。
本工作研究的输油管道沿线地形复杂,山势峻峭,河流纵横,地质情况变化较多,管道采用的环氧煤沥青防腐蚀层耐久性较差。随着应用年限增加,防腐蚀层的老化情况日益严重。
管道管理方于2006年组织开展了管道外防腐蚀检测评价工作,采用交流电位梯度法对防腐蚀层破损点进行了检测定位,共发现防腐蚀层破损点365个。其中,严重破损点17个,中度破损点108个,轻微破损点240个。检测评价工作中获得的管道沿线通电电位分布情况如图1所示。
图1 牺牲阳极作用下管道沿线的通电电位(2006年)
2010年,通过智能内检测发现管道外部出现数千个金属损失点,结合后期阴保电位检测工作发现,腐蚀深度较大的缺陷多位于阴保效果较差的管段。
管道自投运起至2014年,采用牺牲阳极阴极保护方式,沿线以100~500m间隔布置锌或镁合金阳极。管道在运行初期一直采用通电电位法来评价阴保效果,当时认为通电电位为-0.85~-1.30V(相对于铜硫酸铜参比电极,CSE)时,管道处于最佳保护状态。管道沿线牺牲阳极有一部分通过测试桩连接管道,大多数采用埋地电缆直连的方式连接管道,这给后期的检测和评价工作带来了困难。
因为无法断开所有牺牲阳极与管道的连接,所以过去通常采用通电电位法评价管道的阴保效果。基于现行的国家标准GB/T 21448-2017《埋地钢质管道阴极保护技术规范》,现在可采用极化电位来判断管道的阴保效果。鉴于管道上连接的牺牲阳极无法全部断开,所以目前该管道利用极化试片法评价阴极保护的有效性。采用极化试片测量时,将试片埋设于管道服役环境中,试片与管道中心线的水平距离为0.1~0.5m。根据SY/T 0029-2012《埋地钢质检查片应用技术规范》中关于“阴极保护电位检查片”的技术要求,同时考虑管道服役时间较长且防腐蚀层日益严重老化等情况,选择10cm2圆柱形试片。将试片测试线与管道测试线相连,极化一定时间后,将试片与管道断开,即可测得试片的瞬间断开电位,用该电位来评价管道的阴保效果。试片的连接方式见图2。
图2 极化试片与管道的连接方式
基于上述极化试片法,管道管理方于2013年开展了管道全线阴极保护效果的评价工作。在管道沿线共埋设了148片试片,采集了所有极化试片(共148片)的通电电位和瞬间断开电位,电位的分布情况见图3。这次评价工作统一采用-850mV极化电位准则,结果表明,共有84处未达标,占比为57%。
图3 极化试片的通电电位与瞬间断开电位(2013年)
此外,在检测中发现靠近5号站的管段受到一定程度的动态直流杂散电流干扰,疑似受到广州地铁干扰。由图4可见:该管段的通电电位存在明显的动态波动。
图4 受动态直流干扰管段的通电电位波动情况(2013年)
02
外防腐蚀层性能评价
GB/T 19285-2014《埋地钢质管道腐蚀防护工程检验》标准提出了埋地钢质管道外防腐蚀层的分级评价指标。外防腐蚀层状况的非开挖检测评价可采用外防腐蚀层电阻率、电流衰减率(Y值)、破损点密度等不开挖检测指标进行分析。其中,电流衰减率的评价指标见表1。
采用管中交流电流衰减法可以对管中电流衰减情况、电流衰减因子进行判断和计算。该方法适用于除钢套管、钢丝网加强的混凝土配重层(套管)外,远离高压交流输电线地区,任何交变磁场能穿透的覆盖层下的管道外防腐蚀层质量检测。对埋地管道的埋深、位置、分支、外部金属构筑物、防腐蚀层缺陷等都能给出准确信息;根据电流衰减的斜率,可以定性确定各段管道防腐蚀层质量的差异,为更准确的防腐蚀层破损点查寻提供基础。
在检测中,发射机通过测试桩向管道施加电流信号,然后使用接收机沿线探测管中电流信号。管中电流强度从信号馈入点开始随距离的增大而减小。衰减率与管线防腐蚀层状况、土壤电阻率等因素有关。检测电流信号在管道“故障点”处出现迅速下降。故障点可能是管道防腐蚀层损坏或管道与其他金属设施搭接。
接收机以amps/mA或dBmA值显示电流。
根据测得管道电流,利用下式计算出IdB和Y值:
Y=IdB/△X
式中:Y为单位距离管道中电流变化率;△X为检测管道电流两点间的距离;IdB为经对数转换后得到以分贝(dB)表示的电流值。
转换的关系为:
IdB=20×| lg(I1/I2) |
式中:I1和I2分别为相邻2个检测点的实测电流。
在防腐蚀层缺陷处,电流会通过破损点流向大地,故防腐蚀层破损点处电流衰减率(Y值)会突然增大,从电流衰减率与距离的曲线图上该点Y值会突然增大,由此可判定管道防腐蚀层异常的位置,根据电流衰减率变化可以分析管道防腐蚀层平均质量的优劣。
本工作中的输油管道沿线密布牺牲阳极,且多为地下直连无法断开,所以具备进行管中电流衰减测试的管段较少。在对牺牲阳极检测定位并临时摘除了阳极后,对5处管段进行了防腐蚀层性能测试,结果见表2。
表2 管段防腐蚀层的性能评价结果
GB/T 19285-2014标准未列出环氧煤沥青防腐蚀层,故本工作借鉴沥青防腐蚀层且选用管径接近的660mm管道的指标进行了防腐蚀层的评价。从表2可见:换管段采用3LPE防腐蚀层,评级为1级(优异);其他几处原防腐层管段的评级都为4级,即性能严重劣化。
03
外加电流阴极保护改造
基于管道沿线极化试片电位以及防腐蚀层性能评价结果,可以判定管道的防腐蚀层绝缘性能下降严重,管道的阴极保护效果难以达标。为有效抑制外腐蚀的发生、确保管道的安全运行,有必要对管道的阴极保护系统进行增强。鉴于管道沿线多数牺牲阳极无法开挖更换,经馈电试验确定追加外加电流阴极保护的增强方案,并于2014年在2,3,4,5号站进行四处外加电流阴极保护系统的安装和调试投运工作。
在实施外加电流阴极保护系统的安装工作前,对输油管道沿线8处绝缘接头进行了绝缘性能测试。采用固定参比电极同时测量绝缘接头两侧的电位,若电位存在明显差异则确定绝缘法兰的绝缘性能良好。
表3 绝缘接头的绝缘性能测试结果
由表3可见:8处绝缘接头的绝缘性能均为良好。
在四处阴极保护站安装完毕后,对系统进行了调试。四处新建阴极保护站的输出情况见表4。
表4 四处新建阴极保护站的输出情况
由表4可见:受地质情况影响,2和5号站阳极地床的接地电阻较大。
在四处阴保站运行1年后,再次对管道进行阴极保护有效性评价,并对外加电流阴极保护站投运前后管道沿线的极化试片瞬间断开电位进行了比较,见图5。
图5 实施外加电流阴极保护前后管道沿线的阴保电位
表5 全线测试桩处管道电位达标统计结果
由表5可见:在实施外加电流阴极保护系统前(2013年),全线有44处断电电位不达标,达标率为70.2%;外加电流阴极保护系统实施后,2015年测得全线有8处断电电位不达标,达标率为93.9%;2017年仅测得3处电位不达标。施加外加电流阴极保护系统有效增强了管道的阴极保护效果,且随着时间的延长,管道极化效果越来越好,阴极保护电位也越来越负。
从最近的断电电位检测数据(2020年)来看,该输油管道沿线普遍受到日益严重的动态直流干扰,沿线断电电位均有波动(图6),波动最大值出现在D15号测试桩,断电电位为-1.23~-0.26V(图7)。
图6 2020年管道全线测试桩处的断电电位
图7 D15号测试桩位置的通电/断电电位
随着大湾区建设的快速推进,珠三角地区城市轨交系统建设必将进一步提速,该输油管道受到的外部直流杂散电流干扰也会日趋严重。此外,管道原有环氧煤沥青防腐蚀层的绝缘性能仍持续下降,管道的阴极保护电流需求将持续增大。在牺牲阳极和外加电流阴极保护联合使用的情况下,该输油管道的阴极保护基本可以达到有效,但是受外界直流干扰以及防腐蚀层老化和牺牲阳极消耗的影响,保护效果必然受到持续的负面影响。
结语
本工作研究的输油管道于1997年投入使用,原环氧煤沥青防腐蚀层老化严重,建设时期安装的牺牲阳极阴极保护系统在运行多年后已经无法对管道进行有效保护。随着原有牺牲阳极的逐步消耗,阳极电位发生正向偏移,牺牲阳极的输出电流逐步减少且有可能开始吸收外加电流系统输出的阴极保护电流,所以应该密切关注牺牲阳极的消耗情况。在条件允许的情况下,应逐步开挖原有牺牲阳极,剔除已经消耗殆尽的阳极,将仍有效的阳极通过新增的测试桩连接到管道,为后续的检测、整改提供便利条件。
珠三角地区的轨道交通建设正处于爆发式发展阶段,该输油管道受到的动态直流杂散电流干扰日趋严重。有必要对管道受干扰情况进行定期检测评价,并根据评价结果及时增加排流缓解措施或调整阴极保护系统的输出。
老旧管道的延寿问题是国内诸多油气管道所面临的一个课题。采用外加电流阴极保护系统对管道原有的牺牲阳极系统进行增强,可以恢复管道阴极保护的有效性,为老旧管道的延寿使用提供坚实的基础。
免责声明:本网站所转载的文字、图片与视频资料版权归原创作者所有,如果涉及侵权,请第一时间联系本网删除。
相关文章
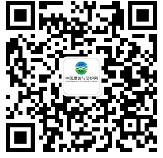
官方微信
《中国腐蚀与防护网电子期刊》征订启事
- 投稿联系:编辑部
- 电话:010-62316606-806
- 邮箱:fsfhzy666@163.com
- 中国腐蚀与防护网官方QQ群:140808414
点击排行
PPT新闻
“海洋金属”——钛合金在舰船的
点击数:7130
腐蚀与“海上丝绸之路”
点击数:5741