自20世纪80年代以来,我国石油石化产业迅猛发展,随着石油化工装置工作环境的逐渐恶劣,高温、高压、强腐蚀性与强氧化性等环境越来越普遍,这对所采用的钢材提出了较为严格的要求。除了要具有良好的力学性能、塑性、韧性外,还必须具有非常好的抗回火脆性、优良的焊接性能和较高的耐蚀性能[1]。早期,此类钢材只能依赖进口且价格昂贵。近年来14Cr1MoR钢以其较好的抗氢腐蚀、抗硫腐蚀、抗氧化性能、优良的焊接性及合理的价格逐渐取代了进口1.25Cr-0.5Mo系列钢,被广泛应用于化学化工、煤化工和石油化工等设备制造领域[2-5]。目前常见的应用设备有氨合成塔[6]、焦炭塔[7,8]、加氢反应器[9]等。
焊接是材料连接技术的主要方法之一,通过焊接形成的14Cr1MoR钢焊接接头及复合板材经济效益高,且经热处理工艺优化后,组织与性能优良,能满足不同设备的使用环境[10-12]。另一方面,由于焊接接头是材料腐蚀与裂纹产生的高发区域,而高温、高压环境和S、Cl等腐蚀性介质存在会加速腐蚀的进行与裂纹的扩展,因此,焊接接头是导致材料失效引发安全事故的主要部位[13-15]。本文以14Cr1MoR焊接接头为研究对象,对其组织及耐蚀性能进行了表征与观察,为14Cr1MoR钢的理论研究与实际应用提供了一定的科学依据。
1 实验方法
以14Cr1MoR钢焊接接头为研究对象,钢基体的化学成分 (质量分数,%) 为:C 0.04~0.17,Cr 1.00~1.50,Mo 0.45~0.65,Mn 0.4~0.65,Si 0.5~0.8,Sn≤0.015,Ni≤0.200,As≤0.016,Sb≤0.0025,Cu≤0.020,Fe余量。采用手工电弧焊制备焊接接头试样,H307焊条化学成分 (质量分数,%) 为:C 0.072,Cr 1.26,Mo 0.55,Mn 0.78,Si 0.21,P 0.013,S 0.008,Fe余量。采用4% (体积分数) HNO3酒精溶液对其焊接接头的截面试样进行腐蚀,分辨焊缝、热影响区及母材区,采用线切割的方法分别截取试样,试样尺寸为10 mm×10 mm×10 mm。电化学试样焊上铜导线并用环氧树脂密封,使裸露的工作表面面积为1 cm2,用200#、400#、600#、800#、1000#水磨砂纸进行打磨,水洗并用无水乙醇擦拭表面,然后吹干备用;实验选取3.5%NaCl溶液。
采用XJP-6A光学显微镜对14Cr1MoR接头的金相组织进行观察;将打磨好的焊接接头截面试样放入3.5%NaCl溶液中,记录不同浸泡时间里焊接接头截面腐蚀形貌。
采用CHI660E电化学工作站,三电极体系,在3.5% (质量分数) NaCl溶液中进行动电位极化曲线和电化学阻抗的测试,其中工作电极为焊缝、热影响区及母材区试样,参比电极为饱和甘汞、辅助电极为铂电极。开路时间1300 s,电化学阻抗测试的扰动电压为10 mV,频率范围为105~10-2 Hz,采用Zsimpwin软件对阻抗谱进行拟合;动电位极化曲线的扫描电位区间为-0.5~0 V,扫描速率为5 mV/s,采用电流法计算腐蚀速率。
2 结果与分析
2.1 焊接接头金相组织分析
焊接接头不同位置金相组织如图1所示。由图可见:焊缝组织以铁素体和贝氏体组织为主,细小碳化物分布在铁素体基体上,组织细小而均匀;14Cr1MoR钢为易淬火钢,其完全淬火区的过热区组织是粗大马氏体和贝氏体及少量碳化物,粗大马氏体组织决定该区的塑性、韧性较差,强度较高,这将导致该区为接头中的一个薄弱环节;焊接热作用在完全淬火区低温区的组织为晶粒细小均匀的贝氏体,塑性、韧性良好,硬度强度较高;不完全淬火区组织是铁素体和贝氏体;母材区的组织为铁素体、珠光体及少量贝氏体。
图1 14Cr1MoR钢焊接接头不同区域金相组织照片
由图1c可见,焊缝热影响区中完全淬火区的过热区组织粗大且分布不均匀,这样的组织导致接头的综合性能较差。因此过热区是焊接接头力学性能的薄弱环节。
2.2 焊接接头的宏观腐蚀形貌
将焊接接头在3.5%NaCl溶液中进行宏观腐蚀试验,不同浸泡时间焊接接头的腐蚀形貌如图2所示。由图可见:经打磨抛光的14Cr1MoR钢焊接接头表面光滑平整,具有金属光泽;室温下焊接接头在3.5%NaCl溶液浸泡腐蚀过程中,第1 h母材区域腐蚀发黑,伴有少量红棕色物质,焊接接头轮廓渐出,焊缝区无明显变化;第2 h在母材表面有明显的红棕色产物出现,母材区域发黑程度增加,焊缝部位无明显变化;第3 h母材表面红棕色产物逐渐增多,母材腐蚀变黑程度持续增加,接头区域开始出现红棕色物质;在接下来的3 h中,母材表面红棕色物质持续增多,母材腐蚀变黑程度进一步加深,焊缝区域红棕色物质增加;随着浸泡时间延长,热影响区渐渐清晰;腐蚀1 d后,焊接接头母材和焊缝表面覆盖一层红棕色物质;第2 d后,整个接头表面红棕色物质厚度增加,腐蚀到第7 d,红棕色物质厚厚地覆盖在接头表面,疏松多孔,易剥落,在红棕色物质剥落后,可清楚看见母材腐蚀变黑,焊缝黑度比母材浅。
图2 焊接接头在3.5%NaCl溶液中浸泡不同时间的形貌
宏观腐蚀结果发现,14Cr1MoR钢在3.5%NaCl溶液中并不耐蚀,前6 h腐蚀变化明显,且14Cr1MoR钢焊缝比母材更耐蚀,浸泡7 d后整个焊接接头表面覆盖厚厚的红棕色物质,且疏松多孔,易剥落,剥落腐蚀产物后,焊接接头表面整体变暗,表面残存有黑色斑块失去金属光泽。
2.3 腐蚀电化学实验结果
2.3.1 开路电位曲线
实验测得开路电位与时间的关系曲线如图3所示。在3.5%NaCl溶液中,开路时间1300 s后,不同位置试样的开路电位不同,其中焊缝电极电位最正,其次是热影响区,电位最负的是母材区;各试样的开路电位均随时间延长缓慢下降并趋于平缓。
图3 3.5%NaCl溶液中焊缝、母材、热影响区开路电位与时间关系曲线
2.3.2 电化学阻抗分析
图4为焊接接头不同位置试样在3.5%NaCl溶液中的电化学Nyquist图谱。由图可见,焊接接头不同区域试样的阻抗谱均呈双容抗弧,由高频区小弧和高频区大弧组成;其中焊缝区容抗弧半径最大,其次是热影响区,母材容抗弧半径最小。
图4 焊接接头不同区域阻抗的Nyquist图谱
根据14Cr1MoR腐蚀特点选用Rs(Qdl(Rt(QpRp))) 等效电路模拟阻抗谱。其中Rs为溶液电阻,Qdl为双电层电容,Rt为双电层放电电阻,Qp为腐蚀产物孔洞电容,Rp为腐蚀产物电阻。将模拟后的电化学参数整理,如表1所示。
表1 焊接接头不同区域的阻抗曲线拟合参数
由图表可见,焊缝区的Rp最大,为1786 Ω·cm2,形成的腐蚀产物附着性与致密度优于热影响区和母材,耐蚀性能较好;其次是热影响区,母材Rp为215.1 Ω·cm2,阻值最小,耐蚀性较差。
2.3.3 动电位极化曲线分析
14Cr1MoR钢焊接接头各个区域的极化曲线如图5所示,由电流法计算的腐蚀速率如表2所示。由图表可见:焊缝区的自腐蚀电位最负,其次为母材,热影响区的自腐蚀电位较正;从热力学角度分析,焊缝具有较大的腐蚀倾向,但是焊缝的自腐蚀电流密度最小,其腐蚀速率却很小,3.5%NaCl溶液中焊缝试样腐蚀速率vL为0.0511 mm·a-1,约是母材的一半。
图5 焊接接头不同区域动电位极化曲线图
表2 焊接接头不同区域的极化曲线参数
2.4 分析与讨论
综合电化学极化曲线和阻抗谱的实验数据,在3.5%NaCl溶液中,14Cr1MoR钢焊缝比母材具有更好的耐蚀性。分析认为14Cr1MoR钢作为低合金高强钢,合金元素以C、Mn、Si、Cr、Mo为主,合金元素的添加提高强度的同时,对合金的耐蚀性能也产生影响[16,17]。14Cr1MoR钢焊缝与母材采用等强原则选择焊材,对比母材与焊材成分发现,所选择的H307焊条中各元素含量基本在母材范围内,其中Si含量偏低,Mn含量偏高,Si-Mn联合脱氧净化焊缝的同时保证焊缝的强韧性;Cr、Mo对提高合金的耐蚀性具有一定作用;焊条中C含量偏低且在焊接电弧作用下会发生部分烧损,使得焊缝比母材具有更低的含碳量和相对简单的相组成 (铁素体和贝氏体),富碳的第二相含量较少,提高了钢的组织均匀性[18,19];相比而言,母材和热影响区组织更复杂,增大了腐蚀微电池阴阳极的电位差,增大了腐蚀速度,因而14Cr1MoR钢焊缝比母材具有更好的耐蚀性。
3 结论
(1) 14Cr1MoR钢焊接接头组织为典型的易淬火钢组织,组织类型多且分布不均匀。
(2) 与焊缝区相比,14Cr1MoR钢母材的耐蚀性较差,短期腐蚀变化明显,长期浸泡产生的腐蚀产物疏松多孔易剥落,对基材没有保护作用。
(3) 14Cr1MoR钢母材的腐蚀速率大于焊缝区,是焊缝腐蚀速率的两倍,焊缝碳含量的降低是其耐蚀性能高于母材的主要原因。
参考文献
1 Wang S H, Xue W. Study on the properties of domestic 14Cr1MoR steel [J]. Heat Treat. Met., 2004, 29(4): 35
1 王顺花, 薛巍. 国产14Cr1MoR钢板的性能研究 [J]. 金属热处理, 2004, 29(4): 35
2 Ren A M, Feng Z G, Li J Y. Study on welding process of 14Cr1MoR steel for hydrogen contact equipment [J]. Hot Working Technol., 2018, 47(15): 242
2 任爱梅, 冯振国, 历金雁. 临氢设备用14Cr1MoR钢的焊接工艺研究 [J]. 热加工工艺, 2018, 47(15): 242
3 Wang W L, Dang S X, Wang Y J. The welding of homemade 14Cr1MoR steel [J]. Electr. Weld. Mach., 2002, 32(7): 32
3 王文利, 党曙昕, 王迎君. 国产14Cr1MoR钢的焊接 [J]. 电焊机, 2002, 32(7): 32
4 Liu D X, Fu R L. Welding procedure analysis for submerged arc welding cracking of 14Cr1MoR plate [J]. Sulphur Phosphorus Bulk Mater. Handl. Relat. Eng., 2017, (6): 42
4 刘东旭, 傅瑞丽. 14Cr1MoR中厚板埋弧焊接裂纹的焊接工艺分析 [J]. 硫磷设计与粉体工程, 2017, (6): 42
5 Fu L Q, Liu X L, Fan H M. Research and development of 14Cr 1MoR steel plate [J]. Jiangxi Metall., 2010, 30(1): 1
5 扶利群, 刘小林, 范红梅. 14Cr 1MoR钢板的研制开发 [J]. 江西冶金, 2010, 30(1): 1
6 Li Y B, Niu H X, Wu Y Y, et al. Study and development of large thickness 14Cr1MoR steel plate for ammonia converter [J]. Wide Heavy Plate, 2016, 22(6): 19
6 李样兵, 牛红星, 吴艳阳等. 氨合成塔用大厚度14Cr1MoR钢板的研制开发 [J]. 宽厚板, 2016, 22(6): 19
7 Han Y M. Introduction of characteristics in design of large coke drum [J]. Process Equip. Piping, 2014, 51(1): 40
7 韩玉梅. 大型焦炭塔设计特点介绍 [J]. 化工设备与管道, 2014, 51(1): 40
8 Zhao X J. Corrosion analysis and anticorrosion measures of 14Cr1MoR coke tower [J]. Corros. Prot. Petrochem. Ind., 2017, 34(3): 17
8 赵新建. 14Cr1MoR焦炭塔腐蚀分析和防护措施 [J]. 石油化工腐蚀与防护, 2017, 34(3): 17
9 Xu J, Zhong M Y, Guo S X, et al. Characteristics of hydrogen damages for hydrogenation reactor wall-materials [J]. J. Chin. Soc. Corros. Prot., 2003, 23: 149
9 徐坚, 钟曼英, 郭世行等. 加氢反应器壁材料的氢损伤特性 [J]. 中国腐蚀与防护学报, 2003, 23: 149
10 He G X, Men X Z, Huang J. Effect of heat treatment process on structure and properties of 14Cr1MoR steel plate [J]. Spec. Steel Technol., 2017, 23(2): 10
10 何广霞, 孟宪震, 黄军. 热处理工艺对14Cr1MoR钢板组织和性能的影响 [J]. 特钢技术, 2017, 23(2): 10
11 Jiang L, Guo X C, Li J J, et al. Welding of stainless clad steel plate 14Cr1MoR+347H [J]. Petro-Chem. Equip., 2009, 38(3): 70
11 姜莉, 郭晓春, 李娟娟等. 14Cr1MoR+347H不锈钢复合板焊接 [J]. 石油化工设备, 2009, 38(3): 70
12 Jian L P, Liu L B, Zhang J M, et al. Effect of rolling and heat treatment on properties and microstructure of 304-14Cr1MoR composite steel plate [J]. Met. Mater. Metall. Eng., 2019, 47(1): 15
12 简乐平, 刘立彪, 张计谋等. 轧制及热处理对304-14Cr1MoR复合板性能和组织的影响 [J]. 金属材料与冶金工程, 2019, 47(1): 15
13 Wang Q Z, Li Q G, Yue Z H, et al. Study on corrosion of 904L (SA240 N08904) explosive-clad plate [J]. Dev. Appl. Mater., 2017, 32(5): 53
13 王全柱, 李启耕, 岳宗洪等. 904L (N08904) 不锈钢复合板腐蚀性能研究 [J]. 材料开发与应用, 2017, 32(5): 53
14 Sui G Z, Mo Y Q, Sun L, et al. Failure Analysis of 14Cr1MoR steel in high temperature sulfur environment [J]. Corros. Prot., 2019, 40: 215
14 隨广洲, 莫烨强, 孙亮等. 14Cr1MoR钢在高温硫环境中的失效行为 [J]. 腐蚀与防护, 2019, 40: 215
15 Zhou J S, Hei P H, Qin J, et al. Analysis of heat treatment on pitting resistance of 14Cr1MoR+904L steel [J]. Dev. Appl. Mater., 2016, 31(2): 49
15 周杰士, 黑鹏辉, 秦建等. 热处理制度对14Cr1MoR+904L耐点蚀性能的分析 [J]. 材料开发与应用, 2016, 31(2): 49
16 Sun Y W, Zhong Y P, Wang L S, et al. Corrosion behavior of low-alloy high strength steels in a simulated common SO2-containing atmosphere [J]. J. Chin. Soc. Corros. Prot., 2019, 39: 274
16 孙永伟, 钟玉平, 王灵水等. 低合金高强度钢的耐模拟工业大气腐蚀行为研究 [J]. 中国腐蚀与防护学报, 2019, 39: 274
17 Han W, Wang J, Wang Z Y, et al. Study on atmospheric corrosion of low alloy steels [J]. J. Chin. Soc. Corros. Prot., 2004, 24: 147
17 韩薇, 汪俊, 王振尧等. 碳钢与低合金钢耐大气腐蚀规律研究 [J]. 中国腐蚀与防护学报, 2004, 24: 147
18 Garcia C I, Lis A K, Pytel S M, et al. Ultra-low carbon bainitic steel plate steels: processing, microstructure and properties [J]. Trans. Iron .Steel Soc. AI ME, 1992, 13: 103
19 Li S P, Guo J, Yang S W, et al. Effect of carbon content and microstructure on the corrosion resistance of low alloy steels [J]. J. Univ. Sci. Technol. Beijing, 2008, 30: 16
19 李少坡, 郭佳, 杨善武等. 碳含量和组织类型对低合金钢耐蚀性的影响 [J]. 北京科技大学学报, 2008, 30: 16
免责声明:本网站所转载的文字、图片与视频资料版权归原创作者所有,如果涉及侵权,请第一时间联系本网删除。
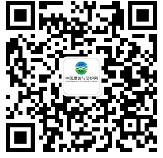
官方微信
《中国腐蚀与防护网电子期刊》征订启事
- 投稿联系:编辑部
- 电话:010-62316606-806
- 邮箱:fsfhzy666@163.com
- 中国腐蚀与防护网官方QQ群:140808414