45K冷镦钢常用于冷镦加工制造紧固件、连接件,如螺栓、螺母等。冷镦加工是在常温下塑性成形的加工工艺,采用冷镦工艺制造紧固件,不但效率高、质量好,而且用料省、成本低,但冷镦工艺对原材料质量要求较高。冷镦钢冷加工成形的性能良好,产品尺寸精度高,表面粗糙度好,生成效率高,是新兴的先进加工工艺。
本文对六角凸缘螺栓断裂失效件的化学成分、表面硬度、断口形貌及显微组织进行理化检测,分析和推断螺栓失效件断裂的原因以及断裂形成机理。
宏观检查
该螺栓失效件材料采用45K冷镦钢加工制造,螺栓型号为M8×40mm。加工工艺流程为冷镦→调质→搓丝→酸洗→镀锌。该六角凸缘螺栓在装配过程中发生断裂,断裂部位位于螺杆中部的螺母锁紧位置(见图1a)。六角凸缘螺栓零件由六角凸缘和螺杆构成(见图1b),该螺栓断裂失效件为客户提供,断裂件六角凸缘端已被截取,断裂件螺杆端也已剖开为两半,且两截断裂件外观色泽偏差较大,右侧断裂件的剖面是线切割加工形成的(见图1c)。
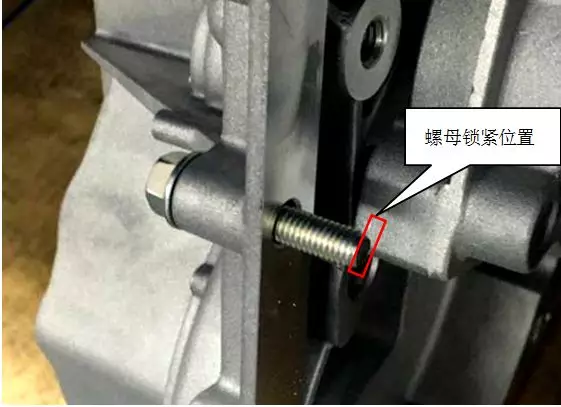
(a)螺栓装配图
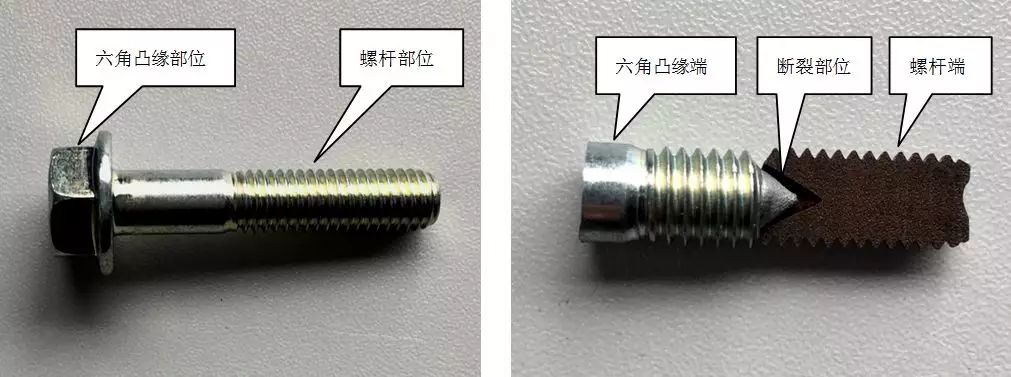
(b)螺栓成品件 (c)螺栓断裂件
图1 螺栓成品及断裂件
结果与讨论
(1)化学成分分析
从该螺栓断裂件上截取试样,采用ARL8860火花放电直读光谱仪进行化学成分检测。依据标准JIS G3507-1-2010《冷镦用碳素钢 第1部分:盘条》进行判定,化学成分符合规范要求(见表1)。
表1 失效件样品化学成分测试结果(质量分数)(%)

(2)表面硬度检测
从该螺栓断裂件上截取试样,采用Qness Q150数显洛氏硬度计进行表面硬度检测。检测结果表明,实测硬度值符合客户规范要求 (见表2)。
表2 失效件样品表面硬度测试结果(HRC)

(3)扫描电镜检测
采用SIGMA 300扫描电子显微镜,对螺栓失效件断口进行检测。六角凸缘端断口为圆锥形凸起,螺杆端断口为圆锥形凹坑。对六角突缘端圆锥凸起断口进行检测,图2a所示左侧为六角突缘端断口的螺牙齿顶外缘,右侧为断口中心凸起圆锥面。距螺杆螺牙底槽部位存在周向开裂的裂纹,裂纹呈多条平行条纹,表明材料表面强度极低。图2a中红框区域的倍率经放大,螺牙底槽裂纹显示多源台阶的应力开裂特征。该处存在应力集中现象,而且材料表面强度低,因而存在多条多源台阶裂纹源的开裂特征形貌(见图2b),由此推断螺牙底槽部位属于断口的断裂起始区。
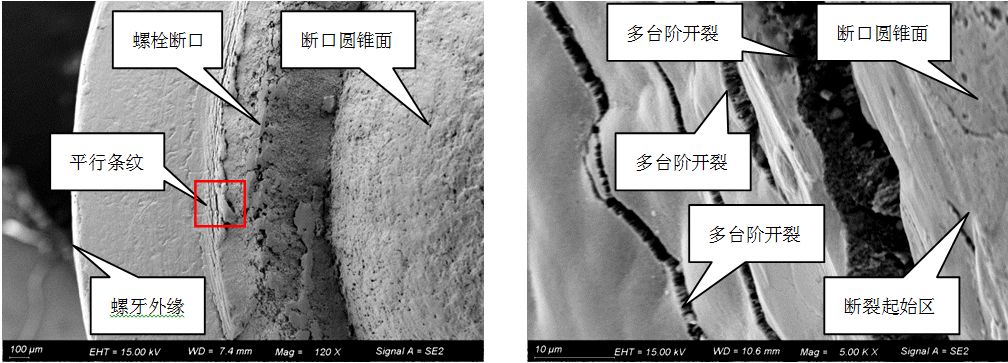
(a)低倍形貌(120×) (b)高倍形貌(5000×)
图2 螺牙底槽形貌
断裂起始区断口呈现细小等轴韧窝特征形貌(见图3a),表明材料基体组织韧性较好。靠近圆锥形凸起尖端的断裂终断区,断口仍以细小等轴韧窝为主,同时存在较多量撕裂棱及变形韧窝(见图3b),该处为断口终断区快速扩展特征。
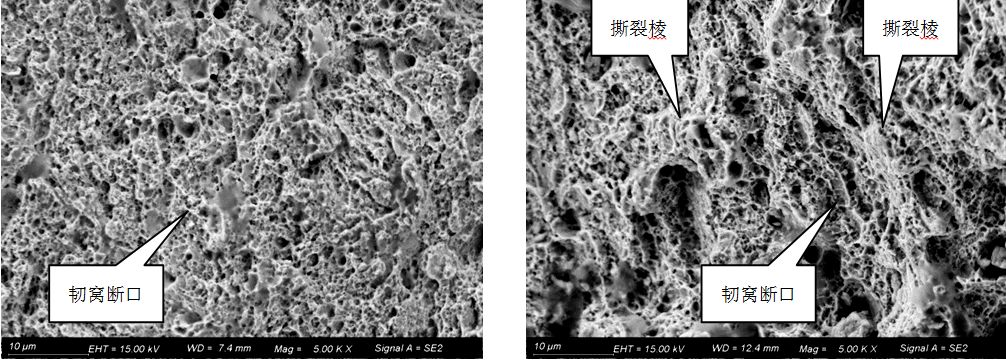
(a)起始区形貌(5000×) (b)终断区形貌(5000×)
图3 螺栓断口形貌
(4)金相检测分析
采用Axio Observer 7m金相显微镜,对螺栓断裂件基体组织进行金相检测。试样未经腐蚀剂浸蚀时,螺牙侧面明显可见不同形态的表面裂纹,表面裂纹的纵深度及垂直深度大多在60~160μm。无论是弯曲裂纹还是分叉裂纹,裂纹的尾部都呈圆钝状(见图4a~4d),显示挤压变形的折叠裂纹特征形貌。
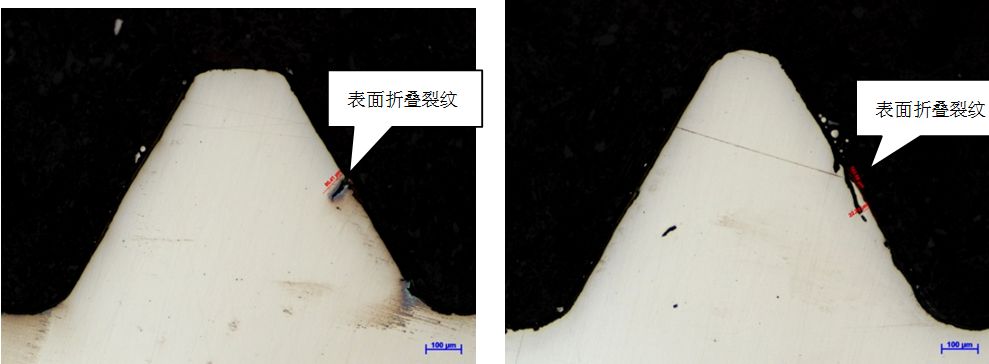
(a)100× (b)100×
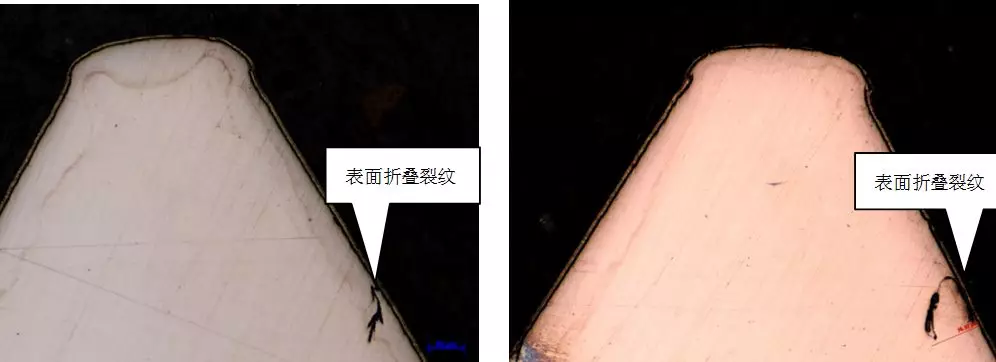
(c)500× (d)500×
图4 螺牙表面裂纹
金相显微镜检测,螺杆上几乎每个螺牙侧面都存在表面折叠裂纹。螺牙底部凹槽由圆角过渡,但过渡圆角的R半径较小(见图5a)。经测量,螺牙底槽R角半径为0.18mm,螺牙底槽R角半径越小,对应的应力集中越大。图示螺牙表层覆盖一层亮灰色的镀锌层,经测量该处镀锌层厚度为9.62μm(见图5b)。
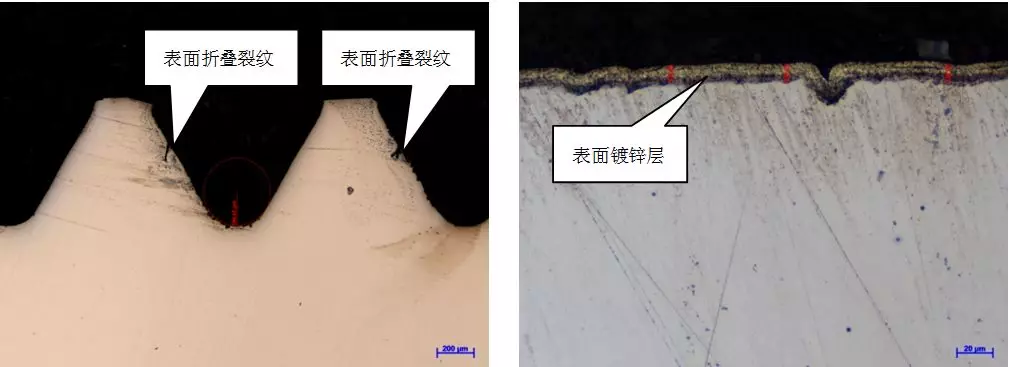
(a)表面折叠裂纹(50×) (b)表面镀锌层(500×)
图5 螺牙表面形貌
经腐蚀剂浸蚀后检测,有些螺牙侧面及底槽都存在表面折叠裂纹,同时螺牙表层呈现亮黄色(见图6a~6b),螺牙表层组织存在差异。图片经放大,表面折叠裂纹缝隙两侧存在明显的脱碳层(见图6c~6d)。螺栓在冷镦过程中产生折叠裂纹,在调质处理的加热过程中发生氧化脱碳,后期搓丝加工过程使折叠裂纹进一步挤压成细长的裂纹。
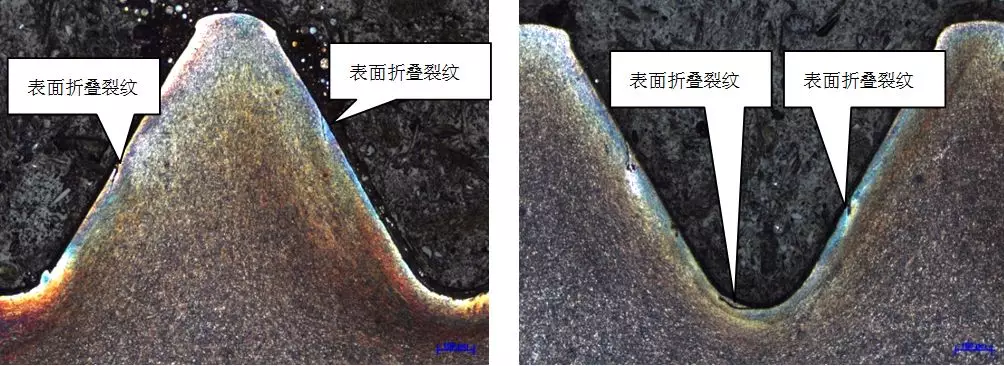
(a)100× (b)100×
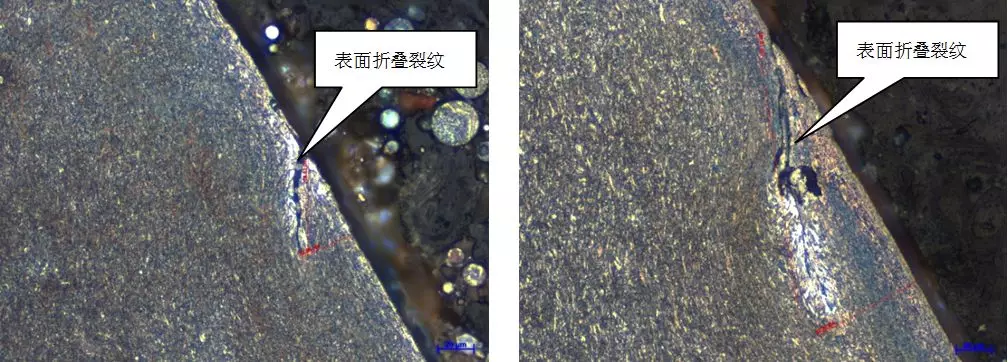
(c)500× (d)500×
图6 螺牙表面裂纹
螺牙侧面发现开口较大的表面折叠裂纹,裂纹间隙两侧的表面脱碳现象更为明显。在表面折叠裂纹的周围呈现变形的纤维状组织,表明搓丝加工之前螺栓表面已存在较大的凹坑,在搓丝过程中经挤压变形而形成折叠裂纹(见图7a)。在表面折叠裂纹的开口处存在两处圆弧状的凹坑,这是表面腐蚀的特征形貌,表明在镀锌处理之前,螺栓零件经过酸洗处理,而且酸洗处理时间较长,已经在表面形成较深的腐蚀凹坑(见图7b)。

(a) (b)
图7 螺牙表面裂纹(500×)
在螺牙底槽部位存在锲形撕裂凹坑,螺牙底槽附近的基体呈现严重变形的纤维状组织。由于搓丝加工产生的拉向应力已经大于材料的抗拉强度,因而造成螺牙底槽表面的撕裂凹坑(见图8a)。经测量,搓丝挤压加工的变形层深度达120μm。在螺牙底槽存在较多量的圆弧状腐蚀凹坑(见图8b),表明螺栓在酸洗处理过程中,酸洗处理时间过长。
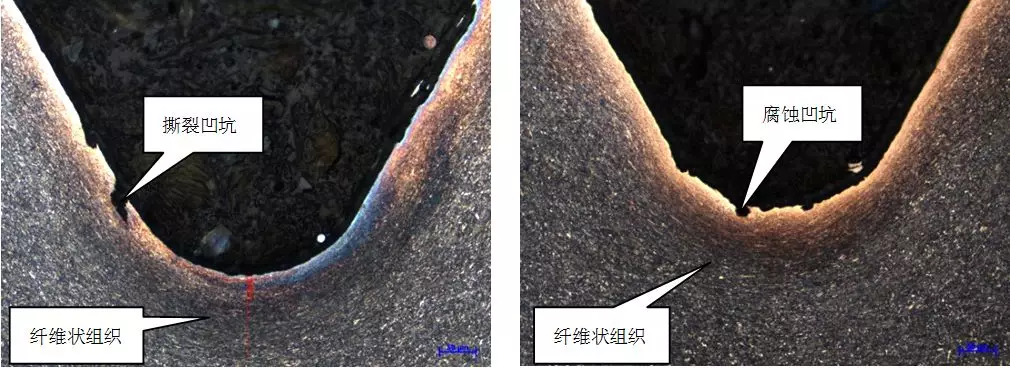
(a)撕裂凹坑(200×) (b)腐蚀凹坑(200×)
图8 螺牙底槽形貌
螺杆端断裂件的开裂起始区,首先形成于螺牙底槽部位,然后向螺杆中心部位及纵向继续扩展至最终断裂(见图9a~9b)。螺杆端断裂件断口呈圆锥形凹槽,断裂终断区位于螺杆心部,终断区的断口剖面呈现大小不等的凹坑,这些凹坑对应于六角凸缘端断口终断区的韧窝特征形貌(见图9c~9d)。
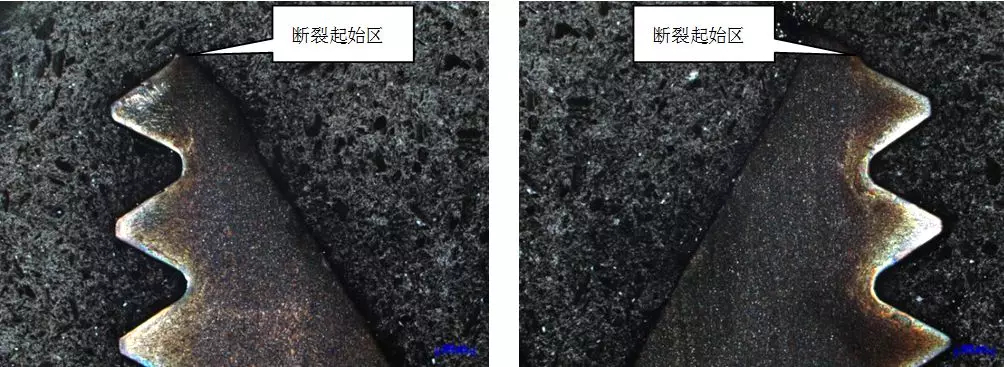
(a)断口起始区(25×) (b)断口起始区(25×)
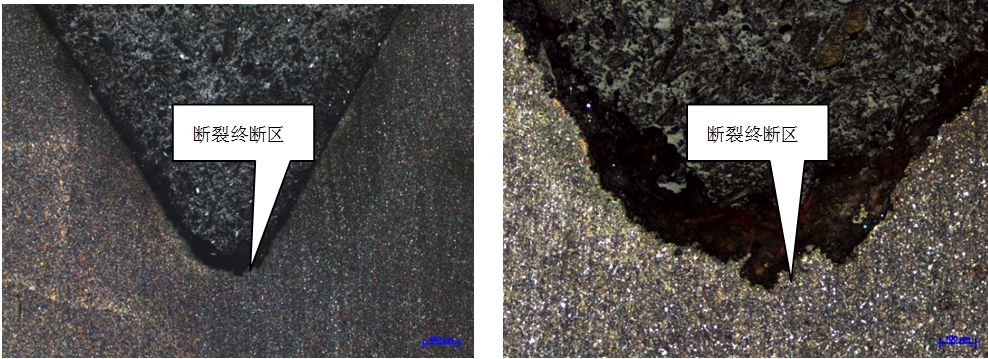
(c)断口终断区(25×) (d)断口终断区(100×)
图9 螺杆端断口形貌
为了准确测量螺栓断裂件的表面脱碳层,在螺栓光杆部位径向截取试样进行检测。金相显微镜检测,螺栓光杆部位的表层存在较深的白亮色脱碳层(见图10a~10b),依据国家标准GB/T224—2008《钢的脱碳层深度测定法》进行测定,表面脱碳层深度达0.11mm。在调质处理过程中,热处理炉内保护气氛不规范,零件因高温氧化脱碳造成较严重的表面脱碳层,特别是外表层全脱碳部位几乎全为铁素体组织。由于表面脱碳层内的碳含量降低,造成表面强度降低。采用Q10M数显维氏硬度计,对螺栓外表层全脱碳区域进行硬度测试,实测硬度值为85HV0.2,依据国家标准GB/T 33362—2016《金属材料 硬度值的换算》进行换算,对应的抗拉强度值约为270MPa。螺栓规范要求的硬度值为22~32HRC,依据国家标准GB/T 1172—1999《黑色金属硬度及强度换算值》进行换算,对应的抗拉强度值为813~1039MPa。因而可以推断,表面脱碳层的抗拉强度只有螺栓材料抗拉强度的1/3~1/4。该表面脱碳层缺陷组织显著降低,材料表面强度,这是造成螺栓断裂的主要原因。
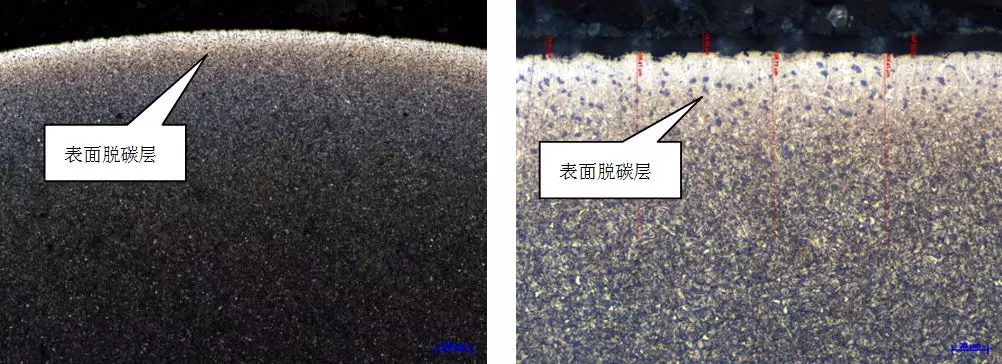
(a)表面脱碳层(100×) (b)表面脱碳层(500×)
图10表面脱碳层
六角凸缘部位以及螺栓杆部的基体显微组织,都为细针状马氏体位向的回火索氏体+少量铁素体(见图11a~11b)。依据国家标准GB/T13320—2007《钢质模锻件 金相组织评级图及评定方法》第三评级图进行评定,调质处理的显微组织评定为2级,标准要求1~4级合格,该显微组织属于合格级别。
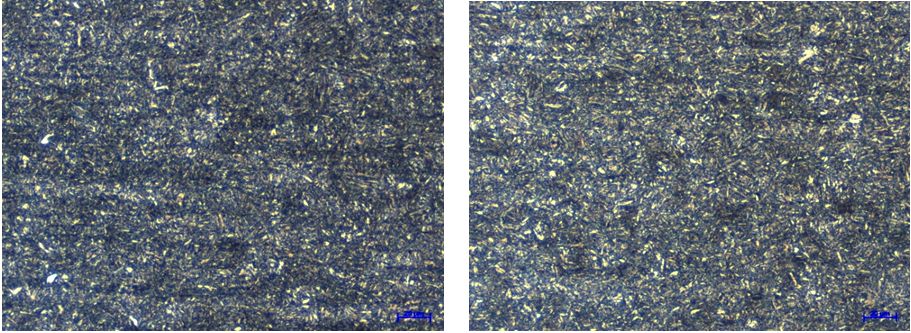
(a)凸缘显微组织(500×) (b)螺杆显微组织(500×)
图11 螺栓显微组织
(5)金相试样扫描电镜测试
对金相组织进行扫描电镜检测,在螺杆螺牙表面覆盖一层深灰色镀锌层(见图12a)。扫描电镜倍率进一步放大,表面镀锌层显示层状分布的多层结晶体,表面镀锌层与螺牙表面基体连接的过渡层结合良好(见图12b)。经测量,该处表面镀锌层深度为9.36μm。
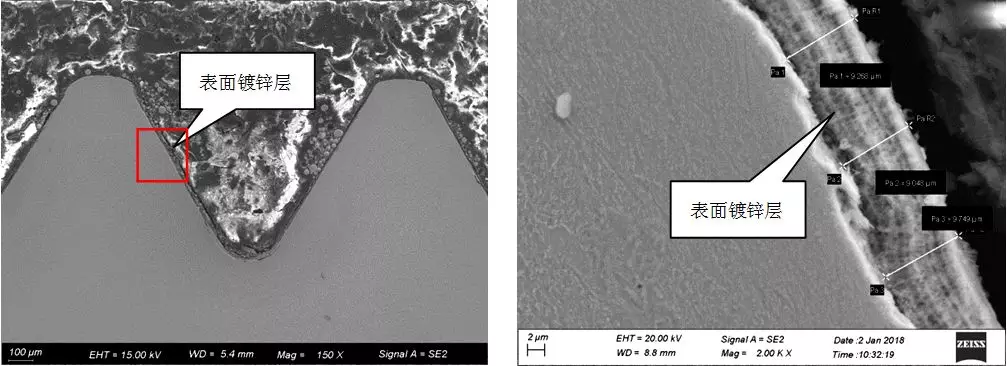
(a)表面镀锌层(150×) (b)表面镀锌层(2000×)
图12 表面镀锌层
螺杆螺牙凹槽表面同样覆盖一层镀锌层,表面镀锌层底部的螺牙凹槽表面存在多条折叠裂纹(见图13a)。扫描电镜倍率进一步放大,折叠裂纹间隙两侧由若干个圆弧状凹坑构成,表明酸洗过程中的表面腐蚀较为严重。由于凹槽部位表面镀锌层沉积更为突出,实测表面镀锌层深度达10.76μm(见图13b)。
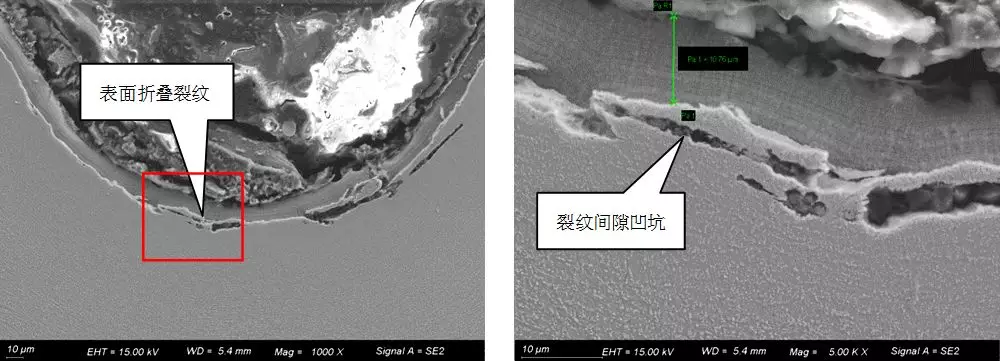
(a)表面折叠裂纹(1000×) (b)裂纹间隙凹坑(5000×)
图13 螺牙底槽形貌
经扫描电镜检测,六角凸缘部位及螺栓杆部的显微组织,都为细针状马氏体位向的回火索氏体+少量未溶铁素体。回火索氏体由颗粒状碳化物构成的针状及条状组织,未溶铁素体晶粒内只有极少量的颗粒状碳化物(见图14a~14b)。检测结果显示,螺栓基体显微组织正常。

(a)凸缘显微组织(5000×) (b)螺杆显微组织(5000×)
图14 螺栓显微组织
(6)金相试样微区能谱测试
对螺杆螺牙部位的表面镀锌层及基体组织进行微区能谱测试,测试区如图所示,谱图1区为表面镀锌层(见图15a),谱图2区为基体组织(见图15b)。能谱测试结果表明,谱图1区域的表面镀锌层含有Zn、Mg、Fe等合金元素,其中Zn含量达92.47%,能谱测试结果显示,螺牙表层属于含有少量Mg、Fe合金的表面镀锌层(见图15c)。谱图2区域的基体组织含有C、Mn、Fe等合金元素,成分显示与45K冷镦钢材料相符(见表3)。由于试样测试面经过硝酸酒精浸蚀,表面残留较多的C元素,因而能谱测试结果含碳量偏高(见图15d)。
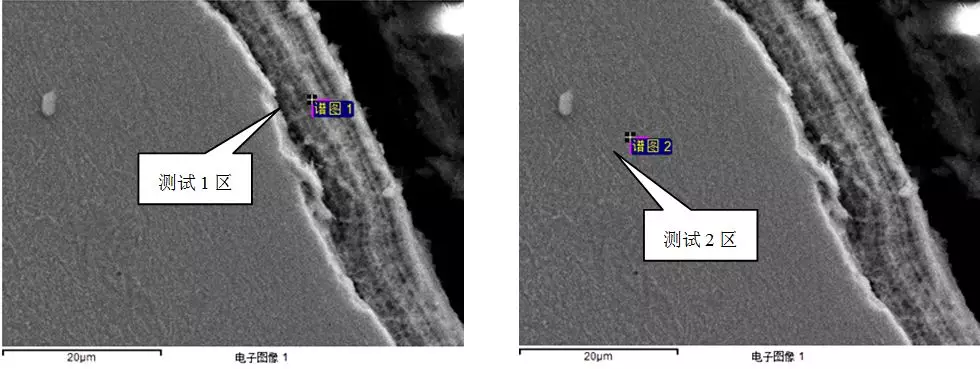
(a)能谱测试1区域(2000×)(b)能谱测试2区域(2000×)

(c)1区域能谱测试结果 (d)2区域能谱测试结果
图15 微区能谱测试
表3 失效件样品微区能谱测试结果(质量分数) (%)

综上所述,六角凸缘端断口为圆锥形凸起,螺杆端断口为圆锥形凹槽。对六角凸缘端圆锥凸起断口进行检测,在螺牙底槽部位存在多条周向开裂的裂纹。裂纹呈多条平行条纹,表明材料表面强度极低,同时裂纹处的多源台阶显示应力开裂特征。经测量螺牙底槽R角半径为0.18mm,螺牙底槽R角半径越小,应力集中越大。该处存在应力集中现象,而且材料表面强度低。螺牙底槽部位存在多源台阶的裂纹源开裂特征形貌,由此推断该部位属于断口的断裂起始区。
螺牙侧面明显可见不同形态的表面裂纹,无论是弯曲裂纹还是分叉裂纹,裂纹的尾部都呈圆钝状,显示挤压变形的折叠裂纹特征,有些螺牙侧面及底槽都存在表面折叠裂纹。在表面折叠裂纹的开口处存在圆弧状的凹坑,这是表面腐蚀的特征形貌,表明在镀锌处理之前,螺栓零件经过酸洗处理,且酸洗处理时间较长,已经在表面形成较深的腐蚀凹坑。在螺牙底槽部位存在锲形撕裂凹坑,螺牙底槽附近的基体呈现严重变形的纤维状组织。由于搓丝加工产生的拉向应力已经大于材料的抗拉强度,因而造成螺牙底槽表面的撕裂凹坑。
螺栓表面存在较严重的表面脱碳层,调质处理过程中热处理炉内保护气氛不规范,因高温氧化脱碳造成螺栓零件表面形成较严重的脱碳层,经测量表面脱碳层深度达0.11mm。该表面脱碳层缺陷组织显著降低材料的表面强度,这是造成螺栓断裂的主要原因。
结论及改进建议
该六角凸缘螺栓断裂的主要原因,是由于调质处理过程中热处理炉内保护气氛不规范,零件因高温氧化脱碳造成较严重的表面脱碳层,显著降低了材料的表面强度。螺栓装配过程中形成拉向应力,在应力集中最大的螺牙底槽产生多条平行裂纹。开裂首先形成于螺牙底槽部位,然后向螺杆心部及纵向继续扩展至最终断裂。
冷镦及搓丝过程形成的折叠裂纹及撕裂凹坑,以及酸洗过程产生的腐蚀凹坑,显著降低了螺栓的加工及使用性能。特别是螺牙底槽部位的折叠裂纹、撕裂凹坑及腐蚀凹坑,加速螺栓的断裂进程。
螺栓在冷镦加工以及搓丝加工过程中,应保证材料的冷加工塑性变形能力,同时控制好一次变形量和变形速率。零件在调质处理过程中,必须严格执行热加工工艺,防止零件表面氧化脱碳,增加材料表面强度及使用性能。在镀锌处理之前的酸洗过程中,必须控制好酸洗液浓度及酸洗时间,进一步降低零件表面的腐蚀程度。
免责声明:本网站所转载的文字、图片与视频资料版权归原创作者所有,如果涉及侵权,请第一时间联系本网删除。
相关文章
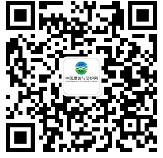
官方微信
《中国腐蚀与防护网电子期刊》征订启事
- 投稿联系:编辑部
- 电话:010-62316606-806
- 邮箱:fsfhzy666@163.com
- 中国腐蚀与防护网官方QQ群:140808414
点击排行
PPT新闻
“海洋金属”——钛合金在舰船的
点击数:7130
腐蚀与“海上丝绸之路”
点击数:5741