1 塔顶油气线检验及损伤情况
焦化装置分流塔顶系统存在H2S-HCL-NH3-H2O低温腐蚀,是装置的重点腐蚀部位,为此塔顶油气线是日常腐蚀监控的重点,需要定期用定点测厚等检测手段对油气线进行腐蚀情况的判定,以防止腐蚀泄漏的发生并对工艺防腐措施进行验证。在装置定点测厚检验时,测厚发现塔顶油气线自分馏塔(C202)顶出口第1个弯头,厚度损失大于50%。见图1(以下简称:油气线弯头),按有关规范判定及强度校核,已不能安全使用,对弯头进行了更换,管线其他部位正常。
塔顶油气线自分馏塔(C202)顶出来,终点至空冷器(A201)入口,管线规格:φ377×9.5mm,材质:20,介质:塔顶油气、水汽、焦粉等,设计温度250℃,操作温度:135℃,设计压力:1.0 MPa,操作压力:0.14MPa。该管线2011年投用至今,上次检修(一年)因腐蚀减薄对部分管段进行了更换。
图1 油气线管道示意图
2 上一周期停工检修检验结果及分析
在一年前的停工大检修中,对分馏塔C202、空冷器A-201及塔顶油气线均进行了检验及腐蚀调查,结果表明分馏塔C202整体状况良好,分馏塔底及1至3层塔盘上存在大量焦粉,各层塔盘无脱落,无腐蚀。空冷器A201,宏观检测发现管板、焊缝、管口内壁有结垢现象,管外壁包裹一层锈垢,除锈后管外壁密集坑蚀,存在严重垢下腐蚀。涡流检测:换热管普遍存在均匀腐蚀加局部坑蚀,个别壁厚损失大于40%,进行了堵管处理剩余换热管壁厚损失20%~40%。说明存在硫氢化铵(NH4HS)结盐腐蚀。
图2 空冷器A-201水冷管(a)(b)、空冷管(c)(d)管箱外观,管束外壁密集坑蚀
塔顶油气线经检验发现有三个弯头减薄严重。最薄处4.86mm,进行了更换,直管段厚度正常。
3 理化失效分析
检验中发现油气线弯头厚度损失大于50%,为进一步查找原因,对该管线进行理化分析
3.1 超声波测厚及强度校核
对油气线弯头外侧、及两侧部位进行厚度检测,外侧厚度范围:4.1mm-7.4mm,距外侧中心线7mm距离,测得两侧部位厚度范围:4.1mm-7.1mm。弯头两侧测厚范围:8.5-9.2mm,该弯头减薄最严重部位在外侧,厚度最薄4.1mm。(强度校核主要参数见表1)
表1 油气线强度校核主要参数
图3 油气线弯头测厚部位示意图
有效厚度计算公式:
式中:tw—计算厚度,mm;P—设计压力, MPa;D—管外径,mm;S—设计温度下许用应力,MPa;φ—焊缝接头系数;Y—计算因数,铁素体钢,在当前温度下取0.4;I—计算系数,
当计算弯管或弯头的外侧厚度时计算公式:
计算I=0.93
计算设计最小厚度(单位mm):
tw =(1.0×377)/(2×(137×0.6/0.93+1.0×0.4))=2.12
强度校核壁厚(有效壁厚计算)(单位mm):
t=实测最小壁厚- 下一检验周期腐蚀余量C
=4.1-((9.5-4.1)/(2019-2011))×3=4.1-2.03=1.97
强度校核壁厚t< 最小设计壁厚tw
依据《压力管道定期检验规则》3.2.3管子、管件壁厚全面减薄评级,耐压强度校核不合格。
3.2化学成分分析
使用PMI-Master Pro/13M0067全谱仪对其油气线弯头进行化分成分分析,结果见表2,可见弯头所用的20号钢化学成分符合GB9948-2013《石油裂化用无缝钢管》标准要求。
表2 化学成分分析结果(质量分数)
3.3 内壁腐蚀状态及能谱分析
将失效的油气线弯头拆下,沿纵向剖开(见图4),观察内壁附着有大量黑色油气产物,截取一部分将其表面清洗干净,发现表面有大面积腐蚀坑,腐蚀坑深度较浅,伴有冲刷痕迹。
图4 油气线弯头内壁形貌
对油气线弯头的腐蚀产物进行能谱分析,得到的腐蚀产物元素组成结果见表3。表3显示,垢物中的元素主要有C、O、Al、Si、S、Fe,垢物中Fe、S元素含量较高, Al,Si元素含量很少。结合表3和油气线介质情况进行分析,判断腐蚀产物主要为含S元素的氧化物或其化合物混合而成,即铁的硫化物,氧化物和过氧化物,属湿硫化氢腐蚀产物。
表3 能谱成分分析结果(质量分数)
3.4 金相分析
按照GB/T13298-2015《金相显微组织检验方法》,经过切割镶嵌制备金相试样,再由多道砂纸预磨、精磨、研磨、抛光和4%硝酸酒精侵蚀,利用德国AXIOPALAN直立光程金相显微镜进行金相分析。
取油气线弯头减薄部位的纵截面,制取金相试样,观察是由管内壁向外壁逐渐减薄。其金相组织为:铁素体+珠光体,晶粒度为8级,夹杂物未发现超标现象(图5)。
图5 油气线弯头金相组织
4 分馏塔顶系统腐蚀机理及控制分析
分馏塔顶部腐蚀主要为低温H2S-HCL-NH3-H2O型腐蚀,原油中大部分氮化物、硫化物和电脱盐后原油含有少量的氧化物经过常减压装置分离以后进入渣油中、它们在焦化过程中裂解,分别生成NH3、H2S和HCL(也可能由装置注水中带人的氯化物)。干态的NH3、H2S和HCL对金属无腐蚀性,但随着塔顶温度的降低,介质中的微量水冷凝,上述腐蚀产物溶解于冷凝水中,形成稀盐酸及湿硫化氢腐蚀环境,对分馏塔顶部塔壁及塔盘、塔顶冷凝冷却系统和塔顶回流系统的设备及管线产生腐蚀。该类腐蚀对碳钢及低合金钢而言,主要表现为稀盐酸对金属均匀腐蚀减薄及局部的点蚀及坑蚀和湿硫化氢应力腐蚀开裂,主要影响因素有腐蚀产物浓度、流速及温度,其中控制露点温度不形成腐蚀产物是工艺防腐的关键。
据计算分馏塔顶露点温度为92.3℃,为满足防腐需求,工艺防腐指标要求应控制分馏塔顶温度高于露点温度14℃。分馏塔顶操作温度实际最小值为125℃,符合工艺防腐指标规定。从实际运行结果得知,分馏塔顶及油气线未发生应力开裂,均匀腐蚀轻微,说明合理的露点温度控制了稀盐酸及湿硫化氢腐蚀。
对焦化分馏塔顶系统,NH4CL及NH4HS结盐是另一种腐蚀形式,其主要原理为焦化过程中裂解生成的气相NH3和HCL、H2S,在一定的温度下结晶形成NH4CL及NH4HS固体铵盐,在设备、管线的低流速部位沉积造成堵塞,影响换热器、空冷器的换热效率。同时NH4CL及NH4HS固体铵盐极易吸水,吸水后形成腐蚀性很强物质,对设备和管线造成垢下腐蚀或其形成的水溶液对金属表面产生磨损腐蚀。NH4CL及NH4HS铵盐水溶液对金属表面的腐蚀主要决定于其浓度和流速,特别是在变径、变向处如大小头、弯头、空冷器入口易造成冲刷腐蚀。上述空冷器(A201)检查所呈现的结垢、腐蚀现象证明焦化分馏塔顶系统存在铵盐结晶,同时油气线腐蚀减薄部位在冲刷严重的弯头外侧,说明铵盐水溶液的冲刷腐蚀是油气线弯头减薄的主要原因。
5 综合分析
通过理化检测分析,油气线弯头化学成分及金相组织未见异常,说明管子本身无质量问题。但通过弯头内壁形貌看出,是从内壁方向腐蚀减薄,且有大面积均匀腐蚀坑,局部减薄严重,并且减薄最严重部位在外侧,厚度最薄4.1mm。能谱检测发现垢物中含有大量硫元素,形成的腐蚀产物,从而会导致弯头由内向外的腐蚀减薄。
根据分馏塔顶系统上一周期检验、腐蚀检查情况及本次在线检测结果表明,分馏塔(C202)、塔顶油气线除上述失效弯头外,整体未发生异常的金属均匀腐蚀减薄及局部的点蚀及坑蚀和湿硫化氢应力腐蚀开裂,说明控制露点温度到位,使塔顶系统低温H2S-HCL-NH3-H2O型腐蚀得到了有效控制。空冷器(A201)检验发现管板、焊缝、管口内壁有结垢及换热管普遍存在堵塞和腐蚀减薄现象说明,塔顶系统存在NH4CL及NH4HS铵盐结盐腐蚀。结合以上事实,说明铵盐的冲刷腐蚀是油气线弯头减薄的主要原因。
6 结论及建议
通过对装置检查中发现的油气线弯头减薄问题,分析所知该管线是由于铵盐的冲刷腐蚀造成。为了达到装置“四年一修”保障装置安全运行,装置目前需要增加和完善的防腐措施,建议从原料性质入手,通过调节上游原料渣油的性质,将原料性质控制在装置设防值的指标范围内,以控制铵盐结晶,同时增加顶循系统的缓蚀剂及水的设施。
加强分馏系统的腐蚀监、检测,发现问题及时处理。根据国内外同类装置经验,炼制高含硫原油后,由于工艺等因素,给分馏系统带来的腐蚀问题,应从工艺防腐蚀和材料升级方面考虑减缓腐蚀。建议加强该部位的腐蚀监、检测,尤其是定点测厚,发现问题及时处理。
作者简介:刘媛媛(1984-),主要从事石油化工设备检验、理化分析、腐蚀与防护工作。E-mail:liuyyws@petrochina.com
免责声明:本网站所转载的文字、图片与视频资料版权归原创作者所有,如果涉及侵权,请第一时间联系本网删除。
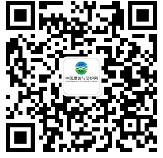
官方微信
《中国腐蚀与防护网电子期刊》征订启事
- 投稿联系:编辑部
- 电话:010-62316606-806
- 邮箱:fsfhzy666@163.com
- 中国腐蚀与防护网官方QQ群:140808414