加工高硫原油对储罐系统的影响及对策
某大型燃料型原油加工企业,各类储罐200多台,其中原油储罐34台,计28台采取内防腐措施。硫含量最高为巴士拉原油(2.65%);酸值最高为魁托油(3.44mgKOH/g),含硫油加工对储罐系统造成腐蚀有所加剧,由于采取了多种防腐措施,有效控制了各类油罐腐蚀,保证了储罐系统正常使用与运行。
油罐腐蚀现状
1 原油罐
在所有油罐中,原油罐的腐蚀较为严重。以原油中转站三台20000m3原油罐为例,投用7年后发生罐底板腐蚀穿孔,最大蚀孔直径达10cm,被迫换底,通过对原油中转站原油罐进行水样分析,发现积水中H2S、SO2、Cl-含量都很高。
2 半成品油罐
半成品油罐腐蚀性也较大,其中焦化粗汽油腐蚀更为严重,罐底(水相)主要表现为非均匀全面腐蚀和垢下腐蚀,腐蚀介质主要为水中溶解氧、H2S、无机盐类,在粗汽油罐的上部及顶部气液相交界处,由于在罐壁表面会形成一层薄薄的水膜,油品中挥发出来H2S及空气O2溶解在水膜中形成腐蚀性较强介质,从而在该处表现为非均匀全面腐蚀,且多以坑点状出现,最大蚀速在0.5~1mm/a。此外,拔头油球罐曾出现湿H2S引起球罐的焊缝及热影响区氢致裂纹。
3 污油污水罐及瓦斯气柜
尽管污油污水罐与瓦斯气柜中H2S及有机硫较成品、半成品油罐与原油要高出许多,但由于从一开始就采取重防腐措施,目前防腐涂层良好,没有对罐体造成腐蚀。
腐蚀机理分析
1 微电池腐蚀
油罐底板积水是造成罐底板电化学腐蚀的重要原因,罐底所含各种离子杂质水溶液与罐底涂层脱落后裸露金属表面构成许多微电池,原油中Ca2+、Fe2+、Mg2+等带电离子增加了电解质水溶液的电导率,加快了腐蚀进程。以罐底板锈蚀为例,腐蚀过程反应产物Fe(OH)2在积水中溶解氧的氧化下生成Fe(OH)3,其进一步氧化成红色铁锈Fe2O3·3H2O。微电池腐蚀由表面开始,逐渐向下扩展形成鼓包和分层,随着腐蚀不断的加深和扩展,进而形成罐底板大面积锈蚀区域。
2 积水中二氧化硫腐蚀
罐底积水中二氧化硫对罐底防腐层脱落钢板可发生酸的再生循环反应。首先由SO2、O2及Fe生成FeSO4,然后FeSO4水解形成氧化物和游离酸,游离酸又加速铁的腐蚀,生成新FeSO4,如此反复循环加速对罐底板的锈蚀。
3 H2S-H2O型腐蚀
当原油罐中内设加热盘管时,往往在加热盘管周围比其他区域腐蚀来得严重,这是由于MgCl2与CaCl2受热水解,氯化氢在有水存在时腐蚀金属。
4 湿H2S环境下的氢致开裂
三台1000m316MnR材质球罐中发现湿H2S氢致开裂,由于焊后没做热处理,加之H2S达200×10-6,投用不长时间在下温带环焊缝热影响区出现大量阶梯状裂纹。另外,液化气球罐、轻油罐顶以及酸性水汽提装置等都普遍存在湿H2S腐蚀问题。
5 细菌腐蚀
原油中淤泥对钢铁产生腐蚀作用的细菌有硫代硫酸盐、硫氧化细菌等,细菌腐蚀促进了罐底钢表面的阳极离子化反应,从而加速罐底板腐蚀。
防腐措施
1 牺牲阳极涂层联合保护
由于罐底操作水层存在,油罐罐底主要表现为电化学腐蚀的特征。因此对罐底进行防腐时,必须进行喷砂处理,要求基材表面达Sa2.5级,然后刷两道环氧导电涂层,选用适合铝合金作阳极材料,施工中铝合金阳极块应均匀布焊在罐底,不得有虚焊,阳极外露表面应清洁,在阳极焊好后对每块阳极进行电流测量确保有效电连接。以确保涂层部分脱落后,罐底能获得有效的电化学保护。
2 热喷涂喷铝+抗静电涂层封闭
热喷涂喷铝前为保证喷涂质量,基材表面需喷砂处理,一般要求Sa3级(即100%喷砂),采用线材火焰喷涂与电弧喷涂两种施工方法,选用抗静电涂料刷涂来封闭孔隙以免腐蚀介质进入基材,一般控制铝层厚度为150μm,涂层总厚度210μm左右。
3 非金属有机涂料
非金属有机涂料涂层是油罐内防腐的重要手段。针对不同油种,选择不同的防腐涂料体系极其重要。成品油罐与20000m3气柜防腐工程,绝大多数油罐经6年使用,没有出现涂层失效与脱落现象。
4 玻璃钢防腐内衬
玻璃钢衬里层主要起屏蔽作用,一般玻璃钢衬里层由底层、腻子层、玻璃钢增强层及面层组成。常用的有环氧、酚醛、呋喃等几种材料。主要应用于含硫污水、污油罐作内防腐内衬。
免责声明:本网站所转载的文字、图片与视频资料版权归原创作者所有,如果涉及侵权,请第一时间联系本网删除。
相关文章
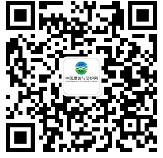
官方微信
《中国腐蚀与防护网电子期刊》征订启事
- 投稿联系:编辑部
- 电话:010-62316606-806
- 邮箱:fsfhzy666@163.com
- 中国腐蚀与防护网官方QQ群:140808414
点击排行
PPT新闻
“海洋金属”——钛合金在舰船的
点击数:7130
腐蚀与“海上丝绸之路”
点击数:5741