回注采出水是油田开发中的一项重要技术。随着陕北油田的不断开发,油田逐步进入高含水期,高矿化度采油污水回注系统的结垢与腐蚀问题越来越突出,已经严重影响了注水体系的正常运行。因此,有必要针对油田注水体系的管线腐蚀与结垢问题进行分析研究,开发出合理经济的防腐蚀治理措施。
陕西延长石油(集团)有限责任公司研究院的科研人员以陕北某油田腐蚀严重区块为研究对象,针对该油田污水回注系统的腐蚀和结垢严重问题,通过现场调研、水质分析、现场挂片腐蚀速率测试等方法,综合分析并评价了四个区块站区污水回注系统的腐蚀和结垢状况,同时进行了防腐蚀技术应用评价,以期为这些技术的现场应用提供数据支撑。
管线的腐蚀程度及腐蚀机理
01油田采出水的水质
按照石油天然气行业标准SY/T 5329-2012《碎屑岩油藏注水水质指标及分析方法》和SY/T 5523-2016《油田水分析方法》,对四个区块站油田采出水的理化性质进行分析,可见四个区块站采出水中,Cl-含量都较高,可能会造成严重的点蚀;S2-质量浓度均超过100mg/L,存在较高的硫腐蚀风险;采出水矿化度为2000~4000mg/L,高矿化度增加了水中离子的导电能力,加快了原电池反应速率,从而加快了原电池的腐蚀速率,对管道腐蚀起到了推波助澜的作用。站区2采出水中的HCO32-、SO42-含量较高,Ca2+含量较低,其余三个站区采出水的Ca2+、Cl-含量很高。四个区块站采出水中存在大量主要成垢离子Ca2+、HCO3-、CO32- SO42- ,说明管道内存在一定的垢下腐蚀风险。
溶解氧是很强的氧化剂,它易使二价铁离子氧化成三价铁离子,从而形成沉淀,溶解氧与腐蚀速率呈正线性关系。硫酸盐还原菌的存在会将采出水中的硫酸盐还原成硫化氢,可能导致管材氢致开裂及应力腐蚀开裂,生成的腐蚀产物硫化亚铁与钢铁表面的黏结性差,易脱落,且电位较正,因而作为阴极与钢铁基体构成一个活性微电池,对钢基体继续产生腐蚀。腐生菌会分泌大量的黏液,黏附在管线上的黏液会造成生物垢堵塞,也会产生氧浓差电池而引起管道腐蚀。
02现场挂片试验
地面管线中的油水混合物,进入站区进行油水分离后,进入污水罐,为了真实反映各个区块站采出水的腐蚀情况,分别在四个污水罐内悬挂挂片测试腐蚀速率。挂片材料为Q235钢,尺寸为80mm×25mm×3mm,现场腐蚀挂片的测试周期为150天。
试验结束后,取出挂片,按照石油天然气行业标准SY/T5329-2012《碎屑岩油藏注水水质指标及分析方法》附录B中化学清洗法进行处理,洗净后的挂片用无水乙醇脱水;干燥后称量,通过失重法计算腐蚀速率。
图1 挂片在不同站区采出水中的平均腐蚀速率
由图1可见:试样在3号采出水中的腐蚀最为严重,在1号和4号采出水中的腐蚀速率较大,在2号采出水中的腐蚀程度最轻。按照SY/T 0087.2-2012《钢质管道及储罐腐蚀评价标准埋地钢质管道内腐蚀评价》,试样在2号采出水中的腐蚀属于中级(0.025≤平均腐蚀速率0.12mm/a),在1号和4号采出水中为较重级别腐蚀(0.12mm/a≤平均腐蚀速率≤0.25mm/a),在3号采出水中的腐蚀最为严重,平均腐蚀速率超出严重级别指标(≥0.25mm/a)3倍以上,腐蚀问题十分严重。
(a) 1号 (b) 2号
(c) 3号 (d) 4号
图2 试样在四种采出水中腐蚀180天后的表面形貌
由图2可见:试样在2号采出水中表面腐蚀较轻,在其他采出水中的表面腐蚀均较为严重,尤其是在站区3的腐蚀最为严重。挂片均表现为典型的局部腐蚀特征。
除去腐蚀产物后,试样的最大腐蚀坑深度已达2.5mm,如果选择无任何防护措施的普通管材,一年内的最大腐蚀深度将会超过5mm。按照标准SY/T0087.2-2012《钢质管道及储罐腐蚀评价标准埋地钢质管道内腐蚀评价》,属于严重腐蚀,其穿孔年限为1~3年,这进一步说明了腐蚀情况的严重性。
03腐蚀产物分析
采用X射线衍射仪(XRD)对四个区块站中管线的腐蚀产物进行采集分析,可见在1,3,4号采出水中,管线表面腐蚀产物中存在FeCO3,这说明管线在这些站区可能存在二氧化碳腐蚀,FeCO3的形成机理见下式:
Fe+H2O+CO2→FeCO3+H2 (1)
在1号和3号采出水中,腐蚀产物中存在大量FeS,说明采出水中存在H2S。采出水中的H2S主要来源于两方面:一是来源于地层,二是来源于SO42-被硫酸盐还原菌(SRB)还原生成H2S。
另外还可见,在1号和4号采出水中,腐蚀产物中高含FeO和Fe2O3,说明管线在此环境中可能存在溶解氧腐蚀,见下式:
在2号采出水中,腐蚀产物中的Ca2+ CO32-含量较高,即CaCO3含量较高。而Fe3+ Fe2+含量相对较低,推测此环境中水质结垢严重,腐蚀较轻,与现场挂片试验结果相符。
FeCO3、FeS、FeO、Fe2O3等腐蚀沉积物及CaCO3、CaSO4、MgCO3等无机盐垢,可能会不均匀地分布在管道内表面,形成锈垢层。由于垢层的阻塞作用,会使垢下成为贫氧区,并与垢层外部形成氧浓差电池。通常垢层具有阴离子选择性,垢层下的Fe2+难以扩散,造成正电荷过剩,使得外部的Cl-迁入导致垢下环境酸化,从而造成严重垢下腐蚀。
防腐蚀措施及其室内效果评价
室内挂片试验及水质分析结果表明,四种采出水成分复杂,管线的腐蚀影响因素众多、失效形式多样。因此,在选择防腐蚀技术时,既要考虑防护效果、作业的难度和相关风险,又要考虑现场的经济适用问题。故本工作针对不同腐蚀类型选择了如下防护措施,并进行了防护效果评价。
01选择涂层
目前,管道防腐蚀涂层品种较多,性能也各不相同,正确选择合格涂层与延长管线使用寿命有着密切的联系。根据腐蚀环境、输送介质等条件,并通过室内评价,选用了QC-01涂层。在盐水、油等条件下浸泡QC-01涂层,表面无鼓泡,且涂层符合API RP 5L2附着力及剥离试验要求,说明QC-01涂层具有良好的附着力。将QC-01涂层置于250℃下加热30min,随后室温水冷却,涂层表面无剥离、无开裂、无鼓泡、无黏接力损失等,即该涂层具有良好的耐热性;按照ASTM D522 ASTM D968等标准开展弯曲及磨损试验,QC-01涂层也具有较好的抗弯耐磨性能。综上,推荐使用QC-01涂层。
02设计阴极保护
目前,小口径管线(管径<60mm)的内壁涂层现场施工较为困难,即使在室内完成涂层施工也很难做到100%无针孔。此外,内壁涂层在使用过程中常遭受磨损,加之涂覆管线接头存在一定的困难,故配合采用阴极保护可有效减少腐蚀穿孔。牺牲阳极保护法是最早应用的阴极保护方法,具有简单易行,不需要电源,不干扰邻近设备和装置。国内常用的牺牲阳极材料有镁、锌、铝及其合金等。
牺牲阳极的输出电流取决于其形状和尺寸,本工作选用线状阳极应用于管线内壁。在实验室测试镁、锌、铝合金的阴极保护电位(相对于铜/硫酸铜参比电极),可见三种合金均符合SY/T 6964-2013《石油天然气站场阴极保护技术规范》标准的要求(阴极保护电位为-0.85V或更负),其中铝合金阳极的保护效果最好,镁合金阳极和锌合金阳极的保护效果较差。
03设计特殊接头的结构
设计特种接头的目的是解决涂覆涂层后管线焊接对接口涂层的破坏。本工作选择三种方案:
方案一是采用耐高温涂层,该涂层能够耐高温2700℃,试验结果表明该方案效果不理想,焊接后涂层表面起泡,即方案一不可取;
方案二是采用耐火保温材料与高温涂层联合使用,经室内试验验证,涂层完好;
方案三是采用新型耐高温隔热陶瓷接头,该接头具有良好的隔热耐温性能和耐腐蚀性能以及在温度剧烈变化时的抗炸裂性能和抗渗透性能,但缺点是强度和韧性较差。
经过室内试验,在温度剧烈变化的条件下,该接头的抗炸裂性能和抗渗透性能都能满足要求,存在的问题是在保证强度和韧性的前提下接头壁厚太厚,内径变化很大,影响管线的正常施工。综上推荐使用方案二。上述三种方法的测试结果见图3。
图3 三种保护方案对特殊接头的防护效果
现场防腐蚀施工
研究了区块站管线的腐蚀影响因素和机理,结合该区内油田的实际生产状况和防腐蚀要求,选择了QC-01涂层、上述推荐使用的方案二特殊接头加线状阳极阴极保护技术,同时对其现场应用效果进行评价。
01现场实施方案
试验场地为陕北某油田站内清水罐进口位置;试验周期为12个月。工艺流程设计如下:试验管线由八段短管道组成,每段管道长0.6m,两端由法兰相互连接,编号依次为No.1~No.8,No.1为裸管,No.2为外涂层管,No.3和No.4为涂层加特殊接头管道,No.5~No.7为施工线状阳极(分别为镁阳极、铝阳极、锌阳极)管道,No.8为内涂层+线状铝阳极管道。连接法兰的编号为:1~8,为了保证No.5~7管道测量数据的准确性和阴保效果,法兰1 2 3为钢普通法兰,法兰4 5 6 7 8为钢绝缘法兰。工艺流程见图4。
图4 工艺流程图
02腐蚀速率
经过12个月现场试验后,将No.1~8号管道取出并解剖,常温下取不同位置的多个小样置于清洗液中搅拌直至腐蚀产物清除干净;酸洗后的试样经过冲洗,放入饱和碳酸氢钠溶液中浸泡2~3min进行中和处理,再用无水乙醇脱水3~5min;最后将试样吹干放入干燥器中干燥24h后,用电子天平称量,通过失重法计算其腐蚀速率。结果表明,裸管的腐蚀速率为0.743mm/a,根据标准SY/T0087.2-2012《钢质管道及储罐腐蚀评价标准埋地钢质管道内腐蚀评价》,属于严重级别腐蚀,说明不采用防护措施的管线存在严重腐蚀问题。对于内涂层管道,由于内涂层覆盖紧密,无破损点,没有腐蚀。
03阴保效果
按照标准要求,选择三个月为一个测试周期,对四种含线状阳极的管道进行测试,结果见下表。
可见对于无内涂层的裸钢管道,使用线状牺牲阳极,阳极的消耗量大,90天后No.7管道的保护电位高于标准SY/T6964-2013《石油天然气站场阴极保护技术规范》规定-0.85V的标准,已经失去保护作用。在整个试验结束时,镁合金阳极和锌合金阳极已经全部损失。在内涂层管中使用牺牲阳极,保护效果很好,保护电位基本稳定。即使随着使用时间的增加,内涂层出现破点,牺牲阳极也能提供足够的保护电流,阻止管线发生腐蚀,延长使用寿命。
04特殊接头的现场应用效果
采用耐火保温材料与高温涂层联合使用方法所设计的特种接头可以解决管线内涂覆涂层后管线焊接对接口涂层的破坏问题,涂层管特殊接头内部形貌见图5。
图5 特殊接头的内部形貌
该接头使用1年后,内涂层致密、无破点。接头两端采用特种密封胶和耐高温密封圈双重密封,达到了阻止输送钢管内介质进入接头本体和输送钢管内壁之间间隙的目的。在接头中部焊接热影响区部位绕缠耐火隔热材料,保证了在输送管焊接后,涂层不遭受损害。以上措施保证了焊接接口部位的防腐蚀等级与管体防腐蚀等级的一致性,延长了管线使用寿命。
防护方法的经济性
调研发现,该油田站外新建注水管线内部未采用保护措施时,管线使用2~3年便会发生腐蚀穿孔,从而导致管线更换。针对这一问题,该项目采用了内涂层和牺牲阳极阴极保护联合使用的方法,并进行了经济性能预测。目前,油田地面管线的设计寿命为20年,按照管线的使用情况,结合现场管线更换年限的统计数据,在基于管线局部腐蚀速率的基础上,设计使用期20年内未加保护的管线需要进行7次以上的维修更换。施加阴极保护和内壁涂层管线的设计寿命分别为7年和10年,因此,在注水管线的使用期内分别需要更换1次和2次。采用内涂层和牺牲阳极阴极保护的注水管线和裸钢的注水管线的经济性评价如下表所示。
由表可以得出,实施涂层加阴极保护防腐蚀措施后,生产运行总成本能够节约34%以上。
结 论
1地面管线腐蚀是由腐蚀性离子(Cl- S2-)?CO2 细菌及溶解氧共同作用造成的。
2按照现场挂片腐蚀速率进行划分,站区2属于中等级别腐蚀,站区1和4属于较重级别腐蚀,站区3属于严重级别腐蚀,局部腐蚀速率最高可达6mm/a。
3QC-01涂层具有较好的使用性能;镁、锌、铝合金牺牲阳极的保护效果不同,均符合标准要求,其中铝合金阳极的保护效果最好,镁合金的次之,锌合金阳极的较差;特殊接头选用耐火保温材料与高温涂层联合使用。
4采用涂层、特殊接头加线状阳极阴极保护联合防腐蚀措施,管道内涂层覆盖紧密,无破损点,阴极保护电位高于标准,管线没有腐蚀。
5实施涂层加阴极保护防腐蚀措施后,生产运行总成本可节约34%以上。
免责声明:本网站所转载的文字、图片与视频资料版权归原创作者所有,如果涉及侵权,请第一时间联系本网删除。
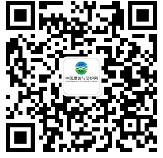
官方微信
《中国腐蚀与防护网电子期刊》征订启事
- 投稿联系:编辑部
- 电话:010-62316606-806
- 邮箱:fsfhzy666@163.com
- 中国腐蚀与防护网官方QQ群:140808414