摘要
针对所提出的恒电位脉冲电沉积铜锡技术,研究工艺条件对镀层成分、晶粒尺寸及耐蚀性能的影响规律,摸索恒电位脉冲电沉积高锡青铜的最优工艺。利用SEM观察分析恒电位脉冲与恒电流脉冲电沉积铜锡镀层的形貌及晶粒尺寸,结合EDS分析电沉积方式对镀层成分分布的影响规律,使用电化学工作站表征镀层的耐蚀性。结果表明,使用占空比33%、沉积电位3 V的恒电位脉冲电沉积工艺,降低了镀层溶解几率而维持络合离子迁移、沉积驱动力,因而对不同尺寸零件均可稳定获得高锡青铜镀层。相同初始条件下,恒电流脉冲镀层平均厚度约6 μm;而恒电位脉冲具有更大的沉积速率,膜层厚度在10 μm以上,且镀层成分比恒电流脉冲镀层更均匀、孔隙率低、晶粒团簇少、耐蚀性能优良,在截面积为78.5 mm2的试样上镀层阻抗较恒电流脉冲提高了两倍。恒电位脉冲还可获得纳米Cu-Sn镀层,晶粒尺寸小于100 nm。相对恒电流脉冲,恒电位脉冲电沉积提高了铜锡镀层质量及耐蚀性,且有利于复杂零件的成分控制及自动化生产。
关键词: 高锡青铜; 恒电位脉冲; 恒电流脉冲; 电沉积; 耐蚀性
铜锡合金镀层平整光亮,耐蚀性能和耐磨性能优异,在液压支柱、千斤顶等中常作为防护性镀层[1-4]。铜锡合金中按铜锡组分差异一般分为低锡青铜、中锡青铜和高锡青铜。低锡青铜为含锡15%(质量分数) 以下的铜锡合金,其在空气中易氧化变色,而中锡青铜含锡15%~30%,二者均不宜做表面镀层。含锡40%以上的铜锡合金为高锡青铜,其在空气中稳定性好、硬度高、耐蚀性能优异,在五金件中常作防护装饰层[5,6]。传统电沉积铜锡工艺主要采用恒流电镀[7],其制备的镀层晶粒大、渗氢严重,在使用中易出现鼓泡现象。脉冲电沉积可降低阴极浓差极化[8,9],有效减少渗氢,改善铜锡镀层性能。目前,已有恒电流脉冲电沉积铜锡的相关研究[10-12]。吴珂[10]在焦磷酸盐-锡酸盐体系通过恒电流脉冲方式获得了铜锡合金镀层,研究该镀层腐蚀形貌显示其腐蚀时主要为小孔腐蚀。李福永等[11]对比了直流电镀与恒流脉冲电镀铜锡合金的渗氢行为,研究显示恒电流脉冲电沉积铜锡镀层渗氢量较直流电沉积减小,占空比和脉冲频率对镀层渗氢影响显著。恒电流脉冲电沉积铜锡由于镀层性能较佳,无须使用参比电极及镀层厚度可控而得到应用。该工艺的不足在于镀层成分不易控制,且对于不同尺寸的零件需要重新计算和调整电流密度,操作复杂,不利于自动化控制[13]。而恒电位脉冲电沉积由于需要增加参比电极且可能因镀层-溶液界面电阻与施加电位接近而发生重新溶解,其研究及应用一直受限。目前,恒电位脉冲电沉积高锡青铜工艺的研究未见报道。恒电位脉冲电沉积可适应零件尺寸变化自动调整电流,有学者通过该方式制备了晶粒尺寸100 nm以下的纳米Ni-Fe-Cr、纳米Co-Ni等,表明恒电位脉冲电沉积还可细化晶粒[14-17]。因此,本文尝试将恒电位脉冲电沉积法运用于高锡青铜耐蚀镀层制备,探究其与恒电流脉冲电沉积铜锡工艺在镀层成分、晶粒尺寸及其耐蚀性能的异同,为提高企业镀层质量及自动化程度提供理论与实际指导。
1 实验方法
1.1 基体预处理
选用27SiMn钢为基材,加工成横截面积分别为78.5和270 mm2的试样 (分别标记为试样A和试样B),用于不同尺寸零件脉冲电沉积。基体试样经砂纸打磨后,置于60 g/L NaOH+30 g/L Na2CO3+46.5 g/L Na3PO4·12H2O+11.5 g/L Na2SiO3·9H2O的碱液中,于70 ℃除油10 min。再用10% (质量分数) 氢氟酸+ 10%硫酸溶液进行活化,时间为30 s。每步工序后均使用蒸馏水清洗、吹干。
1.2 恒电位脉冲和恒电流脉冲方式电沉积铜锡镀层
以无氰焦磷酸盐为基础镀液,镀液配比为:CuSO4·5H2O 15 g/L,SnCl2·2H2O 8.05 g/L,K4P2O7·3H2O 250 g/L,K2HPO4·3H2O 60 g/L,C6H5Na3O7·2H2O 20 g/L,H3PO4 2 mL/L,C6H15O3N 2 mL/L。使用NHDP-12V6A智能脉冲电源进行铜锡合金镀层制备。恒电位脉冲沉积工艺参数为:输出电压3 V,占空比33%,电镀30 min。恒电流脉冲电沉积工艺参数为:输出电流0.2 A,占空比33%,电镀时间10 min。图1为恒电流和恒电位脉冲电沉积工艺参数示意图。铜板为阳极,基材为待镀电极,作为阴极,恒电位脉冲沉积时使用甘汞电极作为参比电极。镀膜后的样品经蒸馏水清洗。
图1 脉冲电沉积工艺示意图
1.3 镀层检测与分析
采用SU6600型扫描电镜 (SEM) 进行镀层表面形貌及晶粒尺寸观察,结合能谱仪 (EDS,Octane Elect Plus) 和NexION 350DICP-MS等离子体质谱仪分析镀层元素组成及分布,采用TIME2600涂层测厚仪对电沉积膜层进行厚度测试。室温下利用Im6/Im6ex电化学工作站对镀层进行开路电位与阻抗测试,介质为自来水。测试时采用三电极体系,饱和甘汞电极为参比电极,铂片为对电极,工作电极为待测样品。阻抗测试时扰动电压幅值为10 mV。
2 结果与讨论
2.1 铜锡镀层的微观形貌与成分分析
图2和3为不同截面尺寸的两种试样上脉冲方式电沉积膜层的SEM像及EDS线扫描分析结果。可知,阴极为截面积270 mm2的试样时,采用恒电流脉冲电沉积的镀层其Sn特征X射线计数强度在80~115,而Cu计数强度为120~180;恒电位脉冲镀层Sn计数强度为80~145,Cu计数强度为110~160。在线扫描中,元素特征X射线计数强度可表征元素含量,计数强度大,元素含量高。因此,对于27SiMn钢基体,恒电流脉冲电沉积镀层Sn含量波动较小,而恒电位脉冲法Cu含量波动较小;二者铜锡元素整体分布接近,镀层无显著优劣。
图2 不同截面尺寸试样上脉冲方式电沉积膜层的SEM像
图3 不同截面尺寸试样上不同脉冲方式电沉积膜层的线扫描分析结果
而阴极为截面积78.5 mm2的试样时,恒电流脉冲电沉积镀层Cu特征X射线计数强度为120~450,其Sn计数强度为300~460;而恒电位脉冲镀层Cu计数强度为20~110,Sn计数强度为85~300。恒电流脉冲电沉积镀层Sn计数强度波动与恒电位脉冲下的基本相近,但Cu的波动明显大于恒电位脉冲下的;且元素分布严重不均,宏观形貌上表现为颜色不均匀。这是由于恒电流脉冲沉积,在恒定0.2 A脉冲电流条件下,待镀件A截面积较小,膜层实际电流密度超过了其极限电流密度,导致镀层局部烧焦,成分不均。而恒电位脉冲条件下,截面积小的A试样电沉积阻力大,电流可自发减小至极限电流密度之下,铜锡离子正常迁移、沉积,因而其镀层中铜锡含量波动较小。
恒温50 ℃下,使用含硝酸5% (质量分数)、盐酸5%的混合溶液将镀层溶解,待镀层完全溶解后,对溶液进行NexION 350DICP-MS等离子体质谱分析,得到不同截面尺寸的试样上电沉积镀层的Sn含量,如表1所示。
表1 不同截面尺寸试样上不同脉冲方式电沉积膜层中的Sn含量
由表1可知,对于B试样,恒电流脉冲电沉积铜锡镀层中的平均Sn含量约为37.5%,为中锡青铜;而A试样上镀层Sn含量达55.9%,为高锡青铜。这表明,恒电流脉冲电沉积于不同尺寸零件上制备的铜锡镀层存在显著差异,这不易于控制镀层成分,因而该工艺在更换零件尺寸时必须重新计算与设定脉冲参数。值得注意的是,图2a与c中Cu含量增加集中于最外层质点,Cu含量降低则发生于内层质点,即恒电流脉冲工艺还易造成镀层沿厚度方向分布不均。结合恒流电沉积过程中槽电压逐渐下降的现象,分析镀层厚度方向分布不均的原因为:恒电流脉冲电沉积时,随膜层增厚,电沉积阻力减小,槽电压减小。槽电压减小,则体系中主要的络合离子[Cu(P2O7)2]6-与[Sn(P2O7)2]6-迁移及还原受阻[18,19],外层沉积的质点中Sn含量减少,Cu比例上升,镀层沿厚度方向分布不均。
而恒电位脉冲法结果与之不同。截面积为270 mm2的A试样,恒电位脉冲电沉积铜锡镀层中平均Sn含量为46.1%,而截面积为78.5 mm2的B试样其镀层平均Sn含量约为51.7%,二者相差不大,均为高锡青铜。这表明,恒电位脉冲电沉积较恒电流脉冲更利于成分控制,稳定获得高锡青铜镀层,且可根据零件尺寸灵活调整施镀电流,便于实现某一特定成分、不同尺寸零件的自动化生产。图2b和d中,Cu含量在最外层质点与内层质点均有出现增加,这表明薄膜内外层铜锡比例接近,元素沿厚度方向无差异。其原因为,恒电位脉冲电沉积时,槽电压维持定值,整个沉积过程中体系中主要的络合离子迁移、还原驱动力不发生改变,故而镀层内外铜锡原子比例接近定值,最终镀层成分较为均匀。
2.2 铜锡镀层的晶粒尺寸分析
由图2a和c可知,A和B试样于恒电流脉冲电沉积铜锡晶粒尺寸分别为0.11~1.7和0.12~1 μm。B试样上镀层晶粒呈球状,连接紧密,且晶粒尺寸相对接近 (其中亮白色物质为杂质)。而A试样的镀层中有较多不规则的团聚粒子且比较疏松,存在大量孔隙;这是由于恒电流下,通过截面积小的柱状试样表面的电流密度高,形核、生长快,原子沉积量大,导致突出点迅速增长,颗粒明显长大;而空隙的形成原因为电流密度过大,析氢副反应加快,引起镀层疏松多孔。
由图2b和d可知,A和B试样于恒电位脉冲电沉积铜锡镀层的晶粒尺寸分别为和0.09~0.5和0.16~1.5 μm。B试样块状样品下镀层亦主要呈球状,连接紧密 (其中,亮白色物质为杂质)。A试样样品下电沉积镀层主要为小球状,其晶粒极小,为小于100 nm的纳米晶。这是由于截面积较小,槽电压恒定时其电流增大,而低于极限电流密度时电流适度增大可促进粒子快速寻找到最低能量点沉积,在断电周期,晶体停止生长,电流再次导通时新晶核生成。因此,沉积粒子不易团簇、生成枝晶,从而晶粒得到细化,获得纳米晶。
2.3 铜锡镀层厚度分析
使用TIME2600涂层测厚仪对不同截面尺寸试样上脉冲方式电沉积膜层进行了厚度测试,结果如表2所示。可知,对于不同截面尺寸的试样,恒电流脉冲电沉积镀层平均厚度接近,约为6 μm;而恒电位脉冲电沉积镀层平均厚度均在10 μm以上。这表明相同条件下,恒电位脉冲电沉积具有更高的沉积速率。故而在恒定时间内,恒电位脉冲镀层较恒电流脉冲镀层更厚。
表2 不同截面尺寸试样上脉冲方式电沉积镀层的厚度
试样B上恒电流和恒电位脉冲电沉积镀层横截面微观形貌如图4所示。可知,试样横截面均出现了显著的衬度差异,自下而上依次为牙托粉层 (镶嵌样品)、铜锡膜层和基体层。牙托粉与膜层间存在间隙,而膜层与基体结合较为紧密。此外,恒电势脉冲电沉积镀层厚度均在10 μm以上,而恒电流脉冲电沉积镀层平均厚度仅为6 μm。这再次表明恒电位脉冲电沉积具有更高的沉积速率,与前述测试分析结果相吻合。
图4 不同脉冲方式制备镀层的截面微观形貌
2.4 铜锡镀层耐腐蚀性能
在室温下测定基体、试样B上恒电流脉冲镀层、试样A上恒电位脉冲镀层的阻抗如图5和6所示。由图5可知,对于试样B,基体、恒电流脉冲镀层、恒电位脉冲镀层三者在低频0.01 Hz时,阻抗分别为1500,12200和14500 Ω·cm2。恒电位脉冲电沉积的镀层阻抗最大,发生腐蚀时传递阻力大,抵抗腐蚀能力最强,比基体提高了6倍以上,优于恒电流脉冲方式下获得镀层的。图6表明,对于截面积较小的试样A,恒电位脉冲电沉积镀层优越的耐蚀性能更为凸显,0.01 Hz时其阻抗约为恒电流脉冲镀层的两倍。这是由于截面积较小时,恒电流脉冲镀层易烧焦,镀层成分不均匀,为中锡青铜,其在腐蚀介质中容易发生点蚀,耐蚀性能较差;而恒电位脉冲较恒电流脉冲电沉积速率快,相同条件下镀层更厚,增厚的膜层可有效防止腐蚀介质中侵蚀性离子向基体渗透,延缓了微型腐蚀电池的形成;同时镀层成分均匀,为Sn含量46%以上的高锡青铜,在腐蚀介质中化学性质稳定,故其阻抗值高、耐蚀性能优异。
图5 试样B及其在不同脉冲方式沉积镀层的Bode图
图6 试样A及其在不同脉冲方式沉积镀层的Bode图
2.5 恒电位脉冲电压法镀层的溶解问题
恒电流脉冲可瞬时恢复电沉积初始条件,而恒电位脉冲在脉冲结束时存在一定的恢复过程,故可能发生沉积金属的溶解。为此,对恒电位脉冲电压法下制备的镀层进行开路电位测试,其结果如图7所示。可知,恒电位脉冲电沉积镀层-溶液的稳定电位在0.45~0.5 V。无外加电流时,金属材料在腐蚀溶液中达到稳定状态的电位为自腐蚀电位,此时金属材料发生金属溶解与去极化剂还原的共轭反应。恒电位脉冲电沉积未得到广泛应用的局限之一正在于电位脉冲结束后重新达到初始电位时,在自腐蚀电位附近可能出现金属镀层的溶解。因此,本研究使用高占空比 (33%),延长脉冲周期,从而减少电位恢复次数;同时选用脉冲电位3 V,与自腐蚀电位0.45~0.5 V保持较大差值。二者协同作用,有效降低镀层的溶解几率,利于提高铜锡电沉积速率,制备出较厚膜层。镀层厚度实验结果与之吻合。此外,高占空比 (30%) 条件下,阴极消耗的Cu2+与Sn2+获得了充分的补充时间,有效减少了氢离子的还原,减轻了镀层渗氢[11]。同时,高占空比下通断时间较长,晶粒团簇和生长被抑制,晶粒细化,从而利于获得质量较佳的镀层。实验结果也证实,该工艺制备的铜锡镀层成分均匀,最小晶粒尺寸小于100 nm。综上可知,30%高占空比、恒电位3 V进行脉冲电沉积,可克服恒电位脉冲沉积镀层溶解缺陷,获得综合性能优异的高锡青铜镀层。
图7 恒电位脉冲电沉积镀层的开路电位
3 结论
(1) 恒电位脉冲电沉积可自发适应零件尺寸变化制备高锡青铜,镀层成分均匀;而恒电流脉冲在不同零件上制备的镀层成分差距大,沿厚度方向分布不均,且不能稳定获得高锡青铜层。
(2) 采用恒电位脉冲模式在截面积为78.5 mm2的27SiMn试样上获得了纳米Cu-Sn镀层,晶粒尺寸小于100 nm。而采用恒电流脉冲模式时,由于试样截面积较小而表面电流密度较高,镀层形核、生长较快,原子沉积量大,突出点迅速增长,颗粒明显长大;且电流密度高引起析氢副反应加快,造成镀层孔隙率高。
(3) 33%的高占空比、3 V沉积电位下进行恒电位脉冲电镀铜锡,因可以减少电位恢复且远离自腐蚀电位而克服了镀层溶解缺陷;且电沉积速率高,所制备的高锡青铜耐蚀性能强,其阻抗值高于恒电流脉冲镀层的,综合性能更优。
免责声明:本网站所转载的文字、图片与视频资料版权归原创作者所有,如果涉及侵权,请第一时间联系本网删除。
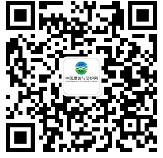
官方微信
《中国腐蚀与防护网电子期刊》征订启事
- 投稿联系:编辑部
- 电话:010-62316606-806
- 邮箱:fsfhzy666@163.com
- 中国腐蚀与防护网官方QQ群:140808414