金属作为主要结构材料,在工业领域发挥着重要作用。在实际生产、运输和装配过程中,金属表面常常会出现划伤缺陷。金属构件在特定的服役环境中,表面划伤缺陷处的力学状态、水化学环境都具有一定的复杂性,这严重影响了金属构件的服役安全,降低了其服役寿命。在现有工程环节,核电站蒸汽发生器传热管表面划伤问题难以避免。在高温高压水服役环境中,表面带有划伤的传热管面临着发生应力腐蚀开裂(SCC)的风险,潜在影响着核电站的安全稳定运行。因此,理清表面划伤的变形行为、破坏机制及其对传热管SCC抗力的影响具有十分重要的意义。
表面划伤及其影响因素
早在19世纪,MOHS就采用划伤法科学地比较了两种材料的硬度,开启了对表面划伤问题研究的先河。
至今,划伤测试还广泛应用于金属、高分子材料及涂层等领域以评估材料的硬度、耐划伤性能、涂层与基材的结合强度、金属表面钝化膜的再钝化性能等。此外,划伤还被应用于微纳米加工过程,如压痕光刻技术使用不同形状的金刚石压头并通过控制载荷,在基材上可以形成具有不同凹坑或沟槽的图案。
典型的表面划伤过程可以描述为:以特定的力将硬而尖的压头压入材料,压头以某一速度在基体表面层运动并使基体表面产生机械变形的过程。在表面划伤过程中,材料的变形机制主要包括弹塑性变形、材料断裂和碎屑分离。
划伤过程和程度受以下三方面因素影响:
1|压头几何参数
在划伤过程中,压头进给使基材发生变形,因此,压头的几何参数会影响划伤过程及基材的损伤特征。实际工程中的划伤,也因划伤来源不同,对应不同的划伤形貌(深度、宽度、角度等)。
压头尖端形状影响着划伤凹槽的变形情况,如相比于立方角状压头,球状压头造成的划伤影响区塑性变形较小。
圆锥形压头广泛应用于模拟工程中金属表面意外划伤的研究,其最关键的几何参数之一为锥形压头攻角(锥形压头半角的余角)。研究表明,使用大攻角的锥形压头进行划伤时,划伤凹槽前端塑性变形更为剧烈,但其所造成的划伤影响区小于小攻角压头。
2|划伤速率
在评估涂层与基材结合力的划伤试验中,涂层分离的驱动力是由弹性变形应力、摩擦应力及涂层内部残余应力共同构成的。涂层恰好发生破坏时所施加的法向载荷称为临界载荷,涂层对基材的附着力决定了临界载荷的大小。另外,划伤速率还可能会影响划伤凹槽区域的物相组成。
3|载荷
根据理论模型研究表明,划伤载荷的大小影响着划伤影响区的变形特点。研究发现随着法向力的增大,划伤变形从弹性变形向塑性变形转变,最终发展为断裂;随着法向力的不断增大,划伤过程由摩擦变形转变为犁耕变形。此外,划伤载荷还影响着划伤凹槽的形貌。如有研究发现随着载荷的增大,划伤凹槽两侧的堆积峰变高,磨损量与应变、载荷呈正比。
传热管材料及其服役环境
蒸汽发生器是压水堆核电站的关键部件之一,它的主要功能是将热量从一回路传至二回路,形成高温蒸汽进而推动汽轮机发电。蒸汽发生器的主要金属构件有传热管、管板和管支撑。传热管是蒸汽发生器的核心部件,由于长期服役于苛刻的高温高压水工况中,其腐蚀和应力腐蚀开裂(SCC)问题是威胁压水堆核电站安全运行的重要因素。
早期传热管材料常采用奥氏体不锈钢及镍基600合金,但在运行过程中均出现了严重的SCC。为了解决这个问题,人们不断开发出各种传热管材料。1992年,加拿大B&W公司Millstone 2号反应堆开始使用镍基690TT合金作为传热管材料。得益于较高的Cr含量,镍基690TT合金作为新型传热管材料,无论是处于几何缝隙内、含氯、含铅环境,还是在除氧高纯水等环境中,其SCC抗力均显著优于镍基600合金和304型不锈钢。目前,镍基690TT合金因出色的抗SCC性能,已经成为压水堆核电站最广泛使用的蒸汽发生器传热管材料。
蒸汽发生器传热管服役环境为高温高压水环境。在二回路侧,腐蚀和SCC多发于传热管和管板顶端区域、管板顶端表面附近的淤泥区、管支撑与传热管间的传热缝隙区,如下图所示。
蒸汽发生器中产生传热缝隙的几何结构:(a) 管板顶端缝隙;(b) 管板顶端淤泥区;(c) 管支撑
传热缝隙中存在着因过程蒸发导致的离子浓缩和沉积效应,导致Na+,K+,Ca2+,Cl-,SOx等杂质离子局部浓缩富集。在传热管与管支撑的接触区域,传热缝隙内的杂质离子浓缩浓度可以增大六个数量级,形成侵蚀性极强的局部环境。传热缝隙内的温度、杂质离子浓度、电化学势及流体性质呈剧烈的梯度变化,这极大地促进了腐蚀和SCC过程。此外,在压水堆核电站运行过程中添加的药剂也使得杂质离子种类变得复杂多样。例如,为了降低二回路中溶解氧(DO)含量和蒸汽发生器用合金材料的腐蚀电位,二回路的给水通路中通常会加入联氨(N2H4)等药剂。联氨的加入可使SO42-被还原成为低价S,如HS-、H2S、S4O62-和S2O32-等。
可见,传热管服役环境复杂而苛刻,极易受到局部腐蚀的影响。
传热管表面划伤致应力腐蚀失效案例
蒸汽发生器传热管约占一回路边界承压面积的80%,而现行通用的传热管壁厚为1~1.2mm。运行经验表明,传热管是一回路压力边界处的脆弱部位之一。传热管一旦失效,可能导致放射性物质由一回路泄漏至二回路,严重时需进行停堆堵管处理。
目前世界上已发生了多起由表面划伤缺陷导致的蒸汽发生器传热管SCC失效案例,其中两个典型案例如下:
01 1992年McGuire2号堆的蒸汽发生器传热管发生了泄漏事故。
对事故构件进行失效分析发现,裂纹萌生于传热管自由端区域,而传统认为该区域不易发生SCC。相比而言,暴露于工况条件更为苛刻的浓缩环境中(即传热缝隙之中)的管段却未发生失效;而传热管自由端的表面却发生了失效,且裂纹萌生于传热管表面划伤缺陷的位置,这受到了人们的广泛关注。
02 由美国Duke公司于1973年4 月投入商业运营的Oconee核电站的1号、2号反应堆曾发生过蒸汽发生器传热管的SCC。
工作人员经过检查,取出了7根问题传热管,经分析,其中一根取自自由端的600合金传热管,在表面划伤处出现了SCC裂纹的萌生与扩展,且其裂纹扩展最深部已到达了管壁约47%厚度处。对多根管段进行测试,结果表明裂纹大都沿合金管制造和组装过程中所形成的不同程度表面划伤凹槽部位扩展。对传热管进行爆破测试,该管在最小的爆破压力条件下就发生了破裂。
表面划伤缺陷对传热管服役过程中的SCC抗力有着极大的影响,理清其损伤机制,科学地评估各种条件下表面划伤对SCC抗力的影响,对于核电站的安全运行具有重要意义。
目前,表面划伤致SCC失效案例均出现在600合金传热管上。虽然现役690TT合金的SCC抗力远高于600合金的,但这并不意味着690TT合金未来就不存在SCC开裂风险。
传热缝隙区工况苛刻,一旦该区域出现划伤,其危害程度就会大大加深,故需要通过试验评估。此外,长期服役的传热管材料还面临热老化等因素的影响。研究表明,热老化690合金的SCC敏感性会提升至与高冷变形690合金相似的水平。
综合这些因素,如果出现表面划伤损伤,长期服役的690合金依然面临SCC风险。美国等核电发达国家都积极开展了核电站延寿工作,其中已有部分延寿至60年以上,我国也处于核电延寿工作评估流程、标准建立的重要时期,故研究传热管划伤的影响,具有现实意义。
传热管表面划伤的来源
在生产制造、运输及安装这三个环节,蒸汽发生器传热管都可能会出现表面划伤。
#在传热管的生产制造环节
因设备及人为原因误操作,可能会给传热管表面造成划伤、刻痕缺陷,这其中既可能在传热管外表面(即二回路侧)造成表面划伤,也可能在传热管内表面(即一回路侧)造成划伤。随着制造工艺的改良、加工精度的提高、生产人员操作水平和意识的增强及诸如役前涡流检测等质量检测手段的进步,在传热管生产制造环节出现表面划伤问题的可能性已经越来越低。
#在传热管的运输环节
因管材搬运、长途运输、封装、吊运过程中的疏忽和防范意识缺失,可能会在传热管表面造成划伤缺陷。人们已经认识到保护传热管表面状态的重要性,加强了运输过程中对管材表面的保护,故在传热管运输环节出现表面划伤问题的可能性也越来越低。
#在传热管的安装环节
穿管阶段一旦操作不当,传热管与管板间会产生接触式的线性相对运动,导致传热管外壁出现划伤。为避免管板与传热管之间的微小振动,避免出现传热缝隙,减小传热管与管板间发生微动磨损和缝隙腐蚀的可能,在核电站设计与安装时,穿管后通常要进行液压胀接。液压胀接阶段,一方面,芯轴要经过多次使用,其配件常出现磨损和起毛边、碎屑的现象;另一方面,液压胀管前诸如封口焊等工序也会在传热管内部形成金属屑,带有这类问题的芯轴插入传热管胀接区时,与传热管内表面间产生摩擦,会对内表面造成划伤。
传热管表面划伤导致的应力腐蚀研究
研究人员针对蒸汽发生器传热管表面划伤导致的应力腐蚀进行了各种试验分析与研究,得到以下结论:
表面划伤会使材料表面和距表面不同距离区域产生不同程度的变形,将会对传热管近表面造成微观结构梯度改变,通常会促进高温高压水中传热管表面的SCC裂纹萌生和扩展。
划伤凹槽底部不仅在剧烈变形层与未变形基体之间存在应变变化,而且变形层内部本身也存在应变的梯度分布。研究表明冷变形会显著提高镍基合金在高温水中的SCC敏感性。冷变形区域会发生硬化和应力集中,同时伴随产生大量的空位和位错等晶体缺陷,从而削弱了高应变区的抗SCC性能,在拉应力作用下更易出现SCC裂纹。此外,冷变形也会提高SCC裂纹尖端的氧化速率。出现在晶界和变形区的SCC裂纹尖端阴离子扩散加快,优先发生氧化,加速腐蚀发生和SCC裂纹的扩展。
材料内部的残余应力会影响SCC行为,尤其是处于近表面或微裂纹尖端附近的残余应力。划伤变形区的残余应力分布不均,差异明显。
材料微观结构梯度变化将对传热管SCC抗力产生影响。划伤过程中产生的滑移带、机械撕裂微裂纹、高度变形的晶界、高能亚稳态晶体区域等都有利于SCC裂纹的萌生和扩展。
此外,因划伤带来的几何形貌改变,表面划伤凹槽底部在SCC测试中易产生应力集中,从而促进SCC裂纹萌生。当应力集中到一定程度时,局部应力逐渐超过材料的抗拉强度,就会形成机械裂纹。在外界载荷不断增加的条件下,这类机械裂纹不断张开,始终无法达到稳定钝化状态,处于活化状态的裂纹尖端与高温高压腐蚀介质持续作用。恒载时,机械裂纹不再扩展,若该机械裂纹末端终止于晶粒内部,裂纹便不再保持活化状态,继续增大外加应力,裂纹就会趋于穿晶扩展;若该裂纹终止于晶界附近,即使在恒载作用下,裂纹也会发生沿晶扩展。
传热管表面划伤的修复措施
在工程上,对于传热管表面划伤位置,常用的处理方法是对划伤凹槽部位进行均匀打磨,其处理原则为将划伤凹槽附近的表面毛刺去除。对于较深的划伤凹槽,由于不能对传热管进行过度减薄,因而只将凸起部位的毛刺去除,以降低表面局部异质度。但经处理后的传热管表面划伤位置依然存在着划伤凹槽,服役时划伤区下方仍保持着局部变形。表面的打磨再处理会对划伤凹槽附近的周围局部组织产生显著影响,进而影响其腐蚀抗力,因此需要进一步通过试验研究对其进行科学评估。
结束语
综上所述,表面划伤问题是影响以核电站蒸汽发生器传热管为代表的金属结构件服役寿命的一个重要因素。基于已有的研究,仍存在一些亟待解决的问题和潜在的研究方向:
1根据表面划伤变形模型将材料在划伤过程中的变形行为大致分为弹塑性变形、材料断裂和碎屑分离这三个变形阶段,取得了一系列的试验验证结果。然而划伤是一个多种变形形式复合的过程,影响因素多而复杂。现阶段对于表面划伤变形模型、损伤机理的研究,一方面多采用有限元模拟方法而缺少试验验证;另一方面缺少金属的晶粒与压头间接触的相互作用模拟及后续试验验证。
2对于不同几何参数、不同划伤速率及不同载荷作用下的划伤,尚缺乏对划伤影响区进行较为系统的微观结构分析表征,定量描述划伤损伤程度的方式也较为简化。在今后的研究中,需要对不同变形参数下划伤影响区产生的微观结构梯度变化、局部力学性能变化、残余应力/应变分布等的影响进行研究。
此外,应从三方面优化划伤损伤程度定量方式:第一,引入诸如划伤凹槽深宽比、两侧塑性剥离堆积截面积等参量对划伤凹槽的几何参数进行描述;第二,研究中应注重对划伤速率进行定量描述;第三,从诸如梯度材料的分层、残余应变的分布、硬度的分布等微观结构组织角度进行描述。增强对金属表面划伤的变形行为和损伤特点的认识。
3SCC由材料、应力、环境三方面因素共同决定。表面划伤带来的微观结构梯度、微区应力集中损伤、材料局部缺陷极大地影响了带有表面划伤的金属材料的SCC抗力,但其具体作用机制尚不清晰。在材料方面,划伤引发材料近表面产生宏观撕裂微裂纹和变形影响区,内部具有大量亚稳态微观晶体缺陷、晶界扭曲;应力方面,划伤造成严重的微区应力集中;环境方面,水化学(如溶解氧、溶解氢、pH、杂质离子等)、温度、压强等条件都会影响腐蚀过程。由此,针对以上影响因素分别开展腐蚀测试试验,严格控制变量,以此衡量不同影响因素对SCC的贡献,建立多因素耦合的数值评估模型,阐明带有表面划伤的金属材料的SCC机制,具有重要的科学意义。
4表面划伤问题影响着蒸汽发生器传热管服役性能和核电站安全运行,划伤诱发的传热管SCC失效,已引起核电行业的重视,但相关研究仍不成熟。工程现场的划伤因其来源和尺寸纷繁复杂,例如,对于不同管子支撑板孔,尤其是梅花管孔在其不同尺寸公差下所形成的表面划伤及其他各类人为因素导致的穿管表面划伤,胀管表面划伤等情形缺乏系统调研。对传热管各类表面划伤程度展开系统调研,建立不同类型、不同尺寸公差的传热管支撑结构的表面划伤模型,具有重要的工程意义。
5目前,690合金传热管表面划伤的安全阈值在国际范围内没有统一的结论。究竟什么尺寸的表面划伤是工程应用中可以接受的?这需要对不同尺寸的划伤进行高温高压水环境腐蚀试验。另一方面,针对传热管表面不同尺寸的划伤缺陷,提出适当的修复手段和方法,并对修复工艺进行有效评估,从而为蒸汽发生器的制造提供指导意见,同样具有重要的工程意义。
免责声明:本网站所转载的文字、图片与视频资料版权归原创作者所有,如果涉及侵权,请第一时间联系本网删除。
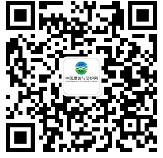
官方微信
《中国腐蚀与防护网电子期刊》征订启事
- 投稿联系:编辑部
- 电话:010-62316606-806
- 邮箱:fsfhzy666@163.com
- 中国腐蚀与防护网官方QQ群:140808414