点蚀是一种阳极区高度集中、隐藏性强、破坏性大的局部腐蚀现象。高氮不锈钢 (HNSS) 具有良好的力学性能和优异的耐腐蚀能力,特别是耐局部腐蚀性能更为突出,越来越受到广大腐蚀研究者的关注[1,2,3,4]。与目前通用的316L等不锈钢 (316L SS) 相比,N作为合金元素加入到不锈钢中,通过降低溶液pH值、抑制Cr和Mo溶解以及促进再钝化等作用,提高了不锈钢的耐点蚀能力[5,6]。乔岩欣等[7]研究了静态和冲蚀条件下,HNSS在NaCl溶液中的耐蚀性都要高于321SS。Chao等[8]研究表明,N是耐点蚀性能的关键元素,在有Mo和Cr存在时,耐点蚀性能进一步提升。
电化学噪声 (EN) 是利用腐蚀过程中电极表面存在的电位或电流随机波动的现象,经过数据计算处理获得腐蚀机理和腐蚀速率等相关信息的一种新兴的电化学研究方法,因其具有原位无损、测量快速等优点,受到越来越多研究者的关注[9,10],尤其是在局部腐蚀领域EN的应用引起了广大腐蚀研究者的兴趣[11,12]。例如,陈崇木等[13]通过EN技术研究了AZ91D镁合金在碱性含氯溶液中的腐蚀过程,李季等[14]利用EN技术研究了304不锈钢在0.5 mol/L FeCl3溶液中点蚀的发展过程和腐蚀机理,Toppo等[15]使用该技术研究了N对两种奥氏体不锈钢在NaCl溶液中的应力腐蚀裂纹萌生和扩展过程的具体影响。
目前,使用EN技术研究HNSS点蚀行为的文献还相对较少。本文以此为出发点,通过对比实验,分析了HNSS和316L SS在6% (质量分数) FeCl3溶液中点蚀行为的EN特征。
1 实验方法
实验材料采用自制HNSS和316L SS,HNSS的化学成分 (质量分数,%) 为:C 0.027,Si 0.120,Mn 0.080,S 0.003,P<0.003,Ni 0.004,Cr 22.80,Mo 1.080,N 1.0,Fe 余量;316L SS的化学成分 (质量分数,%) 为:C 0.023,Si 0.635,Mn 1.110,S 0.003,P 0.025,Ni 10.70,Cr 16.50,Mo 2.05,Fe余量。将两种材料各自加工成10 mm×10 mm×4 mm的试样,背面点焊引出Cu导线,并用环氧树脂将试样封装在PVC管中,只露出一个1 cm2的工作面。用240#~1500#水磨砂纸将试样打磨、抛光,分别用去离子水、无水乙醇、丙酮清洗,干燥后保存。
为了加速点腐蚀的研究过程,实验选用6%FeCl3溶液为腐蚀介质,采用分析纯化学试剂和去离子水配制。实验温度控制在 (35±1) ℃,采用电热恒温水浴锅进行控温。
EN测量使用CS350H电化学工作站。采用三电极体系,工作电极和对电极为两个材质相同的试样,参比电极为饱和甘汞电极 (SCE)。为避免外界信号干扰,将电极体系置于金属屏蔽器中进行测试。本文对HNSS与316L SS进行持续监控,当试样浸入到腐蚀介质后,立即进行电化学噪声测试,测试时间为7 d,采点频率为4 Hz (0.25 s)。
2 结果与讨论
2.1 时域分析
图1为HNSS与316L SS试样在刚刚浸泡到6%FeCl3溶液中的电化学噪声曲线。可以看出,整个过程中曲线只表现出电位与电流的大幅度漂移,并没有出现噪声暂态峰,这是因为Cl-在两种不锈钢表面的钝化膜上发生吸附,导致电极电位下降和电流上升。但也可以看出,316L SS的曲线 (图1b) 出现了两处电位与电流的突变,表明此时316L SS表面的钝化膜已经开始发生破裂和再钝化,而HNSS的曲线 (图1a) 则比较平滑,没有发生大范围的波动,表明HNSS表面钝化膜表现出良好的稳定性和耐蚀性。
图1 HNSS与316L SS在刚浸入到6%FeCl3溶液中时的电化学噪声曲线
图2为HNSS和316L SS在6%FeCl3溶液中浸泡5 h的电化学噪声曲线。其中,图2a为没有进行直流分量剔除的曲线;图2b为经过剔除直流分量处理后的曲线,处理时采用5次多项式拟合方法对噪声原始数据中的直流分量进行剔除,得到近似以零为基准的Gaussian分布图像[9]。从图2b可以看出,随着浸泡时间的延长,Cl-对316L SS表面钝化膜持续侵蚀,电位噪声信号和电流噪声信号均出现了噪声暂态峰,电位噪声暂态峰呈现出快速下降缓慢回升的特点,而电流暂态峰则表现为快速上升而后快速下降的特点。该现象表明试样表面发生了蚀孔形成与再钝化过程,亚稳态点蚀已经出现[16,17]。而浸泡5 h的HNSS并没有出现明显的噪声暂态峰 (图2a),电位噪声信号和电流噪声信号虽发生小幅高频波动,但仍表现出大幅值的漂移,表明HNSS表面钝化膜虽发生轻微腐蚀,但仍具有一定的再钝化能力,对基体的保护作用仍然较好,没有发生明显破裂。
图2 HNSS与316L SS在6%FeCl3溶液中浸泡5 h后的电化学噪声曲线
图3是HNSS和316L SS在6%FeCl3溶液中浸泡48 h时的电化学噪声曲线。该曲线为已经过剔除直流分量处理后的曲线。从图3b可以看出,此时的316L SS噪声暂态峰依旧存在,但由于噪声峰数量增加,寿命明显延长,而且波动幅值的变化使噪声暂态峰不再明显。这种现象是因为Cl-的持续侵蚀已经使钝化膜的局部完全破裂,亚稳态点蚀进入稳态点蚀阶段,导致电极电位与电流发生了很大变化。而此时HNSS的电流噪声信号也出现了明显的噪声暂态峰 (图3a),电位噪声信号波动幅值也呈增大趋势,表明HNSS钝化膜出现了局部破裂,蚀孔开始发展。
图3 HNSS与316L SS在6%FeCl3溶液中浸泡48 h后的电化学噪声曲线
2.2 噪声电阻分析
通常认为,噪声电阻 (Rn) 等同于极化电阻 (Rp),Rn越大,表示发生电化学反应的平均阻力越大,电极表面以均匀腐蚀或钝化反应为主;相反,Rn越小,表示发生电化学反应的平均阻力越小,电极表面则以局部腐蚀为主,多为点蚀。噪声电阻的倒数 (1/Rn) 正比于瞬时腐蚀速率,所以,1/Rn的图像可以看做是腐蚀速率随时间变化的趋势曲线。采用下式对剔除直流分量的噪声数据进行计算,得到Rn,即,
式中,Rn为噪声电阻,σv为电压的标准差,σI为电流的标准差,n和N为个数,Vn为第n个数的电压,In为第n个数的电流, V?V? 和 I?I? 分别为电压和电流的平均值。
图4为HNSS和316L SS在整个实验过程中的噪声电阻图像。可以看出,两种不锈钢的噪声电阻变化趋势均表现为上升趋势。316L SS从浸泡开始,幅值就表现出较大的波动,表明腐蚀程度剧烈;而且腐蚀到第6 d,幅值出现更大范围的波动,腐蚀速率急剧增大,表明此时试样表面已遭到严重腐蚀。而在整个实验过程中,HNSS的幅值在小范围内波动并缓慢上升,表明钝化膜的抗腐蚀性良好,HNSS表面钝化膜的自钝化和修复能力较强。
图4 HNSS与316L SS在6%FeCl3溶液中腐蚀不同时间的噪声电阻倒数曲线
2.3 功率谱密度分析
频域谱代表了电位与电流在不同频率分量时的大小,包含着更为直观和丰富的信息。时-频谱转换的方法有快速Fourier变换 (FFT)、最大熵值法 (MEM) 和小波分析 (WT) 等[9]。本文采用FFT对剔除直流漂移的噪声数据进行分析。
图5是HNSS和316L SS噪声信号通过时-频转换得到的功率谱密度 (PSD)。PSD谱主要有高频段斜率 (K)、白噪声水平 (W)、转折频率 (fc)、截止频率 (fz) 等4个主要特征参数,根据这些特征参数可以表征出噪声特征,得到腐蚀过程机理。从中可以看出,各个曲线的fc和fz几乎是相同的。对曲线进行平滑拟合,得到白噪声水平和高频段斜率数据,结果见表1。研究表明[18],当K≥-20 dB/dec时,试样表面处于局部腐蚀状态;当K<-20 dB/dec时,试样表面则处于均匀腐蚀或钝化状态。从表1中数据可知,HNSS和316LSS的K均大于-20 dB/dec,表明两种不锈钢试样均已发生了点蚀。
图5 HNSS与316L SS的功率谱密度
W可以用来衡量腐蚀速率的大小,W越高,腐蚀速率越大。从表1可以看出,随着浸泡时间延长,同种试样的W呈上升趋势,腐蚀速率随之增大。在不同腐蚀时间段,316L SS的W高于HNSS的,表明316L SS的腐蚀速率大于HNSS的。
2.4 散粒噪声分析
散粒噪声理论属于随机分析的范畴,Sanchez-Amaya等[19]最早将此理论应用到腐蚀研究中,认为电化学噪声信号是由一系列不连续的随机电荷包构成的,且电荷包数量以及每个电荷包所带的电量也都是随机的,所以可以用散粒噪声理论来研究腐蚀过程中电荷包或电量的迁移程度,以此来表征电极表面的腐蚀情况。散粒噪声分析方法有两个重要的特征参数,即:腐蚀事件发生的频率 (fn) 和每个腐蚀事件的电量迁移 (q)[9],用下式分别计算:
式中,B是Stern-Geary常数,ψE和ψI分别是电位和电流功率谱密度白噪声水平对应的值。
fn越大,表明试样表面发生的腐蚀事件越多,越趋于均匀腐蚀;反之,则趋于局部腐蚀[20]。对fn进行累计概率分布计算,可以更好地比较不同腐蚀体系的噪声数据。图6是HNSS和316L SS在整个实验过程中腐蚀事件频率的累积概率分布图像。可以看出,HNSS的fn更趋向于高频段,316L SS的fn更趋向于低频段,表明316L SS发生点蚀的概率较HNSS要大一些。
图6 HNSS与316L SS的fn累积概率分布曲线
2.5 点蚀孕育速率分析
Weibull分布是可靠性分析和寿命检验的基础理论[20],在电化学噪声分析中得到了应用[21]。通过散粒噪声分析可计算出腐蚀事件发生的概率,然后通过下式对其进行Weibull分布变换:
式中,F(fn) 是腐蚀事件发生频率的累积概率,m和k分别是Weibull分布函数的形状参数和尺度函数,t是时间。
散粒噪声信号经Weibull分布变换后,每段曲线段都代表着一个腐蚀失效机制。图7为HNSS和316L SS腐蚀过程的Weibull分布图。线段的高频段表示均匀腐蚀过程,低频段表示局部腐蚀过程。可以看出,HNSS和316L SS的Weibull分布曲线在高频区和低频区的数据点都较为密集,表明腐蚀过程为均匀腐蚀与局部腐蚀的混合状态,且低频区的数据点分布密集,表明两种不锈钢均已发生了以点腐蚀为主的局部腐蚀。
图7 HNSS与316L SS散粒噪声的Weibull分布图
Weibull分布函数理论中,可靠性分析的失效速度r (t ) 表示的是在下一个单位时间内事件发生的概率,这与点蚀孕育速度的概念相一致[22]。如果把腐蚀事件发生的速度r (t ) 理解为可靠性分析中的失效速度,就可以应用Weibull分布函数对其进行分析,r (t ) 定义为:
对Weibull分布函数图像进行线性拟合,求得m和k,拟合结果列于表2。根据式 (5) 计算出点蚀孕育速率与时间的关系曲线,如图8所示。可以看出,316L SS的点蚀孕育速率约是HNSS的2倍,HNSS的点蚀孕育速率更低,其抗点蚀能力也更强。
图8 HNSS与316L SS的点蚀孕育速率曲线
研究表明,316L SS表面钝化膜主要以Cr,Mo,Ni和Fe不同价态的氧化物组成[23,24],但由于Fe含量较多,致使钝化膜存在薄弱区域,容易发生破裂。同时,由于Fe受Cr氧化物极化作用的影响而难以形成氧化物,钝化膜的自修复效果受到不利影响[25]。
HNSS表面钝化膜的主要成分是Fe,O,Cr,Mo和N形成的化合物,钝化膜呈双层结构,表层主要是合金元素反应生成的氢氧化物和沉积盐,内层主要是合金元素的氧化物构成的隔离层,含有极少水化物,这种结构的钝化膜提高了HNSS的耐蚀性[26,27]。此外,HNSS中的N在钝化膜中主要有5种存在形式[4],即:NH3,NH+4,NO-3,Cr2N和氮化物M-N。在钝化过程中,Cr2N首先向钝化膜表面富集,降低钝化膜膜电位,阻止Cl-等侵蚀性离子的侵入,并降低钝化膜破损后基体的溶解速率,提高了材料的耐点蚀性能。随着腐蚀过程的发展,N向钝化膜表层富集,富集在钝化膜表层的Cr2N会发生化学反应生成NH3、NH+4、NO-3等,这些物质可以起到抑制腐蚀的作用,提高了钝化膜对基体的保护性。
3 结论
(1) 316L SS在6%FeCl3溶液中浸泡5 h后,电位噪声和电流噪声出现了噪声暂态峰信号,试样表面发生亚稳态点蚀;当腐蚀48 h时,时域谱波动幅值较大,腐蚀由亚稳态发展到稳态点蚀。而浸泡5 h后的HNSS并没有出现明显的噪声暂态峰,电位噪声信号和电流噪声信号发生小幅高频波动,表面钝化膜虽发生了轻微腐蚀,但仍具有一定的再钝化能力,没有发生明显的破裂;当腐蚀48 h时,电流噪声信号出现了明显的噪声暂态峰,钝化膜也出现了局部破裂。
(2) 随着腐蚀时间的延长,HNSS和316L SS的噪声电阻均表现为上升趋势,但316L SS从浸泡开始,幅值就表现出较大的波动,腐蚀剧烈,而HNSS的幅值在小范围内波动,HNSS表面钝化膜的自钝化能力和修复能力均优于316L SS。
(3) 在相同时间内,316L SS的高频段斜率和白噪声水平强度均高于HNSS的,316L SS具有更高的腐蚀速率,且316L SS的腐蚀事件频率也处于更低的频段,点蚀孕育速率约是HNSS的2倍,316L SS更容易发生点蚀,而HNSS的抗点蚀能力更强。
免责声明:本网站所转载的文字、图片与视频资料版权归原创作者所有,如果涉及侵权,请第一时间联系本网删除。
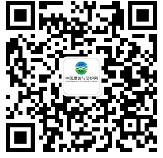
官方微信
《中国腐蚀与防护网电子期刊》征订启事
- 投稿联系:编辑部
- 电话:010-62316606-806
- 邮箱:fsfhzy666@163.com
- 中国腐蚀与防护网官方QQ群:140808414