摘 要:冷喷涂由于具有粉末加热温度低、涂层中氧含量及孔隙率较常规热喷涂涂层显著降低等特点,而广泛应用于制备各种类型的涂层或块体材料。近年来,冷喷涂设备及工艺的改善使其在增材制造和零件修复方面也具有极大的应用前景。综述了冷喷涂制备高性能软质相金属和硬质相金属/非金属涂层的研究进展,重点围绕原始颗粒结构、冷喷涂工艺参数、添加第二相和后处理手段对涂层制备及性能优化的效果进行总结,并对冷喷涂制备复合涂层的结合机理进行了阐述,包括软质相颗粒形成单一涂层和添加硬质相颗粒复合涂层的结合机理,且涂层中颗粒之间的结合主要为机械结合、物理结合、冶金结合和化学结合中的一种或多种结合形式。同时,介绍了冷喷涂技术在增材制造领域和零件修复方面的研究进展和存在的问题。最后,分析总结了冷喷涂的应用前景和存在的问题。
关键词:冷喷涂;增材制造;涂层结合机理;复合涂层;零件修复;后处理
冷喷涂技术是一种固相沉积技术,主要依赖于喷涂过程中的动能使粒子产生变形来实现沉积,因此也被称为动能喷涂(Kinetic Spraying)。图1为冷喷涂装置示意图[1],通过具有一定压力的气体(氦气、氮气或空气等)将粉末粒子(一般粒径为5~50 μm)直接或经过加热进入拉瓦尔型的喷嘴中,使喷涂粒子达到超音速并产生强烈塑性变形,进而沉积在基体上[2-3]。粉末粒子沉积在靶材的现象是一次偶然的发现,在20世纪80年代中期,科学家们在观察超音速风洞负载的颗粒对宇宙飞船表面的侵蚀情况时,发现颗粒在超过一个特定的速度时就可以沉积在靶材上。基于这个现象,Alkhimov等科学家提出了冷喷涂的概念并发表了第一篇论文[4],而后相继地出现冷喷涂的专利[5-6]和研究成果[7-8],从此冷喷涂成为研究的热点问题。图2为2009—2018年有关冷喷涂的发表文章统计,其数量呈直线上升趋势。相关文章主要集中于冷喷涂参数优化、数值模拟、冷喷涂设备研发等方面,这些研究为冷喷涂的规模化、稳定化应用夯实基础。最近几年,冷喷涂作为一种新型的增材制造手段得到了科研人员的青睐[9]。冷喷涂不但可应用于防护涂层和功能涂层的制备,以及零件修复,亦可做为一种块体材料制备的手段应用于近净成形等领域。
图1 冷喷涂装置示意图[1]
图2 2009—2018年发表冷喷涂文章统计(数据来源于Web of Science核心合集)
1 冷喷涂涂层的特点及研究进展
冷喷涂具有以下显著特点[1]:(1)加热温度低,涂层不易氧化,其化学成分可与原料保持一致,有利于非晶、纳米晶及复合涂层的制备;(2)喷涂过程中基体受到的热影响极小,可使用形状复杂或较薄的基体;(3)涂层中存在的残余应力较低,主要为压应力;(4)喷涂速度高,孔隙率低,易获得较厚涂层。但是由于冷喷涂主要基于粉末颗粒在动能作用下的塑性变形进行沉积,对喷涂材料的种类有一定限制,下面将对不同种类冷喷涂涂层研究情况进行总结。
1.1 软质金属的冷喷涂
冷喷涂制备涂层一开始主要针对于易于塑性变形的软质金属,包括Cu、Al、Ni、Zn、Ag等。其典型冷喷涂涂层的照片如图3所示,可见涂层结合紧密,孔隙率低,可制备较厚的涂层。例如,C.Borchers等人[10]采用冷喷涂技术制备得到致密、无氧化物的铜涂层,其电阻率为 1.7 μΩ·cm,结合强度为 30~40 MPa,维氏硬度为 140~160HV0.3。L.Ajdelsztajn 等人[11]采用冷喷涂的方法制备了孔隙率极小、界面结合良好的纳米晶结构 Al5083涂层,其显微硬度达到(261±8)HV(300 g),显著高于铸造等手段获得的材料。N.M.Chavan等人[12]制备得到的 Ag冷喷涂涂层的电导率可达块体材料的70%。
图3 冷喷涂软质金属涂层
1.2 第二相粒子的添加对涂层喷涂效率和性能的影响
金属在冷喷涂过程中往往会造成大量粉体的浪费,粉末的喷涂沉积效率对于涂层的成本控制非常重要。实验结果显示,在喷涂过程中适量添加硬质相颗粒可以使软质相颗粒的沉积效率提高 20%~30%,同时可减少涂层的孔隙率、增加基体与涂层间的结合力[13]。Eric Irissou等人[14]的研究表明,当涂层中Al2O3的质量分数从0%增加到30%时,Al的沉积效率提高了4倍多,同时还提高了涂层的抗盐雾腐蚀能力。这是由于Al2O3的加入在基体上形成了大量弹坑,有利于 Al的射入沉积,同时也增加了基体与涂层间的接触面积,提高涂层与基体之间的结合力,并增加涂层的致密性。HeliKoivuluoto等人[15]研究了添加 Al2O3对铜涂层组织和力学性能的影响,也讨论了原始铜颗粒形态对涂层致密性的影响。结果显示,球形铜颗粒相比树枝状铜颗粒能更有效地减少涂层的孔隙率。硬质相Al2O3产生的锤击效应可使涂层更加致密,并提高涂层与基体的结合力,涂层的形貌照片如图4所示。同样地,在 Ni[16]、FeAl[17]、Al[18]等涂层中也可通过添加硬质第二相,显著提高粉末的沉积效率和涂层性能。而当硬质相的含量占据绝大部分时,软质金属颗粒会作为粘结相,使得难于变形的金属实现冷喷涂制备。
图4 添加第二相粒子的涂层[15]
1.3 难变形金属/陶瓷的冷喷涂
由于难变形的金属/陶瓷粉末,如 SiC、Al2O3、W、WC等,在冷喷涂过程中粒子的变形能力非常弱,粒子与粒子之间、粒子与基体之间不易产生有效结合而形成涂层。这一问题虽然可通过提高喷涂压力(3~4.4 MPa)和采用氦气作为载气得到一定程度的解决,但效果有限,且大幅度增加了涂层的制备成本[19]。研究表明,将一些软质相金属作为粘结相,可以实现难变形金属的冷喷涂。Ha Yong Lee等人[20]在喷涂压力为0.7 MPa下,将Al作为粘结相分别制备了SiC和Al2O3涂层。Hyun-Ki Kang等人[21]采用冷喷涂技术制备了 W-Cu复合材料,结果表明,由于 W的变形不充分,喷涂过程中钨粉存在较大(W质量分数约为40%)的损失,涂层的孔隙主要存在于W的富集区。N.M.Melendez等[22-23]在喷涂压力为0.6 MPa下制备得到 WC-Ni复合涂层,涂层扫描电镜照片如图5a所示,该复合涂层具有高硬度和低磨损率,但是涂层中普遍存在 WC的损失。笔者[24]在喷涂压力为2 MPa下研究了不同W含量对W-Cu喷涂后组织及性能的影响,涂层照片及相关性能如图5b—d所示。结果显示,随着 W 含量的增加,复合涂层的孔隙率减少,抗磨损性能提高,W 的沉积效率在30W70Cu体系中可达 72%。以上研究表明,由于硬质相颗粒变形程度弱,在喷涂过程中都会存在硬质相颗粒的损失。
图5 冷喷涂硬质相涂层
Gao等人[25]为了提高硬质相颗粒的变形能力,采用多孔结构的WC-Co粉体作为原始材料制备涂层。结果显示,采用易于变形的多孔结构原始粉体,可以更容易将WC-Co沉积在基体上,沉积效率很大程度上取决于原始粉体的孔隙率。有研究人员也提出采用核壳式粉体作为原始喷涂粉体,从而避免硬质相的损失。Li等人[26]对采用水热氢还原法制备的 Ni包覆Al2O3粉体进行冷喷涂,喷涂后涂层中 Al2O3的体积分数为(29±6)%,仍然少于原始粉体中 Al2O3的含量(40%~45%),这主要是因为在喷涂过程中,微粒在冲击到基体时发生反弹。Shuo Yin等人[27]采用Cu包覆的金刚石作为原始粉体进行冷喷涂,实验结果表明,采用包覆粉体制备得到涂层中金刚石的质量分数达到43%,硬质相高于以往报道采用混合粉体作为原材料的量,其中采用金属镍作为过渡层,可增加金刚石和Cu之间的界面结合力。Ni包覆B4C[28]、Ni包覆金刚石[29]、Ni包覆石墨[30]、Ni包覆 FeSiAl[31]等作为喷涂粉末进行冷喷涂,均可提高硬质相颗粒的含量,进而提高涂层性能。
1.4 易氧化材料的喷涂制备
冷喷涂由于低的喷涂温度,为一些易氧化材料涂层的制备提供了可能。Shuo Yin等人[27]利用冷喷涂制备了Cu-Diamond复合涂层,低的喷涂温度有效避免了金刚石的石墨化。采用冷喷涂技术得到的 Cu-Graphene复合涂层呈现优异的抗摩擦磨损性能[32]。Kwon等人[33]采用冷喷涂技术制备 Cu-碳纳米管(CNT)复合涂层,当CNT的质量分数为0.5%时,该涂层具有较高的热导率。Cho等人[34]也证实了CNT的添加可以提高复合涂层的热导率。
1.5 冷喷涂涂层的后处理
低孔隙率、致密的结构意味着冷喷涂涂层具有良好的力学性能、热电性能。然而,颗粒在沉积过程中经历剧烈的冲击变形又会产生残余应力导致加工硬化,对力学性能、热性能和电性能等产生不利影响。因此,一般都需要对涂层进行适当的热处理,以消除涂层中的残余应力和加工硬化,提高涂层的相关性能。以下对涂层进行热处理的方式进行举例说明。Huang等人[35]研究了热处理对Al、Cu涂层力学性能的影响,结果显示,经过600 ℃热处理后,Al涂层的延伸率为25%(相当于块体材料的一半),抗拉强度为 70 MPa(接近于块体材料);经过 400 ℃和500 ℃处理后,Cu涂层的抗拉强度和延伸率都优于块体材料,如图6a、b为退火前后Cu涂层的金相照片。热处理的温度和气氛都是影响热处理后涂层性能的关键因素[11]。需要指出的是,热处理对于冷喷涂涂层性能的改善效果有限,如Ti及316不锈钢涂层[35]。对于这类涂层,有学者提出可采用搅拌摩擦焊技术进行后处理,能有效消除涂层中的孔隙和微裂纹,细化组织,并增强组织均匀性。F.Khodabakhshia等人[36]采用冷喷涂将Ti沉积在Al基板上,研究表明,该涂层经过搅拌摩擦焊后,Ti和Al之间形成了Al3Ti中间化合物,使得界面结合力由机械结合转变为冶金结合,显著提高界面结合力。Huang等人[37]对冷喷涂Ni-Ti涂层进行搅拌摩擦焊处理,发现在后处理过程中原位生成了无明显缺陷的 Ni-Ti金属间化合物层(如图6c、d所示),相比于未后处理的涂层,其硬度和抗磨损性能分别提高了4.5倍和2倍。由此可见,对于冷喷涂涂层来说,进行热处理是常规的后处理手段,而热处理的效果是有限的,因此也会进行其他的后处理手段,如搅拌摩擦焊等。
图6 原始涂层及后处理涂层
1.6 零件修复
由于冷喷涂过程中所需温度低,基体的温升小,产生较小的热应力,非常适用于零件修复。如图7所示[38],图中都是采用冷喷涂技术对部分损坏的零件进行修复。图7a是减速器外壳在服役过程中与配合面接触受到严重腐蚀导致不能继续使用,采用冷喷涂技术对外壳和密封面进行修复,保证了涂层的耐蚀性和耐磨性,并节省了再加工周期和成本。图7b为飞机轮子在服役过程中对轮总成内、外两部分的配合面造成的腐蚀和磨损损伤,经过冷喷涂修复后就可以不用替换新的轮子,使可能报废的轮子重新达到使用要求,实现零件重新利用。图7c为T700发动机前壳在工作过程中受到腐蚀和磨损,需要将该部件拆卸并安装新的部件,而采用冷喷涂修复技术对油底壳腐蚀密封面进行修复,从而实现对部件的回收利用。
图7 冷喷涂用于零件修复[38]
2 冷喷涂涂层的结合机制
冷喷涂涂层的结合机制与传统的热喷涂涂层有很大不同。图8为单一颗粒形成涂层过程的示意图[39],可分为四个阶段[40-43]:(1)喷涂粒子在基体上形成弹坑,建立第一层颗粒层;(2)喷涂颗粒间产生变形和重排;(3)喷涂颗粒间形成结合,孔隙减少;(4)原始颗粒间的结合被破坏,引起加工硬化,产生大的体积变形。图9是含硬质相颗粒的复合涂层的形成示意图[24]。在喷涂过程中软质金属呈喷射状,硬质颗粒围绕在软质金属周边并在基体上形成弹坑,建立起涂层的第一层。若喷涂粒子中硬质相含量较高,喷涂过程中硬质相颗粒相互碰撞的机率就会增加,造成部分硬质相的损失,并限制涂层的厚度;而当硬质相含量较低时,硬质相的损失会明显减少,软质相作为粘结相增加涂层的厚度。虽然硬质相颗粒不易变形限制涂层的厚度,但硬质相的锤击效应会使涂层与基体之间的结合力增加,同时降低涂层的孔隙率。
图8 涂层形成示意图[39]
图9 涂层结合示意图[24]
在不同材料和工艺条件下,涂层中颗粒之间存在机械结合、物理结合、冶金结合和化学结合中的一种或多种结合方式[44]:
1)机械结合。在喷涂过程中,喷涂粒子发生绝热剪切失稳产生变形,颗粒与颗粒之间发生混合或机械咬合。机械结合是涂层与基体的主要结合方式。
2)物理结合。喷涂过程中,高速运动的颗粒撞击到基体表面,绝热剪切失稳及其局部化产生的射流可以将粒子表面的氧化膜带走,使其产生干净的表面,并在较高压力下形成物理结合。
3)冶金结合。粒子在喷涂过程中发生绝热剪切失稳,并产生大量的热量,温度可瞬时达到材料的熔点,从而使界面达到冶金结合。冶金结合的界面结合强度非常高,其主要发生在低熔点材料的冷喷涂过程中。
4)化学结合。喷涂过程中,高速运动的粒子产生塑性变形,使基体和涂层间发生反应,生成一种中间化合物即发生了化学结合。对冷喷涂涂层进行后处理可获得化学结合。
3 冷喷涂增材制造
增材制造技术是将原始粉体进行逐层沉积,最终得到具有复杂形状成品的方法。冷喷涂具有成形温度低、不易氧化、成形速度快等优点,而成为一种颇有前景的增材制造手段,如钛及其合金被广泛应用于制备航空航天零件、医用植入材料和防护涂层。由于钛的活性高,极易氧化,传统制备手段较难生产优异性能的复合材料,使得冷喷涂成为制备钛及其合金的一种新方法。如图10a为一件沉积在铝板表面的复杂形状Ti6Al4V三维打印零件,其沉积效率高达80%,沉积时间则短至15~30 min[45]。冷喷涂增材制造也应用于能源材料领域,如图10b为通过冷喷涂制备的NiAl含能块体材料[46]。同时,冷喷涂增材制造是制备复杂的近终成形样品手段之一,如图11所示[47]。
图10 冷喷涂制备
图11 冷喷涂制备零件[47]
冷喷涂制备钛及其合金涂层内部普遍存在微孔,同时颗粒之间以机械结合为主,结合力较弱,使得其抗腐蚀性能和力学性能较低[48-49],因此需要优化冷喷涂参数和进行喷涂后处理等手段来提高块体的性能。V.N.V.Munagala等人[50]研究了不同Ti6Al4V粉末形状对涂层附着力的影响。结果表明,采用不规则的原始粉末比球形粉末具有更好的附着力,同时也发现喷涂中粉末的喷涂速度对附着力的影响更大。D.MacDonald等人[51]采用Armstrong process方法制备的Ti粉为原料并进行冷喷涂,该工艺制备的粉体具有低容重的特点,呈现出珊瑚状结构。结果显示,所制备的Ti涂层具有致密的结构,在经过3 h的热处理后,该涂层表现出与块体材料相当的硬度和抗拉强度。Ren等人[52]证实了经过热处理后可以降低涂层的孔隙率。Luo等人[53]在喷涂Ti6Al4V和Ti过程中引入大颗粒的不锈钢颗粒,借助大尺寸颗粒对涂层的锤击效应可增加涂层的致密性。不仅仅是 Ti及其合金,其他种类的材料也可通过冷喷涂增材制造。K.Petra?cˇkova等人[54]采用冷喷涂技术制备A357铝合金,经过退火处理后与铸态A357-T61相比,强度相当,延伸率得到提高(超过了 5%)。Yang等人[55]通过冷喷涂技术制备较厚致密的纯铜块体,经过热处理后,其抗拉强度增加了34.2 %,断口形貌从原始喷涂的脆性断裂转为塑性断裂。Ma等人[56]通过冷喷涂技术制备了低孔隙率且力学性能与块体材料相当的Inconel 718合金,经过热处理后,涂层与基体的结合力达到899.4 MPa,极限抗拉强度为 1272 MPa,延伸率为 9.64%,杨氏模量为2.06 GPa。Chen等人[57-58]采用冷喷涂手段制备马氏体时效钢300,经过固溶-时效处理后,孔隙率为0.168%,屈服强度为599.8 MPa,延伸率为1.64%。同时也证明了加入 WC颗粒可以提高材料的抗磨损性能。
此外,在冷喷涂增材制造过程中还存在一些问题。例如,是否可以通过对喷嘴进行改进,来提高制备精度,减少后续机加工,以实现真正意义上的近净成形;在喷涂过程中沉积效率也需要进一步提升,减少原始粉体的浪费并实现可循环利用;某些材料对喷涂气体的限制也会明显增加成本,如P.Vo等人[48]在制备Ti-6Al-4V块体中发现,只有采用昂贵的氦气作为喷涂气体才能得到较致密的块体。
4 结论与展望
冷喷涂由于其低温快速成形的特点不仅可以制备涂层,用于零件修复,也可以作为一种新型的增材制造手段制备块体材料或复杂零件。可以看到,冷喷涂拥有很多涂层或材料制备的优势,也存在明显的不足之处。如何扩大喷涂粉末的范围、提高喷涂粉末的沉积效率、提高涂层中颗粒之间的结合力等,均是将来要重点解决的问题。这就需要科研人员去深入理解颗粒在高速碰撞过程中颗粒与颗粒之间、颗粒与基体之间的碰撞行为,为得到理想涂层或块体材料做理论指导。同时,也要从改变工艺参数着手,对制备方式进行优化,如原始粉体的结构、冷喷涂参数、后处理手段等。希望通过以上优化手段使得冷喷涂技术在制备高性能涂层和块体方面更加具有吸引性。同时,无损检测技术的不断进步,也将会使增材制造技术在安全可靠性上更加具有保障性。
免责声明:本网站所转载的文字、图片与视频资料版权归原创作者所有,如果涉及侵权,请第一时间联系本网删除。
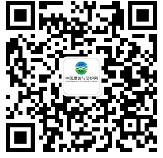
官方微信
《中国腐蚀与防护网电子期刊》征订启事
- 投稿联系:编辑部
- 电话:010-62316606-806
- 邮箱:fsfhzy666@163.com
- 中国腐蚀与防护网官方QQ群:140808414