钛和钛合金的密度低、生物相容性好和耐腐蚀性能优异,在生物医学领域得到了广泛的应用。钛合金能与骨形成骨整合且没有不良反应,是一种良好的牙种植体材料。近年来,Ti6Al4V钛合金已经用于牙科植入、正牙丝和冠桩等方面。在使用过程中,钛合金溶解在唾液或龈沟液内并与腐蚀产物直接接触。在口腔内F-引起的腐蚀是比较常见的,因为在牙膏、凝胶和饮用水中有大量的F-,近来甚至将F-添加到烹饪盐中。许多市场销售的氟化凝胶含有高达10000×10-6(质量分数,%)、pH值介于7.2~3.2的氟离子。钛对卤化物(特别是F化物)、H和O极为敏感,使钛合金表面形成的致密钝化膜溶解或剥落而丧失其保护性能。Mabilleau G等将氟化物和氧化物作用于钛表面,发现氟离子使钛表面的氧化层溶解,使表面粗糙度提高。Kumar等分析了Ti6Al4V、CP-Ti和Ti15Mo三种钛合金在不同氟离子浓度下的腐蚀行为。结果表明,电流密度与电解液中的氟离子有很强的相关性,随着氟离子浓度的提高腐蚀电流密度增大。
基于原材料性能及服役环境考虑,有必要对钛合金进行表面强化处理,提高其表面强度、硬度与耐磨性。因此,评估改性后钛合金在不同电解质、浓度、pH、温度等条件下的使用寿命,已成为当前的研究热点。对20CrMnTi、38CrMoAl等合金表面渗碳,可提高金属表面的硬度、耐磨性及耐蚀性。本文研究在不同真空感应渗碳工艺条件下Ti6Al4V钛合金渗碳层在含氟酸中的?泡腐蚀和电化学腐蚀行为,并结合相结构和组织演变分析其腐蚀机理。
1 实验方法
1.1 Ti6Al4V的表面渗碳
实验用材为退火态Ti6Al4V,样品的直径为15 mm厚度为10 mm。使用真空感应脉冲热处理装置,在不同温度下对Ti6Al4V进行表面渗碳。渗碳工艺如图1所示。将样品放入真空感应脉冲热处理装置中,渗碳温度分别为850℃、880℃和910℃,渗碳压力为-70 kPa,时间为1 h,当试样表面温度到达目标温度后往炉内充入甲烷气体(纯度大于99.99%)-70 kPa并保压10 min进行强渗,然后抽出气体并保温5 min进行扩散,循环保温1 h后随炉冷至室温。
1.2 耐蚀性能测试
将钛合金浸泡在0.2%HF腐蚀溶液中进行加速腐蚀测试,以0.5 h为周期更换腐蚀液并称量质量损失以计算腐蚀速率;在1%HNO3+1%HF混合水溶液中,以饱和氯化钾溶液为电解液的甘汞单盐桥式为参比电极(25℃下的电极电势为0.2415 V),铂电极为辅助电极,使用BioLogic电化学工作站测试极化曲线、阻抗和Mott-Schottky曲线。极化曲线的扫描速度为5 mV/s,扫描范围Ei-El为-1 V~0 V。对极化曲线进行Tafel拟合,计算试样的腐蚀电位和腐蚀电流;阻抗谱的扫描频率为200 kHz~100 mHz。使用ZSimDemo 3.30d软件进行等效电路拟合。Mott-Schottky曲线的扫描频率为1 kHz~100 kHz,最后拟合1 kHz得出平带电位和施主密度或受主密度。
1.3 组织结构与腐蚀形貌表征
使用多晶粉末衍射仪(XRD,D8-Advance)以Cu(0.154174 nm)作为靶材,分析腐蚀前后渗碳层的相结构;为了分析试样截面组织,用5%HNO3+5%HF进行截面金相腐蚀,在金相显微镜下分析腐蚀后试样渗层的组织;用扫描电子显微镜(SEM)及能谱(EDS)分析?泡后渗碳层的腐蚀形貌和腐蚀产物。
2 实验结果
2.1浸泡腐蚀
将相同表面积的未渗碳试样和渗碳试样置于0.2%HF腐蚀液中。试样与腐蚀液接触后产生大量的气泡,发生快速腐蚀反应并在溶液中生成蓝色化合物(三氟化钛)。腐蚀速率(g/(m2·h))为
其中m0为腐蚀前质量(g);m1为腐蚀后质量(g);A为试样的表面积(m2);T为腐蚀时间(h)。使用式(1)计算腐蚀速率,结果列于表1。
从图2可见,未渗碳试样的腐蚀速率呈直线上升趋势,腐蚀速率为4.65×10-10 g·m-2·h-1;渗碳后,随着温度的升高质量损失降低,即腐蚀速率降低,在910℃腐蚀速率降至3.3×10-10 g·m-2·h-1。由于钛合金在HF腐蚀液中难以钝化,整个腐蚀过程为快速全面腐蚀。渗碳后表层形成的不同厚度的TiC和CTi0.42V1.58渗碳层能抵抗HF的侵蚀,且随着温度的升高渗碳层增厚腐蚀速率降低。
2.2 电化学腐蚀
2.2.1 极化曲线
图3给出了不同状态下的极化曲线。可以看出,感应渗碳使极化曲线向左上方移动,表明腐蚀倾向降低。渗碳后均出现明显的钝化过度区,表明渗碳使表面钝化能力增强。未渗碳的Ti6Al4V钛合金在1%HF和1%HNO3水溶液中一直处于活化溶解状态,而没有出现明显的钝化。这表明,在实际服役过程中渗碳表面的钝化膜具有较好的自愈性。
对极化曲线拟合得到的相应参数,列于表格1。从表格1可知,随着温度的升高自腐蚀电位(Ecorr)从未渗碳样的-0.94 V升高到-0.68 V;腐蚀电流(Icorr)从未渗碳样的4.10 mA·cm-2降至1.65 mA·cm-2;极化电阻(Rp)从未渗碳样的6.36 Ω·cm-2升高到15.8 Ω·cm-2。这些结果表明,感应渗碳使表面的抗HF腐蚀性能提高2.5倍。未渗碳样品的Tafel斜率βa/βc小于1,而渗碳试样的βa/βc大于1。这表明,未渗碳样在反应过程中主要受阴极极化过程的控制,快速渗碳改变了Ti6Al4V钛合金在1%HF和1%HNO3溶液中反应受阴极极化过程控制的情况。
2.2.2 阻抗
图4给出了交流阻抗谱。渗碳前后试样的交流阻抗谱形状相似,只有容抗弧的半径不同,表明具有相同的腐蚀机理和不同的耐蚀性能。从图4a可见,在高频区存在感抗弧,表明在腐蚀过程中钛合金表面发生自腐蚀析氢和氢气的吸附反应。渗碳试样高频区的阻抗模值均在不同程度上高于低频区域的阻抗模值,并随着温度的升高阻抗模值增加。这表明,渗碳层使电阻的增大,即腐蚀的阻力增大。在阻抗模值的相同频率范围内出现高频相角峰,表明表面渗碳层能抵抗腐蚀。
在拟合出的等效电路图中,各电路元件并非标准电器元件,而是频率的函数,从而得出等效电路随频率变化的阻抗图谱。在外加频率下腐蚀过程中表面离子远动并非随机的布朗运动,而是呈周期或准周期的震荡。震荡周期不同,界面的元件参数也不同。根据图4d中的等效电路使用电化学阻抗模型式(2)函数
拟合出阻抗值(表2)。式(2)中Z(f)是一个复数;L为氢气析附反应感抗;Rs为溶液电阻;Q(CPE)为双电层电容常相位角元件(Q1表示电极表面吸附的腐蚀产物膜电容,Q2表示电极反应双层电容),n为弥散指数(电极表面具有一定的粗糙度,表面反应存在一定的弥散效应);Rf为腐蚀产物膜电阻;Rt为电荷转移电阻(Ti-Ti+3);X2为相对误差值。从表格2可知,随着渗碳温度的升高电荷转移电阻Rt和腐蚀产物膜电阻Rf均增大,Rt从未渗碳样的0.2 Ω·cm2增大到5.7 Ω·cm2(910℃),Rf从未渗碳样的0.2 Ω·cm2增大至最高23.6 Ω·cm2。这些结果表明,渗碳使腐蚀过程中的电子转移阻力增大,使耐蚀性提高。
2.2.3 Mott-Schottky曲线
极化曲线表明,渗碳的Ti6Al4V钛合金表面比未渗碳样易钝化,而钝化膜具有半导体特性且与耐蚀性能密切相关。通过Mott-Schottky曲线及拟合得出的施主密度或受主密度结果分析表面半导体的空间电荷层电容与本体电势的分布,可判断表面反应进行的可能性。当半导体面与电解液接触时,表面出现空间电荷层且电荷的符号与溶液中的相反。n型半导体与p型半导体的空间电荷层与电容与电位的关系Mott-Schottky为
其中CSC为空间电荷电容(F·cm2);Nd为施主密度(cm-3);Na为施主密度(cm-3);ε为介电常数,钛的取值约为56 F/cm;ε0为真空介质常数,其值为8.85×10-14 F/cm;e为电子电荷,其值为1.602×10-19 C;E为电极电位(V);Efb为平带电位(V);k为玻耳兹曼常数;T为绝对温度。其中n型半导体的直线段斜率为正,p型半导体的直线段斜率为负。
图5给出了钛合金在HF腐蚀溶液中的Mott-Schottky曲线,并对Mott-Schottky曲线拟合得到施主密度或受主密度的值(表3)。测试电压为0 V~1 V,测试频率为1 kHz~100 kHz。该曲线为1 kHz下的Mott-Schottky曲线。从图5可见,未渗碳的Ti6Al4V钛合金有两种不同的半导体特性,在0 V~0.4 V范围内具有n型半导体特性,在0.4 V~1 V范围具有p型半导体特性。快速渗碳后的表面呈n型半导体特性,且随着温度的升高施主密度降低。实验结果表明,未渗碳的试样存在表面氧化膜和基体两种状态,在HF溶液中表面氧化膜呈n型半导体特性,基体呈p型半导体特性,p型半导体的受主密度增大了F-离子在表面的吸附并促进F-对表面的腐蚀。渗碳试样的表面主要呈n型半导体特性。在0 V~0.4 V范围内平带电位较低,因为电位处于低电压时随着电压的升高钝化膜/溶液界面处的电子被消耗,使施主密度提高,平带电位低于0.4 V~1 V范围。n型半导体的施主密度随温度的升高而降低,即温度的升高使钝化膜的稳定性增加,表面的缺陷浓度降低,抗蚀性能增强。
3 分析和讨论
3.1相结构
图6给出了不同条件下渗碳试样的XRD图。图6a给出了Ti6Al4V钛合金和渗碳后未腐蚀试样的XRD图。从图6a可见,对Ti6Al4V钛合金渗碳可在表面制备一层TiC的陶瓷相和CTi0.42V1.58复合化合物相。在感应渗碳过程中,甲烷分解出活性碳原子和钛原子以及合金元素反应生成混合化合物相。由于碳原子半径(小于0.077 nm)比钛的半径(0.147 nm)小,碳容易扩散至钛表面与钛形成化合物。同时,随着渗碳过程的进行一部分活性碳原由表及里进行扩散,形成固溶体。与未渗碳样品相比,在910℃渗碳试样钛的特征峰有明显的下降,而在850℃和880℃渗碳的试样XRD峰与未渗碳样品的XRD峰相似。其原因是,在885℃前渗碳时钛的主要为较密的hcp结构,对碳原子的溶解度小且扩散较慢,少量的碳原子对钛的晶格影响较小;在885℃以上渗碳钛转变为较为疏松的bcc结构,扩散速度提高,反应生成的TiC和CTi0.42V1.58复合化合物相增加。
图6b给出了图6a中对应样品浸泡腐蚀后的XRD图。对HF溶液?泡腐蚀后试样的XRD峰基分析结果表明,腐蚀后残留的相主要为Ti和CTi0.42V1.58,而没有TC。在?泡腐蚀过程中,HF对钛有及强的腐蚀性。随着腐蚀过程的进行,表面碳化物被腐蚀剥落。
3.2 显微组织
图7a、b、c分别给出了850℃、880℃、910℃感应渗碳后的显微组织。表面渗碳使表面形成等轴状α相和片状α相,随着温度的升高等轴α相厚度增大,组织变粗。由于碳元素为α相稳定元素之一,随着渗碳温度的升高表面碳含量增加,促进表面β相向α相转变。渗层组织与基体的过度比较缓和,层间组织的分布没有突变,表明渗层与基体间的结合力较强。致密的组织和有一定厚度的渗层能阻止了腐蚀介质中阴离子的侵入。
3.3 腐蚀形貌
图8a、b给出了未渗碳样品在不同倍数下的表面腐蚀形貌,图8c、d给出了在880℃渗碳试样在不同倍数下的表面腐蚀形貌,图8e给出了图8c中区域(e)范围内的能谱图,图8f给出了图7d中区域(f)范围内的线扫描能谱图。由图8可见,钛合金在HF腐蚀溶液中发生局部溶解,腐蚀表面出现大量的α、β-Ti的凹陷区和白色疏松状(主要含F、C、O、Ti元素)的混合凸出区。钛合金在大多数有机酸(碱)溶液、氧化性介质中形成致密的钝化膜而不易腐蚀,但是在还原性酸溶液(HF)中钛合金的表面强化层容易破坏(或溶解)形成多空的非保护性膜,从而使钛的腐蚀速率提高。从局部区域的元素组成可以观察到存在少量的碳化物和氧化物,表明Ti6Al4V钛合金在HF腐蚀溶液中的主要腐蚀机制为析氢腐蚀。
4 结论
(1)Ti6Al4V钛合金渗碳前后在0.2%HF溶液中均发生很快的全面腐蚀,随着渗碳温度的提高耐蚀性能随之提高。
(2)未渗碳的Ti6Al4V钛合金呈p型半导体特性,渗碳层在1%HF和%HNO3水溶液中呈n型半导体特性,其腐蚀电流密度降低,电子转移阻力增大使耐蚀性能提高。
(3)Ti6Al4V钛合金表面的渗碳层由TiC和CTi0.42V1.58复合化合物相组成,表层组织为大量α-Ti相和少量β-Ti相。渗碳层在HF溶液中腐蚀后生成大量α-Ti和β-Ti的凹陷区和白色疏松状(主要含F、C、O、Ti)的凸出区,其腐蚀机理主要为析氢腐蚀。
免责声明:本网站所转载的文字、图片与视频资料版权归原创作者所有,如果涉及侵权,请第一时间联系本网删除。
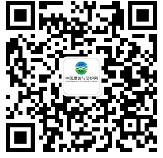
官方微信
《中国腐蚀与防护网电子期刊》征订启事
- 投稿联系:编辑部
- 电话:010-62316606-806
- 邮箱:fsfhzy666@163.com
- 中国腐蚀与防护网官方QQ群:140808414