Ti及钛合金具有密度小、比强度高、耐蚀性好等特点,已广泛地应用于航空航天、汽车、化学工业等领域。但是,钛合金硬度低、耐磨性差,在服役过程中易发生粘着磨损和咬合[1,2,3,4],限制了其应用。对钛合金进行适当的表面处理可有效改善其耐磨性,提高构件的服役寿命[5,6,7]。钛合金表面硬化处理方法[8,9,10]主要可通过电镀硬铬或化学镀镍,采用物理气相沉积 (PVD)、热喷涂、激光熔覆等技术来沉积氮化物、WC-Co等硬质涂层,以及渗氮、渗碳和微弧氧化 (MAO,也称作等离子体电解氧化PEO),等等。经过上述方法处理后,钛合金的耐磨性都有不同程度的提高。
MAO技术是一种借助高电压、高电流和瞬时高温在Al、Mg、Ti等阀金属表面原位生长一层陶瓷氧化膜层的技术[10,11,12,13,14,15],其原位反应涉及复杂的热化学、等离子化学和电化学过程。MAO技术具有工艺简单、溶液环保、膜层结合良好、适于复杂形状工件涂装等诸多优点,自上世纪30年代起得到了广泛的关注和研究,并已得到了应用。
采用MAO技术在钛合金表面生成MAO陶瓷层提高了钛合金的耐磨、耐蚀性能。但是,钛合金MAO层一般较薄,粗糙且疏松多孔,硬度相对较低。研究[16,17,18,19]表明,采用交流电源在铝酸盐-磷酸盐电解液中钛合金表面生长出的TiO2/TiAl2O5陶瓷层较厚且相对致密,耐蚀、耐磨性能较好。然而,该MAO层致密层的厚度也只有约20 μm,硬度在600~880 HV。钛合金MAO陶瓷膜对钛合金耐磨性能的改善程度有限。
Al及铝合金MAO膜的主要成分是α-Al2O3和γ-Al2O3。与钛合金MAO膜层相比,铝合金MAO膜层具有更高的硬度和更好的耐磨性[20,21]。因此,有学者提出可在钛合金表面涂镀一层Al或铝合金作为中间层,之后再进行MAO。Hu等[22]在纯Ti表面热浸镀铝后进行了不同时间的MAO处理,随MAO时间的延长,氧化膜的厚度、硬度、耐磨性都显著增加。欧阳小琴等[21]和卜彤等[23]分别在TC4钛合金表面溅射镀铝和多弧离子镀铝后再进行MAO,结果表明获得的陶瓷膜层的耐磨和耐蚀性能都优于钛合金MAO膜。但是,上述研究中[21,22,23]制备的MAO陶瓷膜都较薄,而且,未给出陶瓷膜/预镀铝层/钛合金基材体系的界面结合强度的相关数据,而MAO陶瓷层的厚度和结合强度是影响涂层的耐磨和耐蚀性的关键因素。
本文以TC4钛合金为研究对象,在其表面多弧离子镀铝后进行了不同时间的MAO处理,研究了MAO处理时间对所制备膜层的微观结构、硬度、耐磨性及结合强度的影响。
1 实验方法
基体材料为TC4钛合金,其化学成分 (质量分数,%) 为:Al 5.5~ 6.8,V 3.5~4.5,Fe≤0.3,O≤0.2,H≤0.015,C≤0.1,Ti余量。用线切割将TC4钛合金棒材切割成尺寸为10 mm×10 mm×5 mm的块体,并对钛合金10 mm×5 mm的端面进行钻孔,用水性砂纸对试样进行打磨并倒角,之后清洗并吹干;攻内螺纹后用铝线连接。在DH-4型电弧离子镀设备上进行多弧离子镀铝,靶材为纯Al靶 (纯度为99.99%)。为清洁样品表面以提高涂层与基体结合强度,预先用脉冲负偏压对样品轰击3 min。沉积时主要参数如下:Ar气压为0.14 Pa,电弧电流70 A,偏压-100 V,真空室温度为200 ℃,镀膜时间4 h,镀铝层厚度约40 μm。样品经多弧离子镀后使用聚四氟乙烯生料带对连接铝线处进行紧密缠绕,然后将其置于20 g/L Na2SiO3-5 g/L NaOH溶液体系中进行MAO处理,MAO实验采用自制非对称双极多功能交流脉冲电源,以样品为阳极,石墨板为阴极,电流密度为2 A/dm2,脉冲频率为800 Hz,正负向脉冲的占空比分别为70%和20%。MAO时间为2,3和4 h。MAO处理后,样品用去离子水冲洗,再用冷风吹干,置于密封袋中备用。
使用FEI-Inspect F型扫描电子显微镜 (SEM) 对氧化物陶瓷膜的表面及截面形貌进行观察,使用SEM上自带的能谱分析仪 (EDS,Oxford X-max) 检测样品中的元素成分。采用PW1700型X射线衍射仪 (XRD) 对氧化膜进行相分析。利用FM-700型显微硬度测试仪测试MAO膜的截面显微硬度,载荷为50 g,保压时间15 s。在SRVⅢ型往复摩擦磨损试验仪上对MAO试样进行摩擦磨损实验,摩擦副为直径10 mm的WC-Co球 (Co含量8%,质量分数),球硬度1600 HV,行程为1 mm,频率为5 Hz,载荷为10 N,摩擦时间为30 min,环境温度维持在大约24 ℃,湿度在约39.5%。每个样品重复3次,相近的重复结果视为最终性能。使用Zwick/Roell Z050型拉伸试验机测量膜层与基体的结合强度,测试过程中横梁位移速率为0.5 mm/min,实验进行至样品拉断为止,测试中采用E-7结构胶作为黏接剂。
2 结果与讨论
2.1 MAO膜微观结构
图1为TC4钛合金离子镀铝后MAO膜的表面形貌。可以看出,MAO不同时间所得到的膜层表面均存在熔融颗粒、火山喷射状孔洞及一些微裂纹,其中熔融颗粒为熔融再凝固的固体氧化物;直径为几微米到几十微米不等的孔洞为残留的放电通道;裂纹是由于喷射出的高温熔融氧化物接触较冷电解液,在热应力的作用下而产生的。微弧氧化2 h时 (图1a),熔融颗粒和放电微孔的尺寸较小。随MAO时间延长至3 h (图1b),膜层厚度增加,导致表面的放电薄弱点减少,同时所需的击穿电压也随之增加;伴随氧化反应过程中熔化-凝固持续进行,熔融氧化物不断向外喷溅,熔融颗粒尺寸变大。当MAO时间达到4 h (图1c),施加的电压达到最大值,但放电集中在较少的部位,局部的剧烈放电导致更多的高温熔融氧化物形成;当这些熔融氧化物沿放电通道喷射出时,在表面遇冷形成尺寸更大的熔融颗粒,膜层表面粗糙度增加,放电微孔直径也由几微米增长到几十微米。
图1 TC4钛合金离子镀铝层MAO膜的表面形貌
图2为TC4钛合金离子镀铝层MAO膜的截面形貌。可知,MAO膜分为两层:存在明显孔洞及少量裂纹的疏松层和内部致密层,疏松层与致密层之间没有明显的分界线,致密层存在少量与基体不连通的微孔。随MAO时间的增加,氧化物陶瓷膜的厚度增大,留存的镀铝层厚度减小。MAO处理4 h (图2c) 时,镀铝层完全氧化,部分基体也被氧化,并形成厚度约1 μm的过渡层。由于Al氧化为Al2O3时体积膨胀,因此镀铝层完全氧化后,氧化膜厚度 (约60~70 μm) 大于原始镀铝层厚度 (约40 μm)。从图2还可看到,随着MAO时间的延长 (图2a和b),MAO膜层的致密层变得更厚、更致密,疏松层内的孔洞尺寸增加;但微弧氧化4 h后,在局部被氧化的基体处出现贯穿整个氧化膜的裂纹 (图2c中箭头所指),致密层的缺陷反而增多。EDS分析 (图3) 表明,贯穿裂纹附近膜层中生成了一定量Ti的氧化物。Liu 等[24]和Gao等[25]在纯Ti表面沉积一层Al,然后进行MAO,测试了MAO后Ti在氧化膜中的分布,结果表明:当Al层完全氧化后,再延长氧化时间时,Ti出现在MAO膜的放电通道中,在放电通道靠近Ti基材的膜中检测到Al2TiO5,以及电解液的残留。这与本文的研究结果是一致的。他们认为,MAO过程中放电机制为陶瓷层[24]或阻障层[25]的击穿。因此,可以推断本研究中Ti氧化导致其上Al2O3陶瓷层产生贯穿裂纹与贯穿性放电通道形成有关。但是,在Al层未完全氧化时,MAO只发生在镀铝层,同样发生等离子放电和Al2O3陶瓷膜的击穿,但是却未出现这种贯穿性裂纹,其中原因尚需深入研究。
图2 TC4钛合金离子镀铝层MAO膜的截面形貌
图3 TC4钛合金离子镀铝层MAO 处理4 h形成的膜层截面元素EDS分析结果
2.2 MAO膜的相结构
图4是MAO不同时间获得的膜层的XRD谱。可见,MAO膜层均由α-Al2O3和γ-Al2O3组成。其中,α-Al2O3是主要组成相。在图谱中20?~40?的范围内有很多漫散射峰,说明有非晶相的存在。结合EDS检测结果可得出,这些非晶相主要成分为SiO2。从图中可看出,随氧化时间的延长,α-Al2O3衍射峰强度逐渐增强,其结构为斜方六面体,是Al2O3的高温稳定相,它的存在使得氧化陶瓷层具有良好的耐蚀、耐磨等性能。
图4 TC4钛合金离子镀铝层MAO膜的XRD分析结果
去掉MAO膜的疏松层后,表面XRD谱见图4b。可见,MAO膜致密层仍主要由α-Al2O3和γ-Al2O3组成。与未去掉疏松层的样品 (图4a) 相比,γ-Al2O3衍射峰大幅减弱,α-Al2O3衍射峰有所增强,说明γ-Al2O3相主要存在于疏松层,而α-Al2O3相则主要存在于致密层。这是因为α-Al2O3相形核所需的Gibbs自由能大于γ-Al2O3相的[26],MAO初期的成膜与电解液直接接触,在电解液的冷淬作用下,主要形成γ-Al2O3相。但是随着反应的不断进行,反应初期形成的致密层不再接触溶液,其冷却速率变慢,内部的γ-Al2O3在电弧热作用下逐渐转化为α-Al2O3;氧化时间越长,转化的α-Al2O3量也就越多。
2.3 MAO膜的硬度
表1为TC4钛合金镀铝层MAO膜的截面硬度。可见,无论是MAO膜的致密层还是疏松层,其硬度相对于基体钛合金 (硬度约为350 HV) 均有提高,并且同一涂层的致密层硬度均高于疏松层。随MAO时间的延长,疏松层硬度呈递减趋势,这与疏松层内孔洞等缺陷随氧化时间的延长而增大、增多有关;微弧氧化3 h时的膜层致密层硬度最高,为1261 HV,约是基体硬度的4倍,这主要归因于随着氧化时间的延长,更多的γ-Al2O3转化为高硬度的α-Al2O3。当MAO时间延长至4 h时,致密层硬度值反而降低,这是由于此时TC4基体亦发生了氧化反应,Ti的氧化物及Ti离子通过放电通道向外喷射迁移,膜层中生成了一定量Ti的氧化物,可能由于含量较少,所以XRD未能检测到,Ti的氧化物硬度较低,因此导致了MAO膜致密层硬度值降低,致密层中裂纹等缺陷增多也是导致其硬度降低的原因之一。
表1 TC4钛合金镀铝层MAO膜疏松层与致密层硬度的测量值与平均值 (HV)
2.4 MAO膜的结合力
对TC4钛合金镀铝层MAO膜的结合强度进行了测试。氧化3 h获得的膜层的结合强度最高,为68 MPa;氧化4 h获得的膜层结合强度最低,为34 MPa;氧化2 h获得的膜层结合强度为40 MPa。观察拉断后样品的断口形貌可知,氧化2 h获得的MAO陶瓷层主要在疏松层/致密层界面附近发生断裂,有小面积区域在致密层/镀铝层界面断裂;氧化3 h获得的MAO陶瓷层部分在致密层/镀铝层界面断裂,部分在致密层内部发生断裂;氧化4 h获得的MAO陶瓷层主要在致密层/钛合金界面发生断裂。因此,可知,镀铝层/钛合金基体界面结合非常好,其结合强度大于68 MPa;MAO膜/钛合金基材界面结合较差,强度最低。MAO膜较薄时,MAO膜/镀铝层/钛合金体系较易在疏松层/致密层界面附近被拉断;而当MAO膜较厚时,MAO膜/镀铝层/钛合金体系较易在MAO膜/镀铝层界面以及致密层内部被拉断。
2.5 MAO膜的耐磨性能
钛合金及钛合金镀铝层MAO不同时间获得的氧化膜层的摩擦磨损实验结果见图5和表2。观察图5的摩擦系数曲线可见,在相同的摩擦实验条件下,钛合金摩擦系数呈锯齿状波动,且波动幅度较大,摩擦系数约为0.82;微弧氧化2和3 h获得的膜层的摩擦系数随时间的延长逐渐增大,分别在7和10 min后变得较平稳,稳态摩擦系数分别约为0.62和0.63;微弧氧化4 h获得的膜层的摩擦系数开始时快速增加,并大幅波动,随后又快速降低至约0.6,然后逐渐增加,在13 min后变得较平稳,膜层稳态摩擦系数约为0.71。可见,MAO膜的摩擦系数较钛合金都有不同程度的降低。由表2可见,钛合金基材的磨损量最高,微弧氧化2和3 h获得的膜层磨损量较钛合金降低了二个数量级,微弧氧化4 h获得的膜层磨损量较钛合金降低了50倍。可见,钛合金镀铝经MAO处理后在钛合金表面形成了硬度较高的Al2O3陶瓷膜,显著提高了钛合金的耐磨性。
图5 TC4钛合金及其镀铝层MAO膜的摩擦系数曲线
表2 TC4钛合金及其镀铝层MAO膜的摩擦磨损实验结果
图6是钛合金及钛合金镀铝层MAO不同时间的膜层与WC-Co球对磨后的表面和截面形貌。钛合金磨损后表面呈犁沟状形貌,附着少量磨屑,磨损表面和磨屑均未检测到W,说明钛合金的磨损机制为微切削引起的磨粒磨损。钛合金镀铝层MAO膜磨损后表面犁痕比较平整光滑,存在少量的磨屑,局部区域发生鳞片状的剥落,MAO时间越长的样品磨屑和剥落区域越多,3种膜层样品磨损后表面均分布着大量的裂纹。对磨损区域的截面形貌进行观察,可见MAO膜层在摩擦过程中仅疏松层受到磨损,磨损后膜层表层变得密实,裂纹只分布在表层,磨损后膜层表层的EDS分析检测到少量的W,说明样品与摩擦副发生了材料转移现象。从图1可知,MAO膜表面胞状突起较多,对磨件在与膜层表面胞状突起多次作用中,使其脱落形成磨粒,这些颗粒填充到疏松层的孔洞中,使磨损层逐渐变得密实 (图6d,f,h)。从磨损后表面形貌 (图6c,e,g) 也可见磨损表面磨屑较少,平整光滑。虽然测量的MAO膜疏松层的硬度相对较低些 (表1),但其硬度值是孔洞和裂纹等缺陷存在时的值,密实后其硬度可能会接近致密层的硬度,从而导致对磨副WC-Co的磨损 (对磨副WC-Co球的硬度为1600 HV),部分WC的磨屑也转移并填充到MAO膜层的表层。由于MAO陶瓷膜是脆性材料,磨损过程中表层发生脆性断裂形成了裂纹,少量区域还发生了鳞片状剥落,因此推断MAO膜的磨损机制主要为微切削和断裂机制引起的磨粒磨损。综合分析实验结果可知,本研究条件下MAO时间越长,所制备膜层的摩擦系数和磨损量都越大,这种变化趋势与其膜层疏松层的微观结构和硬度值密切相关,MAO膜疏松层存在的孔洞与裂纹缺陷越多,硬度越低,膜层的摩擦系数越高,磨损量就越大。
图6 TC4钛合金及其表面镀铝层MAO膜磨损后的表面和截面形貌
另外,MAO层与残留镀铝层的厚度对钛合金镀铝层MAO膜的摩擦磨损性能也有影响。虽然从目前的摩擦磨损实验结果来看,微弧氧化2 h的样品的磨损率最小,但是其氧化物陶瓷层的厚度也是最小的。随着摩擦磨损时间的延长,陶瓷层逐渐消耗,其耐磨性随之逐渐降低。微弧氧化3 h的样品的MAO层相对较厚,而且硬度较高,界面结合强度也较高,因此随着摩擦磨损时间的延长,其耐磨性会逐渐优于氧化2 h的样品。微弧氧化4 h的样品的陶瓷层最厚,但是因其镀铝层已几乎完全氧化,Ti基材亦被氧化,氧化物层中形成贯穿性裂纹及含Ti的氧化物,疏松层和致密层的硬度都是最低的;而且,氧化物陶瓷层与基材的结合强度也是最低的,因此氧化4 h样品的耐磨性及综合性能不如氧化3 h的样品。综上所述,控制钛合金镀铝层的MAO时间,使其表面形成的MAO陶瓷层较厚,并保证有一定厚度的残余镀铝层,例如5~10 μm,这样的涂层/合金体系应具有较好的综合性能。
3 结论
(1) 钛合金离子镀铝并MAO处理得到的MAO膜主要由α-Al2O3和γ-Al2O3组成。随着MAO时间的延长,Al2O3陶瓷膜的厚度增加,其致密层硬度亦增加。但是,当MAO时间增长到钛合金基材亦发生氧化时,Al2O3膜致密层内裂纹缺陷增多,硬度下降,Al2O3膜与钛合金基材结合强度降低。
(2) Al2O3陶瓷膜的硬度明显高于钛合金基体的,显著提高了钛合金的耐磨性。
(3) MAO陶瓷膜/镀铝层/钛合金体系的结合强度大于40 MPa,最高可达68 MPa。
免责声明:本网站所转载的文字、图片与视频资料版权归原创作者所有,如果涉及侵权,请第一时间联系本网删除。
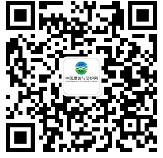
官方微信
《中国腐蚀与防护网电子期刊》征订启事
- 投稿联系:编辑部
- 电话:010-62316606-806
- 邮箱:fsfhzy666@163.com
- 中国腐蚀与防护网官方QQ群:140808414