0 引 言
近年来,热喷涂技术已经被广泛应用于制备不同工况条件下材料表面的冲蚀磨损防护涂层,主要利用其对基体热影响小、设备简单以及生产效率高等优点,目前已取得了较好的效果。热喷涂WC-Co涂层是一种在高温焰流作用下以WC作为硬质相,Co作为粘结相形成的一种硬面涂层。由于Co对WC有很好的润湿性,当温度升高到一定值时,WC能溶解在Co中,温度降低时又形成WC骨架。所以WC可用Co作为粘结相进行高温烧结或复合,使得WC-Co涂层具备高硬度和良好柔性,使得材料表面有效推延冲蚀破坏的孕育期,抑制或减少冲蚀磨损破坏。
大气等离子喷涂(APS)过程涉及极为复杂的等离子电弧的传热与流动、粉末粒子与等离子射流之间以及熔融粒子与基体之间的相互作用,这使得涂层综合性能对喷枪类型、喷涂距离极为敏感。刘延宽等人运用Fluent软件对HVOF焰流进行仿真模拟, 揭示喷涂过程中焰流速度、温度对粒子速度和温度的影响。文魁等人采用SprayWatch3i在线监测系统测量了F6大气等离子喷枪在不同喷嘴条件下产生的等离子射流中Al2O3-3TiO2粒子的温度和速度,研究了粒子的扁平化程度及涂层性能。在喷涂过程中,粒子速度与温度之间的关系是相互矛盾的,在同等喷涂距离下,若要增加粒子的飞行速度,粒子加热的时间就会缩短,降低了粒子的温度;若要增加粒子的温度,粒子的速度就会降低。所以在喷涂过程中,需要获得较好的粒子温度与速度的配合(即合适的喷涂距离)才能获得高质量涂层。
WC-12Co硬质涂层由于具有良好的耐磨耐蚀性能,被广泛应用到工业的各个方面。V·Bonache等人采用等离子喷涂制备微米结构与纳米结构粉末的WC-Co涂层,研究发现电流为625 A时,微米结构的WC-Co涂层在45°冲蚀角下失重率大于大于90°冲蚀角。王海军等人采用HVOF法制备WC-Co涂层,研究了冲蚀角30°与90°下WC-Co涂层的冲蚀磨损性能,研究发现冲蚀角为90°时失重率大于30°,其涂层的失效形式是涂层疲劳剥落。李阳等人利用HVOF法制备WC-Co-Cr涂层,分析了涂层孔隙和层状结构等缺陷对15°、45°、75°和90°攻角下的料浆冲蚀行为。目前,就不同工艺参数对等离子喷涂制备WC-Co涂层性能研究报道较多,主要集中于电流与主气流量方面;涂层抗冲蚀磨损性能研究主要集中于不同冲蚀角度对其的影响。文中以Q235钢为基体采用等离子喷涂制备WC-12Co涂层,研究不同喷涂距离对涂层显微组织、力学性能及抗冲蚀磨损能力的影响,通过测量不同喷涂距离下粒子速度与温度,揭示粒子温度与速度对涂层性能的影响,并探讨WC-12Co涂层冲蚀磨损的机理。
1 试 验
1.1 涂层的制备
基体为Q235钢,粘结拉伸试验采用Φ 20 mm×6 mm试样,冲蚀磨损试验采用30 mm×40 mm×5 mm试样。喷涂时粘结层选用NiCr5Al粉末,粒度为25~45 μm,其质量分数为:5%Al,余量为NiCr。采用喷雾造粒获得WC-12Co球形团聚粉,粉末SEM形貌如图1所示。WC颗粒通过Co黏结相团聚成球形,WC-12Co粉末的粒度分布均匀、且表面光滑,流动性能较好。粒度25~45 μm,流动性20.1 s/50 g,松装密度4.4 g/cm3,其组成(质量分数/%)为:88.0WC,12.0Co,喷涂前所有粉末进行烘干处理。喷砂及等离子喷涂参数见表1。喷涂前将Q235基体表面打磨平整,超声波清洗净化30 min,清除油污及铁锈,而后用粒径为0.5~1.0 mm棕刚玉喷砂粗化处理,喷砂后用过滤的洁净压缩空气将基体表面杂质和浮尘吹除,2 h内完成等离子喷涂试验。涂层制备采用上海大豪纳米材料喷涂有限公司生产的DH-2080型等离子喷涂系统,圆柱形喷嘴内孔径为6 mm。
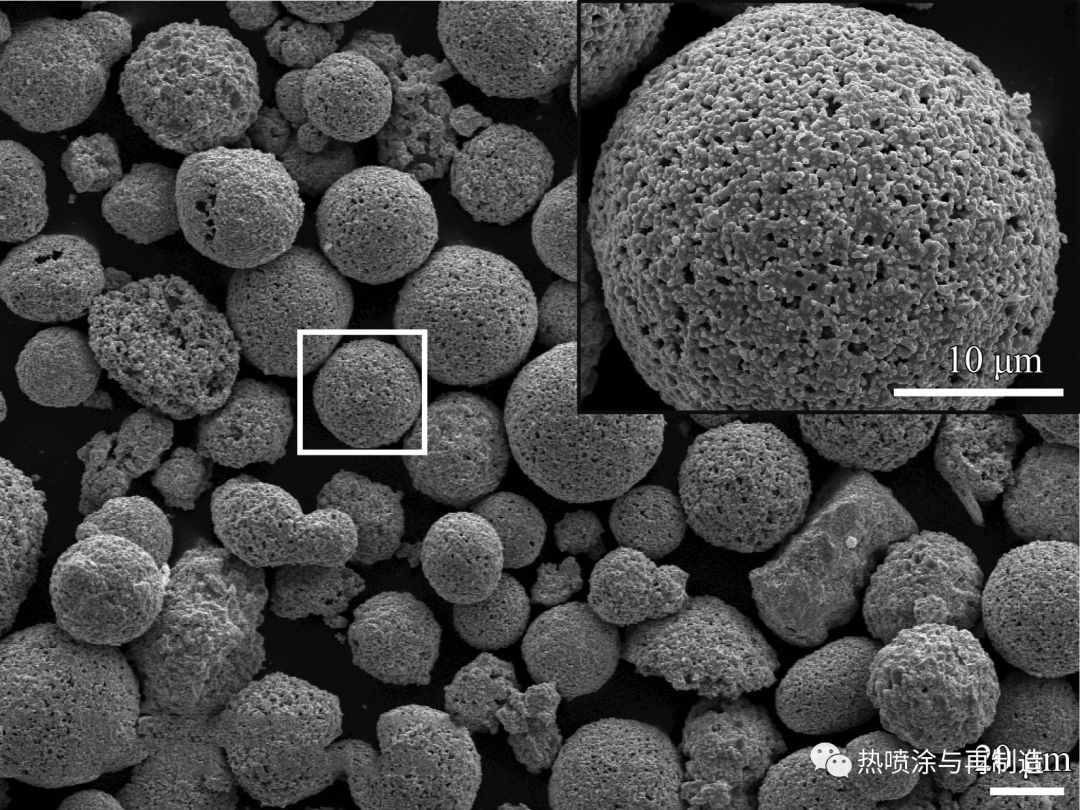
图 1 WC-12Co粉末的微观形貌
表 1 喷砂和等离子喷涂工艺参数
Process |
Parameters |
Values |
Grit-blasting |
Air pressure / MPa |
0.4 |
Blasting distance / mm |
200 |
|
Blasting angle / (°) |
90 |
|
APS |
Current / A |
350 |
Gun traverse speed / (mm·s−1) |
60 |
|
Powder feeder rate / (g·min−1) |
60 |
|
Argon volume flow / (L·h−1) |
2 500 |
|
Hydrogen volume flow / (L·h−1) |
100 |
1.2 涂层的分析与表征
采用LED-1430VP扫描电镜(SEM)观察涂层截面形貌。采用D&Advance型号衍射仪测定涂层物相成分,其基本参数:阳极靶为Cu靶,管电压40 kV,管电流30 mA,扫描速度2°/min,扫描范围为20°~80°,步长为0.02°。涂层成分测定采用OXFORD-2000型能谱仪。Spray Watch 2i热喷涂在线监测系统用于测量等离子射流中飞行粒子的温度和速度。孔隙率测定采用图像灰度法。采用HXD-1000TB维氏硬度仪对涂层显微硬度及韧性进行测定,硬度及韧性均采用0.5 kg载荷。压痕韧性的计算方法如式(1):
KIC=0.113H?D1/2(1+CL/2D)3/2KIC=0.113H?D1/2(1+CL/2D)3/2 (1)
式中,H为涂层维氏硬度,GPa;D为维氏压痕对角线长,μm;CL为压痕四角延伸出的裂纹长之和,μm。涂层的结合强度测定按照GB/T 9793-2012标准进行,采用E-7胶将涂层试样与喷砂后的Q235钢对偶件粘接,经3 h固化后, 通过万能材料试验机测定涂层的结合强度。冲蚀磨损试验采用自制的干砂型常温冲蚀磨损试验机进行,选取新疆当地黄沙,其成分与微观形貌如表2和图2所示,沙粒形状不规则,大部分呈尖角状。角度(0°~90°)利用自制的冲蚀夹具进行调节。采用型号FA2004精度为0.1 mg的电子天平称量试样的冲蚀磨损失重,沙粒流量为250 g/min,每4 min测量一次,计算得到单位面积上的失重量。
表 2 沙粒的主要化学成分
Element |
O |
Al |
Si |
Ca |
Fe |
Mass fraction / % |
48.99 |
8.92 |
27.51 |
2.14 |
4.94 |
图 2 550 μm (30目)沙粒的微观形貌
2 结果与分析
2.1 喷涂距离对涂层相结构的影响
图3为粉末与不同喷涂距离下涂层的XRD图谱。通过对比不同喷涂距离的涂层衍射结果可以看出,4种涂层的主要组成相为WC相,并且涂层中都有一定量的W2C相与脆硬相Co6W6C相,说明涂层中WC已经出现不同程度的氧化脱碳(2WC+O2→W2C+CO2; 2WC→W2C+CO),生成W2C相。通过对比W2C主峰(101)晶面(2θ=39.6°,d=0.227 nm)与WC主峰(100)晶面(2θ=35.7°,d=0.251 nm)的峰高比表3可以看出,喷涂距离为120 mm涂层的W2C/WC峰高比最大,130 mm与140 mm涂层的W2C/WC峰高比最小。说明当喷涂距离为120 mm时脱碳行为最为严重,喷涂距离130 mm与140 mm时脱碳程度最轻。通过EDS分析不同喷涂距离下涂层C的质量分数分别为9.54%,4.67%,12.23%和12.19%。喷涂距离为120 mm时涂层C的质量分数最低,进一步说明WC氧化脱碳严重。
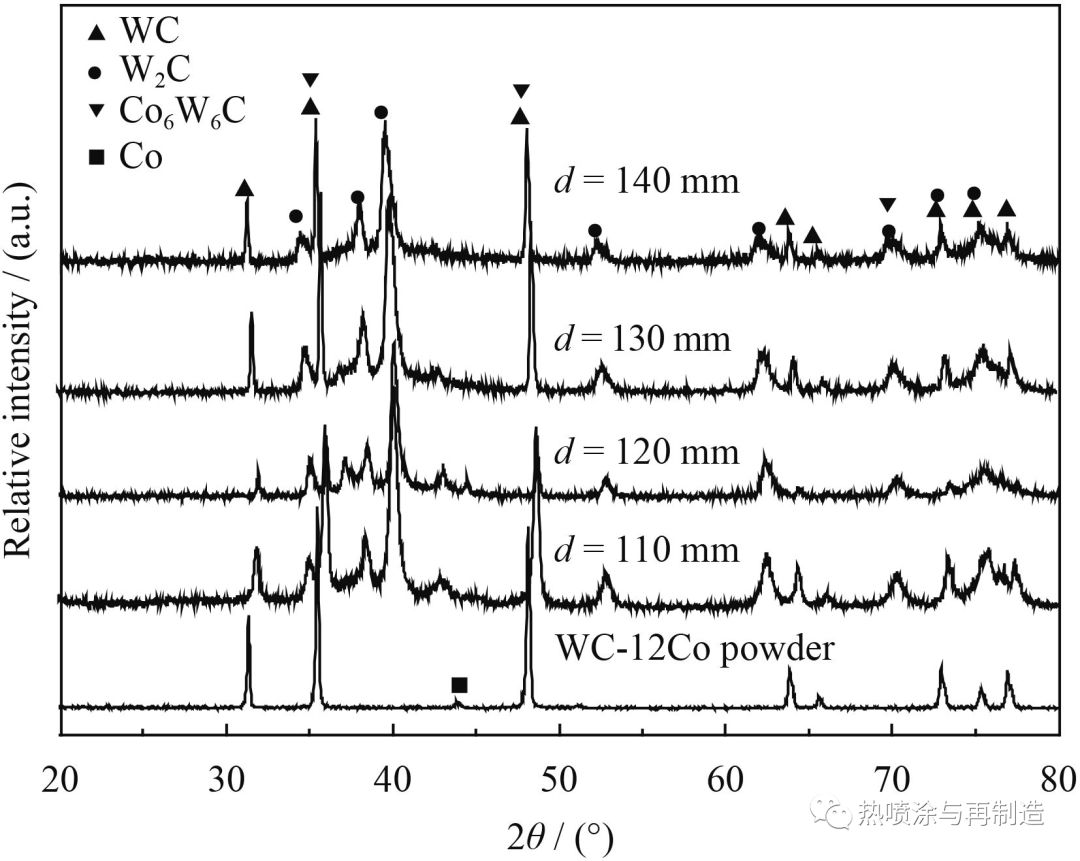
图 3 不同喷涂距离下涂层XRD图谱
2.2 喷涂距离对涂层截面显微组织的影响
图4为不同喷涂距离的涂层截面SEM形貌。由图中可以看出,喷涂距离为120 mm时,涂层沉积厚度最大,涂层厚度约为458 μm(见表3),孔隙率为11.73%,且涂层内部存在一尺寸较大的孔洞。喷涂距离为110 mm和130 mm时,涂层比较致密,孔隙率分别为3.91%和4.04%。喷涂距离为110 mm时,涂层的沉积效率较130 mm时更低,沉积厚度分别为275 mm和361 mm,二者沉积厚度均符合作者设计要求。喷涂距离为140 mm时,涂层沉积效率最差,涂层厚度约220 mm且孔隙率也较大。通过测量4种涂层不同位置的孔隙率看出,涂层近表面处孔隙率较涂层内部孔隙率更大一些。
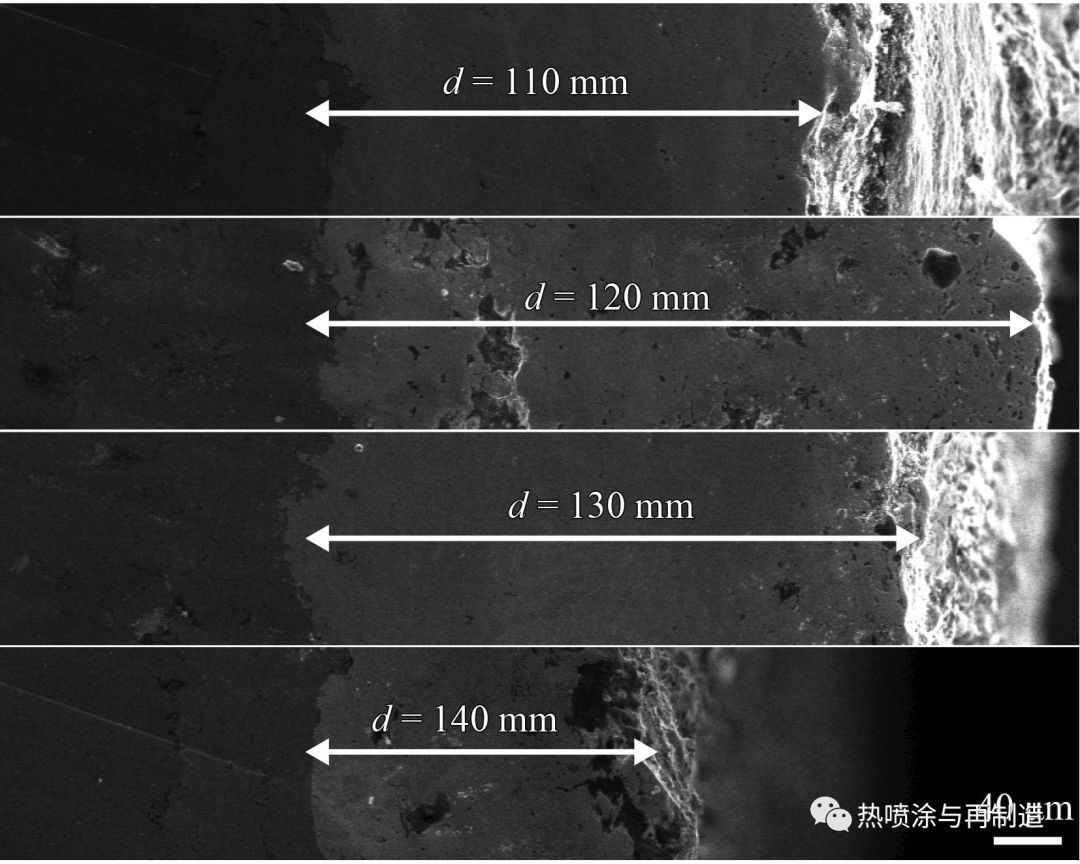
图 4 不同喷涂距离下涂层的截面SEM形貌
2.3 喷涂距离对涂层力学性能的影响
通过不同距离下涂层结合强度和韧性(见表3)的对比,喷涂距离为130 mm时涂层韧性与涂层结合强度均最好,喷涂距离为140 mm时涂层韧性与涂层结合强度较差。图5为不同距离下涂层的压痕裂纹扩展形貌喷涂距离为110 mm时,涂层较为致密,但是脱碳程度相对较高,WC的氧化脱碳使得涂层韧性有所下降。喷涂距离120 mm时涂层脱碳较为严重,孔隙率较大,在压头垂直载荷下涂层出现坍塌现象,压痕周围细小裂纹较多(图5(b)),加之严重的脱碳,涂层韧性下降较快。涂层孔隙率增大,压痕对角线长度增加,该喷涂距离下涂层的显微硬度最低(约907 HV0.5)。喷涂距离为130 mm时,涂层的压痕裂纹扩展形貌(图5(c))中涂层扩展裂纹最少,压痕面积较小,涂层显微硬度可达1 309 HV0.5(表3),涂层韧性较好。通过对比涂层的结合强度(表3)得知,喷涂距离为130 mm时涂层扁平粒子间的结合力较大,在压头垂直载荷作用下,裂纹的扩展能力较弱,从而使得该喷涂距离下涂层压痕裂纹数量较少。喷涂距离为140 mm时涂层力学性能最差,随着喷涂距离的增大,高温熔滴的速度大大降低,粒子的动能不断减小,这是导致涂层力学性能及组织结构均较差的原因。

图 5 不同距离下涂层的压痕裂纹扩展形貌
2.4 涂层冲蚀磨损性能
图6为不同喷涂距离下涂层的冲蚀磨损量随冲蚀时间的变化曲线,冲蚀磨损参数为冲蚀角30°,550 μm(30目),沙粒速度为13.33 m/s。对比4种涂层的冲蚀磨损量,喷涂距离130 mm时涂层抗冲蚀磨损能力最好,110 mm与120 mm次之,喷涂距离140 mm时涂层耐冲蚀磨损能力最差。在冲蚀时间为1~4 min时间段内,磨损量增长幅度较大,4~8 min内磨损量增长幅度减缓,8 min以后涂层冲蚀磨损量增长缓慢。喷涂距离为130 mm时涂层表现出优异的抗冲蚀磨损能力,主要是因为该参数下涂层组织致密,涂层显微硬度、韧性以及结合强度较好。喷涂距离为120 mm时,由于涂层孔隙率较大,涂层脱碳严重,主相WC的量减少,而硬脆相Co6W6C增多,从而使得涂层耐磨性下降。
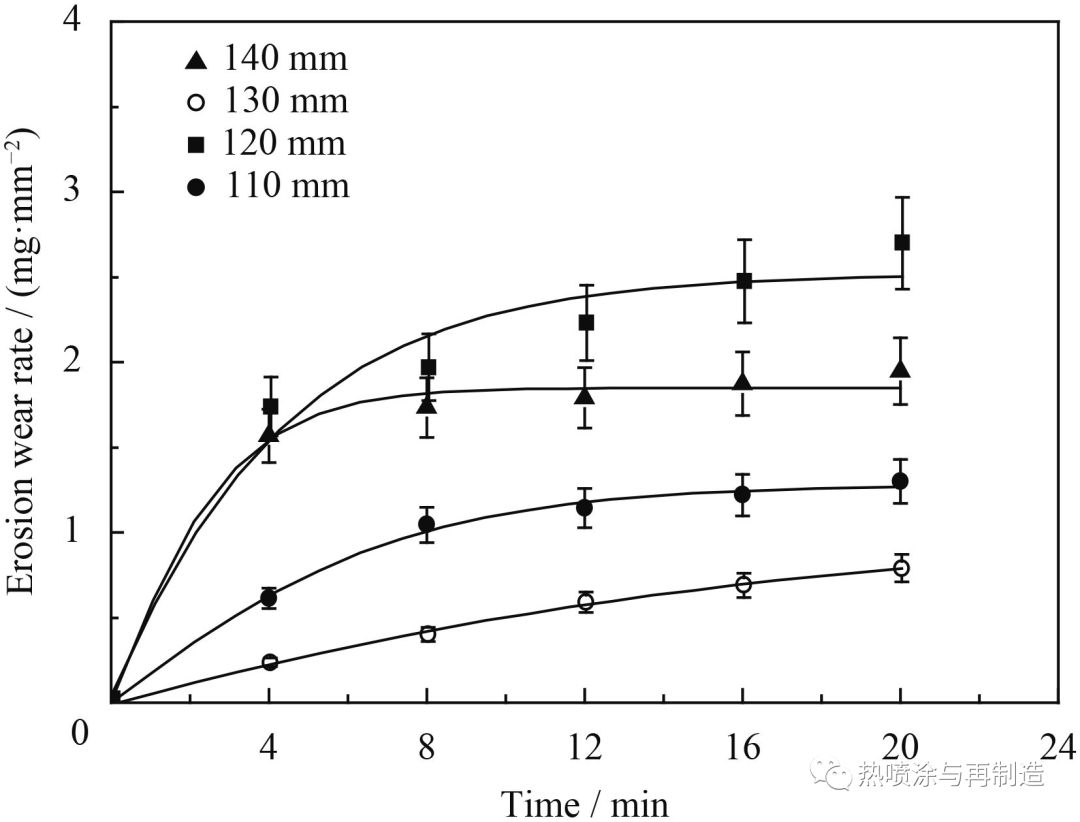
图 6 不同喷涂距离下涂层的冲蚀磨损量
图7为不同沙粒直径下涂层的冲蚀磨损量随冲蚀时间的变化曲线,采用喷涂距离为130 mm时制备的涂层,冲蚀角90°,沙粒速度为13.33 m/s。通过3种不同沙粒直径下涂层冲蚀磨损量的对比,0~12 min时,270 μm(50目)沙粒冲蚀磨损量最大,12 min以后550 μm(30目)沙粒磨损逐渐增大,20 min时270 μm(50目)与212 μm(70目)沙粒冲蚀磨损量接近。由于涂层近表面处孔隙率大于涂层内部,在0~12 min时270 μm(50目)沙粒能获得较大的冲蚀量,随着近表面处孔隙率较大且疏松的涂层剥落以后,冲蚀量也逐渐减缓。而550 μm(30目)沙粒能够持续获得较大动能,与涂层相互撞击时对涂层产生的冲击力较大,从而能获得较为平稳的冲蚀磨损率。
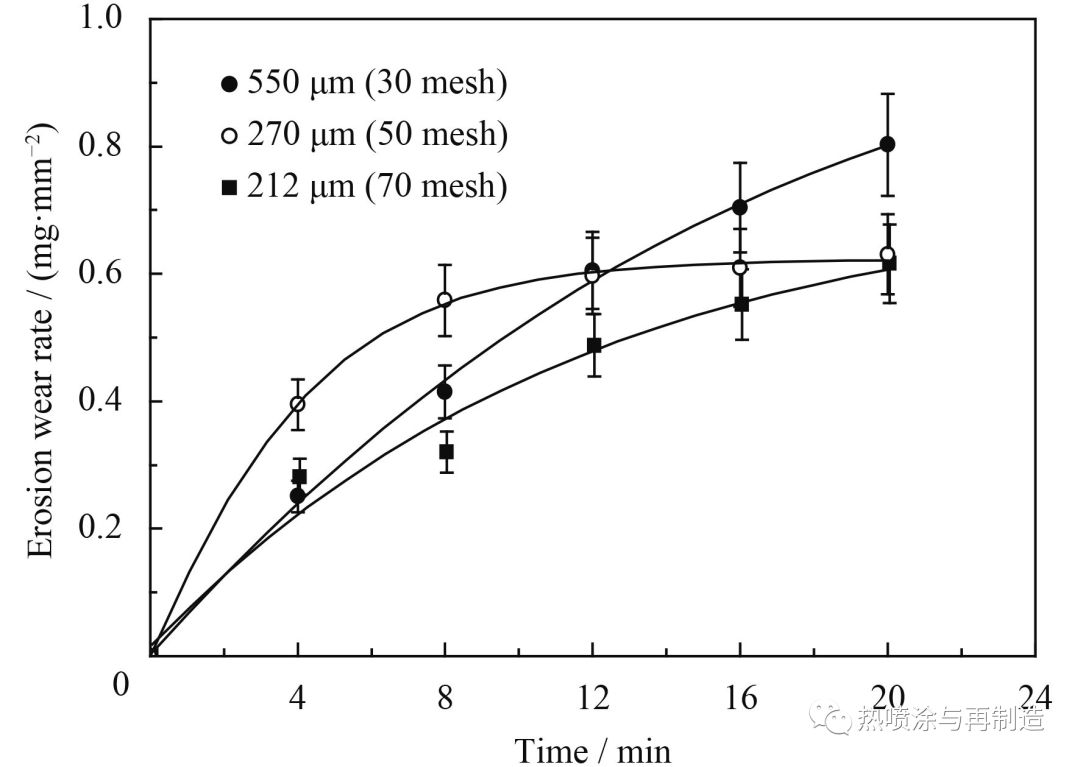
图 7 不同沙粒直径下涂层的冲蚀磨损量
图8为不同沙粒速度下涂层的冲蚀磨损量随冲蚀时间的变化曲线,基本参数为喷涂距离130 mm,冲蚀角90°,550 μm(30目)。沙粒速度15.68 m/s时冲蚀磨损量大于速度为13.33 m/s时的磨损量。冲蚀磨损量与沙粒的速度存在如式(2)关系:
V=Kv0nV=Kv0n (2)
式中:v0为粒子速度,m/s,n为常数。在正向冲击条件下,陶瓷材料n值约为3。通过式(2)得知,涂层冲蚀磨损量随着沙粒速度的增大而增大,与试验结果一致。资料表明,沙粒的速度对涂层的冲蚀机理没有影响。

图 8 不同沙粒速度下涂层的冲蚀磨损量
图9为不同冲蚀角度下涂层的冲蚀磨损量随冲蚀时间的变化曲线,试验参数:喷涂距离为130 mm,550 μm(30目),沙粒速度13.33 m/s。在冲蚀到20 min时,冲蚀角为60°时冲蚀磨损量最大,冲蚀角90°时冲蚀磨损量次之,冲蚀角为30°时冲蚀磨损量最小。在0~4 min时,30°与90°冲蚀磨损量增长较为缓慢,而冲蚀角为60°时冲蚀磨损量增长较快。
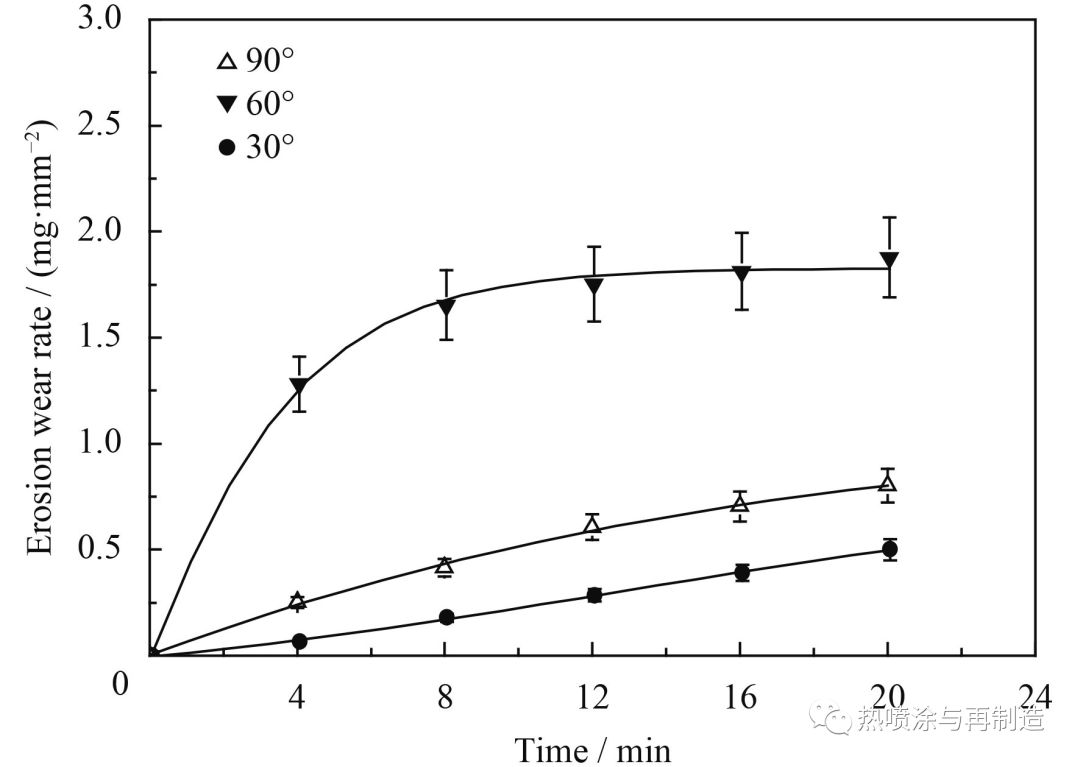
图 9 不同冲蚀角度下涂层的冲蚀磨损量
3 讨论
图10为粒子速度与温度随喷涂距离变化曲线。由图看出粒子温度在120 mm处达到最大,100~120 mm之间温度增长较快,120 mm以后粒子温度缓慢降低。粒子速度在100 mm处最大约为315 m/s,100~150 mm之间粒子速度呈递减趋势,140 mm处粒子速度下降较快。WC熔点为2 776 ℃,WC在低于室温到2 776 ℃的温度范围内都是稳定的。喷涂距离110 mm到140 mm的粒子温度都高于2 776 ℃,理论上该范围内粒子可以完全熔化。但事实上WC并不能完全熔化,受等离子射流向粉末粒子传热能力的大小及粉末粒子自身的热导率,粒子在射流中停留时间较短(约10?3 s)。
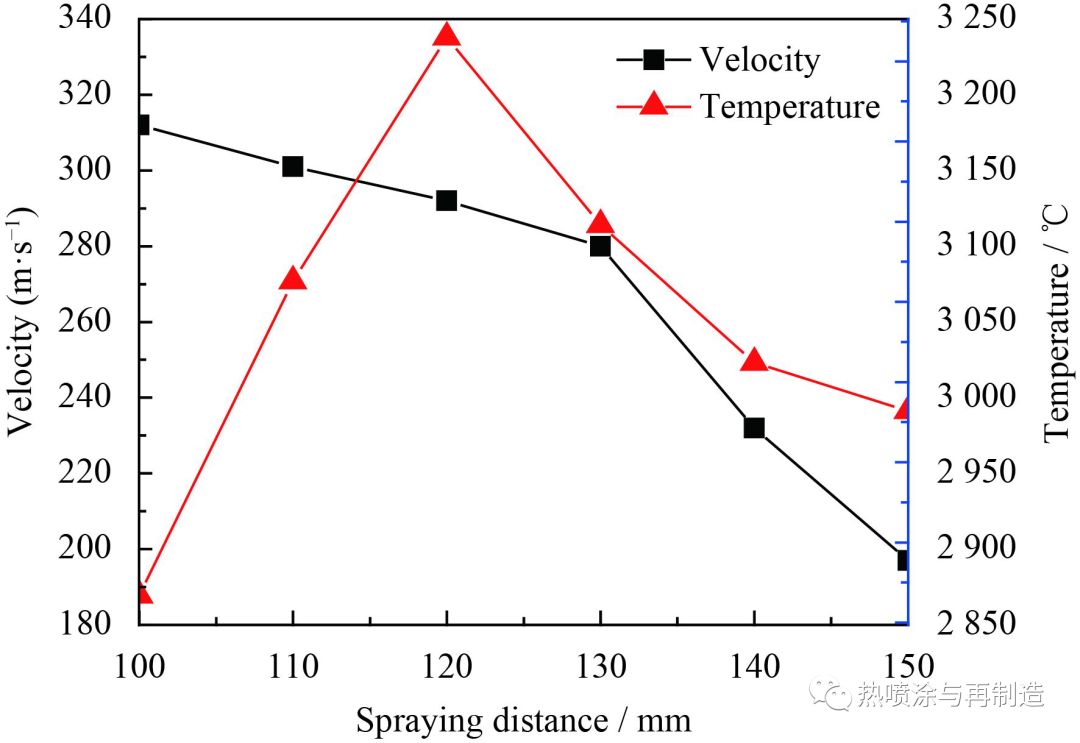
图 10 喷涂距离对飞行粒子温度与速度的影响
文献中提出,熔滴的飞行速度及温度是影响涂层的结构和性能的两个重要参数。在喷涂过程中,喷涂粉末经历加速、熔化和撞击这3个过程,高速飞行的高温熔融粒子在撞击基体或先沉积扁平粒子的瞬间,具有良好的熔化和扁平状态是保证涂层具有高的致密结构和结合强度的重要因素。等离子焰流的速度与温度沿轴线截面呈高斯分布,焰流中心速度、温度高。图11为不同喷涂距离下涂层表面形貌,120 mm处粒子温度最高且速度相对较大,扁平化粒子基本全部熔化,边缘呈溅射状。130 mm粒子基本熔化,粒子扁平化程度好,边缘无溅射状。110 mm与140 mm粒子未充分熔化,110 mm粒子熔化程度稍好于140 mm粒子,可以看到扁平粒子中心有未熔化WC颗粒。
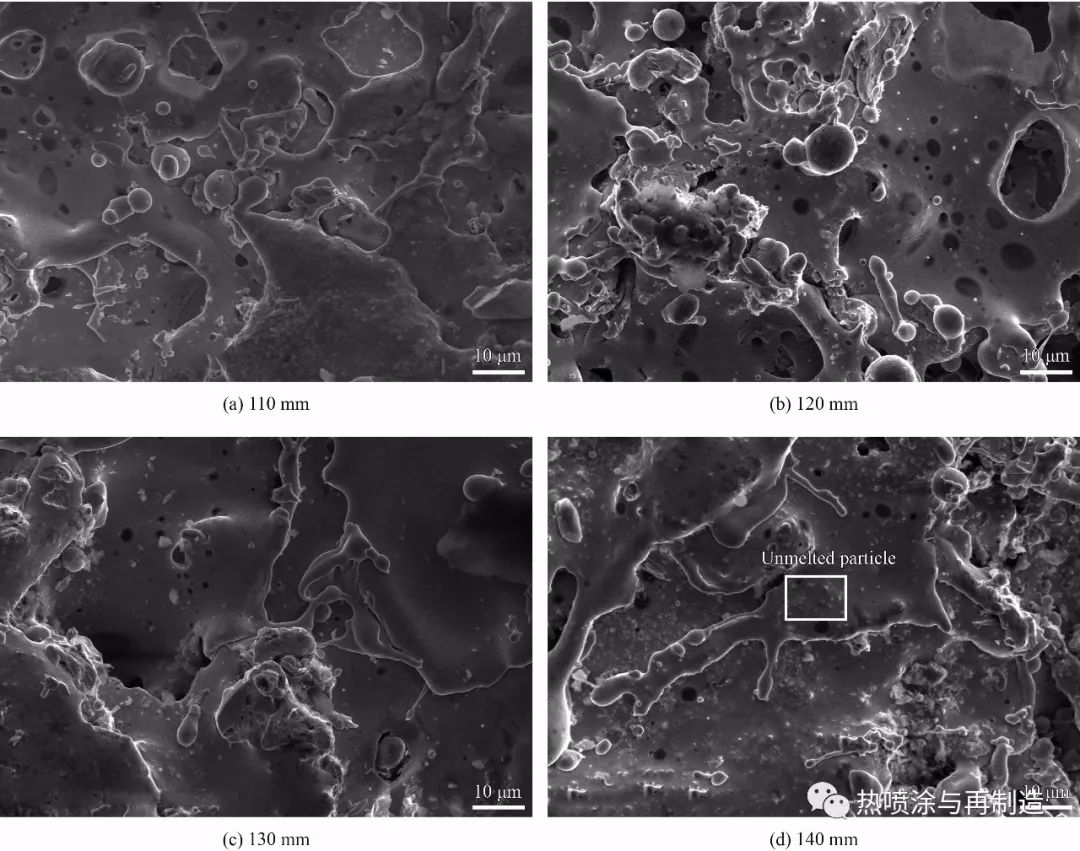
图 11 不同喷涂距离下涂层的表面形貌
110 mm粒子飞行速度快,在等离子焰流中停留时间较短而没有完全熔化,上层扁平粒子中未熔化WC颗粒对下层扁平粒子不断冲击作用,致使涂层致密度较高,没有明显孔隙。但由于涂层离喷嘴较近,等离子焰流对涂层再次加热,致使该距离下涂层氧化脱碳,脆相W2C增多,柔韧相Co部分被消耗,降低了涂层硬度与涂层韧性。120 mm粒子边缘出现飞溅,影响了其他高温熔滴的飞行路径和扁平化程度,扁平粒子之间搭接不平整,致使出现大量孔洞。根据XRD分析(图3)得知120 mm涂层脱碳最为严重,由于该距离处粒子温度最高,粒子速度有所降低,粒子在等离子焰流中加热时间变长,使得WC严重脱碳,涂层严重脱碳致使W2C增多,大量Co相被消耗产生Co6W6C,使得涂层硬度与韧性明显降低。130 mm粒子扁平化程度较好,边缘无明显飞溅,扁平粒子之间搭接完好,粒子充分熔化,增加了熔滴的流动性,可有效减小涂层的孔隙率。其原因是粒子温度和速度有所降低,二者达到了一个良好的配合度,结合强度达到最大。XRD分析130 mm涂层氧化脱碳程度较轻,WC与Co得到较好保留,WC颗粒间的润湿性有极大改善,这有助于增加Co黏结相与WC颗粒间的互扩散、固熔,使得粉末颗粒间的结合强度提高,增加裂纹尖端临界应力场强度,最终提高该距离下涂层的硬度与韧性。140 mm时粒子温度与速度都降低较快,粒子未充分熔化,未熔化WC颗粒撞击基体后出现反弹,降低了涂层沉积效率,同时影响其他飞行粒子的路径,减弱了未熔粒子的冲击作用,致使涂层结合强度下降,扁平粒子之间搭接程度较弱,涂层孔隙率升高。虽然140 mm脱碳程度较轻,涂层硬度适中,但孔隙率的升高使得涂层断裂韧性下降。
图12为冲蚀角为90°时不同喷涂距离下涂层表面的冲蚀磨损形貌。从低倍SEM形貌可以看出,喷涂距离为120 mm和140 mm有明显的剥落痕迹,表面较为粗糙,140 mm时涂层表面有明显的剥落坑。喷涂距离为110 mm与130 mm涂层表面较为平整。通过对比不同喷涂距离的涂层高倍SEM形貌,喷涂距离为110 mm和130 mm时,涂层表面有沙粒撞击后发生的变形,而在喷涂距离为120 mm和140 mm时并没有发现。可能是110 mm和130 mm涂层的韧性好、结合强度高的缘故,减缓了沙粒对涂层的撞击作用,且涂层具有低孔隙率,从而提高了涂层抗冲蚀磨损的能力。喷涂距离为140 mm时涂层表面出现较大的剥落坑,其原因是该涂层力学性能较差,孔隙率较大导致抗冲蚀磨损能力变差。同时也说明说明涂层抗冲蚀磨损能力主要取决于涂层孔隙率、显微硬度、韧性及结合强度。

图 12 不同喷涂距离下涂层表面的冲蚀磨损SEM形貌
图13为不同冲蚀角度下(喷涂距离为130 mm)涂层表面的冲蚀磨损形貌。从30°冲蚀角下的冲蚀磨损形貌图13(a)(d)可以看出,涂层片状脱落痕迹较为明显,表面嵌入沙粒较少。涂层表面的冲蚀坑及硬质相剥落坑较多,部分区域有变形犁沟出现,凹坑内存在部分细小未熔合的WC颗粒。分析原因是涂层在冲蚀磨损初期,高速形状不规则沙粒以低角度冲击到涂层表面,高速沙粒与涂层中包裹WC的柔韧性相Co相互撞击,不规则沙粒将粘结相挤向两侧,形成犁沟;高速沙粒与硬质相WC相互撞击时,动能较小的沙粒被反弹出去;而动能较大的沙粒则不断撞击WC,使得硬质相WC与粘结相Co相对滑动,发生塑性变形形成唇片或变形脊。冲蚀过程继续进行,由于塑性变形形成的唇片被沙粒切削脱落,W颗粒失去粘结相Co的包裹而裸露出来。随着冲蚀的加剧,裸露的WC颗粒被高速沙粒撞击而剥落,致使涂层冲蚀磨损。图14(a)(b)(c)为30°涂层冲蚀表面EDS面扫描分析,质量分数:7.77%C,2.20%O,32.80%Co,57.33%W。Co元素明显增多,W元素降低,其他元素变化不大,说明部分WC颗粒被冲蚀剥落,与冲蚀机理分析结果一致。所以微观切削、犁沟变形和微观疲劳剥落是30°冲蚀角下的冲蚀磨损特征。由于WC-12Co涂层表面硬度较高,抗低角度冲蚀能力强,涂层冲蚀磨损率低,说明涂层具有较好的抗低角度冲蚀磨损能力。
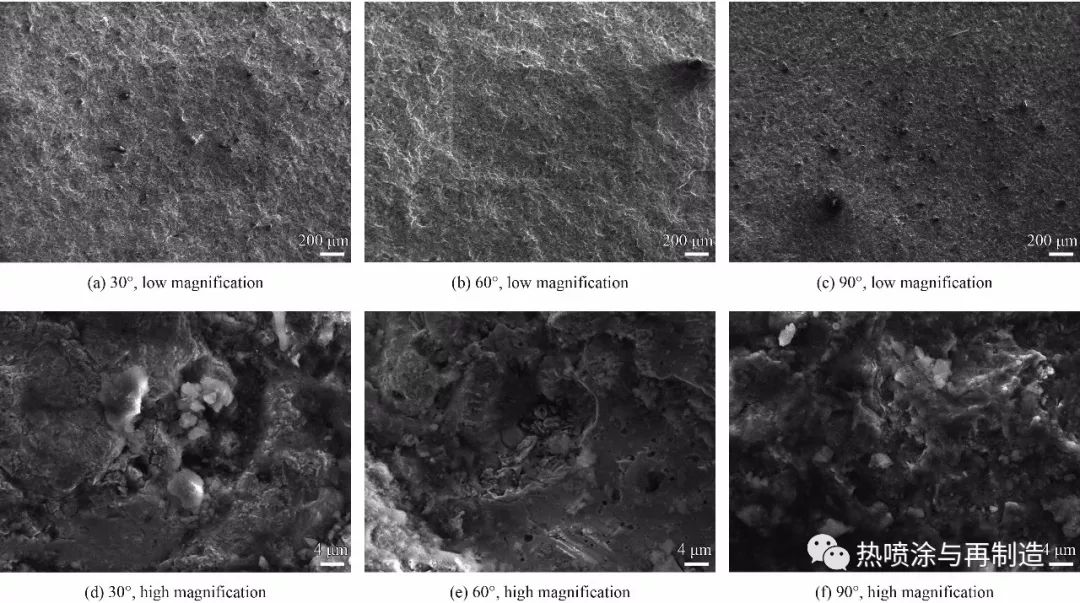
图 13 不同冲蚀角度下涂层表面的冲蚀磨损SEM形貌
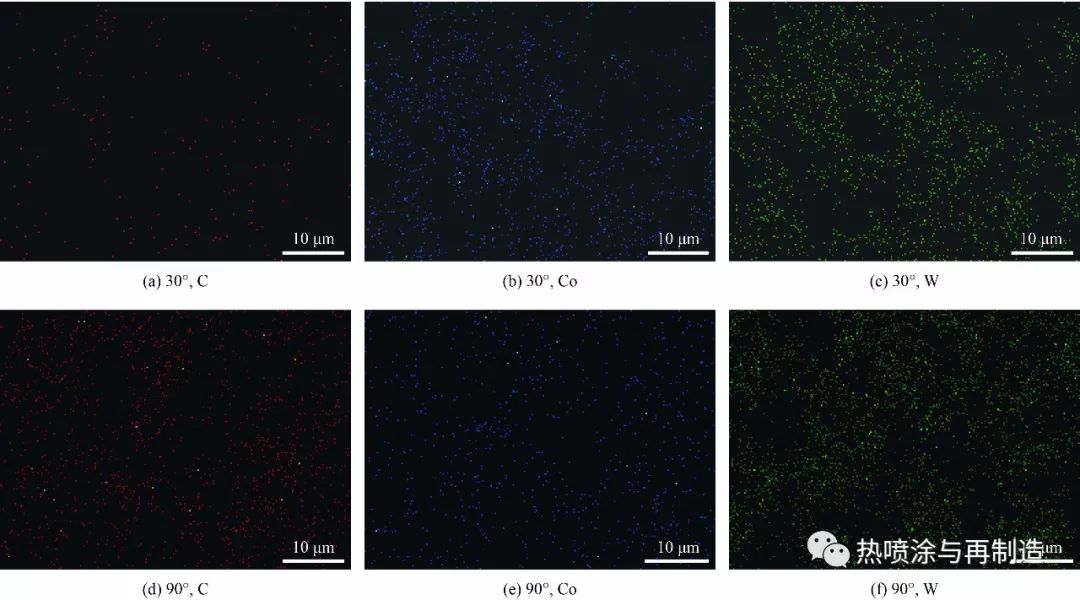
图 14 冲蚀表面EDS面扫描分析
在90°冲蚀角下的冲蚀磨损形貌图13(c)(f)可以看出,涂层主要受到磨粒锤击作用的影响,涂层没有明显的切削痕迹,有显著的层状剥落痕迹,表面较为平整。图14(d)(e)(f)为90°涂层冲蚀表面EDS面扫描分析,质量分数:12.23%C,4.55%O,16.32%Co,66.90%W,4种元素含量变化基本没有变化。冲蚀颗粒正面高速冲击涂层表面,受到挤压形成突出的唇片(图13(f)),冲蚀粒子不断对突出的片状进行捶打,涂层周围出现畸变层,经过严重的塑性变形之后,涂层次表面形成脉动循环应力,促使裂纹不断扩展,直至裂纹贯通使得涂层破坏剥落造成涂层质量流失,主要表现为疲劳剥落。
从60°冲蚀角下的冲蚀磨损形貌(图13(b)(e))可以看出,涂层中小型凹陷增多,涂层片状脱落痕迹明显,表面嵌入沙粒较少。冲蚀坑(图13(e))明显较30°时增大,周围由于涂层剥落而出现明显的分层现象,在切削和锤击效应的双重作用下,涂层表面受到沙粒垂直撞击的力度增大,涂层失效形式介于30°与90°之间,致使涂层的失重率高于90°和30°的失重率。
4 结论
(1)在等离子喷涂WC-12Co涂层中,喷涂距离对涂层显微组织结构及力学性能影响较大。综合比较不同喷涂的涂层组织及力学性能,喷涂距离为130 mm时涂层质量较好,喷涂距离为120 mm与140 mm时涂层质量较差。
(2)高速飞行的高温熔融粒子在撞击基体或先沉积扁平粒子的瞬间,具有良好的熔化和扁平状态是保证涂层质量良好的重要因素。选择合适的喷涂距离能够保证较好的粒子温度与速度的配合,提高涂层抗冲蚀磨损能力。
(3)冲蚀时间在0~4 min内,涂层冲蚀磨损量增长较快,8 min以后磨损量缓慢增长。涂层抗冲蚀磨损能力主要取决于涂层孔隙率、显微硬度、韧性及结合强度。喷涂距离为130 mm时涂层的抗气固两相流冲蚀磨损能力更好。550 μm(30目)沙粒对涂层冲蚀磨损量最大,270μm(50目)与212 μm(70目)沙粒对涂层冲蚀量基本一致;随着沙粒速度增大,磨损量逐渐增大。
(4)在冲蚀角为60°时冲蚀磨损量最大,90°次之,小角度30°冲蚀磨损量最小;在小角度30°冲蚀时,微观切削、犁沟变形和微观疲劳剥落是冲蚀磨损的特征,涂层具有较好的抗塑性冲蚀磨损能力;在大角度90°时,疲劳剥落为主要特征,涂层有较好的抗脆性冲蚀磨损性能。
更多关于材料方面、材料腐蚀控制、材料科普等方面的国内外最新动态,我们网站会不断更新。希望大家一直关注中国腐蚀与防护网http://www.ecorr.org
责任编辑:殷鹏飞
《中国腐蚀与防护网电子期刊》征订启事
投稿联系:编辑部
电话:010-62313558-806
邮箱:fsfhzy666@163.com
中国腐蚀与防护网官方 QQ群:140808414
免责声明:本网站所转载的文字、图片与视频资料版权归原创作者所有,如果涉及侵权,请第一时间联系本网删除。
相关文章
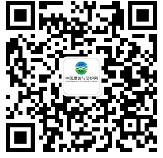
官方微信
《中国腐蚀与防护网电子期刊》征订启事
- 投稿联系:编辑部
- 电话:010-62316606-806
- 邮箱:fsfhzy666@163.com
- 中国腐蚀与防护网官方QQ群:140808414
点击排行
PPT新闻
“海洋金属”——钛合金在舰船的
点击数:8125
腐蚀与“海上丝绸之路”
点击数:6461