文/ 付安庆 尹成先 冯耀荣 白真权 韩燕 吕乃欣
中国石油集团石油管工程技术研究院 石油管材及装备材料服役行为与结构安全国家重点实验室
前言
我国油气资源西部接替东部格局正加快形成,特别是新疆地区2030 年前有望建成亿吨级油气生产基地。评价调查显示,新疆地区石油地质资源量228亿吨,占全国22%。塔里木油田是我国“西气东输”工程的主力气源地,克拉玛依油田是我国西部地区的千万吨及大油田,塔河油田已跻身我国陆上十大油田之列。新疆地区油气田开发生产工况环境普遍具有“高温、高压、高CO2、高H2S、高Cl-、高矿化度”的特点,最高压力达130MPa、最高温超过200℃、CO2 含量最高达4MPa、H2S 含量最高达1MPa、Cl- 浓度普遍在十万以上、矿化度在二十万左右,这些复杂苛刻的工况条件加之特殊的作业的工艺(如井下的酸化压裂、地面集输管线各种加注药剂)导致油气管柱和管道发生严重腐蚀失效。由于新疆地区油气田开发环境较为苛刻,腐蚀问题引起的石油管材失效已成为油气资源安全开发和生产的主要威胁之一,特别是随着我国新《安全生产法》和《环境保护法》的颁布实施,安全和环境保护两大主题已成为油气田开发生产过程中的重中之重。
井下管柱常见的腐蚀失效形式
1.酸化液腐蚀
对于一些碳酸盐层,需要采用酸化压裂工艺将原来不连通的孔隙连通起来,最终提高石油或天然气的采出率。
碳酸盐岩层酸化压裂液一般采用的土酸酸液,其主要成分为10%HCl + 1.5%HF+3%HAc + 5% 酸化缓蚀剂,其对油气井管柱具有非常高的腐蚀性。该类腐蚀已成为塔里木油田库车山前区块超深高温高压气井油管柱的主要威胁之一(现场照片如图1),主要是因为井下180 ~ 200℃超高温工况和酸液的高腐蚀性共同作用,而且残酸返排过程中因酸化缓蚀剂浓度急剧降低,导致残酸返排阶段腐蚀性还持续较强。
腐蚀介质:酸化压裂液。
腐蚀程度:高腐蚀性。
腐蚀特点:局部腐蚀,腐蚀周期短(酸化压裂周期在2-4 小时,残酸返排周期3-6 天)。
治理措施:开发新型酸化压裂液体系、开发高效耐高温的酸化缓蚀剂和升级管材。
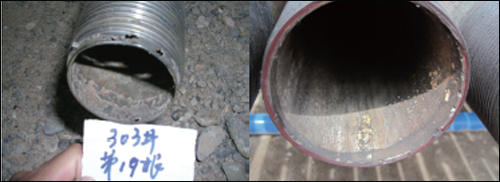
图1 超级13Cr油管酸化液腐蚀
2.含CO2/H2S地层水腐蚀
地层水是指在油气井正常生产过程中随着油气介质的产出水,地层水的主要离子包括:CO32-、HCO3-、OH-、Cl-、SO42-、Ca2+、Mg2+、K+、Na+,新疆地区油气田井下地层水总矿化度在二十万左右,其中Cl 离子的含量在十几万左右,其pH 值一般在5 ~ 8 之间。由于井下的CO2 或H2S 的存在导致该类腐蚀是所有油气田井下管柱发生腐蚀的主要原因之一,而由于其高含Cl-,其往往导致管柱发生局部腐蚀,特别是局部腐蚀,如图2 所示。
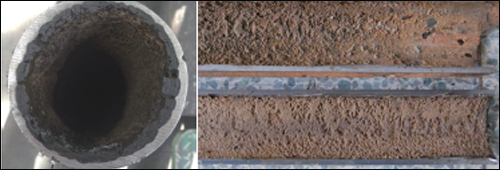
图2 P110碳钢油管内表面地层水腐蚀
腐蚀介质:地层水,CO2,H2S(少量)。
腐蚀程度:较高腐蚀性。
腐蚀特点:局部腐蚀,腐蚀周期长,伴随油气井的整个生产过程。
治理措施:升级管材。
3.注气井氧腐蚀
注氮气法被广泛应用于提高石油采收率(EOR 或IOR),但伴注气技术的应用,随之而来的腐蚀问题也日益凸显,由于井下的腐蚀环境复杂,在注气焖井的过程中,若未及时采取相应的防腐蚀措施,往往会造成油管腐蚀事故频发。塔河油田所注氮气主要来源于膜制氮,膜制氮制得的氮气纯度在95%-98% 之间,氧气含量3%-5%。
在注气过程中,注气时间较短,注气温度较低(30℃),因此注气过程对油管腐蚀的影响相对较小,但经焖井后,注气带入的氧在后续的限压放喷生产和进行压井换机抽管柱生产过程中会发生氧腐蚀,进而给生产过程带来较严重的危害,所以氧腐蚀及腐蚀产物(氧化物)结垢成为导致井下管柱、大小柱塞和抽油杆失效的主要因素。腐蚀介质:注入水,O2,CO2。
腐蚀程度:高腐蚀性。
腐蚀特点:局部腐蚀,且结垢非常严重,腐蚀周期长,伴随油气井整个注气过程。
治理措施:升级管材,内镀层、非金属内衬。
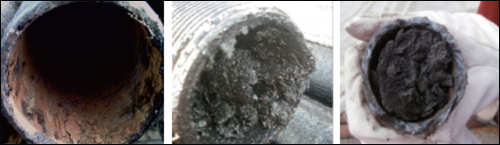
图3 碳钢油管在注气过程中的腐蚀及结垢
4.应力腐蚀开裂
由于新疆地区油气田井下腐蚀环境普遍较为苛刻,普通碳钢油管已无法适应该类服役工况环境,超级13Cr 马氏体不锈钢油管得到普遍应用,近年来,超级13Cr 应力腐蚀开裂问题屡屡出现。
据报道,超级13Cr 马氏体不锈钢在氯化物完井液(CaCl2、MgCl2、NaCl 等)、磷酸盐完井液(K2HPO4、Na2HPO4 等)、硫化氢(H2S)溶液中会发生应力腐蚀开裂。研究表明导致超级13Cr 马氏体不锈钢应力腐蚀开裂的敏感介质形成的混合环境(即两种或两种以上的介质混合)更容易引起应力腐蚀开裂的发生。
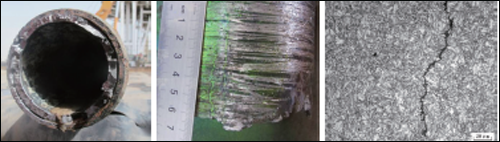
图4 为超级13Cr 油管在磷酸盐完井液中的沿晶型应力腐蚀开裂
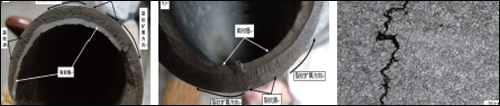
图5 为S135钻杆在硫化氢环境中的沿晶型应力腐蚀开裂。
(1)磷酸盐完井液应力腐蚀开裂腐蚀介质:磷酸盐。
腐蚀程度:较高应力腐蚀开裂敏感性。
腐蚀特点:起源于油管外壁,沿晶型和穿晶型皆存在。
治理措施:优化完井液配方,采用甲酸盐完井液体系。
(2)硫化氢应力腐蚀开裂腐蚀介质:硫化氢。
腐蚀程度:极高应力腐蚀开裂敏感性。
腐蚀特点:起源于油管内壁,沿晶型。
治理措施:升级管材。
全尺寸实物管柱腐蚀系统介绍
采用小试样在高温高压釜系统中模拟油气田工况进行挂片实验是研究石油天然气工业高温高压环境中管材及设备腐蚀的最常见最经典方法,该方法往往不能真实反映现场井下管柱的腐蚀行为,主要是因为:首先,小试样由于尺寸因素往往无法全面反映全尺寸管柱的腐蚀行为和形貌;第二,小试样如四点弯曲法和应力环法虽然可以加力,其加载的均为单方向的应力,不能反应井下管柱的复杂受力状况,井下管柱一般都受到内压、外拉、振动、交变等复杂载荷;第三,小试样无法反映管柱接头在服役过程中因腐蚀导致密封失效的行为,而接头密封失效往往是导致管柱最重要的失效因素之一。鉴于小试样模拟工况腐蚀研究方法的缺点,石油管工程技术研究院自主研发了“全尺寸石油管高温高压实物拉伸应力腐蚀系统”,该系统相对于高温高压釜内的小试样腐蚀方法具有如下三个优势:第一,其内压、外拉力、温度和介质等重要工况参数可完全满足超高温高压气井极端工况下管柱腐蚀的研究需要;第二,全尺寸管柱研究过程中涵盖了管柱接头的腐蚀研究,由于现场管柱大部分的失效与油管接头腐蚀密封泄漏有关,而常规的小试样研究方法无法反映接头的真实腐蚀行为;第三,该系统将全尺寸(Full-scale)与小试样(Small-scale)方法有机结合在一起,考虑到小试样研究的方便性,在全尺寸管柱内设计了小试样挂样系统。
“全尺寸石油管高温高压实物拉伸应力腐蚀系统”,如图6 所示,主要用于测试全尺寸油管和套管柱在复杂苛刻服役工况环境下的腐蚀、应力腐蚀开裂、接头密封失效,具体参数为:最大内压为100MPa、最高温度为200℃、最大轴向拉力700 吨、最长管段为12m、最长连续工作时间720 小时,介质包括浓酸溶液、浓碱溶液、浓盐溶液、CO2 和H2S等腐蚀性气体等。全尺寸实物管材腐蚀试验系统在一年的投用时间内,已成功为塔里木油田公司超13Cr 油管、西南油气田公司耐蚀合金油管、中海油非金属管线进行了研究和评价实验。
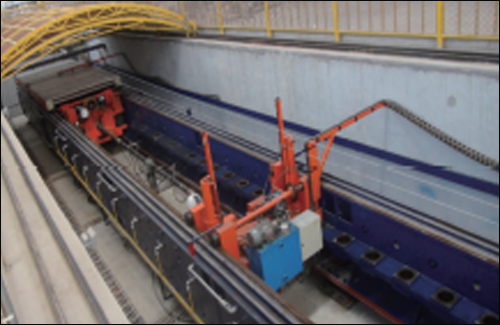
图6 全尺寸石油管高温高压实物拉伸应力腐蚀系统
全尺寸实物管柱腐蚀评价研究案
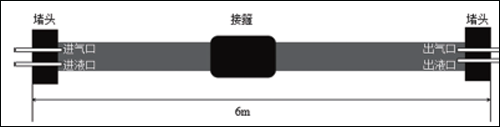
图7 全尺寸超级13Cr油管实验连接示意图
高压气井经过酸化压裂后返排的残酸,即鲜酸(10%HCl + 1.5%HF + 3%HAc+ 5.1%TG201 缓蚀剂)与碳酸盐地层作用后的反应产物,本实验所用残酸液取自油田现场,其pH 值在2.7 左右。
1.超级13Cr油管断裂部位断口表征
图8 和图9 分别为管柱发生断裂后的宏观照片和微观形貌。从图8(b)可以看出管柱断裂有明显的三个区域,其中区域A 为裂纹源区,有两个半圆形的灰黑色区域,放大后如图8(c)所示,初步判断起裂源是油管内壁的两个腐蚀坑,图9(a)的微观形貌可证明确实存在腐蚀产物,该断裂为典型的沿晶断裂,图9(a)的微观形貌表明是典型的韧窝状韧性断裂;区域C 为瞬断区,从图9(a)可以看出管柱在该区域发生了一定的颈缩后然后断裂,图9(c)显示微观形貌为韧窝状。基于以上分析,可以推断油管断裂起源于内壁的腐蚀坑(区域A),在管柱内压及外拉力的共同作用下,油管从区域A 内壁起裂,然后迅速扩展到区域B,最终扩张到C 区发生完全断裂。
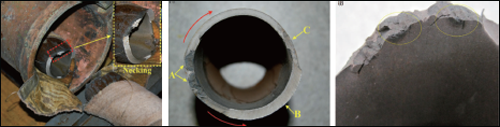
图8 全尺寸13Cr油管已断部位断口宏观形貌
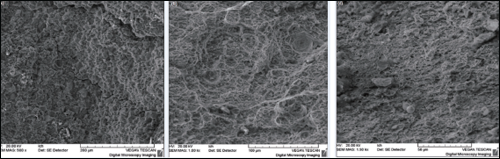
图9 全尺寸13Cr油管已断部位断口微观形貌
(a、裂纹源区;b、裂纹扩展区;c、瞬断区)
2.超级13Cr油管内表面腐蚀坑及裂纹形成过程
(1)腐蚀坑特征
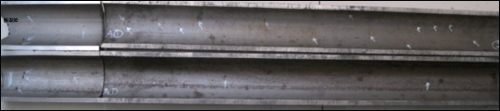
图10 全尺寸13Cr油管内壁腐蚀坑宏观形貌(靠近断裂处)
全尺寸13Cr 油管内壁腐蚀坑宏观形貌如图10 所示,在靠近断裂位置的75cm 管段范围内有宏观可见腐蚀坑25个,对腐蚀坑进行微观观察,发现大部分腐蚀坑周围已出现了“X”状的裂纹,这些裂纹均以腐蚀坑为中心,以“X”
状向四个方向扩展,部分裂纹在扩展的过程中出现了二次裂纹形貌,如图11所示。

图11 全尺寸13Cr油管内壁腐蚀坑微观形貌
(2)腐蚀坑到裂纹发展过程如前所述,被测试的超级13Cr 全尺寸管柱经历了高温—高内压—高拉应力—高腐蚀性残酸的交互作用,毫无疑问,以上四个关键因素必将导致13Cr 管柱内壁发生腐蚀,随着测试时间的推移甚至进而发生开裂。结合实验及测试结果将油管内壁腐蚀—点蚀—裂纹—断裂的整个过程分为如下五个过程,如图12所示。
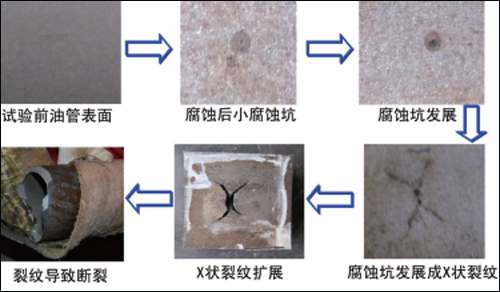
图12 全尺寸13Cr油管内壁腐蚀坑-裂纹-断裂发展过程
3.超级13Cr油管力学性能
表征为了考察管柱在经历高温—高内压—高拉应力—高腐蚀性残酸多因素交互作用后的力学性能,对实验后的管柱和未使用的新管柱进行了屈服强度、断裂强度、断后伸长率、冲击功等力学性能测试,同时选取了塔里木油田现场某口井失效的超级13Cr 油管进行了同上的测试,以比较实验室全尺寸腐蚀测试后管柱和现场失效管柱力学性能的差异性。从表1 中可以看出,无论是全尺寸测试后管柱还是现场失效管柱,其力学性能都满足API Spec 5CT 的要求,全尺寸测试后管柱和现场失效管柱的屈服强度及抗拉强度相对于新管柱变化较小均在10MPa 以内,断后伸长率基本相同,冲击功方面,全尺寸测试后管柱和现场失效管柱明显低于新管柱。通过对比全尺寸测试后管柱和现场失效管柱的力学性能参数,基本非常接近,印证了采用全尺寸石油管高温高压实物拉伸应力腐蚀系统可以模拟井下油管的服役行为。

4.超级13Cr油管接头螺纹表征
根据油田现场统计表明约有50%左右的管柱失效与接头密封泄漏有关,因此,本研究对实验测试后的超级13Cr油管接头进行了分析,如图13 所示。
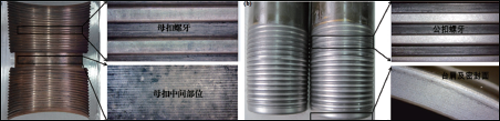
图1 3 全尺寸13Cr油管螺纹( 公母扣)形貌
从本实验的测试结果来看,母扣螺牙、母口中间部位、公扣螺牙、公扣密封面、公扣台肩面均为发现有腐蚀痕迹,可见在实验过程中油管接头未发生密封泄漏,密封性能良好。
结语
随着人类对天然气能源需求的与日俱增,石油管材及装备面临着前所未有的高温、高压、高含H2S/CO2、交变载荷、高流速、复杂作业工艺等苛刻服役环境带来的腐蚀难题,亟待系统研究腐蚀机理和相应的防腐技术。石油管工程技术研究院腐蚀与防护研究团队将以石油管材及装备材料服役行为与结构安全国家重点实验室建设为契机,在现有实验装备的基础上,逐步引进超高温高压应力腐蚀实验装备、在线实时微区腐蚀研究装备、大型多相流腐蚀模拟及预测软件,同时进一步加强自研全尺寸腐蚀装备的开发和功能升级。
责任编辑:班英飞
《中国腐蚀与防护网电子期刊》征订启事
投稿联系:编辑部
电话:010-62313558-801
邮箱:ecorr_org@163.com
中国腐蚀与防护网官方 QQ群:140808414
免责声明:本网站所转载的文字、图片与视频资料版权归原创作者所有,如果涉及侵权,请第一时间联系本网删除。
相关文章
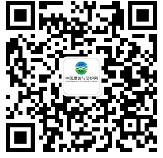
官方微信
《腐蚀与防护网电子期刊》征订启事
- 投稿联系:编辑部
- 电话:010-62316606-806
- 邮箱:fsfhzy666@163.com
- 腐蚀与防护网官方QQ群:140808414
点击排行
PPT新闻
“海洋金属”——钛合金在舰船的
点击数:8135
腐蚀与“海上丝绸之路”
点击数:6475