一、薄带铸轧微合金高强钢中团簇诱导的强塑机制
薄带铸轧流程简约高效,是双碳背景下钢铁工业实现节能减排目标的重要手段。微合金高强钢是制造业重要的钢铁材料,传统长流程生产的微合金高强钢中要达到最佳析出强化效果需要高浓度的碳化物形成元素和复杂的热处理工艺,大幅提高生产成本的同时增加了二氧化碳排放量。薄带铸轧技术的快速凝固速度和单道次热轧允许微合金溶质在奥氏体中保持过饱和固溶状态,使在后期卷取过程(相变)中引入团簇强韧化机制成为可能。本文章主要报道了在薄带铸轧含Nb微合金高强钢中的团簇诱导强塑机制方面的新研究进展,Nb-N富集团簇形态和分布状态的调控对微合金高强钢的强韧化作用,多原子层团簇与位错的动态相互作用,及其在薄带铸轧先进高强钢开发中的潜在应用。
薄带铸轧流程简约高效,能源消耗和二氧化碳排放量仅为传统连续热连轧工艺的10%和16%,是双碳背景下钢铁工业实现节能减排的重要手段。微合金高强钢是制造业重要的材料,传统长流程生产的微合金高强钢(HSLA)中要达到最佳析出强化效果需要高浓度的碳化物形成元素(如Nb、V和Ti等)和复杂的热加工工艺,提高生产成本的同时极大地增加了二氧化碳排放量。薄带铸轧工艺的快速凝固速度和单道次热轧工艺使微合金元素在奥氏体中保持过饱和固溶状态,为随后的γ→α相变过程中引入溶质团簇强化机制提供了有利条件,可在节约能源消耗的同时节省微合金元素的添加量。
在本工作中,我们通过利用薄带铸轧亚快速凝固、低压下量轧制的工艺特点,通过调控卷取温度,在薄带铸轧含铌微合金钢中成功引入了界面和随机分布型的多原子层团簇,并显著提升了材料的机械性能,其中650℃卷取的团簇强化型铁素体样品在与480℃卷取的无团簇贝氏体样品相比,机械性能显著提高,抗拉强度从630 MPa增加到670 MPa,延展性增加了近90%(从10.3%增加到19.1%)。借由球差扫描透射电子显微镜、三维原子探针层析以及透射电镜下的原位力学测试设备的协同表征,发现这些多原子层微合金富氮团簇在调整材料位错滑移行为方面发挥了关键作用,促进位错局部双交滑移的同时,显著增强了位错增殖和位错的均匀分布,这些机制相互配合,共同保持了较高应变量条件下的加工硬化率,从而同时提高了强度和延展性。该研究成果拓展了薄带铸轧微合金高强钢中的团簇诱导强塑机制,揭示了薄带铸轧HSLA中团簇状态、分布模式及其与位错的动态相互作用关系,明确了团簇强塑化机制在薄带铸轧先进高强钢开发中的潜在应用,同时揭示了薄带铸轧技术在制备低成本高性能微合金高强钢方面的显著优势。
相关研究成果以“Cluster mediated high strength and large ductility in a strip casting micro-alloyed steel”发表Acta Materialia上。第一作者: 黄禹赫许帅。通讯作者: 高军恒研究员, 赵海涛研究员, 汪水泽研究员, 毛新平院士。通讯单位:北京科技大学碳中和研究院,辽宁材料实验室钢铁再生技术研究所。
全文链接:
https://doi.org/10.1016/j.actamat.2024.120102
图1. 拉伸性能。(a) Nb-480、Nb-620和Nb-650的应力-应变曲线。屈服强度 (σy)、极限强度 (σUTS) 和均匀伸长率 (ε) 分别由方形和菱形表示。(b) 相应的加工硬化响应 (dσ/dε)。值得注意的是,Nb-650表现出较高的加工硬化率和更显著的加工硬化行为。
图2. Nb-650钢中多原子层团簇的精细显微组织表征。(a) 铁素体的TEM明场图像。插图是沿 [100]α晶带轴拍摄的选区电子衍射图案 (SADP)。(b)团簇的暗场图像。用于暗场成像的衍射点在中由(a)中的黄色圆圈突出显示。(c) 团簇的HR-HAADF-STEM图像和相应的FFT图。(d)富Nb、N的团簇由初始状态演化到NbN纳米析出物的示意图,显示了涉及不同氮原子占据量的衍射图样演化趋势。
图3. Nb-650试样内团簇的原子探针断层扫描(3D-APT)。(a) Nb-650中溶质原子分布。(b) 和 (c) 分别展示了具有1 at%特征元素组成等浓度面的随机分布和相界分布型团簇,及随机分布和相界分布型团簇及基体界面处的平均化学成分变化情况。
图4. Nb-650中位错构型的TEM观察。(a) 在2%应变下,位错多呈平面滑移模式。(b) 在8%应变下,发现了一系列位错特征,包括位错环 (红箭头指示)、位错偶极子 (白箭头突出) 和位错钉扎点 (黄色箭头标示)。(c) 在断裂试样中,位错亚结构显示出主要由高密度位错偶极子组成的偶极墙的存在。
图5.由团簇的钉扎效应引起的位错双交滑移。(a) 位错1和2 (白色虚线突出) 在同一路径上滑移。(b) 滑移的位错2被两个障碍物钉扎,白色箭头突出显示处。(c) 对于位错2 (白色箭头突出显示的中点),观察到强的钉扎效应,同时一个位错环即将形成(红色虚线)。(d) 在位错1和2的滑移面上观察到位错增殖,形成了新的位错3和4。(e) 示意图显示团簇-位错交互引起的的双交滑移增强了位错增殖。
图6. Nb-650合金中滑移痕迹形貌分析。(a) 在2%应变水平的变形下,滑移痕迹主要沿直线排列 (白色虚线和白色箭头指示)。(b) 在5%应变时,滑移痕迹表现出直线和波状图案的组合 (黄色箭头强调)。(c) 进一步进展到10%应变时,波状滑移线的存在增加。(d) 在15%应变时,除了与不同滑移系统相关的直滑移痕迹 (左上角白色虚线标示) 外,还观察到波状滑移痕迹的增多,特别是由大量波状滑移线 (黄色框区域包围) 标示的。
本研究系统地探讨了富溶质团簇的形成机制及其在提升薄带铸轧微合金高强钢强度和延展性方面的作用。作为富含铌和氮的GP型团簇,这些多原子层团簇与铁素体基体完全共格,并在卷取过程中由于铌原子的受限扩散而表现出高热稳定性。对Nb-650变形结构的分析显示,塑性变形初期以平面滑移为主。随着应力和应变的增加,频繁的位错-团簇相互作用诱导并促使交滑移成为主要机制。原位TEM观察动态地揭示了富溶质多原子层团簇和位错在机械载荷下的相互作用。多原子层团簇在塑性变形过程中促进了位错钉扎、交滑移和局部双交滑移,帮助位错增殖和均匀分布,延缓局部应力峰值,增强了加工硬化和延展性。多原子层簇与位错之间相互关系的揭示,有助于深入理解其对微合金高强钢机械性能的影响,对推动基于薄带铸轧技术开发新型低成本高性能且环境友好的团簇强化型微合金高强钢起到很大助力。
二、高强塑低锰含量中锰钢非均质结构调控及强塑化机制研究
中锰钢(3-12 wt. % Mn)通过残余奥氏体的相变诱导塑性(TRIP)效应展现出优异的强塑性。然而,为了实现锰原子向奥氏体内的配分以提升残余奥氏体的热稳定性,需要进行长时间的临界区退火。此外,中锰钢的高锰含量也导致了其它问题,如成本增加、焊接等问题。不同于调控残余奥氏体以提升中锰钢强塑性的传统思路,本研究通过传统的轧制和短时临界区退火工艺,在低锰含量的中锰钢 (3 wt. % Mn) 中设计了一种新型异质结构,该结构由交替分布的带状马氏体区和带状超细晶双相区(马氏体+铁素体)组成。异质结构的形成归因于锰的带状分布(富锰区对应马氏体区,贫锰区对应超细晶双相区)、初始组织内高度分散的马氏体-奥氏体(MA)岛(临界区退火过程中作为逆转变奥氏体的有效形核位点)以及临界区退火过程中锰原子的低扩散速率(抑制晶粒长大并促进超细晶结构的形成)。拉伸试验结果表明实验钢展现出优异的强塑性(拉伸强度1452 MPa,总延伸率17%)和优异的加工硬化能力。优异的加工硬化能力和延伸率主要归因于带状马氏体区和超细晶双相区之间明显的硬度差异,这引起了强烈的异构强化效应(HDI)。本研究提出了一种开发高性能钢材的新方法,为解决中锰钢在机械性能、高锰含量和临界区退火时间长之间长期存在的矛盾提供了一个有效的范例。
作为最具代表性的先进高强度钢之一,中锰钢(3-12 wt. % Mn)因其优化的组织结构和优异的力学性能而被广泛研究。中锰钢为了优化残余奥氏体的稳定性获得持续的应力诱导相变效应(TRIP),不可避免地需要长时间的临界区退火(最长可达24小时)。过长的临界区退火时间使现有生产线难以实现中锰钢的工业化生产。此外,高锰含量及钒、钼、铝等合金元素的添加不仅增加了成本,还加剧了中锰钢的可焊性和铸造性等问题。因此,制备出具有高强度和高延伸率且易于规模化生产的中锰钢仍然具有很大的挑战。
为了最大限度地发挥TRIP效应对力学性能的贡献,奥氏体逆转变机制受到了广泛的关注。研究表明,由于碳和锰的扩散速率不同,奥氏体的逆转变过程主要分为两个阶段。具体来说,逆转变奥氏体的形成始于由快速碳扩散控制的快速生长期,这一阶段在几秒钟内完成,随后是由锰扩散控制的较慢生长期。因此,将退火时间缩短到几十秒对于实现大量锰分配到逆转变奥氏体中以优化其力学稳定性是具有挑战性的。此外,低锰含量的逆转变奥氏体在随后的冷却过程中或在塑性变形的早期阶段容易转变为新鲜马氏体,这不可避免地削弱了TRIP效应对力学性能的贡献。因此,为了有效利用残余奥氏体的TRIP效应,长时间的临界区退火是必不可少的,尽管这使中锰钢的工业化生产变得极具挑战性。
在中锰钢中,沿轧制方向经常能观察到锰偏析带,即使经过长时间的高温均质化处理,这些偏析带也很难被消除。偏析带通常会削弱材料的各向异性并降低力学性能的可预测性,最终降低材料在应用中的可靠性。近年来,不同于传统的消除偏析带的思路,基于偏析带内贫锰区和富锰区的成分差异来设计异质结构进而得到高性能中锰钢已有成功的实践。然而尽管通过引入异质结构可以提高强度和延展性,但这些中锰钢要么含有高锰含量,要么需要长时间的临界区退火,这些都是阻碍中锰钢规模化应用的障碍。
在本研究中,我们基于中锰钢中的不均匀锰分布以及新颖的合金成分和工艺路线设计,得到了一种由带状马氏体和超细双相结构组成的非均质中锰钢。这种具有非均质结构的中锰钢不仅具有比传统中锰钢更高的强度和相当的延展性,而且锰含量更低(3 wt. %)且临界区退火时间更短(8分钟)。通过对在不同热处理阶段的显微组织进行表征和分析,揭示了这种非均质结构的形成机制。通过维氏硬度试验和循环加载试验,揭示了这种新型中锰钢的强化机制。
相关研究成果以“Heterostructure mediated high strength and large ductility in novel medium-Mn steels with low Mn content”发表Acta Materialia上。第一作者: 朱晴。通讯作者: 高军恒研究员,汪水泽研究员。通讯单位:北京科技大学碳中和研究院,辽宁材料实验室钢铁再生技术研究所。
全文链接:
https://doi.org/10.1016/j.actamat.2024.120092
图1. IA和I-IA的工艺路线图
图 2. HR 样品的显微组织分析。(a) SEM 和TEM 图像,白色虚线突出显示了贝氏体区和马氏体区的分布特征。θ 表示渗碳体,α表示铁素体/马氏体,γ表示奥氏体。(b) EBSD 相分布图证明了渗碳体的形成。HAGB 表示晶界取向差大于 15°,而LAGB 表示晶界取向差在 5°-15° 范围内。(c) EPMA 锰分布图。
图 3. IA 样品的显微组织分析。(a) SEM 图像,白色虚线突出了超细晶双相区和块状区的分布特征。(b) IA 样品中铁素体和马氏体的晶粒尺寸分布。插图显示了块状区多边形铁素体的晶粒尺寸分布。(c) EPMA 锰分布图。 (d) 和(e)分别为块状区和超细双相区中粗大铁素体晶粒的亮场TEM 图像。插图显示了 (d) 中灰色圆圈标记区域的选区电子衍射图案。
图 4. I-IA 样品的显微组织分析。(a) SEM 图像,白色虚线突出显示了沿轧制方向交替分布的层状马氏体区和层状超细双相区。(b) 超细双相区内铁素体和马氏体的晶粒尺寸分布。(c) EPMA 锰分布图。(d) 超细双相区的TEM亮场图像。
图 5. IA 和 I-IA 样品的力学性能。(a) 室温工程应力-应变曲线。(b) 相应的真实应力-应变曲线及加工硬化率曲线。
图 6.贫锰区和富锰区在轧制和退火过程中的显微组织演变示意图。
图 7.在 720 °C 下进行 8 分钟临界区退火过程中奥氏体逆转变的Dictra模拟。(a) 模拟中使用的扩散偶示意图。(b) 随退火时间变化的奥氏体体积分数,红点表示测量的逆转变奥氏体/马氏体的体积分数。(c-d) 在 0.001 秒、1 秒、480 秒和 100,000 秒时锰和碳浓度分布情况。
图 8. IA 和 I-IA 合金的包辛格效应和背应力强化贡献。(a)循环加载试验得到的真应力应变。(b) 不同真应变对应的IA和I-IA的背应力。
本文设计了一种具有层状异质结构和相对较低锰含量的新型高性能中锰钢。详细地讨论了层状异质结构的形成机制和 I-IA 合金的强化机制。主要结论如下:
-
通过常规轧制和短时间临界区退火工艺,在 I-IA 合金中构建了由层状马氏体区和层状超细双相区组成的新型异质结构,表现出1452 MPa 的高极限抗拉强度和 17% 的高延伸率的结合。
-
对于 I-IA 合金,层状马氏体区的形成归因于较高的锰含量以及富锰区缺乏有效的逆转变奥氏体形核位点,而超细晶双相区的形成则归因于 I-HR 样品贫锰区中高度分散的 MA 岛的形成,这些 MA 岛成为逆转变奥氏体的优先形核位点,同时锰原子的低扩散速率限制了临界区退火温度下相界面的迁移。
-
与 IA 合金相比,I-IA 合金具有更高的屈服强度和极限抗拉强度、更大的延展性和更强的加工硬化能力,这归因于其独特的层状组织特征:层状马氏体区的形成、层状超细双相区中更细小的等轴马氏体和铁素体晶粒、更薄的层片厚度,以及层状马氏体区和超细双相区之间更大的显微硬度差异和更清晰的界面。
免责声明:本网站所转载的文字、图片与视频资料版权归原创作者所有,如果涉及侵权,请第一时间联系本网删除。
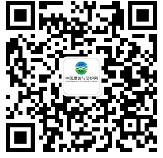
官方微信
《腐蚀与防护网电子期刊》征订启事
- 投稿联系:编辑部
- 电话:010-62316606
- 邮箱:fsfhzy666@163.com
- 腐蚀与防护网官方QQ群:140808414