激光—电解整体制造技术,可实现金属高性能、大型、复杂结构的高效率、低成本、精确成形,在航空发动机制造中应用前景广阔。然而,电解加工过程中,过渡金属试件表面所形成的超钝化膜一旦发生局部破坏,便会诱导选择性溶解进而降低电解加工质量,这在激光增材制造过渡金属构件中表现得尤为突出。需要指出的是,自上世纪七十年代以来,尽管研究者们对超钝化膜进行了一定数量的研究,但是对该膜的定义尚未达成一致(如“阳极膜”、“氧化膜”、“腐蚀产物膜”以及“钝化膜”),这意味着人们对超钝化膜形成机理仍然缺乏准确的理解;针对电解加工过程中超钝化膜的失效,人们普遍认为这是由高速流动的电解液对超钝化膜的冲刷作用所致,而对金属微观组织以及膜内点缺陷的诱导机制尚不明确。
近日,青岛理工大学、西北工业大学以及加州大学伯克利分校等开展联合研究,基于点缺陷模型(PDM)理论,采用FIB-SEM双束系统和高分辨TEM对激光增材制造镍基高温合金表面超钝化膜进行观察分析,探究了超钝化膜的形成过程,阐明了“二次钝化”诱导超钝化膜的形成本质(因此,二次钝化膜即为超钝化膜);同时基于金属微观组织特征及点缺陷模型理论,揭示了超钝化膜的失效是由Nb偏析区表面膜的自诱导开裂、流体流动剪切应力引起的膜侵蚀降解以及金属阳离子空位在金属/膜界面凝结导致两者脱粘等共同作用所致。相关工作以“Unveiling the transpassive film failure of 3D printing transition alloys”为题发表在《Corrosion Science》上。该研究青岛理工大学郭鹏飞副教授为第一作者,西北工业大学林鑫教授与加州大学伯克利分校D.D. Macdonald教授为通讯作者。
论文链接:https://doi.org/10.1016/j.corsci.2022.110412
根据点缺陷模型(PDM)理论,含Cr合金表面钝化膜(primary passive film)通常被视为含有Ni、Fe和Cr的间隙取代基的点缺陷Cr2+xO3-y。因此,在沉积态718合金上形成的钝化膜晶体框架是Cr2O3,其他合金元素替换阳离子亚晶格上的Cr原子(如Mo),或者作为间隙原子出现在钝化膜中(如Fe、Ni)。进入超钝化区后,Cr(III)氧化为Cr(VI)[],此时钝化膜破坏,同时表面会立即形成另外几种氧化物(如Ni2O3),如图1所示。当反应产物扩散速率较慢时,氢氧化物或羟基氧化物会附着在氧化物表面,形成外层。这种氧化物(内层)以及氢氧化物(外层)在金属表面的形成直接导致了“二次钝化(secondary passivation)”,极化曲线中的二次钝化区(图2)可以很好的证明这样一点。需要说明的是,通过阳极反应产物的吸附或者沉淀形成超钝化膜的观点是没有根据的,因为在流动电解液的作用下,电流密度为40A/cm2时,仍没有达到极限扩散电流密度(见Supplementary materials),即传质过程不是阳极溶解的速率控制步骤。
图1 电流密度为2A/cm2时,超钝化膜的(A)原子细节图以及(B)金属与(C)超钝化膜的衍射斑
图2 沉积态Inconel 718合金在NaNO3水溶液中的动电位极化曲线
微观组织特征中的偏析行为诱导各微区表面二次钝化膜氧化物组成、晶格结构等的差异(如γ相和Nb偏析区表面),这势必使得超钝化膜向金属一侧的迁移速率以及超钝化膜在溶液一侧的溶解速率存在显著不同,两相表面膜/膜界面逐渐脱粘,并最终导致超钝化膜的开裂(如图3A和图4A);高速流动的电解液对超钝化膜的冲刷作用所诱导的金属/膜界面剪切力,亦会诱导膜的破裂失效。另外,在如此高的外加电压下,膜/溶液界面处的界面反应(4)[如图5]的反应速率极快,产生的大量金属阳离子空位不断向金属/膜界面处移动,考虑到金属/膜界面处界面反应(1)不具备电压依赖性,因此,未湮灭的金属阳离子空位在金属/膜界面处凝结(超钝化膜中的氧分布可以印证,如图4C所示),最终使得超钝化膜与金属脱粘,促进膜的破裂。当电流密度达到20 A/cm2时,超钝化膜已经局部破裂(如图4B所示)。
图3 电流密度为2A/cm2时,超钝化膜的(A)上表面形貌和(B)剖面形貌以及(C)元素分布
图4 电流密度为20A/cm2时,超钝化膜的(A)上表面和(B)剖面形貌及在超钝化膜剖面上(C)元素分布
基于超钝化溶解实验以及PDM,最终建立了过渡金属/二次钝化膜/溶液界面处的界面反应原理图(如图5所示)。本研究厘清了电解加工过程中过渡金属或合金表面超钝化膜的形成本质,揭示了超钝化膜的失效机制,可极大促进激光—电解整体制造技术的发展。
图5 基于点缺陷模型的金属/二次钝化膜/溶液界面处的界面反应示意图
免责声明:本网站所转载的文字、图片与视频资料版权归原创作者所有,如果涉及侵权,请第一时间联系本网删除。
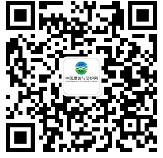
官方微信
《腐蚀与防护网电子期刊》征订启事
- 投稿联系:编辑部
- 电话:010-62316606-806
- 邮箱:fsfhzy666@163.com
- 腐蚀与防护网官方QQ群:140808414