导读:本文通过涂层与基体的相互作用,研究了涂层对钛合金疲劳性能的影响。结果表明:具有较高硬度和断裂韧性的TiN/AlN超晶格涂层抑制了表面应变局部化,改变了疲劳裂纹萌生位置,使107次循环疲劳强度提高了23.7%。位错重分布和“二次滑移”在钛合金中被发现,其目的是消除应力集中。
钛合金因其优良的比强度和耐高温性等优点被广泛应用于燃气轮机压气机部件中。然而,由于吸入外来颗粒进入涡轮发动机,叶片等钛合金压缩机部件的冲蚀磨损可能会导致严重的问题。保护涂层的应用是提高钛合金抗冲蚀性和抗氧化性的有效途径。为了改善钛合金的表面性能,各种涂层,如搪瓷涂层、铝涂层和氮化涂层被投入使用。涂层性能的不同,对钛合金疲劳性能的影响也不同。多项研究表明,高硬度涂层在不同程度上降低了金属材料的疲劳极限,这已远远超出了应用的可接受范围。因此,研究硬质涂层对钛合金疲劳性能的影响是十分必要的。
已有研究表明,残余应力、硬度和涂层的附着力对金属基体的疲劳性能有重要影响。目前已有少量研究表明,陶瓷涂层可以提高钛合金的疲劳极限,这是由涂层的硬度和附着力决定的。根据这些解释,涂层不会改变疲劳裂纹的萌生位置,但会抑制循环加载过程中表面形貌的发展,延缓疲劳裂纹的萌生。然而,基于这些解释,一些实验现象并不能被理解。虽然硬质涂层抑制了金属的塑性变形和滑动,但涂层的早期开裂仍然降低了疲劳极限。较强韧性的硬涂层可防止滑带向表面断裂,并能承受表面皱折,避免膜破裂。因此,可以减轻对基体疲劳寿命的负面影响。这意味着,要获得最佳的抗疲劳裂纹起裂性能,需要包括硬度和韧性在内的综合性能。由两种双向层周期在纳米范围内的交替相干材料组成的多层膜称为超晶格膜,已被报道用于提高陶瓷膜的硬度和断裂韧性。超晶格涂层可能对金属基体的疲劳性能有有益的影响。
此外,在涂层和金属基体的界面处,剪切模量变化显著。虽然涂层与基体之间的相互作用会影响基体的性能,但其对金属疲劳性能的影响却很少被研究。涂层与基体的相互作用可以影响晶体中位错结构的发展,增强底层的韧性金属。这种强化机制是由像力引起的近程相互作用和塑性约束引起的远程相互作用引起的。涂层与基体的弹性模量差越大,相互作用越强。这项研究调查了超晶格涂层对金属基体疲劳行为的影响。
在本研究中,北京科技大学庞晓露教授团队利用交替氮化钛和氮化铝沉积在钛合金基体上,总厚度为1μm。由于TiN和AlN界面处于共格态,因此下文将该涂层称为TiN/AlN超晶格涂层或TiN/AlN涂层。为了进行比较,在钛合金基体上沉积了相同厚度的氮化钛(称为镀TiN)。测试了TiN/AlN涂层和TiN涂层的力学性能,并对涂层和无涂层样品进行了拉伸轴向疲劳试验。观察了试样表面和断口形貌,研究了位错密度分布。结果表明,TiN涂层和TiN / AlN超晶格涂层沉积在钛合金上。研究了未涂层和涂层钛合金的疲劳行为。TiN/AlN涂层样品的疲劳性能显著提高。这种改进是由于超晶格涂层的硬度和韧性。涂层-基材相互作用影响位错分布。相关研究成果以题为Significant improvement in fatigue life of titanium alloy induced by superlattice coating发表在International Journal of Fatigue上。
链接:https://doi.org/10.1016/j.ijfatigue.2022.107367
本研究的基底材料为钛合金。在膜沉积之前,基板与无涂层的钛合金处理相同。本研究选择了两种涂层,即TiN涂层和TiN/AlN超晶格涂层。以Ti为靶材,采用直流电沉积法在基体上制备了纯度为99.995%的TiN涂层。将基板在丙酮和乙醇中超声清洗10分钟。用于沉积的TiN和AlN层在一个双分子层周期内的厚度分别为4 nm和1.5 nm。在厚度为1 μm的钛合金基体上沉积了TiN/AlN超晶格涂层。
基体微观结构为α + β两相均匀结构,如图2a所示,晶粒尺寸约为20 μm。组织由等轴α相和少量β相组成。结果表明,α相和β相的体积分数分别为94%和6%。岛状转化β随机分布在等轴α晶粒中,具有较高的力学性能。双相钛合金的应力演化主要由初生α相(αp)控制,αp一般比β相更软。在这种两相合金中,疲劳裂纹的形核可能发生在αp。
图2(a)钛合金的扫描电镜显微图 (b)钛合金衬底、TiN膜和TiN/AlN超晶格膜的XRD图 (c) TEM横断面形貌 (d)超晶格薄膜的HRTEM图像截面形貌及相应的FFT图像
用XRD对衬底、TiN膜和TiN/AlN膜的结构进行了研究,结果如图2b所示。结果表明,薄膜存在于面心立方晶体结构中。衍射峰的位置与TiN峰的位置基本一致,表明AlN相在立方相中是稳定的。多层涂层的TEM图像显示1.5 nm厚的AlN层和4 nm厚的TiN层(图2c)。图2d为高分辨率透射电子显微镜(HRTEM)观察到的薄膜截面和相应的快速傅里叶变换(FFT)图像。结果进一步表明,AlN稳定在亚稳立方(c-AlN)中,而不是稳定的纤锌矿结构(w-AlN)中。
钛合金、TiN涂层和TiN/AlN涂层的弹性模量和硬度如图3所示。TiN涂层的硬度和模量分别为26 GPa和310.1 GPa, TiN/AlN涂层的硬度和模量分别为35.2 GPa和345.1 GPa。结果表明,TiN/AlN超晶格涂层的硬度(H)和模量(E)均较TiN涂层好。基于上述结果,TiN和TiN/AlN涂层的H3/E2比值分别为0.36和0.183。这表明TiN/AlN超晶格涂层比TiN涂层具有更高的抗塑性变形能力。
图3 钛合金、TiN涂层和TiN/AlN涂层的弹性模量和硬度。
由于c-AlN(晶格参数ac - AlN = 0.406 nm)和TiN(晶格参数aTiN = 0.424 nm)的晶格不匹配,导致超晶格涂层在界面附近产生不同的应力状态。随着TiN和AlN层裂纹扩展,不同的应力状态有助于降低裂纹扩展速率。另外,在涂层开裂过程中,c-AlN向w-AlN转化,比体积增大。裂纹自由表面的增加可以通过吸收能量来影响裂纹的扩展。综上所述,超晶格结构可以提高涂层的韧性。
图4为无涂层和涂层钛合金的最大应力-载荷循环曲线。结果表明,涂层材料的高周疲劳性能优于无涂层材料。在高应力幅下,TiN涂层试样比无涂层试样更早破坏,这可能是由于涂层的早期脆性开裂。随着应力的降低,TiN涂层对基体的疲劳性能有积极的影响。而镀TiN/AlN超晶格薄膜的试样的疲劳强度明显提高。这说明涂层的性能对钛合金基体的疲劳性能有很大的影响。
图4 无涂层钛合金、TiN涂层试样和TiN/AlN涂层试样的S-N曲线。疲劳极限分别为475 MPa、500 MPa和587.5 MPa。
图5 在相同应力幅值下,无涂层钛合金、TiN涂层试样和TiN/AlN涂层试样的循环变形曲线。
为保证涂层对钛合金疲劳裂纹萌生位置的有效性,计算了不同应力下涂层和无涂层试件的疲劳裂纹源位置。如图6d所示,无涂层试样的裂纹源位于表面,TiN涂层试样的裂纹源位于界面附近,TiN/AlN涂层试样的裂纹源位于衬底内部。根据无涂层和涂层钛合金的疲劳断口形貌,证明TiN/AlN超晶格膜影响疲劳裂纹萌生机制。
图6 循环应力(650 MPa)下的疲劳断裂形貌:(a)为无涂层钛合金,(b)为TiN涂层钛合金,(c)为TiN/AlN涂层钛合金。(d)疲劳裂纹萌生位置与表面之间的距离。
通过观察无涂层试样、TiN涂层试样和TiN/AlN涂层试样疲劳后的表面形貌,研究了涂层对疲劳裂纹萌生的影响。在无涂层试样断口附近的表面,出现了清晰的滑移带(图7a)。TiN涂层试样和TiN/AlN涂层试样表面相对光滑(图7e和f),但TiN涂层试样表面出现裂纹(图7b)。共焦激光扫描显微镜(样品形貌)在图7 d的观察表明,裸样品的表面粗糙度为1.2μm,这是一个数量级大于大型表面粗糙度(?300海里)锡涂层和锡/ AlN涂层样品由于循环荷载(图7 e和f)。由于表面粗糙度是一个关键因素在疲劳裂纹成核和传播,锡的光滑的表面涂层和锡/涂层样品不容易形成微裂纹。
图7 无涂层试样(a, d)、TiN涂层试样(b, e)和TiN/AlN涂层试样(c, f)在650 MPa疲劳后的表面形貌。(a-c) SEM, (d-f) CLSM。
在无涂层的疲劳试样中,表面滑移带导致应力集中并形成疲劳裂纹(图6a和图7a和d)。对于TiN/AlN涂层试样,表面应变局部化被显著抑制,疲劳裂纹在钛合金内部形成(图6c和d),这消耗了更多的疲劳寿命。对于TiN涂层样品,虽然涂层抑制了表面粗糙,但在涂层与亚表面滑移带相互作用的地方发生了裂纹,这也影响了钛合金[20]的疲劳寿命。如上所述,涂层的韧性也是影响钛合金疲劳性能的重要因素之一。
图8 核平均取向偏差(KAM)沿深度分布:(a)无涂层钛合金,(b) TiN涂层钛合金,(c) 600 MPa疲劳后的TiN/AlN涂层钛合金。(d)相应的位错沿深度平均分布。
样品平均分为14个区,每个值代表对应区域的位错密度随深度的平均值。不同样品的位错密度分布趋势不同。在近表面,无涂层和TiN涂层样品的位错密度分别约为7.3 × 1014 m?2和8.7 × 1014 m?2。然后,随着与表面距离的增加,它减小。TiN/AlN涂层试样的位错密度在界面附近约为10.9 × 1014 m?2,呈先增大后减小的趋势。矩阵中存在局部最大GND,其位置与疲劳裂纹源位置对应,如图6d所示。
图9 600 MPa疲劳试验后TiN/AlN涂层-基体界面的截面形貌:(a, b)界面位错堆积;(c)界面附近衬底的亮场TEM显微图(插图显示相应的SAED图样);(d, e)和双光束暗场图像和(c)中绿框区域对应。
图10 疲劳断裂机理示意图:(a)无涂层试样,(b) TiN涂层试样,(c) TiN/AlN涂层试样。
总之,在本研究中,在钛合金上沉积了TiN涂层和相同厚度的TiN/AlN超晶格涂层。研究了TiN涂层和TiN/AlN超晶格涂层对钛合金疲劳强度的影响。讨论了涂层性能对裂纹萌生机理的影响。主要结论如下:
(1) AlN在TiN/AlN超晶格多层膜内稳定在亚稳立方(c-AlN)中。TiN涂层的硬度和模量分别为26 GPa和310.1 GPa, TiN/AlN涂层的硬度和模量分别为35.2 GPa和345.1 GPa。超晶格结构提高了涂层的硬度和韧性。TiN/AlN超晶格涂层的力学性能优于TiN涂层。
(2) TiN涂层可以抑制钛合金表面的粗糙化,但由于韧性较差,TiN涂层在循环载荷作用下首先开裂。TiN涂层对钛合金的疲劳强度影响较小。
无涂层试样、TiN涂层试样和TiN/AlN涂层试样的107次循环疲劳强度分别为475 MPa、500 MPa和587.5 MPa。TiN/AlN超晶格涂层抑制了表面应变局部化,抵消了高应力集中,提高了疲劳强度。涂层-基体优异的抗疲劳性能是由于涂层具有优异的力学性能,如高弹性模量、较高的断裂韧性和优异的抗疲劳性能。这些结果突出了涂层力学性能对钛合金循环加载的重要影响,为涂层的设计提供了新的思路。
免责声明:本网站所转载的文字、图片与视频资料版权归原创作者所有,如果涉及侵权,请第一时间联系本网删除。
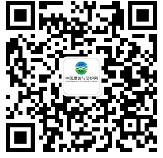
官方微信
《腐蚀与防护网电子期刊》征订启事
- 投稿联系:编辑部
- 电话:010-62316606-806
- 邮箱:fsfhzy666@163.com
- 腐蚀与防护网官方QQ群:140808414