导读:由于其诱人的结构和力学性能,高熵合金(HEAs)和中等熵合金(MEAs)引起了相当大的研究兴趣。具有单一面心立方(FCC)相的HEAs/MEAs的强度需要改进。因此,本研究展示了一种通过温度依赖的层错能调塑性机制调节低温预应变诱导的晶体缺陷来提高fcc相HEAs/MEAs室温强度的策略。由于冷轧引起的高位错密度、机械孪晶和堆垛层错,使等原子CoCrFeNi HEA室温屈服强度从243 MPa提高到941.6 MPa(30%冷轧),提高了约290%,同时保持拉伸延伸率为18%。经热处理部分恢复后,屈服强度和极限抗拉强度略有下降,分别为869和936 MPa。相反,伸长率提高到25.6%。本研究探讨了这种通过预应变诱导晶体缺陷来开发单相高性能HEAs的可能性。
由于其有趣的结构和性质,高熵合金(HEAs)和中熵合金(MEAs)含有等原子或近等原子金属元素,在过去十年中获得了相当多的关注。等原子CoCrFeMnNi、CoCrFeNi和具有单一面心立方(FCC)相的CoCrNi合金是研究最广泛的HEAs/MEAs,这是因为它们在较宽的温度范围内具有特殊的抗拉强度和延展性。通过降低堆垛层错,它们的力学性能得到了进一步的增强能量(SFE),加入间隙原子,调整局部浓度波动,增加晶格畸变,控制化学短程有序。SFE是决定塑性变形机理的关键因素FCC相金属和合金的力学性能。SFE的降低促进了机械孪晶和FCC→密排六方(HCP)马氏体转变,导致强度和延性增加,这是指分别称为孪晶诱导塑性效应和相变诱导塑性效应。然而,无沉淀的HEAs/MEAs往往产量不足的优势。
大量析出增强的HEAs/MEAs已被进一步发展增强其强度。然而,要达到较高的机械性能,需要仔细控制沉淀过程,作为形成异质金属间化合物和/或其他脆性不连贯的析出相显著降低强度和延展性。控制析出形成HEAs/MEAs比稀合金更困难,因为容易与之脆性在多主元素固溶体中形成析出相。随着塑性变形过程中应变的增加,由于形变诱发晶体缺陷的强化/硬化效应。因此,预应变可以用来增加金属的瞬时屈服强度合金。此外,SFE具有显著的温度依赖性在HEAs/MEAs中观察到,随着温度的降低,SFE显著降低。变形温度的下降,降低了SFE,并通过抑制热激活位错恢复来促进缺陷的积累。当SFE降低时,更容易将位错限制在单个滑移面上,从而阻碍了位错的交叉滑移。因此,位错的恢复被抑制,因为恢复需要交叉滑移。低温预应变诱导缺陷可以更有效地提高室温强度。
本文的目的是展示一种通过低温预应变诱导晶体缺陷显著提高无沉淀fcc相HEAs/MEAs室温强度的策略。等原子CoCrFeNi HEA被选为演示该策略的模型合金。低温滚压(CR)被用于引入高密度的缺陷,然后在介质(HT)下进行热处理温度进行微调的微观组织和室温对HEA的拉伸性能进行了研究。随后,使用成熟的中子衍射线剖面分析方法和电子显微镜表征,我们建立了晶体缺陷、微观结构和力学之间的相关性行为。相关研究成果以题“Strengthening of high-entropy alloys via modulation of cryo-pre-straining-induced defects”发表在金属顶刊Journal of Materials Science & Technology上。
链接:
https://doi.org/10.1016/j.jmst.2022.04.055
图1 (a)非原位中子衍射测量的设置,(b) EBSD IPF图显示CR前CoCrFeNi HEA的晶粒结构,(c) CoCrFeNi的中子衍射剖面CR前的HEA, CR后的HEA,以及随后在500、600和700℃高温1h后的HEA。用轴向探测器收集中子衍射剖面,反映微观结构样品沿RD方向的特征。
图1(b)中的EBSD反极图(IPF)图说明了晶粒形态CR前的CoCrFeNi HEA,其中晶粒结构被再结晶。退火孪晶是经常观察到的,如箭头所示。平均晶粒直径为22.4 μm。此外,未观察到明显的织构。CR前、CR后以及随后在500、600和700℃高温下1 h后样品的中子衍射剖面如图1(c)所示。利用中子衍射法确定HEA的晶格参数为0.355 nm。每个样品包含一个FCC相,表明CR和/或HT过程中没有发生相变。在CR之前,样品的中子衍射谱峰相对较低窄,说明缺陷密度低。然而,CR后,由于晶体缺陷的积累,峰变宽。HT后,峰再次变窄,表明Cr诱导的缺陷得到了部分恢复。我们分析和比较了缺陷和织构。
图2所示。CR后CoCrFeNi HEA的EBSD IPF图(a-c)和边界图(d-f) (a,D), 20% (b, e),和30% (c, f)厚度减少。亚晶界的长度分数(2°-5°)、低角度晶界(5°-15°)、高角度晶界(15°-180°)分别为在边界图中插入
图2显示了CR样品的EBSD IPF图(图2(a-c))和边界图(图2(d-f))。平均晶粒尺寸约为20 μm,与CR前的尺寸相当。然而,从插入的图中可以看到,CR后形成了显著的晶粒织构,三个样品沿RD均具有{001}和{111}织构。晶粒被CR塑性变形和扭曲,导致高密度的局部畸变和亚晶界,取向错角为2°-5°。此外,随着CR应变的增加,亚晶界的比例增加(图2 (f))。
图3所示。CoCrFeNi HEA在(a-c) 600℃下CR后和后续HT后1 h的EBSD IPF图谱或(d-f) 700℃1 h。CR菌株分别为10% (a, d), 20% (b, e)和30% (c, f)。
HT样品的晶粒特征通过EBSD IPF图谱如图3所示,图4用边界图表示。600℃高温1 h后,几乎没有变化平均晶粒尺寸保持在20 μm左右,与CR前一致。此外,晶粒织构保持不变,局部扭曲和亚晶界的密集网络被保留(图3(a-c)和图4(a-c))。经过700℃高温处理后,10% CR和20% CR样品的晶粒特征与经过600℃高温处理的样品相似。晶粒尺寸无明显变化,织构较强,晶粒内亚晶界密度较高。而30% CR和700℃高温处理后的样品则表现出一种特征这与其他样本不同。其晶粒尺寸减小到9.2 μm,亚晶界长度分数显著降低。此外,织构也发生了改变。这表明样品中发生了静态再结晶。
图4所示。样品经600℃CR和HT处理1 h (a-c)或700℃处理后的EBSD边界图1 h (d-f),对应于图3中的EBSD IPF图。CR菌株分别为10% (a, d), 20% (b, e)和30% (c, f)。图中显示了2°-5°(红色)、5°-15°(绿色)、15°-180°(蓝色)的定向错角边界的分布。边界图中插入了亚晶界(2°-5°)、低角度晶界(5°-15°)和高角度晶界(15°-180°)的长度分数。
图5所示。(a)叠加故障概率,(b)位错密度,(c)获得的逆极图
从CR前CoCrFeNi HEA中子衍射图的线廓分析,20% CR后,以及在600℃或700℃高温1 h后的20% CR样品。CoCrFeNi HEA的塑性变形机制与温度密切相关。在室温下,变形诱发的位错在小应变下呈波浪状形态,如图6(a)所示;在大应变下,位错缠结和机械孪生发生。随着温度的降低,HEA的SFE迅速降低。当HEA在较低温度下塑性变形时,位错恢复受到抑制,更容易发生机械孪生。如图6(b)所示,在10% CR的样品中形成了纳米孪晶,而在10%室温轧制的样品中没有形成孪晶(图6(a))。由于动态Hall-Petch效应,机械孪生更容易激活,增加了位错的积累。除了纳米孪晶,在图6(b)中还经常观察到位错缠结,这表明位错密度比图6(a)中要大。图6(c)和(d)分别显示了600℃和700℃高温后对应的微观结构,其中大量位错缠结被恢复,位错分布更加均匀。而cr诱导的纳米孪晶则被保留了下来,这表明孪晶在700℃以下是热稳定的。通过阻碍位错运动,保留的位错和纳米孪晶增加了HEA的强度。
图6所示。在(a) 20和(b) -196℃轧制厚度减少10%的CoCrFeNi HEA的TEM亮场(BF)图像。(c) 600℃1 h, (d) 700℃1 h,经10% CR和高温处理后的HEA的TEM BF图像。TEM图像中的白色圆圈显示了获得选定区域衍射图案的区域。
图7所示。(a-e) CoCrFeNi HEAs的室温拉伸性能:(a) CR样品;(b)600℃CR和HT处理1 h后的样品;(c) 700℃CR和HT处理1 h后的样品;(d)屈服强度比较;(e) UTS的比较。(f) CR试样、CR和HT后试样在600℃1 h或700℃1 h的屈服强度增强(△σ)和计算得到的△σd、△σ g、△σsf、△σx。
我们在本研究中展示了一种通过调节cr诱导的晶体缺陷(如位错、sff和纳米孪晶),在室温下显著改善等原子CoCrFeNi HEA的机械性能的策略。力学性能的进一步调整是通过调整的数量和分布来完成的缺陷。晶体缺陷对HEA强度的贡献是用中子衍射线剖面分析和电子显微镜观察定量的。结果表明,cr诱导缺陷有助于强化,同时保持可接受的拉伸延性,这为高性能单fcc相hea的发展提供了见解。例如,CoCrFeNi HEA的室温拉伸屈服强度从243 MPa(再结晶时)提高到941.6 MPa(30%冷轧),同时保持18%的拉伸伸长率。这归因于位错、纳米孪晶和sf的密集分布。收率和抗拉强度分别为869和936 MPa,拉伸伸长率为25.6%。本研究证明了在使用温度以外的温度下通过调整预应变引起的晶体缺陷来开发单相高性能HEAs的可行性。
免责声明:本网站所转载的文字、图片与视频资料版权归原创作者所有,如果涉及侵权,请第一时间联系本网删除。
相关文章
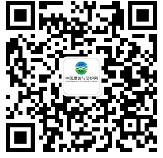
官方微信
《腐蚀与防护网电子期刊》征订启事
- 投稿联系:编辑部
- 电话:010-62316606-806
- 邮箱:fsfhzy666@163.com
- 腐蚀与防护网官方QQ群:140808414
点击排行
PPT新闻
“海洋金属”——钛合金在舰船的
点击数:8148
腐蚀与“海上丝绸之路”
点击数:6486