导读:本文提出了一种采用高效率埋弧等离子体作为替代热源的新型电弧熔丝增材制造方法,即埋弧增材制造技术。经过初步探索发现,通过促进α-Fe(BCC)由柱状晶到等轴晶的完全转变(即CET),可实现大型低碳铁素体-珠光体钢构件的近净成型,并获得均匀且近似各向同性的微观结构。沉积态构件的顶部区域主要由柱状α-Fe晶粒构成,具有典型的优先<001>α取向。均化区域因受到原位内生性热处理的作用(IHT)从而多次触发快速的同素异形体转变(主要是多层穿透的正火、全层穿透的临界区退火和持续持久的回火的组合,即NIT)。因此,理论上当每个新沉积层的净层厚不大于受该层影响下已沉积层细晶区的宽度时,每个新层中的微观结构可以逐渐被后续层细化和均匀化。因此,均质区主要由近完全等轴的α-Fe组成,显示出沿沉积方向的均质特性。在全层穿透NIT的影响下,珠光体轻微球化,平均尺寸(从4μm降至2μm)和体积分数(从5%降至1%)都得到降低,这可以有效减轻裂纹敏感性。透射电镜结果表明均质区不仅晶内位错数量显著减少,而且其形态也从缠结态演变为可动态。上述转变连同晶粒细化和大角度晶界的形成,导致α-Fe基体中的内部应变更低且更分散。因此,构件获得了优异的夏比冲击韧性(在-60°C时超过300 J),且强度无明显恶化。冲击、拉伸和硬度测试显示出几乎各向同性的机械特性。我们相信这种新方法将会在未来的大、中型构件增材制造中展现出巨大前景。
金属增材制造(AM)因其能够在航空航天、汽车、核能和医疗在内的工程行业中实现复杂的近净成型而引起了极大的兴趣。作为一种逐层制造方法,该技术发展迅速,通常在制造策略的创新上受到广大研究者与工程师的重点关注——即追求具有更高的沉积速率、更好的表面光洁度以及具有定制机械性能甚至更大尺寸部件的加工能力。
基于最初在上世纪90年代获得专利的粉末输送方法,金属AM方法可大致分为两大类:粉末床融合(例如,选择性激光熔化(SLM)、电子束熔化)或定向能量沉积(例如,激光金属沉积(LMD))。SLM方法通过高能量密度和精确控制的热源(通常是精密设计的镜面控制激光器)来局部熔化预置粉末,具有熔池小,凝固率高等特点,因此可以获得具有较高表面光洁度的复杂几何结构。因其普遍采用具有高附加值特征(例如:钛合金、镍合金和高熵合金等)的填充材料,从而显著降低成本,减少浪费,被称为是一种具有良好经济平衡的环保技术。然而,低沉积速率(约50g/h)和仅能加工小型产品的能力阻碍了SLM方法的更广泛应用。虽然通过LMD可以实现更高的沉积速率 (480-900g/h),但对于该非致密粉末输送技术,诸如微裂纹和孔隙率等缺陷将无法避免,这些缺陷也成为了限制LMD产品性能的主要原因。
电弧熔丝增材制造(WAAM)因采用电弧-丝材系统,具备制造致密构件的能力。沉积速率的大幅提升与制造大规模、完全致密组件的能力相结合,使WAAM比其他粉末输送技术更具优势。然而,在WAAM的大幅推广之前仍然存在一些挑战。包括难以达标的机械性能和由冶金问题引起的各向异性、表面质量差、残余应力和变形等问题。
受传统热处理和其他成型制造方法的启发,许多WAAM技术结合了后处理的某些工艺特点,即通过沉积后加热、加压或两者兼有之,以消除传统增材工艺中的缺陷,例如孔隙率和各向异性等。然而上述做法仅停留在理论与工艺的研究阶段,装置繁杂且效果有限,很难进行大规模推广;热处理对构件尺寸有苛刻的限制,难以处理大型构件且成本高昂,这也为拥有致密均匀组织的大型零件的加工带来困难。
在此,天津大学材料科学与工程学院程方杰教授团队的博士研究生李宇航(第一作者)首次提出了一种新型SAAM技术,该技术能够原位、高效(沉积效率~20kg/h)制造具有各向同性等轴微结构的大型、高致密度构件。由于工艺自带的热作用属性使沉积层具有特殊的大宽厚比的特点,使工艺本征的原位IHT具有全层穿透特性,这种方法不仅避免了昂贵的后热处理,而且还可以原位调整微观结构。
低碳钢作为目前最常见且拥有无限市场需求的工程材料之一,拥有最简单的铁素体-珠光体相系统。作者认为该系统最适合研究微观结构演变以揭示SAAM固有原位IHT的本质。因此,本研究选用AWS-EM12K埋弧焊丝(SAW)作为丝材原料,OK FLUX 10.62作为焊剂进行大型构件的埋弧增材制造过程。此外,灵活的加工路径和复杂的几何可访问性是SAAM区别于常规传统等材、减材制造的显著优势,若构件性能可以与传统方法制造的零件相媲美,这种新的加工模式对于高强钢构件的大规模制造将具有巨大的应用前景。相关研究成果以题“Submerged arc additive manufacturing (SAAM) of low-carbon steel: Effect of in-situ intrinsic heat treatment (IHT) on microstructure and mechanical properties”发表在增材顶刊 Additive Manufacturing上。
论文链接:
https://www.sciencedirect.com/science/article/pii/S221486042100289X?via%3Dihub
研究表明,由于经历了多次快速的同素异构转变,SAAM组件顶部具有典型择优取向的<001>α柱状微观结构(尺寸为 46.8± 21.7μm)随着沉积过程中埋弧热源逐渐远离,后热循环次数的逐渐增加,该柱状微观组织逐步转变为细小的等轴均质结构(尺寸为 10.1 ± 4.2 μm),结果发现完整的CET过程需要至少四次连续热循环。因SAAM过程自身独有的沉积层大宽厚比、高热输入和高层间温度的特点,其加工构件中每一沉积层的热历史与其他AM方法得到的存在显著差异。当沉积层的净高度不超过一阈值(即受该沉积层影响下已沉积层细晶区的宽度)时,每个新层中的微观结构都可以通过独特的原位全层穿透IHT细化和均匀化。否则,将会形成一系列周期分布约1.7倍净层厚间距的HAZ带。幸运的是,较高断裂伸长率值和平滑的应力-应变曲线表明HAZ带并未对机械性能造成影响。
SAAM低碳钢构件均质区因具有软化、均质的铁素体基体上弥散分布低体积分数渗碳体相的微观组织特征,其UTS和?分别达到了454 MPa和29.8%(水平方向),441 MPa和35.6%(垂直方向),维氏硬度稳定在约148 HV。拉伸、夏比冲击和维氏硬度测试表明机械近似各向同性。轻微球化的渗碳体颗粒、可动线型位错、细晶粒和 HAGB 的形成显着降低和分散了α-Fe基体中的内部应变,从而获得了优异的延展性和冲击韧性(-60℃夏比冲击韧性超过300J,韧脆转变温度低至?102 °C)。
图1 (a)三维SAAM平台;(b)SAAM设备的z轴放大图(包含焊丝、送丝机构、焊剂料斗和SAW焊枪);(c) SAAM 的加工过程示意图和温度测量点的位置(未展示焊剂挡板);(d) 扫描路径与SAAM-EM12K钢构件成品
图2 (a)SAAM构件从柱状晶区(CGZ)到均质区的光学显微照片(由右上角的橙色框表示)。(b)晶粒尺寸随相对高度的变化。图(c)、(d)、(e)和(f)为(a)中用‘c’、‘d’、‘e’和‘f’标记的选定区域的放大SEM显微照片;(g)是(f)中用‘g’标记的区域的放大 SEM显微照片。
图3 距SAAM构件顶部 (a) 6 mm、(b) 30 mm 和 (c) 50 mm 处 P 的SEM显微照片。(d)和(e)分别是(a)和(c)中标记为‘d’、‘e’的区域的放大TEM显微照片。(f)示意图展示了P的测试点,以及相应位置的尺寸和面积分数。
图4(a)反极图(IPF),(b)取向差角度图,(c)Kernel平均错位角(KAM)彩色图,(d)指示测试位置的示意图(测试位置距顶部50mm),(e)错位角分布,(f)KAM分布
图5(a)CGZ(未收到热影响)和(b)均质区(经历36次后热循环)的位错形态
图6(a)由热电偶(TC1-TC4)测得的典型SAAM加工过程的构件热历史,热电偶(TC1-TC4)在增材过程进行中分别于完成第1,14,28和48层后距离顶部3.5mm,7.5mm, 7mm和9mm处墙的侧壁点焊。蓝色虚线框表示在(b)中放大的区域,其中显示了从第29到第33沉积层的五次连续热历史(用红色实线表示)。除了测量的热历史之外,图(b)还给出了假想的无法测量的第4次和第5次热循环(用灰色虚线表示)。(c)光学显微镜下的组织与通过 TC3 获得的热循环的相对位置一致,其中每道由虚线分隔(红色代表道次6-10,白色代表推测的无法测量的道次4和5)。(d)使用JMatPro计算得到的α-Fe和奥氏体相平衡体积分数随温度的变化
图7原位IHT过程中的微观组织演变示意图(a)整体视图和(b)NIT作用下的组织相变过程
图8 SAAM样品在垂直和水平方向的应力-应变曲线。插图显示了相应的光学显微照片,其中α-Fe在垂直和水平方向上均呈现等轴晶特征
图9层间温度约为300℃时SAAM样品的冲击韧脆转变曲线。TDBTT通过使用Boltzmann函数拟合冲击吸收功与温度曲线来确定。
免责声明:本网站所转载的文字、图片与视频资料版权归原创作者所有,如果涉及侵权,请第一时间联系本网删除。
相关文章
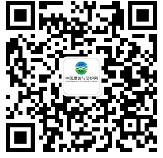
官方微信
《中国腐蚀与防护网电子期刊》征订启事
- 投稿联系:编辑部
- 电话:010-62316606-806
- 邮箱:fsfhzy666@163.com
- 中国腐蚀与防护网官方QQ群:140808414
点击排行
PPT新闻
“海洋金属”——钛合金在舰船的
点击数:7130
腐蚀与“海上丝绸之路”
点击数:5741